Table of Contents
The gold sluice box is an efficient alternative to panning for gold, allowing the prospector to quickly sift through a much greater volume of sediment. Although many affordable varieties are available to purchase, they are even more affordable to build. With a little knowledge, skill, and creativity, a prospector can build a custom sluice box from almost any type of solid material available.
First, the prospector/builder of gold mining equipment must understand how sluice boxes work. The boxes mimic a stream bed, allowing water and sediment to wash over it and deposit denser objects along the parts of the stream where the water moves more slowly. Imagine a current of water or air moving over a surface. The current slows down when it is forced to move around or over an object, and this is where the dense particles settle out of the current. For example, when sand or snow is carried off of the ground by wind, the air current slows down when it encounters a fence. The heavier particles are deposited, leaving a trail on the opposite side of the fence; whereas the lighter ones remain in the current. Another example is when a current is forced through a winding path. It will slow down when it hits each curve, and the heaviest particles will be deposited there; whereas the lighter ones remain in the current. With this concept in mind, one can envision a variety of sluice box designs.
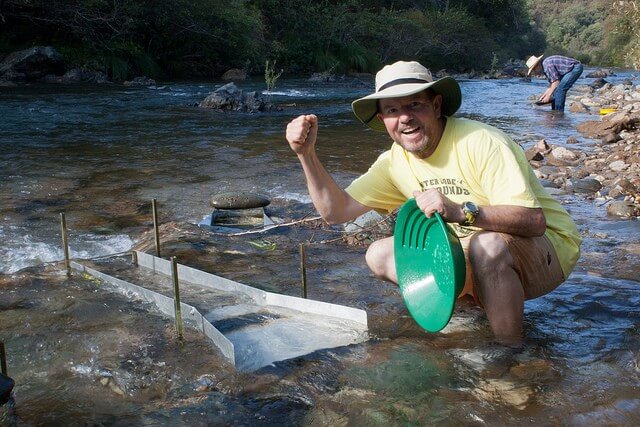
Regarding the actual construction of the box, you will need at least part of it to be submerged in the stream at a slight angle, so that you can take advantage of the natural current to wash the particles through the box, and the box must be held in place either by posts or by a heavy rock or two. You will need a section, either above the main part of the box, or right next to it (as in the photo above), where the sediment can be dumped into the box. Also before designing the sluice box, it’s important to know that boxes less than four or five feet in length have been shown to be just as effective as longer boxes.
Finally, one must take into consideration the types of materials available to build the box, the design that is most conducive to trap the gold particles that are being sought, and even ergonomic aspects that will make the process most comfortable for the prospector. Sluice box designers have incorporated riffles, curves, and even carpet to catch the finest particles. They maybe magnetized in areas to catch tiny magnetic minerals to which gold particles are sometimes attached, and may be made out of materials such as wood, plastic, aluminum, or a combination of them. Before designing your box, take into account all of the options and do a bit of research on the size and type of gold particles that are common in the deposit.
Sluice Matting: Rubber and Corduroy
Rubber Matting, as shown in the illustration at left, is used in placer and mill operations, replacing blankets for recovering coarse and fine gold. The innumerable small recesses catch and retain the values, particularly in the fine sizes. Rubber Matting is very easily washed, a fact which simplifies its clean-up. It is so tough that its life is many times that of ordinary blankets. Full rolls are 24 inches wide by 50 feet long; weight of full rolls is only 100 lbs., for ease in handling, but any length is available. This Rubber Matting can be furnished on a continuous belt concentrator similar to a vanner, with water sprays for the removal of the concentrates. This unit is built two feet wide and can be furnished in any length required to meet specifications for a particular operation.
Corduroy Matting is made up of strongly ribbed fabric material. It is widely used by the mining industry for gold recovery in sluices, launders, and on tables. Both a wide rib, best suited for placer undercurrents, and a narrow rib, designed for ground ore treatment, can be obtained in a width of 36″ and in any lengths desired. The weight is approximately one pound per yard of length.
Gold Sluice Fabrication
A sluice is generally defined as an artificial channel through which controlled amounts of water flow. Sluice box and riffles are one of the oldest forms of gravity separation devices used today (Photo 3). The size of sluices ranges from small, portable aluminum models used for prospecting to large units hundreds of feet long. Sluice boxes can be made out of wood, aluminum, plastic or steel. Modern sluices are built as one unit although sluices formed in sections are still used. A typical sluice section is 12 feet long and one foot wide. As a rule, a long narrow sluice is more efficient than a short wide one. The sluice should slope 4 to 18 inches per 12 feet, usually 1-1/8 to 1 -¾ inches per foot, depending on the amount of available water, the size of material processing, and the size of the gold particles.
The riffles in a sluice retard material flowing in the water, which forms the sand bed that traps heavy particles and creates turbulence. This turbulence causes heavy particles to tumble and repeatedly exposes them to the trapping medium. An overhanging lip, known as a Hungarian riffle, increases the turbulence behind the riffle, which agitates the sand bed, improving gold recovery (Figures 3-5). Riffles can be made of wood, rocks, rubber, iron or steel, and are generally 1-½ inches high, placed from one-half inch to several inches apart. The riffles are commonly fastened to a rack that is wedged into the sluice so that they can be easily removed. Mercury may be added to riffles to facilitate fine gold recovery, but its escape into the environment must be prevented.
In addition to riffles, other materials are used to line sluices for enhanced recovery. In the past, carpet, corduroy, burlap, and denim were all used to line sluices to aid in the recovery of fine gold. Long-strand Astro-Turf, carpet, screens, and rubber mats are used today for the same purpose (Photo 4). In Russia, some dredges use sluices with continuously moving rubber matting for fine- gold recovery (Zamyatin and others, 1975).
To perform efficiently, a sluice needs large amounts of clean water. Enough water should be added to the feed to build up a sand bed in the bottom of the sluice. For maximum recovery, the flow should be turbulent, yet not forceful enough to wash away the sand bed. Russian studies have shown that recovery increases with the frequency of cleanups. On one dredge, gold recovery was 90% for 12-hour gold cleanups and increased to 94% when sluices were cleaned every 2 hours (Zamyatin and others, 1975).
For cleanup, clear water is run through the sluice until the riffles are clear of gravel. A pan or barrel is placed at the discharge end to prevent loss of concentrate. Starting from the head of the sluice, riffles are removed and carefully washed into the sluice. Any bottom covering is removed and washed into a separate container. Cleanup continues until all riffles are removed and washed. Large pieces of gold should be removed by hand, then the concentrate is washed out of the sluice or dumped into a suitable container. The collected concentrate may be sent to a smelter but is usually further concentrated by panning, tabling, or a variety of other methods, including re-sluicing. After cleanup, the sluice is reassembled and more material is processed.
Gold recovery with sluices can vary depending on a number of factors. Fine gold losses can be minimized by cleaning up more frequently, reducing the speed of the slurry flow to 2 to 3 feet per second, and decreasing the size of the feed, usually be screening. Some operators have increased recovery by adding a liner to the sluice to trap fine gold, and others have lengthened sluices to increase the square footage of particle trapping area.
Overall, sluices are widely used today due to their low cost and availability. They have many advantages. They require little supervision and maintenance; they can tolerate large fluctuations in feed volume; they are portable; properly operated, they can approach a gold recovery of 90%; and they entail a minimal initial investment.
Disadvantages include: very fine particles of gold are not effectively recovered; frequent cleanups are required; sluices can not operate when being cleaned; and large volumes of clean wash water are needed. Although some manufacturers offer sluice boxes, the majority of those in use are fabricated for specific operations, usually by local firms or by the individual.
How to Operate a Gold Sluice
A sluice is generally defined as an artificial channel through which flows controlled amounts of water. In gold placering, the sluice includes sluice-boxes which collect the gold by means of various configurations of riffles, corrugations, mats, expanded metal, or the like, which trap the heavier particles while allowing the waste to continue through. Figure 5 shows a portable
lightweight metal sluicebox suitable for test work or a small-scale placer operation. An important part of any sluicing operation is its water supply, and where water is not plentiful, pumps, pipelines, or even dams with special headgates may be required.
Small-scale sluicing by hand methods has been called quite appropriately shoveling-into-boxes. In contrast, in ground sluicing, usually a more efficient operation, most of the excavation is accomplished by the action of water flowing openly over the materials to be mined. In either case, the materials pass through a sluice, where gold is collected behind riffles. A variation of the sluicing technique, where water is stored and released against or across the materials intermittently, is called booming.
