Table of Contents
It was a German limestone quarry that saw the World’s first mobile crusher. The idea was born to take advantage of a continuous belt conveyor haulage and eliminate the costly road construction and up-keeps on wet ground. Since then, the mining industry, mostly quarries have seen 100s of mobile crusher installation crop-up most (70%) of which are under 1000 TPH and feed directly at the excavator face.
An in-pit and mobile crusher facilitates the transport of crusher material (ore, stone, rock) out of the mining area via also mobile or portable conveyors. The type of primary crushing is done using any of the several types of crushers available today capable of taking coarse/large rocks:
Better than 70% of mobile crushers are installed in limestone operations with around 15% being gyratory, 30% hammer, 25% impact and under 10% jaw crushers.
The word “Mobile” has been coined to indicate any type of “Movable” crusher. Most mobile systems of crushing equipment may consist of any crusher on tracks, wheeled frame or skid allowed it to crawl or walk. This does not make the mobile crushing equipment portable, it just makes it mobile in reference to the ore supply source. If you combine a hopper, rock feeder and conveyor to those crushers, you have a fully equipped and functioning mobile crushing plant.
As you can image, not all crusher plants have the same level of mobility. We have therefore created sub-types of Mobile Crusher Labelling listed here in reverse order of mobility:
- The mobile crusher
- Semi mobile crushers
- Movable crusher
- Portable crusher
- Modular crusher
- Semi-fixed crusher
The true mobile crusher which are supplied directly by the excavator at the face and, using its integrated conveyor, follows the main conveyor as mining advances.
Semi mobile crushers are still operated at the mining face but are not moved as often as the mobile crusher.
A movable crusher is positioned in the mine’s center at the same mining level as it working face. Such a crusher is mobilized every couple of years to keep it economically close to the core mining operation. Highland Valley Copper is a good example of large movable crushers (2) and the effort it takes to move a crusher that surely not portable.
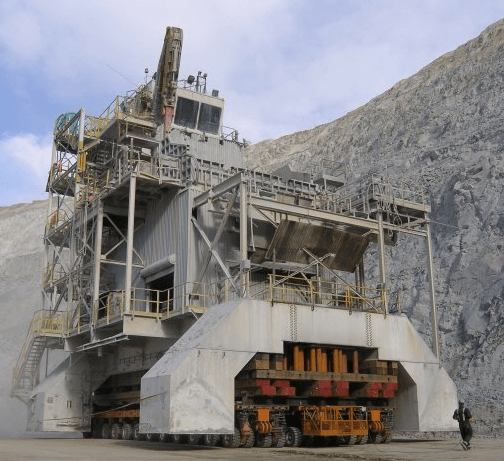
A portable crusher is not like a “portable” item as we are accustomed to. It means a crusher you can take apart or disassemble and transport on a road or highway if necessary. This ambiguity in terminology might cause a small prospectors and miners might search the internet for portable crushers but not find anything they hoped to fit in their pick-up truck or trailer & a large mining contractor to only find hobby size crushers.
The crushing station of the modular crusher can be dismounted into “light weight” modules and reassembled to the desired located generally in under 30 days. Since the resulting modules will still push over 60 tons plus measure over 40′, and the moving of such crusher still takes a month, the frequency of relocation is around 3 to 5 years apart.
The semi-fixed crusher is sitting on a steel platform to minimize concrete structure costs. These large crushers are normally moved every 10+ years.
Such large “mobile crushers” are transported and moved using crawlers like those by Mammoet seen here below.
![]() |
![]() |
The concept of mobile crushers is not new. Since their introduction about twenty-five years ago, mobile crushers have continued to gain widespread attention. Mobile crushers reduce minerals in the open pit mine to sizes which can be transported by belt conveyors thereby reducing or eliminating the need for truck haulage. Truck haulage is costly, often representing as much as 50% of the total mining cost. More than 80% of the cost of truck haulage is for fuel and lubricants, tire replacements, and operators wages, and it can be anticipated that the cost of these items will continue to increase at a steady pace. Compared to truck haulage, transportation by belt conveyor is more energy-efficient, less labor-intensive, and less subject to inflation. Therefore, mobile crushers, used in conjunction with belt conveyor systems, offer one of the most effective available methods of reducing energy consumption and mining costs.
How Mobile Crushers Operate
A mobile crusher is a completely self-contained unit mounted on a frame, which is moved, by means of a transport mechanism, along the wall of the mine pit as mining progresses. Excavated rock is fed, by means of a shovel or a front-end loader, into the mobile crusher, where it is crushed to sizes which a belt conveyor can handle. The crushed material is delivered to a shiftable belt conveyor system, which follows the movement of the crusher.
