Table of Contents
The extraction and recovery process of vanadium as a by-product from the tailings of a uranium processing plant poses many problems. In this study vanadium is recovered from impounded resin-in-pulp tailings and from the current tailings of a uranium plant which did not include a circuit for vanadium recovery in its initial design. Since the vanadium content is quite low, capital expenditures and operating costs must be maintained at a minimum.
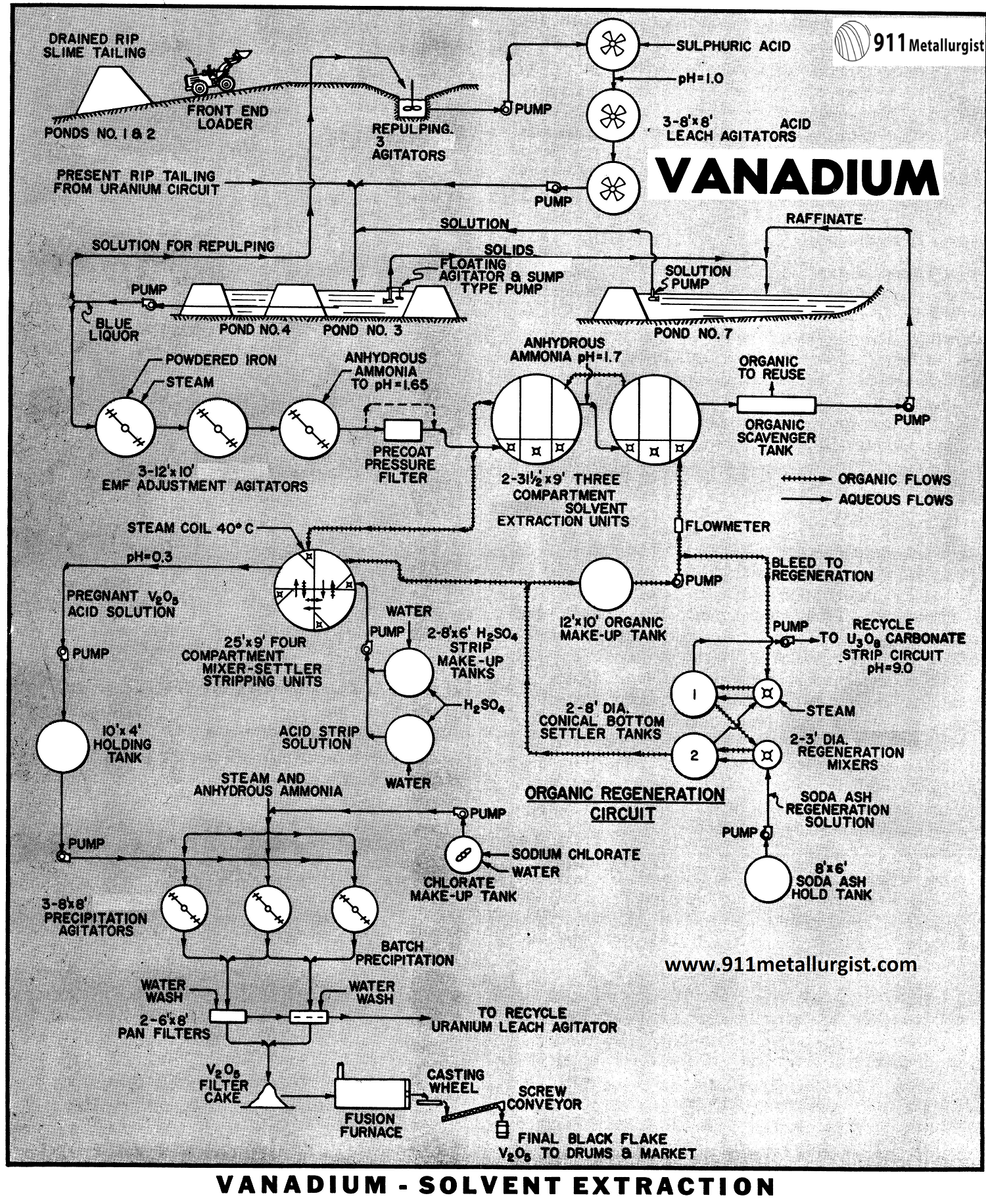
The Flowsheet of Vanadium Extraction Process
Repulping and Leaching
The accumulated and drained slime tailings are excavated from Ponds No. 1 and 2 at the rate of 100 to 150 tons per day on a three shift basis using a front end loader. The slimes are repulped with solution from Pond No. 4 to about 50% solids in a ground level sump using three stainless steel Turbine-Type Propellers. The repulped slimes are pumped to three 8′ x 8′ Leach Agitators arranged in series. Sulphuric acid is added to a pH of 1.0 to dissolve the vanadium. Retention time in the agitators is approximately six hours. The leached slurry is pumped to an ingenious system of excavated ponds which serve as washing and decantation vessels in place of conventional thickeners. Pond No. 3 receives the leached slurry together with the current slime tailing from the RIP uranium circuit. The vanadium-bearing (“blue liquor”) is piped from Pond No. 3 through a decantation tower to Pond No. 4. A sump-type pump and Propeller Agitator mounted on pontoons in Pond No. 3 are used to mix and transfer the solids from this pond to Pond No. 7 where the solids are combined with the raffinate from the subsequent vanadium SX circuit. The solution from Pond No. 7 is returned to Pond No. 3 using a trestle mounted pump which can be lowered or raised to compensate for the level of the pond. Ponds No. 3 and 7 serve as washing ponds whereas Pond No. 4 is a clarifying pond. The final tailing is allowed to accumulate in Pond No. 7.
EMF Adjustment
The clarified “blue liquor” from Pond No. 4, except for that portion recycled to the initial slime repulper, is pumped to the EMF adjustment circuit consisting of three 12′ diameter X 10′ deep Reducer Type Agitators in series. The agitators are constructed of wood stave tanks which are equipped with wood shafts and paddles to resist corrosion and impart mild agitation. Steam and powdered iron are added to the first agitator to produce an EMF of approximately 250 millivolts. This step reduces all ferric iron to the ferrous state and insures that all vanadium has been reduced from pentavalent to quadrivalent form. The steam is used to promote the reaction rate between the powdered iron and acid.
Anhydrous ammonia is added to the discharge of the No. 3 EMF adjustment agitator to produce a pH of 1.65 prior to passing to a precoat pressure filter for removal of carbon, slimes, and unreacted iron.
Solvent Extraction
The filtrate is then treated through six stages of solvent extraction consisting of two 3-stage mixer-settler units in series to extract the vanadium. The organic extractant is a kerosene solution containing 6% di-2-ethyl-hexyl phosphoric acid and 3% tributyl phosphate. Anhydrous ammonia is added to the fourth stage mixer to adjust the pH to 1.7. The raffinate, after passing through an organic scavenger tank, is pumped to Pond No. 7 for dilution purposes.
Two 31′-6″ diameter x 9′ deep Solvent Extraction units are used for recovery of the vanadium. Each of these units is divided into three main compartments which constitute the mixer-settler stages. Vertical Pumping Turbines are used in the mixers which permit the counter-current flow of aqueous and organic from stage-to-stage without the use of pumps or airlifts.
The organic extractant is fed to the last stage mixer at a rate of 85 GPM through a flowmeter and after flowing counter-currently to the aqueous through six extraction stages emerges as the pregnant organic.
Stripping and Regeneration of Organic
The pregnant organic is stripped in a four-stage Mixer-Settler Stripping Unit using a sulphuric acid solution. The acid strip solution contains 135 grams sulphuric acid per liter and represents a flow of approximately three gallons per minute. The No. 1 mixer, through which the pregnant organic solution enters, is equipped with a steam coil to raise the temperature to 40°C for improvement in phase disengagement.
The stripping unit consists of a 25′ diameter x 9′ deep wood tank divided into quadrants each of which has a mixing chamber. Vertical Pumping Turbines are employed in each mixer. The pregnant V2O5-( acid strip solution containing about 55-65 grams V2O5, per liter and having a pH of 0.3 is pumped to a 10′ x 4′ deep holding tank preparatory to precipitation.
The barren organic from the stripping circuit is recycled to the V2O5 solvent extraction circuit. However, about 10% of this flow is continuously regenerated using a 12% soda ash solution. A two-stage mixer-settler circuit is used for regeneration. The mixers are 3′ diameter and equipped with Vertical Turbine Mixers. The settlers are 8′ diameter conical bottomed tanks. Steam is added to the No. 1 mixer. The regenerated organic solution is returned to the organic make-up tank and reused.
Precipitation, Filtration and Fusion
The pregnant V2O5, acid strip solution is pumped to one of three precipitation agitators where the V2O5 is precipitated on a batch basis.
Steam is introduced to the agitator being used for precipitation to obtain a temperature of 70°C. Anhydrous ammonia is added to raise the pH from 0.3 to 0.6. The equivalent of 0.2 pound sodium chlorate per pound of V2O5 in solution is added.
The precipitated vanadium oxide (98-99% V2O5) is alternately filtered on two 6′ x 8′ rubber lined pan filters. Water washes are applied to the filters and the filtrates recycled to the uranium circuit to utilize the remaining chlorates as an oxidant for the uranium.
The V2O5 filter cake is manually added to a propane fired fusion furnace which operates at approximately 1900°F. The melt flows from the furnace onto a rotary casting wheel where it forms a 3/16″ thick by 3″-4″ wide band of “black flake” (99% V2O5).
Source: This article is a reproduction of an excerpt of “In the Public Domain” documents held in 911Metallurgy Corp’s private library.