The Mineral Processing Flowsheets shown on the following pages are based on actual data obtained from successful operating plants. Metallurgical data are shown in these flowsheets which incorporate Crushers, Grinding Mills, Flotation Machines, Unit Flotation Cells, and Selective Mineral Jigs as well as other standard milling equipment.
The Flotation Machine, the Selective Mineral Jig and the Unit Flotation Cell have revolutionized flowsheet design and have made it possible for both small and large plants to increase recoveries and economical return. The Unit Flotation Cell and the Selective Mineral Jig have been perfected to meet the most important principle in ore dressing.
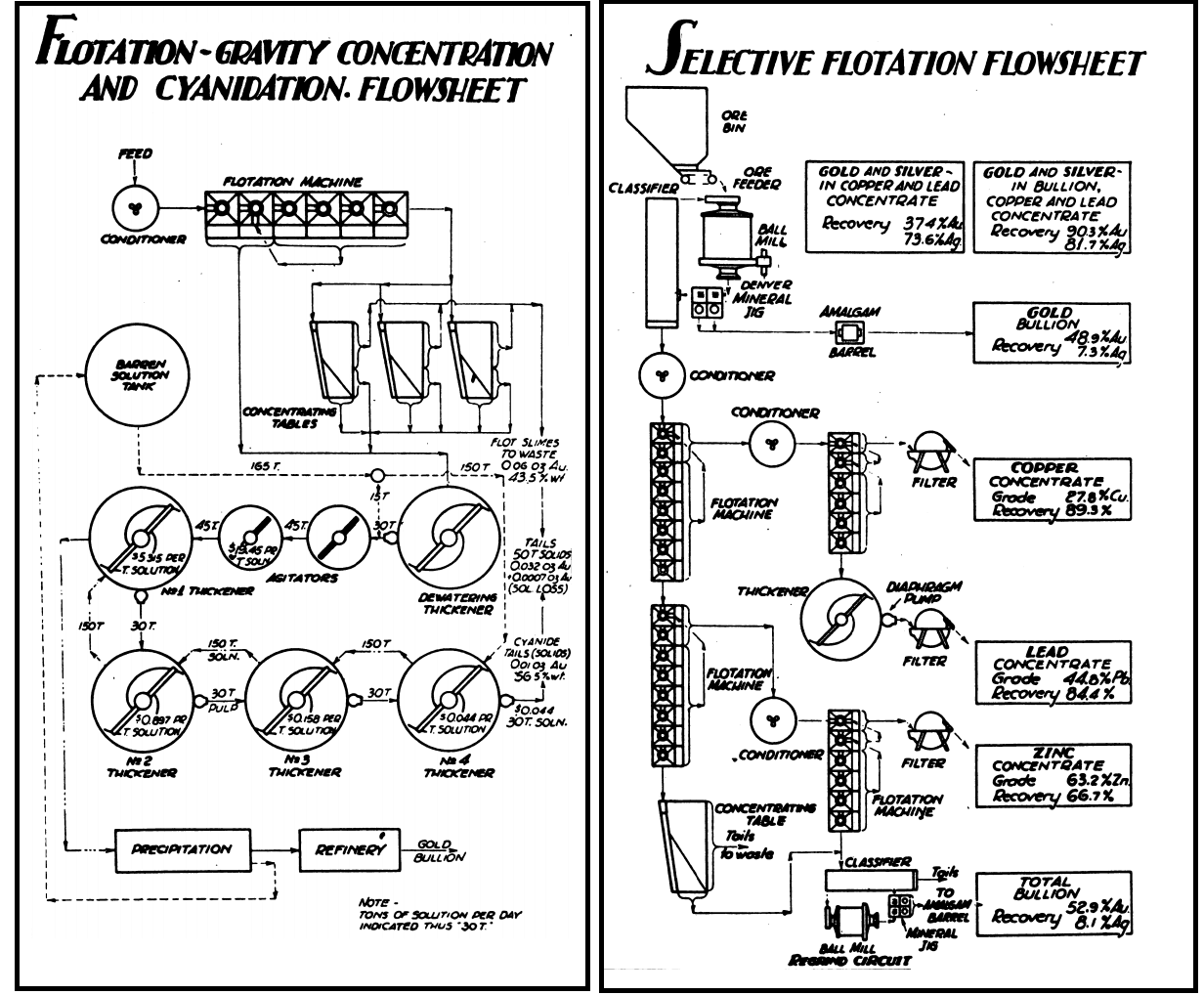
“Recover Your Mineral As Soon As Liberated!“
To recover this free mineral, either the Unit Flotation Cell or Jig or both can be installed in the grinding circuit without auxiliary equipment such as pumps or elevators, and for successful operation do not usually require more water than necessary for classifier dilution.