The mobile crusher unit is moved on crawlers, rubber tired wheels, or hydraulically operated walking pads. Figures 1, 2, and 3 show three operational mobile crusher units that are moved, respectively, by crawlers, rubber tired wheels, and walking pads.
The crawlers can move the mobile crusher unit 300-500m/h (1000-1500 ft/hr) and can negotiate slopes up to 10%. They exert a soil pressure of 10-20 N/cm² (14-28 psi) and can travel on difficult terrain.
The rubber tired wheels, each with its own hydraulic motor, can move the mobile crusher unit 500-1000 m/h (1500-3000 ft/hr). Since the tired wheels exert a greater soil pressure, approx. 40-90 N/cm² (55-125 psi), they are used only where soil conditions permit.
The hydraulically operated walking pads offer low deadweight, high safety in difficult terrain, and great mobility in all directions. They can move the mobile crusher unit 60 m/h (200 ft/ hr) and exert a soil pressure of 15-25 N/cm² (20-35 psi). Since they are subject to less wear and tear than the other transport methods, they require less maintenance. The walking pads can be operated synchronously by control from a central console.
Most of the commercial mobile crushers in operation today are designed for crushing limestone and have a theoretical output of 300-1000 metric tons per hour. A few larger units now in operation, which were designed for particular applications, have outputs of 1000-1500 metric tons per hour. Mobile crushers of still greater capacity are being developed in Europe.
Fig. #4 shows a typical cross section of a mobile crusher. Most mobile crusher units use hammer mills, impact crushers, roll crushers, or jaw crushers, but recent developments have made it possible to use standard gyratory crushers also.
Mobile crushers are of two types: direct-feed and indirect-feed. Direct-feed mobile crushers receive the material from front-end loaders, without using a feeder. If the front-end loader can not reach the top of the receiving hopper, an access ramp is used. The ramp can be part of the crusher assembly, moving together with the unit, or it can be an independent structure, moved on skids or on crawlers.
Indirect-feed crushers receive the material via feeders, usually of the heavy-duty, apron type. In many cases, the receiving hoppers are located at a lower elevation than the crusher inlet, and the material is fed into the crusher via an inclined feeder.
Crushed material is collected under the crusher, on a short apron or belt conveyor, which usually discharges onto a cantilevered swiveling conveyor. The swiveling conveyor delivers the material to a self-propelled bridge conveyor, which forms a connecting link between the mobile crusher and a shiftable conveyor and provides flexibility in operation.
Mobile crusher units usually come complete with dust collection systems, power substations, control panels, access platforms, stairs, means for weather protection, and a hoist structure, all of which add substantially to the weight of the units.
In over 50 installations throughout the world, loader-mobile crusher-belt conveyor systems have proved to be cost-effective.
The decision whether to use a mobile crusher unit at the open pit or a conventional fixed crusher installation located elsewhere at the mine site must be made during the planning phase of the mining project. The decision will depend on many factors, including the type of mineral to be mined, the size reduction required, the annual capacity, operating schedule, and life span of the mine, the distance from the mine pit to the delivery point, and the difference in elevation between these two locations.
Mobile Crusher Installation Design
To determine the most efficient crushing and transportation system for a mining project requires a detailed engineering study which investigates all of the pertinent factors. As part of a study, we compared mobile crusher systems with stationary crusher systems and investigated several alternative systems for crushing and transporting limestone from the face of the mine pit to a screening station. Our investigation included visits to several mobile crusher installations in Europe, where we observed mobile crushers in operation and talked with plant personnel who had operated both mobile and stationary crushing systems.
We present below some of the conclusions of our engineering study and we also discuss the effects which the subsequent inflation and higher energy costs have had on the projections we made in the study.
In our mobile crusher system concept, the blasted limestone, 1500 x 0 mm (60″ x 0), is charged by front-end loaders into the receiving hopper of the crusher and conveyed, via an apron feeder, to the impact crusher. The crushed limestone, minus 120 mm (-5″), is collected on a discharge conveyor under the crusher and transferred to a slewing conveyor. The slewing conveyor discharges the material onto a 1050-mm (42-inch) bridge conveyor which moves on crawlers. The material continues to the screening station, via shiftable conveyors 1 and 2 and stationary conveyors 3 and 4.
In our stationary crusher system concept, the blasted limestone is loaded by 5.4 m³ (7-cubic yard)shovels into 36-T (40-ton) rear-dump trucks. The trucks carry the limestone to a stationary crusher located outside the pit. The crushed limestone is conveyed a short distance to the screening station by a 1050-mm (42-inch) conveyor.
