Table of Contents
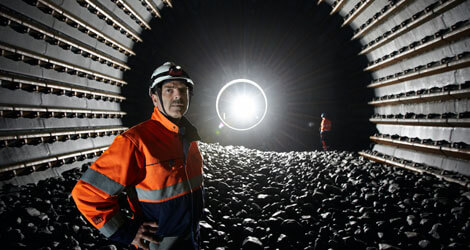
There are basically two groups of Grinding Mill Liners. Ones with a HIGH PROFILE and those with a LOW PROFILE. The high profile liner is designed to give the media the higher lift. This type will be used in mills that are designed for primary grinding and as a result require the impact of the higher cascade. Ball mills working as the secondary portion of a grinding circuit will utilize the lower profile liners. The reason is as lift decreases, friction increases. To function effectively they need this type of grinding action to obtain the maximum contact of their high surface area. There are two other factors that the liner design must accommodate other than the degree of lift. The TYPE of grinding media and the SIZE of the media. To do this, there have been developed different liner profiles, RIPPLE LINERS, WAVE LINERS, SINGLE STEP LINERS, DOUBLE STEP LINERS, SHIPLAP LINERS and LIFTER BARS. These are also known as a KICKER BAR LINERS. The important measurements being the WIDTH of the valleys, the HEIGHT of the lifting portion of the liner and the overall THICKNESS of the liner.
(A liner takes up space and will reduce the tonnage accordingly.) When a mill is being designed, the type of liner that will be used is’ very important. The wrong liner design will increase power and steel consumption, as well as reduce the grind and throughput of the mill.
Liners not only come in different designs, they are available constructed from different materials. Liners may he built from MANGANESE STEEL for rod mills and ball mills that use bigger than two inch balls. Or they may be what is known as CHILLED CAST IRON LINERS. This type of liner have their own content formulas and are cast in their own manner as well. An example of such a liner is the NIHARD LINERS. In the last few years RUBBER LINERS for secondary grinds have also been used with some success.
For an operator the biggest effect that the liners will have on his job will be the result of wear.As the liners wear out the lifting portion of the liner will be reduced until the liner has a lower profile.
This means that the cascade of the media will become flatter as the as the leading edge of the lifter wears away. The amount of unground material will slowly increase until the mill can no longer grind the bigger ore. When this happens the liners will have to be changed.
If you ever have to start up a mill that has had a complete liner change I would suggest starting at a reduced tonnage and slowly bring the tonnage up to its maximum. This is because the new liners may have too much lift and literally throw the media across the mill spoiling the cascade action. Once the LEADING- EDGE of the liner has worn off a bit you will be able to increase the tonnage again. You will notice that the grind will continue to improve due to the liners slowly wearing away providing a longer retention time for the ore to be processed in. This of course has a limit, once the liners wear past a critical size the efficiency of the mill will slowly deteriorate until the liners are completely worn out requiring replacement.
Grinding Mill Rubber Liners
This system combined rubber plates with cast manganese lifter bars which “assures that the major portion of the surface of the mill will be protected with an abrasion -resistant resilient surface under compression and that the remaining portion of the lining will be capable of sustaining the lifting load, will maintain a uniform lift and will resist abrasion “.
Today’s rubber mill liners have built up from these origins and rubber liner manufacturers have worked closely with the mill operators to develop better compounds and better designs to provide the best liner system for each application.
Rubber liners are not the perfect solution to all grinding applications as you well know, however rubber does have several features that make it an attractive material.
Abrasion Resistance: Today’s rubber compounds are specifically designed to resist wear by abrasion. The success has been well documented in regrind mill applications where rubber has outlasted cast metal liners and given better cost effectiveness.
Impact Resistance: This feature is more important in the larger grinding mills. Rubber liners absorb the impact of the larger grinding media and thus protecting – the mill structure and prolonging it’s life.
Weight: Rubber weighs about 15% of an equivalent volume of steel. This means that a rubber liner system reduces the load on the mill structure and also reduces the basic power draw. Another benefit is that liner components are lighter, easier and safer to handle. A major factor in today’s milling operation where fewer people are available for liner changeouts.
Noise: Noise control is becoming a major factor in the workplace and rubber mill liners result in a quieter environment, particularly in primary mills with larger grinding media.
Tight Seal: Because rubber liners can be produced to relatively close tolerances and rubber is deformable, a rubber liner system is designed as a tight liner. This protects the structure of the mill from any abrasive or corrosive wear. Another very important side benefit for gold operations is that the amount of free gold trapped between or underneath the liners is significantly reduced.
Flexibility: This feature of rubber is particularly significant in the use of rubber for grate discharge mills. The natural flexibility of rubber reduces the potential of blinding the grates. This will be discussed in greater detail later in this paper.
The design of rubber mill liners is very specific to the grinding application and will not be covered in this paper. Instead, three design concepts based on rubber as a lining material will be discussed. These are combination liners, rubber grates and rubber covered pulp lifters.
Rubber & Steel Combination Liners
Long ago, it was recognized that there were grinding applications where rubber alone was not effective. The patent for the combination liner was issued for a design that extended the use of rubber into those applications. Although rubber technology has improved, there are still applications today where rubber alone is not effective and the combination liner is successfully used. These applications include semi autogenous mills and primary single stage ball mills.
The revised and updated design of a combination liner is a rubber plate with a separate metal lifter bar. Most of the volume of the liner is rubber so that the features and benefits of a rubber liner are retained. This plate can be either a plain contoured slab liner plate as shown or it may have a molded intermediate rubber lifter if required due to the chordal spacing, the size of the grinding media and feed.
The rubber plate is held in place by the metal lifter bars. A metal spacer sits between the rubber slabs and lifters to keep the liner from shifting. This spacer is usually made of low cost mild steel and is a one time item as it does not experience any wear and does not need replacing. This results in significant cost reduction of the liner system.
The metal lifter bar design is generally a function of the grinding application and mill size. The cross section however must retain two critical dimensions. The first is that the lips or edges of the lifter that extend over the rubber plates must be kept at a minimum of 25 mm to provide adequate clamping of the liner plates by the lifter.
The second critical dimension is the depth of the base. This should also be a minimum of 25 mm to prevent any lateral displacement. The base of the metal lifter must also be a flat smooth surface in order to properly seat on top of the metal spacer. The lifter bar is bolted through the shell with oval head taper grade 5 forged bolts.
This design has several important benefits. First, the amount of scrap loss in metal lifter bars at change out is kept to a minimum through the use of the mild steel spacer. The spacer also provides a solid base for the lifter so that the liner bolts can be properly torqued down. The second benefit of this design is that there is no metal in the rubber plates, as the lifter is supported by the permanent metal spacer. This simplifies the manufacturing of the rubber liners, and makes the plates lighter and easier to handle on installation.
The metallurgy of the lifter bars must be carefully matched to the grinding application. In mills with high impact such as large SAG mills, a high impact resistant Cr-Mo steel is required. In applications of low impact, the more abrasion resistant, castings such as Nihard are utilized to achieve maximum life through high abrasion resistance.