These flowsheets also show some other more important arrangements made possible with standard Machines.
Many of the flowsheets given here have been made possible because of the fact that a coarse pulp (particles as coarse as 1/4″) can be circulated in the “Sub-A” Flotation Machine without sanding or choke-ups and with high metallurgical efficiency.
“Sub-A” Flotation Machines have the gravity flow principle and flexibility that has made possible the development and application of many of these flowsheets. In fact, the elimination of pumps in handling concentrates for cleaning and recleaning has simplified flowsheets and reduced operating expenses to the operator’s advantage and profit. It should be pointed out that it is not only the cost of pump wearing parts but the time lost in shut-down for pump repair that is important in profitable mill operation.
The basic principles illustrated and described here can well serve as basis for other ideas that will increase recovery or add to the simplicity of mill operation.
Intelligent ore testing can be the difference between a sound business investment in a mining operation and a highly speculative “venture.”
Ore Testing takes the guesswork out of answering the question of “can this ore be milled profitably.” It also gives conclusive answers to the subordinate- questions of “what type of flowsheet will give the greatest net return on this operation, and can increased value and/or increased mill capacity be obtained by the addition or substitution of equipment in the mill?”
In other words, ore testing is the key to the basic question of the economic possibility of a mining operation. It gives the answer to this question at a minimum of expense without making a costly investment in equipment to learn it the hard way.
TABLE OF CONTENT – LIST OF PROCESS FLOWSHEETS
All of these circuits are field tested.
- Sequential Selective Flotation Process Flowsheet
- Flash Flotation Circuit – 2 Product Processing
- Straight Flotation Flowsheet – 1 Product
- Selective/Sequential Flotation Flowsheet of 3 Products
- Coarse Flotation, Gravity and Regrind
- Closed Circuit Flotation with Regrinding Flowsheet
- Flotation & Shaking Tables with Open Circuit Ball Mill
- Flotation & Cyanidation Leaching of Concentrate
- Flotation, Gravity and Tailings Cyanidation Leaching Circuit
- Flotation of Cyanide Tailing
- Ball Mill Grinding with Gravity Gold Revovery & Flotation Circuit
- Coarse Flash Flotation Circuit
- Flash Flotation with Whole Ore Cyanidation Leaching
- Coarse Sulphide Flotation with Gravity Gold Recovery Circuit
- Gold Jig and Shaking Table with Amalgamation Treatment
- Gold Mineral Jigging followed by Flotation
- Gravity Gold Recovery from Flotation Concentrate Process Flowsheet
- Coarse Gold Jigging & Coarse Sulphides Float with Fine Gold Rich Base Metal Flotation
- Recover Gold by Jigging in Grinding Circuit
- Gravity Gold with Amalgamation and Cyanide Leaching Extraction
- Gravity Circuit by Jig and Whole Ore Cyanide Leach
- Continuous counter-current decantation cyanidation flowsheet
- Gold Recovery by Batch Cyanide Leaching Plant
- Portable Tungsten Processing Plants
- Tungsten Extraction Process Flowsheet
- Tungsten-Gold Extraction Flowsheet
- Portable Lead and Zinc Flotation Plant
- Portable Bulk Flotation Plant with Gravity Gold Circuit
- Crushing Plant Flowsheet & Design-Layout
- Manganese Gold Process Flowsheet
- Manganese Ore Processing Plant Flowsheet
- Flowsheet of Manganese Ore Beneficiation Process Plant
- Gold Process Plant Flowsheet
- Oxide Lead Pb Process Flowsheet
- Fluorspar Extraction Processing Flowsheet
- Flowsheet of Copper Extraction Process by Froth Flotation
- Sulphur Process Flowsheet by Flotation
- Extraction of Molybdenum by Flotation
- Chromite Process Flowsheet
- Feldspar Processing Plant Flowsheet
- Mercury Process Recovery/Extraction Circuit Flowsheet
- Scrap Metal Recycling Process Flowsheet
- Silica Ore Extraction Process Flowsheet
- Coal Processing Plant Flowsheet
- Coal Flotation Machine
- Flotation Deinking for Paper Recycling
- Foundry Sand Reclamation Process
- Designs for Small Portable and Mobile Gold Leaching Plant
- CCD Counter Current Decantation Cyanide Gold Leaching
- Gravity Recovery OR Flotation Circuits ahead of Gold Cyanide Leaching
- Gold Cyanidation Circuits
- Cyanide Processing Equipment and Plant Configuration Options
- Small Gold Processing Plants
- Small Gold Ore Processing Plant
- Ore Processing Plant & Equipment
- Base Metal Ore Processing Plant & Equipment (Copper & Lead+)
- Gold Leaching Plant for Sale
- Small 50 to 75 TPD Process Plant Design & Equipment List
- 100 to 125 TPD Process Plant Design & Equipment
- Process Equipment List for a 50 Tons Per Day TPD Flotation Plant
- Mobile Ore Processing & Beneficiation Plant
- Gold Extraction Processes
- Design and Construction of Small Mineral Processing Plants
- Barite Beneficiation Process and Plant Flowsheet
- Slurry Distributors
- Types and Models of Sample Cutters & Samplers
- SRL Pump Types and Parts
- Types of Agitators
- Small Mineral Processing Plant Design