The economic evaluation of mobile crusher systems versus stationary crusher systems which we made in our study revealed the following facts about mobile crusher systems:
- The design of mobile crushers has advanced to the point where they are as rugged and as reliable as stationary crushers. In Europe, owners who have operated both mobile and stationary crushers prefer the mobile units.
- By eliminating the need for truck drivers, mobile crushers reduce mine manpower requirements and thereby increase mine overall productivity.
- With truck and shovel waiting time eliminated by use of mobile crushers, less idle time is experienced.
- Mobile crusher systems are more economical to operate than stationary crusher systems.
When we made the study, we did not anticipate the rapid increases in the costs of energy and labor which we have experienced since. The revised escalation curves adjusted for these increased costs. It can readily be seen that the yearly cost increases projected for mobile crusher systems are lower than those projected for stationary crusher systems.
If you compare the fuel and labor cost increases for a mobile crusher system with those for a stationary crusher system.
These constantly increasing costs make it more and more costly to operate stationary crusher-truck haulage installations. On the other hand, mobile crusher-belt conveyor system installations, being far less subject to these constantly increasing costs, are more economical to operate. Therefore, mobile crushers, used in conjunction with belt conveyor systems, should be seriously considered when planning new mining facilities. They should also be seriously considered when planning to increase efficiency in existing mining facilities.
High-Capacity Mobile Crushers
The economies and flexibility of mobile crusher installations discussed above have raised the question of how these advantages can be introduced in mining operations where crusher capacities of 4000-6000 metric tons per hour are required and where only large gyratory crushers can be used.
The best way to utilize the economies and flexibility of mobile crushers in such operations is to use a semi-mobile gyratory crusher unit, located in the mine pit but at some distance from the blasting and digging area. This separation of the crusher unit from the digging area is dictated by the high crusher capacity required. If the crusher unit operated in the digging area, the shovel or front-end loaders would not have enough room to feed directly to the crusher the large tonnages required. Therefore, the semi-mobile gyratory crusher unit is located at a relatively short distance from the blasting and digging area and is fed by trucks.
The trucks are rear-dump trucks, which are loaded by shovels or by front-end loaders, as in conventional operations. The trucks carry the blasted material from the blasting area to the crusher. It is important that the mining operation be planned so that the trucks have to travel only relatively short distances and that they do not have to negotiate prolonged haulage uphill. The semi-mobile crusher units are designed in such a way that they can be fed by rear-dump trucks.
Every six months to two years, depending on the progress of the mining operation, the semi-mobile crusher unit is moved from one operating location to another, by means of an independent transport mechanism.
Several European manufacturers are actively engaged at present in the designing phase of larger high-capacity, semi-mobile crushers. To give an idea of the direction this planning is taking, we present below descriptions of three different approaches for using semi-mobile crushers in high-capacity mines.
Fig. 9 shows a semi-mobile crusher unit, with a gyratory, operating adjacent to a specially built embankment. The crusher is fed by rear-dump trucks, which drive on the embankment and can converge on the crusher from three directions. The crushed material is collected on an apron conveyor under the crusher and is transported to a location outside the pit.
As the mining operation progresses, the distance from the truck loading area to the crusher unit increases to the point where it becomes more economical to relocate the crusher in order to shorten the truck haulage distance. At that point, a new embankment is prepared, and the crusher is moved to the new location, by a hydraulically operated walking pad mechanism or by an independent heavy-duty crawler-transporter like the ones shown in Fig. 10. This type of transporter has been recently developed for transporting heavy equipment in the lignite fields of West Germany.
The transporter rides under the crusher supporting structure, lifts the entire assembly approximately 0.6 m (24 inches), and carries it to the new location. The carrying platform of the crawler-transporter rests on jack cylinders which absorb the vertical forces of the load, and is guided by a center pin which absorbs the load’s horizontal forces. When loaded, the crawlers man transporter exerts a soil pressure of 20 N/cm² (28 psi) and can travel about 12 m/min (40 feet/minute). Unloaded, it exerts a soil pressure of 5 N/cm² (7.0 psi) and can travel about 25 m/min (80 feet/minute). It can move on difficult terrain and can negotiate slopes of up to 10%. A hydraulic system, driven by a diesel engine, provides the power for lifting and travel. In addition to moving semi-mobile crushers, the crawler-transporter can move other heavy equipment within the mine, such as transformers, drive and tail sections of shiftable belt conveyors, and miscellaneous equipment components.