The sluicebox in its simplest form might be a 12-foot-long plank of 1- by 12-inch pine lumber, to which sides about 10 to 12 inches high are nailed, with braces secured at several places across the top. Larger sluices can be made with battens to cover joints between boards where gold might slip out, and with braces built around the outsides of the box for greater rigidity. To provide for a series of boxes, the ends should be beveled or the units tapered so that one will slip into the other in descending order and form a tight joint. Four to eight such boxes in series would be a typical installation.
Two men hand-shoveling into sluiceboxes can wash 5 to 10 times as much gravel as could be put through a rocker in a day. The slope of the sluice and the supply of water must be adjusted so that the gravel, including larger cobbles, will keep moving through the boxes and on out. Slopes of 4 to 12 inches per 12-foot box are normal, but if water is in short supply the slope may be increased. Trestles are necessary to support the boxes over the excavated ground, gulleys, or swales.
Inside the boxes, various kinds of riffles may be employed, depending upon the availability of material and personal preference. The riffles, which go on the bottom, are usually set crosswise in the box, but they can also be effective when placed lengthwise, the concentrates settling between them. They may be of wood, or of strap or angle iron, or a combination of the two. Straight, round poles or a pattern of square blocks or stones can serve for riffles. Rubber or plastic strips have even been used. Durability is important for prolonged operations, so wood may be armored with metal. Expanded metal, heavy wire screen, or cocoa mats make good riffles for collecting fine gold.
A common height for riffles is 1½ inches; they may be placed from one-half to several inches apart. Fastening the riffles to a rack, which is then wedged into place in the box. permits their removal. A tapered shape on the cross riffle, with the thinnest edge to the bottom, tends to create an eddying action that is favorable for concentration. Another way to achieve this eddying action is to cant the riffle or even just the top of the riffle. Burlap or blanket material is commonly placed under the riffles to help in collecting fine gold. Mercury may be added to some sections of the sluice if there is much fine gold, but care must be taken to prevent escape of the mercury.
Sluice cleanups should be made at fairly regular intervals. After running clear water until the sluice is free of gravel, riffles are removed in sections starting at the upper end. With a thin stream of water, the lighter of the remaining material is washed to the sections below. The gold, heavy sands, and amalgam, if mercury has been used, are scraped up and placed in buckets. This mixture then can be panned or cleaned up in a rocker to obtain a final concentrate or amalgam.
How to Feed a Sluice
It is common in a small operation, when feeding the sluice, to place a heavy screen or closely spaced bars of some sort across the section where the gravels enter, to eliminate the larger particles, which are probably barren anyway. The screen or bars (a “grizzly”) should be sloped so the oversize material rolls off to the side. The size of mesh or spacing will depend upon the gradation of feed, but would generally be in the range of ¼ to 1 inch, with 3/8 inch being a common size. In larger operations a rotating screen, or trommel, might be used. In a ground sluicing operation, possibly all materials would be run through the sluiceboxes. Provisions must be made for removing the oversize material, and, if required, stacking it away from the work area.
If the gravel contains much clay it may be desirable to use a puddling box at the head of the string of sluiceboxes. This may be any convenient size–for instance, 3 feet wide by 6 feet long, with 6- to 8-inch sides. The clayey material is shoveled into this box and broken up with a hoc or rake before being allowed to pass into the sluice. The importance of this step is that if allowed through the sluice, the unbroken clay lumps may pick up and carry away gold particles already deposited.
Usually, the shoveling-in method proceeds as follows: After the boxes are set, shoveling begins at an advantageous point. Experienced miners work out the ground in regular cuts and in an orderly fashion. Enough faces are provided so that shovelers will not interfere with one another. Provision is made to keep bedrock drained, and boulders and stumps are moved a minimum number of times. Cuts are taken of such a width and length that shoveling is made as easy as possible. The boxes are kept as low as possible so a minimum lift of gravel is necessary. At the same time an adequate slope must be maintained for the gravel to run through the boxes under the limitations of the available water. Allowance for dump room must also be provided at the tail end of the sluice. Leaks in the sluice are stopped promptly, and shoveling is done in such a manner that the sluice does not become clogged nor does water splash out. (Water in the pit hampers shoveling.)
