As there is seldom enough ground available on which the tailing of a flotation plant can be run to waste without being stacked, it is usual to impound it in some form of dam where the solids can be deposited and the water decanted off for return to the plant. It is generally advisable to recover as much of the water as possible in order not only to save the expense of obtaining a fresh supply but also to return to the flotation circuit any reagents that it still contains in solution. Assuming that it is necessary to return the water to the plant, it is best to dispose of the tailing pulp in two stages, dewatering it in a thickener close to the plant before sending it to the dam, which can seldom be near and often has to be a considerable distance away. This method keeps at a minimum the cost of pumping, which is the heaviest item of expenditure.
Tailing Thickeners
In modern practice the first stage of dewatering is generally carried out in a Traction Thickener, which is of the same general design as the machine described in connection with concentrate thickening, except that in the larger sizes of tanks often only the walls and central column are of concrete, the bottom being of tamped earth.
The capacity of a tailing thickener depends on the nature and size of the gangue and on the W/S ratio of the pulp. For rough calculations in the absence of definite data, it is usual to allow 8-12 sq. ft. of settling area per ton of dry tailing per 24 hours. The underflow should contain no more water than is needed to make it flow without choking along the launder or pipe-line to the dam. This is seldom possible with more than 50% of solids and a greater dilution is frequently necessary.
Tailing Dams
The tailing dam should be situated where the slope of the ground enables the pulp to be retained with the minimum length of artificial embankment, since its height has to be raised at frequent intervals as the basin becomes full. The area enclosed must be large enough to allow of the settlement of the solid material, including the finest slime, at the maximum rate of inflow, so that clear water can be continuously decanted off and pumped back to the plant.
When a new dam is to be started, an embankment of earth or masonry is usually first constructed to the height of a few feet, but subsequently the tailings deposited in the basin are utilized to raise it. This is often done by hand on a small scale. The dam is usually divided into two sections, and, while one section is being filled, the wall of the other is raised a foot or two with material excavated from the edge of the basin.
For a large dam a mechanical excavator is employed instead of hand labour. Fig. 70 shows the method of construction.
If a large proportion of the tailing is coarse and granular, the wall can sometimes be built by direct deposition from the pulp as it enters the dam without the necessity for excavation. A launder to carry the tailing is placed for the purpose a few feet above the embankment along its whole length (Fig. 71), and holes are bored in the side or bottom at short intervals so as to direct a series of streams of pulp inside the inner edge of the existing wall. The coarse portion of the tailing settles where it falls in a series of conical piles, which eventually become large enough to join up, forming a continuous wall. The fines flow into the interior of the dam where they settle, and clear water is drawn off at the far end through a decanting pipe. When the wall reaches the level of the bottom of the launder, the pulp is turned into a new one erected for the purpose at a higher level, the old launder being removed and used again.
Types of Tailings Dam
The above method often proves unsatisfactory with some classes of ore, especially those that have been finely ground, as an embankment wall composed of material containing more than a certain proportion
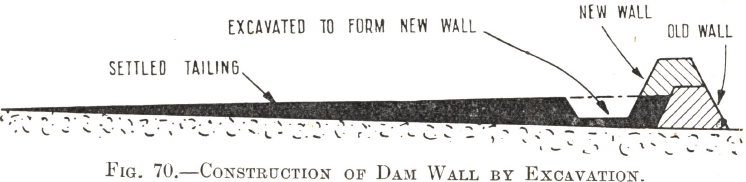
of slime is likely to slide and cause the dam to break away. The procedure usually adopted in such cases is to separate the tailing into coarse sand and fines in a classifier, and to use the coarse product to build up the wall ; the remainder of the pulp is discharged into the interior of the dam. A wall of this class being of a porous nature, the slime which
settles on the inside face penetrates a short distance, but quickly forms an impervious layer that prevents leakage. The classifier should be situated at the dam itself and not in the plant, since deslimed sand needs a launder of steeper slope than unclassified tailing, the slope required being, as a rule, too steep to make it practicable under normal circumstances to send the sand separately to the dam. A self-contained rake
classifier unit, running on a temporary track on the dam wall, is often used for the purpose, a part or the whole of the tailing pulp being diverted into it to supply the amount of coarse sand needed. The unit is placed at one end of the embankment on a short section of wall built up to the required height. As the sand is discharged over the end of the classifier, it is distributed on the adjoining 10-20 ft. of old wall until the level is the same as that of the first section, when the unit is moved forward and another section started (Fig. 72). This procedure is followed until the whole length has been raised to the required height.
Stationary classifiers, such as hand-operated or automatic cones or spitzkasten, are sometimes used in place of a moving unit. They are erected at short intervals along the length of the dam wall under the tailing launder. The underflow is directed to the inner edge of the existing embankment by short lengths of launder, which are shifted as required so as to build up a continuous wall of the desired dimensions.
There are many other ways of running a tailing dam, but most of them are based on one or other of the methods described above, from which they differ for the most part only in detail.
Tailing Disposal Costs
Filtering and tailing disposal costs are comparatively small items compared with those of the other sections of the plant. They cannot be predicted accurately in the absence of definite data, because filtering costs depend so largely on the tonnage of concentrate produced, and tailing disposal costs on the method of working the dam and its distance from the plant. The costs likely to be encountered in the treatment of a low-grade copper ore and a high-grade lead-zinc ore are variable, but they can only be regarded as average approximations. Various miscellaneous items are grouped with the tailing disposal costs in addition to those of returning the tailing water from the dam and of pumping the fresh supply to the plant; they include such items as assaying, heating, and lighting, and any special charges for transporting ore or concentrate in the vicinity of the plant which cannot be allocated to one of the other sections.