The crawler-transporter is the largest commercial unit now available and can carry loads of up to 1000 metric tons. To move semi-mobile crushers heavier than 1000 metric tons, two or three crawler-transporters can be used. Crawler-transporters with capacities greater than 1000 metric tons are now being designed in Europe.
A second type of semi-mobile crusher unit consists of two sections: the feed section and the crusher section. The feed section consists of a feed hopper for receiving material from rear-dump trucks, an apron conveyor for elevating the material to the crusher, electrical gear, and a supporting structure. The crusher section consists of a gyratory crusher, loadout conveyor, spillage conveyor, dust collector, and supporting structure. While in operation, each section rests on pontoons, and the two sections are docked together to form one operating unit.
Fig. 11 shows the feed section of this type of semi-mobile crusher as it is being moved to its operating position on four wheel assemblies. Each assembly consists of a hydraulically propelled wheel, 2.8 m (9.2 feet) in diameter, and a hydraulic lift cylinder. During operation, the wheel assemblies are retracted or removed, and the feed-section rests on a supporting structure. The wheel assemblies are bolted to the feed section and can be detached and used to move the crusher section.
The two sections of semi-mobile crushers can also be moved by the fork-lift, piggy-back transporter shown. A hydraulic system, driven by a diesel engine, powers the lifting and steering cylinders and the hydraulic motors for propelling the wheels. The transporter is positioned under one of the sections of the crusher unit. It lifts the section approximately 0.6 m (24 inches) and carries it, piggy-back fashion, to the new location, where it lowers the section into operating position. The same procedure is followed for the second section of the crusher unit. When loaded, the transporter can travel about 360 m/h (1100 feet/hour) and can negotiate slopes of up to 10%. Today, fork-lift, piggyback transporters are available for service loads of up to 1000 metric tons.
The third type of semi-mobile crusher unit, also consists of a feeder section and a crusher section. The crusheris a coal breaker, but a gyratory crusher can also be used if the inclined feeder is made long enough to accommodate the greater height of the gyratory crusher.
As in the case of the two semi-mobile crusher units described immediately above, the material is transported from the mine face to this crusher unit by rear-dump trucks. The trucks dump the material into the hopper of the feeder section, which rests in a specially excavated trench and which has a capacity equal to the capacity of three trucks. The material is conveyed from the hopper to the crusher by a heavy-duty apron feeder. The crushed material is transported by belt conveyors to a point outside the mine pit. When it becomes necessary to move the crusher unit to a new location, the two sections are moved separately by crawler-transporters or by specially designed stradle carriers.
More on mobile-crushing and large in-pit machines.
Operation of Mobile Crushing Plant
Fujiwara quarry of Cnoda Cement Co., Ltd. is located at the northern part of Mie Prefecture, in central Japan, and it has been operated since 1932.
Present limestone production is approximately 4 million tons per year. The products are delivered for Fujiwara plant, located at 2 km east of the quarry.
Present production rate is 350,000 tpm, but capacity of facilities, after “Central-shaft MCP” mining system was introduced, is 400,000 tpm.
The Fujiwara quarry has two quarries, upper quarry (elevation of 780 m above sea level) and lower (500 m above sea level). The upper quarry was developed in 1977 for installation of MCP. Recently the production ratio between the upper and lower quarry is 97:3 ; the MCP crushes the majority.
Coarse rock is crushed to minus 250mm and then dropped into the shaft by a spreader. From the shaft, the crushed rock is extracted by a roll feeder, installed at the bottom of the shaft, and is fed onto a belt conveyor. Materials, conveyed by belt is fed to a secondary crusher and reduced to minus 110mm. Crusher discharge is again conveyed by belt conveyor to the intermediate stockpile (capacity; 120,000 t).
However the MCP was adopted at Fujiwara Quarry for the various reasons as follows.
- Cost reduction
- High productivity
- Simplification and reduction of the underground structure
- Protection of the shaft wall
- No attendant underground
At the start, because of initial trouble, a large amount of trouble time occurred for one year. Some defects are vibration, graveles dropping from pan-conveyor’s chink, breaking of drive shaft of the apron conveyor’s reduction gear, and breakdown due to overheating in the bush of the apron conveyor’s intermediate shaft..
Shot limestone is pushed and dropped by bulldozers from the face to the lower loading space through an open chute. Front-end loaders load this piled rock under the open chute and carry it to the MCP.
In this mining method, if the haulage distance to MCP is over 150 m, MCP is moved to the piled rock to shorten the haulage distance and a shiftable belt conveyor is installed between MCP and shaft. Operating period of one block is from one and a half to two years.