Table of Contents
The Beneficiation flowsheet shown with this study is particularly adapted to the concentration of tungsten ore in small tonnages. Tungsten minerals are generally in the friable class and therefore concentrating processes are hindered by the excess amount of fines produced in the crushing and grinding steps. Special consideration must be given to the stage reduction and concentration to avoid excessive losses in the fines. The Mineral Jig plays an extremely important role in this flowsheet due to its ability to handle an unclassified feed, with outstanding recovery in the coarse sizes and substantial recoveries in the fine sizes. A selective high grade product is obtained with a minimum amount of water.
Tungsten ore Beneficiation FLOWSHEET
Crushing Tungsten Rock
The Crushing section begins with a picking belt feeder of sufficient length to allow convenient inspection and the picking out of high grade or waste prior to crushing. A Vibrating Grizzly is used to remove the fines from the Jaw Crusher feed and thereby increase crushing capacity. The Jaw Crusher discharge is elevated to a Vibrating Screen which efficiently controls and limits the maximum size going to the gravity concentrating circuit. The Vibrating Screen oversize is reduced in the Crushing Rolls. This unit was selected for this flowsheet because it provides efficient reduction with a corresponding production of only a comparatively small amount of fines. The discharge from the Crushing Rolls is returned in closed circuit with the Dillon Vibrating Screen.
Tungsten Gravity Recovery and Regrind Circuits
The Selective Type Mineral Jig is the first machine in the gravity concentration circuit and handles the unclassified Screen undersize. As indicated in the accompanying table, the Mineral Jig shows the highly efficient concentration in all sizes of a feed which is minus 10 mesh. Although the Mineral Jig can be adapted for coarser feeds, this particular Jig was fitted with 3 mm. opening lower screens.
The hutch product from the Mineral Jig passes over a cleaner jig producing a high-grade tungsten concentrate and a middling product which is then reground. The fines in the middling product are removed in a Dewatering Classifier and the sand product passes to a Peripheral Discharge Rod Mill.
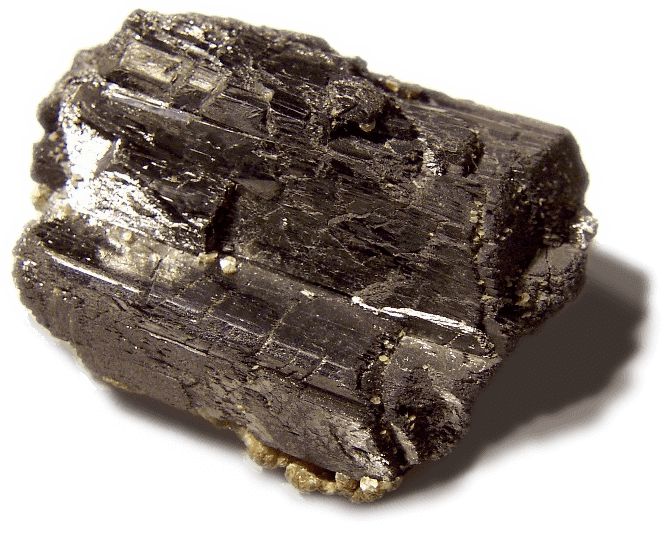
The Peripheral Discharge Rod Mill permits rapid discharge with minimum contact time and therefore this mill is ideal for limiting the number of fines in the ball mill discharge. After the middling product is quickly ground to liberate additional minerals, it is then re-jigged to recover the additional high-grade tungsten.
In tungsten plants, it is common practice to treat gravity tailings by flotation. Shown below is a characteristic “soap flotation” froth in a “Sub-A” Flotation Machine recovering ferberite from gravity plant tails in a Colorado tungsten concentrator.
The rougher jig tailing and the classifier over-flow pass to a Hydraulic Classifier which prepares a sized feed for tabling and slime concentration. The Concentrating Tables produce a high-grade concentrate, a middling product which is returned to the Peripheral Discharge Ball Mill, and a final tailing. The very fine tungsten is concentrated by means of the Buckman Tilting Concentrator which is especially designed for slime concentrations.
Canadian Tungsten Beneficiation Practice
A typical tungsten recovery plant in Canada utilizes a 16″x 24″ Duplex Mineral Jig in a closed grinding circuit. It operates as a rougher unit on a rod mill discharge at 50% solids and produces a concentrate running about 50% WO3. The hutch concentrate is discharged at intervals to a 12″x 18″ Duplex Mineral Jig which operates as a cleaner unit. The feed to the cleaner jig is 70% solids and the product grades from 72-73% WO3, and amounts to 65% of the gravity concentrate recovered. The cleaner jig tailings return by gravity to join the rod mill discharge and are returned to the rougher jig.
The final jig concentrate is, on an average, made up of 77% scheelite, 8% ferberite, 4% hematite and 11% silicates and oxides. The specific gravity is 5.73. The mesh analysis of the final jig concentrate is as follows:
Tungsten Extraction Process Summarized
The ability to recover a high-grade concentrate from an initial coarse unclassified feed, with a minimum amount of slimes, is one of the outstanding features of this flowsheet. Special consideration is given to the friable nature of the tungsten by using Crushing Rolls and the quick pass grinding offered by the Peripheral Discharge Ball Mill. Previous experience in the concentration of tungsten ores indicates that the fine sizes carry the tungsten losses. For this reason, the Buckman Tilting Concentrator is installed and is particularly adapted to overcome this loss.
Although not indicated on this flowsheet, tungsten ores are often subjected to magnetic separation and test work will indicate the advisability of using this process on a particular ore. Even scheelite, though not itself amenable to magnetic concentration, is often treated magnetically to remove garnet.
Source: This article is a reproduction of an excerpt of “In the Public Domain” documents held in 911Metallurgy Corp’s private library.
Tungsten-Gold from Wolframite
Tungsten from Scheelite
https://www.911metallurgist.com/tungsten-processing
It has been a universal observation that rich grades of ores and minerals are getting depleted, simultaneously the demands for civilization are ever increasing coupled with the occurrence of poor grades of ores and minerals posing a problem to the processing engineers. At the same time, the cost of mining and milling are increasing, creating a situation where the management has to handle and process low grade ores at an economic level keeping environmental stipulations and control to be safeguarded which has been an additional cost for the management to comply with.
It is observed from the mineral processing technologies available that both by gravity concentration, flotation and allied techniques it is not possible to recover substantial amounts of minerals values lost in the tailings and slimes from the processing sector where these rejects contain values in the particle sizes of 0 to 20 microns. The latest technology developed in various countries (which culminated in creation of a class of centrifugal gravity separators such as multi gravity separator. Knelson separator, Falcon concentrator and Kelsey Jig etc. proved their ability to recover the mineral values efficiently in the range of 0 to 20 microns. Now is a situation where processing engineers can program recovery of values from old tailings, mill rejects, marginal, sub-marginal and lean ores and over burden, which till today have been left over for want of technology, can be projected and processed as a usable source of minerals.
The recovery of tungsten from the rejects, tailings, old dumps and recovery of very finer values in the ranges of 500-1000 ppm present in the granite rock are recovered satisfactorily compared to those results obtained by processing the ores anywhere in the world. The mineral processing engineer now has to look into the possibilities of recovery of recoverable values and associated minerals in the tailings, old rejects and ore dumps of earlier mining activities.