In processing gold, once it is completely dissolved the solution that is formed by that dissolved gold is called the ‘PREG’ or short for PREGNANT SOLUTION. In other words solution that is full of gold and is accordingly yellow in shade/colour. The solids are now considered the waste and the liquid is the concentrate. To separate the two the solids are allowed to settle in a tank called a THICKENER and the pregnant solution disturbing its sediment. Here is the Merrill Crowe Process from A to Z.
The OVERFLOW, or the portion that is being decanted, will be sent to a holding tank. While the solids will be taken from the bottom of the thickener, w filtered and washed to be sure there isn’t any solution left on the rock particles. Once that is done the solids then will be discarded as final tails. The water that was used to wash the solids will be put back into the thickener so that it may decant off as pregnant solution. These two pieces of equipment the thickener and the filter will be discussed in another session discussing the drying of concentrates.
It is also these final tails that cause an environmental impact. The disposal of them may be very expensive.
We now have the gold separated from the solids but it is in liquid form. Our next step is to prepare it’ for precipitation. There are two pieces of equipment that the pregnant solution must go through. The first is a CLARIFIER. What a clarifier does is ensure that all of the waste rock is filtered out of the pregnant solution before it begins the precipitation cycle.
The second is a device that I describe as a DE-OXYGENATOR. To have the gold precipitate, all of the oxygen in the pregnant solution must be removed. This is the job of the de-oxygenator. The clarifier, the de-oxygenator and another type of filter called an FILTER PRESS make up the precipitation circuit. The cleaning of the pregnant solution and the removal of the oxygen may be done in one step. The first thing that is required is the solution be pumped to the clarifier. A clarifier is a frame work that a big square filter bag fits over. A vacuum is applied to the inside of this bag. The solution is pulled through the tight weave of these filters trapping any solids that may have been decanted from the thickener with the pregnant solution.
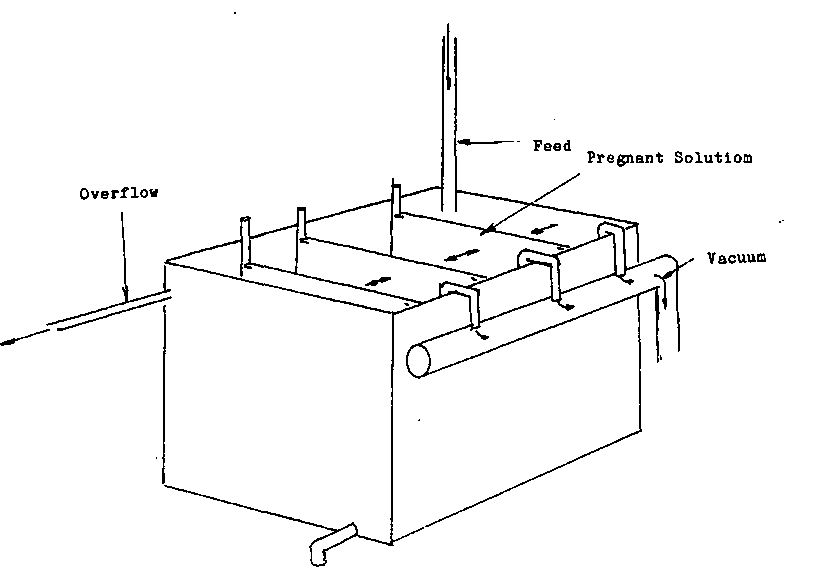
In the same vacuum circuit is the DE-OXYGENATOR. This is simply a tank and a pump.
The vacuum pulls the pregnant solution through the clarifier to the tank. The pump pulls the solution from the tank and forces it through the FILTER PRESS.
The rate that the pump discharges the pregnant solution is controlled. This is to maintain the tank level at approximately one half full. The vacuum in the top half of the de-oxygenator will remove any oxygen that is in the solution.
The pump has two functions first to propel the solution through the filter press and as an addition point for the reagents that aid in the PRECIPITATION of the gold. As the pregnant solution is pumped to a filter press, two things are added to the solution. An OXIDIZING AGENT, and in this case, ZINC DUST (Merrill Crowe Flowsheet). The oxidizing agent will prepare the surface of the zinc and provide the interface for the gold to attach itself to the zinc. This is the process that is called precipitation.
The dictionary meaning of precipitation is: The process of separating any of the constituents of a solution, or rephrased, take the gold out of the solution. To do this, once the Zinc dust and the Oxidizing agent has been added to the solution it is pumped through filter presses. The zinc dust will be combined with the gold and be called the PRECIPITATE. This precipitate will be trapped on the cloths that form the filtering section of the presses. The solution that has been pumped through the filter presses will not have any gold left in it. At this point the liquid will be referred to as the BARREN SOLUTION.
Once the press is full it will be taken apart with the precipitate going to be smelted, and the gold removed.
The operation of this circuit is quite straight forward.
Proper operator maintenance of the filters to ensure that there isn’t any unwanted solids getting through the filter material and constant monitoring of the control Variables will ensure the recovery of the mineral.
Before we leave cyanidation lets go over those variables that the operator will have to watch: