Table of Contents
In the metallurgical treatment of uranium ores large tonnages must be handled. Many ores are low grade so it becomes necessary to employ systems which can be operated on a continuous basis at low cost. A vast amount of research has gone into the development of suitable processes. One is solvent extraction, which has proven extremely efficient and simple in operation. Diligent work has gone into selection of the proper solvents. The solvent is a high flash point kerosene with 10% by volume of Di-2-ethyl hexyl phosphoric acid and 2.5% primary decyl alcohol or tributyl phosphate. It is lighter than and immiscible with water.
Uranium Processing Flowsheet
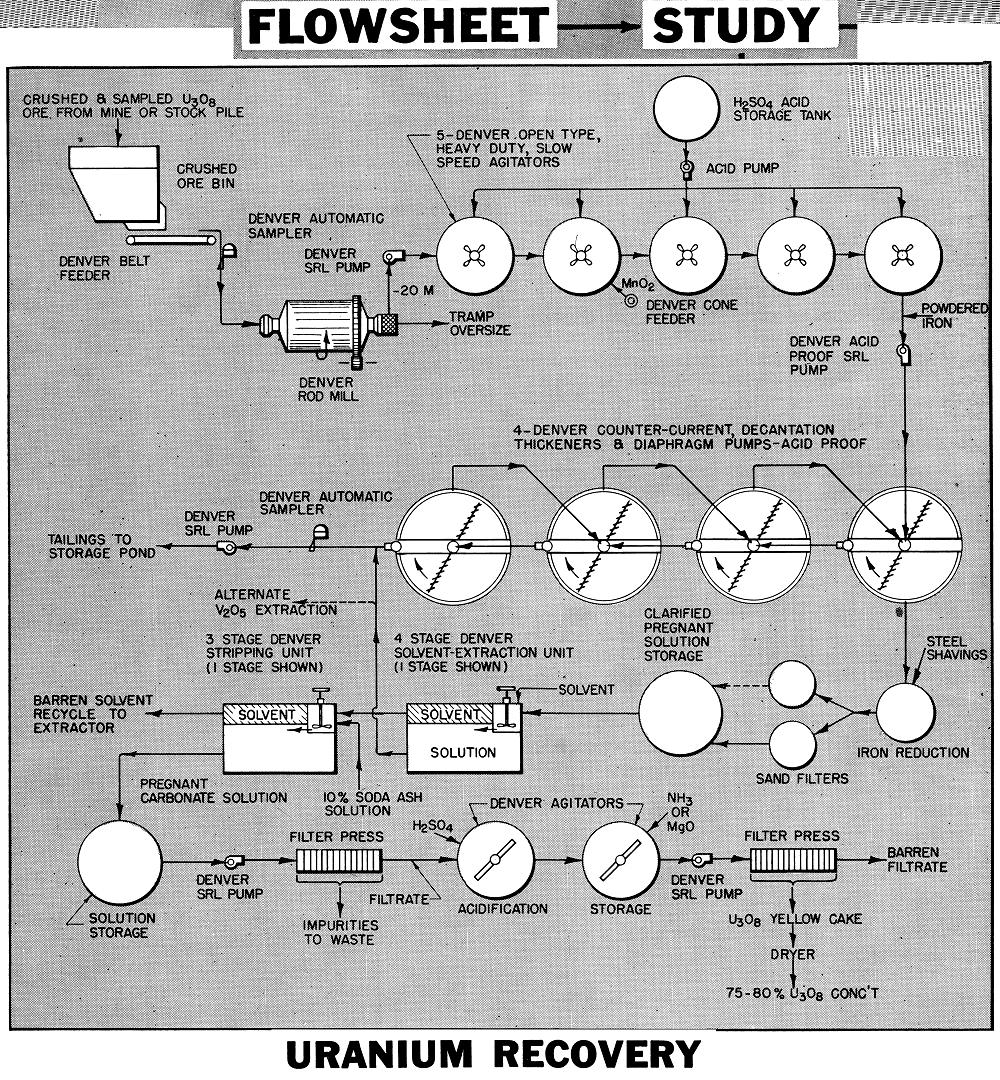
The flowsheet is generally applicable on sandstone and limestone ores containing uranium in the form of acid soluble carnotite and roscoelite. The values are dissolved with sulphuric acid and lime content is limited to about 6% to avoid excessive acid consumption. Dissolved uranium is extracted from the clarified and adjusted pregnant acid solution by the solvent extraction method, then the values are stripped out of the solvent and precipitated in the usual manner as yellow cake. Vanadium, if present, can also be recovered as a separate product by modifying the process.