All material of a size that will run through the sluice is shoveled in, and the oversize material is thrown to one side. Boulders from the first cut should be stacked outside the pit, on barren ground if possible. The width of a cut is usually limited to the distance a man can shovel in one operation. When shoveling from more than several feet away, it is best to set boards above and on the opposite side of the box; this increases the efficiency of the shovelers. The greatest height a man can shovel into a box is 7 to 8 feet, and above 5 or 6 feet the efficiency of the shoveler is markedly reduced. If the gravel is over 3 or 4 feet deep, it usually is excavated in benches to facilitate digging and to, permit the upper layers to be raised a minimum shoveling height. Where the gravel is shallow, wheelbarrows may be used. Another way is to shovel the gravel onto a conveyor belt that discharges into a trommel, discarding the oversize material and running the undersize material through the sluice. Where two or more persons are working in the same cut, the height of succeeding benches is governed by the character of the material being dug and the distance the gravel has to be lifted.
The sluice may be maintained on the surface of unworked ground or supported on bents on the opposite side of the cut. After the first cut the boulders are thrown onto the cleaned-up bedrock. Where cuts are run on both sides of the sluice, the boxes are supported on bents as the ground underneath them is dug out. At other places the boxes may be set on bedrock and the dirt may be shoveled into the head of the sluice from short transverse cuts at the upper end of the pit. Work usually begins at the lower end of a deposit so that bedrock may be kept drained, and then proceeds across the deposit by regular cuts. The length and order of the cuts will depend upon local conditions. As heavy sands and gravel build up deposits between the riffles in the sluice, it may be necessary to stir these up to prevent packing and the consequent override of gold particles. A tined implement such as a pitchfork is often convenient for this. Larger stones that lodge in the sluiceway may be similarly removed.
Supplying Water
The quantity of water available will influence the scale of operations and the size of sluice used. A minimum flow of 15 to 20 miner’s inches (170 to 225 gallons per minute) is required for a 12-inch-wide sluicebox with a steep grade. Smaller flows than this can be utilized by storing the water in some kind of reservoir and using the supply intermittently. A common practice followed where the quantity of water is limited is to use a grizzly or screen over the sluice to eliminate oversize material and thus increase the duty of the water. Reduction in the amount of material to be treated by first running it through a trommel to wash and screen out the coarse size is another effective way to lower the water requirements.
Water usually is conducted via ditch to the sluice. However, if the ground is rich enough it may be practicable to pump water for the sluice. The feasibility of obtaining a gravity flow should first be investigated, as the expense of pumping may be more than the cost of a long ditch, when the cost is distributed over the yardage of gravel moved. A suitable number of sluice-boxes or some other removal system may be used to transport the tailings to a dumping ground away from the working area. A tailings or settling pond may be required to maintain downstream water quality.
Ground sluicing utilizes the cascading effect of water to break down the gravel; hence, the requirements for water are much greater. The chief application of ground sluicing is to streambed deposits. Pipelines, flumes, or ditches would be necessary if ground sluicing were applied to gravels higher up on banks or terraces, and the larger scale hydraulic methods would then become more favorable. If booming is to be done, a dam and reservoir are needed. The dam is usually equipped with a gate mechanism that permits either automatic or manual control and quick release of the impounded water for maximum washing effect. The water may be passed over the upper face of a gravel bank or diverted against the bottom in order to undercut and carry away the gravel as the face of the bank breaks down. All materials are channeled toward the sluice.
The natural flow of a stream can be used by diverting the current with boards or simply with piled boulders. “Shears” can be constructed of 1- or 2-inch-thick boards 12 feet long nailed to pairs of tripods so that the boards slope back from the water flow at an angle of about 60°. The tripods are built in such a way that boulders can be piled inside the base to hold them in place. A row of these shears may be used to divert the force of the water against a bank, or two rows may be used to form a flume.
The seasonal nature of stream flow in different areas must be kept in mind when planning any placer operation. State and Federal agencies can provide information on stream runoff for many of the more important streams, information which will indicate the limitations in water supply that might be expected due to seasonal changes.