Crushers may be divided into three general classes, with respect to the manner in which they do their work:
Pressure Crushers: This category embraces the several types of gyratory crushers and jaw crushers, as well as the double crushing rolls, with either smooth or corrugated shells.
Impact Crushers: This division is represented chiefly by the various styles of hammermill; also by the cage type disintegrator.
Combination Impact and Sledging Crushers. In this class we have the single or double sledging roll crushers. An example of the former is the Fairmount crusher, of the latter, the Edison roll crusher.
Some further subdividing and qualification might be applied to these general classifications, but these, for the most part, are not of particular importance. Pressure crushers, for example, may be divided into two subclasses: the reciprocating, and the continuous-pressure, types. The gyratory and jaw crushers come under the first category, the crushing rolls under the second. Strictly speaking, the gyratory motion is not a reciprocating one, but it is so with respect to any vertical radial plane through the crushing chamber; therefore it is convenient to view it in that light. Some roll crushers, notably the light coal crushing type, have more of a tearing action, as contrasted to the heavy sledging performance of such machines as the Fairmount crusher.
Here are several, but not all, types of crushers:
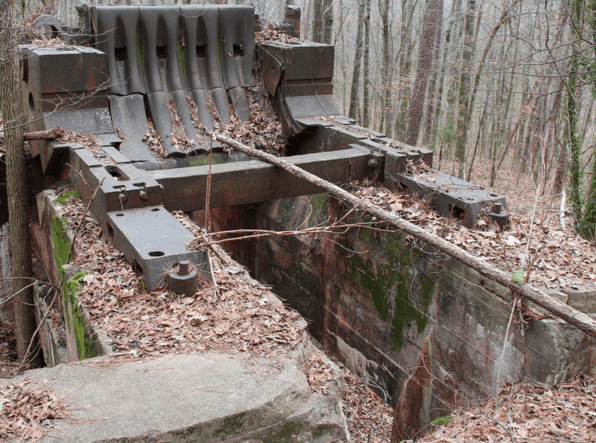
During the same years wherein the industry was concerned with development of larger and still larger primary crushers,another member of the family was born: the single, sledging- roll crusher. The Allis-Chalmers Co. entered this field in 1911, building two sets of 36″ dia. x 60″ face single-roll crushers, flux limestone plant. Taking the name of its proving ground, this machine was christened the “Fairmount crusher.” The machine quickly achieved a high degree of popularity, and although its field of application is relatively limited, quite a number of them were in-stalled for primary crushing service. The line was expanded to include smaller sizes, as well as the big 60- x 84-in. machine.
Development of concentration and cyanidation in the mining industry called for finer crushing than was feasible in the gyratory or jaw crushers then available. This requirement was met for a number of years by the double smooth-face crushing rolls, originally known as “Cornish” rolls. As the mining industry during the period we are discussing was a very active one, the development in this type of crusher had reached a fairly high stage before the end of the century, and some excellent heavy-duty roils were available at that time. That this machine was not used to any considerable extent in the commercial crushing plants of that period was due simply to the fact that there was no demand for the smaller sizes of crushed stone, at least not any more than could be taken care of by the crushing methods then in vogue in such plants.
This brings us to the rather significant fact that, while all of the interesting and rather remarkable development we have outlined was going on, very little, if anything, was being done to develop special crushers for secondary and fine-reduction work, other than the work on crushing rolls just described.
The design scheme of crushers:
a – jaw, b – cone, c – mushroom, d – hammer, e – roller;
1 – fixed cheek with the rotation axis; 2 – a movable cheek; 3, 4 – the eccentric shaft; 5 – rod; 6 – hinged rear bearing spacer cheeks; 7 – spring; 8, 9 – width adjustment mechanism of the discharge gap; 10 – pull the lock device; 11 – bed; 12 – still cone; 13 – cone moving; 14 – traverse; 15 – hinge suspension rolling cone; 16 – cone of the shaft; 17 – drive shaft; 18 – eccentric; 19 – amortization spring; 20 – foot ring ;21 – regulating ring; 22 – thrust bearing cone; 23 – rotor; 24 – liner plates; 25 – grate; 26 – hammer; 27 – main frame; 28 – crushing rolls.
Ruslan Udintsev