Crushing, Grinding and Sampling of Uranium Ore
The crushing, grinding and sampling plant shown in our flowsheet study M7-F46 on uranium concentration and Bulletin No. U3O8 is generally applicable. The crushing circuit is based on wet grinding. A peripheral discharge Rod Mill or a large discharge mill is used.
The ore is ground to approximately all —20 mesh in the Rod Mill in one pass. A Spiral Screen removes tramp oversize. Mill discharge density is kept high to avoid dewatering ahead of agitation. For finer grinding, cyclones, screens, or classifiers may be employed to make the size split and return the oversize to the mill for further reduction.
Raw Leach Agitation of Uranium
The ground ore, at 55 to 60% solids, is agitated 12 to 16 hours in a series of Heavy Duty Slow Speed Agitators with Turbine Type Propellers. These are of special design to keep coarse solids in active suspension with minimum HP without excessive agitation.
Sulphuric acid is stage added to the agitators to maintain a pH of 1.0. An oxidant (manganese di-oxide) is added to and steam introduced into the pulp as required, to aid the dissolution of the values. Pulp flows between agitators by gravity. The pulp is uniform and air lifts are usually not required. Tanks are wood with 4″ staves and hoops are protected. Shafts and propellers are rubber covered.
Uranium Washing and Countercurrent Decantation
Pulp from the agitators (pH of 1.0) has in excess of 95% of the U3O8 in solution. A small amount of iron powder may be added to the pulp to reduce any ferric iron.
The leached pulp now passes to 4 Acid- Proof Thickeners for separation of the solution values in countercurrent decantation. Settling aids are added to promote flocculation and the production of crystal clear solutions. To aid settling and washing the flocculated solids, the diaphragm pump discharges are diluted down to 10-15% solids by recycling a portion of the thickener overflow back to the incoming feed launder. Final washed solids are pumped to tailing storage area.
All machine parts wetted by the pulp and solutions are rubber covered or of stainless steel 316. Tanks are wood with acid construction.
Uranium Solution Reduction and Clarification
The pregnant acid solution overflowing the primary thickener passes upward through a tank with a deep bed of loosely consolidated steel shavings to reduce any ferric iron present. This is important in keeping the U3O8 extraction system up to maximum efficiency. The solution overflowing the iron reduction tank passes through a sand filter bed for further clarification and removal of any graphitic carbon picked up from the iron shavings.
Solutions are stored in wood tanks prior to extraction of uranium for checking or adjustment in solution strength, pH, EMF, and metal content, as required.
Solvent Extraction Circuit of Uranium
Consists of mixers and settlers with solvent passing countercurrent to the flow of pregnant acid solution. The solvent, having a greater affinity for uranium in acid solution, strips the values from the solution. For high efficiency this usually requires 4 stages of countercurrent decantation. The kerosene solvent mixture collects at the surface of the acid solution in the settlers and is drawn off by gravity or by means of air lifts.
Agitators provide for efficient transfer of the uranium values. This step is controlled to avoid emulsification and loss of solvent in the barren solution. Commercial operation has been very successful with little or no loss of solvent.
Generally 1 gallon of solvent flows countercurrent to every 4 or 5 gallons of pregnant solution.
Uranium Stripping Circuit
A 10% sodium carbonate solution strips the uranium values out of the solvent in a Mixer-Settler arrangement. Two to three stages are sufficient for transfer, since stripped solvent is recycled back to the extraction unit for re-use. Solvent flows by gravity while the sodium carbonate stripping solution may be advanced countercurrent with air lifts.
Pregnant carbonate liquor, containing uranium, filtered to remove solids, is ready for precipitation. All equipment in the stripping section is of mild steel.
Uranium Neutralization and Precipitation
Uranium is recoverable from pregnant carbonate liquors by two general methods:
- destruction of the carbonate with acid, followed by precipitation of the uranium as yellowcake with ammonia or magnesia;
- caustic precipitation.
In the flowsheet shown the clarified and filtered carbonate solution passes through two Rake or Paddle Type Agitators for acidification and precipitation. The precipitated solution passes through a filter press where the yellow cake is collected. This cake analyzing about 75-80% U3O8 is dried and packed in drums for shipment.
Remarks on Uranium Metallurgy
Solvent extraction of uranium is remarkably simple in continuous operation. Equipment is inexpensive. It is competitive in chemical cost with any of the established methods of uranium recovery. Equipment products are used extensively in these plants although much of it is special to handle the corrosive solutions.
https://www.911metallurgist.com/radium-uranium-vanadium-extraction-recovery-carnotite/
https://www.911metallurgist.com/radium-uranium-vanadium-processing/
https://www.911metallurgist.com/vanadium-uranium-extraction-recovery/
https://www.911metallurgist.com/radium-extraction-recovery/
https://www.911metallurgist.com/processing-extraction-recovery-radium/