- Concentrator Metallurgical Continuous Sampling Analysis
- How to Make Gravel and Sand
- Silver & Cobalt Processing by Gravity and Flotation
- Chemical Smelting
- Solvent Extraction Process SX Theory
- Solvent Extraction Training SX Course
- Kyanite and Sillimanite Beneficiation Process
- Mini Portable Gold Process Plant
- Assay Laboratory Equipment
- Laboratory Conditioner
- Types of Bearings
- Flotation Blowers
- Types of Ball Mill
- Reagent Emulsifier
- Rock Crushers Types and Capacities
- Types of Classifiers in Mineral Processing
- Laboratory Crushers
- Laboratory Cyanide Leach Plants
- Mercury Amalgamation
Selection of Treatment Process
The results obtained through ore testing and the intelligent interpretation of the results very often lead to a simple method of treatment giving good profits, where some other treatment might mean less profit or an actual deficit. Our Lab gives a good illustration of what proper selection of treatment methods based on ore testing can result in. Test results give you facts.
Data from ore testing not only allows determination of the proper method of treatment, but gives a sound basis for the selection of the proper equipment to be included in the flowsheet.
The 911MPE Process Equipment Ore Testing Laboratory is continually being confronted with and solving such problems. Very often situations arise where the most common methods of treatment may not be successful but little known and ingenious methods may be applied. The flowsheet showed the results obtained from testing a complex lead-zinc-copper-iron ore containing values in gold. Exceptionally high grade and recovery were obtained in this instance. Utilizing a patented process special reagents made profitable production of lead/copper and zinc-iron concentrates and subsequent separation of these concentrates into four (4) separate products.
Although flotation has made profitable the bene-ficiation of many low grade ores both metallic and non-metallic, it is not always true that flotation will give the greatest economic retiirn. For instance, in many cases, cyanidation of gold ores either direct or as part of a composite method of treatment may be the answer to the question of, “what treatment will give the greatest dollar value return on the mill investment ?”
Ore testing gives definite and conclusive answers to the following type of metallurgical question.
An ore sample was received at the 911MPE Equipment Laboratory of a character which would ordinarily respond to the counter-current decantation method of cyanidation for extracting gold. Samples of the Same ore gave results concurring with test work by others but this method was not recommended due to settling difficulties encountered.
Work was not stopped here, however. Eventually, a successful method for treating this ore was found by sacrificing a small loss in slime. The final flowsheet evolved with recoveries indicated which made profitable installation of a reasonable cost plant, overcoming the difficulty arising from the physical characteristics of the ore.
Increasing Profits in Operating Mills
Very often it is possible to improve recoveries in a mill which is already operating, by instituting new techniques or altering the flowsheet. There are many possibilities of such improvement.
Change of reagents in a flotation circuit may give higher recovery, a better grade of concentrates or both. A “Sub-A” Unit Flotation Cell installed in the grinding circuit may permit an increase in tonnage milled, a decreased loss in slimes and a better overall recovery.
A Mineral Jigs installed in the grinding circuit in cyanide mills have proved very successful in increasing recovery. It is always advisable to recover your mineral values as soon and as coarse as possible.
Net return of an operation may be increased by production of bullion at the mine instead of shipping ore, or by the treatment of concentrates.
Process Flowsheet Selection
From the many hundreds of flowsheets reviewed and based on test work and from operating plants throughout the world, we present a few of the more typical ones for your information and guidance.
Many of these flowsheets are in use in various plants and others present a composite of the good features of many successful installations.
Typical flowsheets are shown for both metallics and non-metallics as well as industrial products, wastes, etc. De-inking of waste paper by flotation, for example, is coming into prominence with Flotation Cells as it is now possible to recover for the paper industry a useful and usable product on a much more attractive basis than in the past.
Your flowsheet should be designed without “bottlenecks” or weak links which present problems that can seriously effect operating efficiency. The old saying of “one hour’s delay means no profit today” is more true today than ever before due to higher operating costs. This adage emphasizes the importance of having your flowsheet designed efficiently and tailored for your specific operation, and the need for selecting standard reliable equipment designed to give you continuous service.