Table of Contents
Before processing by the gold refinery, gold can be extracted from ore by the following series of operations:
- Coarse crushing;
- Fine grinding;
- Straking for free gold;
- Flotation;
- Concentrate roasting;
- Straking for free, gold;
- Cyanidation of concentrates;
- Precipitation of gold from cyanide solution.
The last operation is performed in a Merrill-Crowe radial leaf type precipitator, to which zinc dust is fed continuously, together with a small amount of lead nitrate to form a lead-zinc couple that more readily precipitates gold than pure zinc alone. The resultant zinc slimes therefore contain as principal constituents; gold, silver, lead, copper, and zinc, in varying amounts, with minor quantities of other elements and radicals.
Part I describes the clean-up of zinc slimes from the Merrill-Crowe plant; then traces the history of the smelting processes used to separate the gold as far as possible from the base metals in the slimes.
Initially, in 1930, slimes were pressed in a leaf filter, acid treated with dilute sulphuric acid, roasted and smelted in Salamander crucibles using a simple silica-borax flux. By 1936, however, the copper content of ore had risen so much. that the bullion contained relatively large amounts of base metal, and caused a large increase in refining charges at the Mint.
The bullion was then granulated and sulphured with moderately satisfactory results. Later, however, with increases in mine tonnages, the work of granulating and sulphuring 15,000 to 16,000 oz. of bullion per month became too heavy and exhausting. Pyrite concentrates from the flotation plant were then added to the silica-borax flux, producing a bullion of satisfactory grade, and mattes containing quantities of gold and silver that were only partially recovered by re-melting with 20% soda ash.
Current practice still adheres to the matte smelt, which is therefore fully described herein. The matte smelting process was extended after 1943 to include recovery of metals from the matte and slag, and forms the subject of Part II of this report.
It will be noted that in the general ore treatment scheme, free gold is separated from the ore during fine grinding, and again after roasting of the concentrates, by passing over strakes covered with corduroy cloths. Recovery of the gold by amalgamation and retorting, although not properly a smelting process, is included after the description of smelting because it is an essential and highly important part of gold-room procedure.
Brief reference will also be made to the smelting of raw zinc slimes from a second plant of the Lake View and Star, Ltd., that recovers gold from old flotation tailings by cyanidation, filtration and precipitation.
- Recovery of Metals from Mattes and Slags
- By Products of Gold Refinery
- Slags
- Mattes
- Lead Bath Treatment of Matte
- Reduction of Mattes to Metals
- Cupellation of Base Bullion
- Treatment of old Furnace Liners
- Recovery from Cupellation Oxides
- Removal of Copper from Fine Gold
- Acid Treatment of Fine Gold
- Treatment of Roasted Slime with Sulphuric & Nitric Acids
- Treatment of Raw Slime with Hydrochloric & Sulphuric Acids
- Treatment of Roasted Slime with Hydrochloric Acid
- Treatment with Ferric Sulphate
- Smelting in Furnaces Lined with Carbon-Free Refractories
- Fusion of Gold Slime with Salt Cake
- Conclusion
Past Gold Refinery Practice
Clean-up
Zinc slime was collected in the Merrill tank over a period of about 10 days. On clean-up day, the inlet solution flow was stopped at 7.30 a.m. and the tank run out into a monteju that delivered to either of two Dehne Alter presses. Slime collected on the cloths was hosed down with a spray of high pressure water, and passed through to the press until the leaves were full, indicated by a cessation of liquid flow from the Alter. Air was then turned on the press until excess solution had been blown out, when the press was opened and the cake scraped out with wooden scrapers into rectangular galvanised tubs capable of holding about 220 lb. of moist slime, which contained approximately 33% moisture. It was then weighed and the net weight recorded.
In July, 1930, when the plant started, the filter cake was transferred to a lead-lined wooden vat containing warm dilute sulphuric acid of about 6% strength, and stirred by hand with a wooden paddle until action was complete. It was then filtered again through the same presses, washed with water, blown with air and again weighed before transferring to the muffle furnaces for roasting. Adding of the slime was stopped in 1933, because the treatment did not result in any loss of weight in the slime, nor improvement in bullion grade.
Each clean-up day, when the tank had been emptied of solution and slime, one man used to enter the tank and chip off a segment equal to about one-third of the area of the bottom. This was necessary because a layer of zinc dust, about ¼ in. to 3/8 in. thick, accumulated and had to be removed. The zinc chips contained gold, although in much smaller amounts than in the main slime. It was roasted and smelted in a similar manner, and with the pressed slime.
Cloths from the Merrill and Dehne presses were removed when holed, or coated too badly with gypsum. They were burnt in the muffle furnaces after the main roasting of slime was completed, and fluxed with the last smelting charge for the day.
Clean-up of the Merrill tank took approximately four hours, but slime was available from the presses by 10 a.m. It was transferred, after weighing, to the muffles for roasting.
Roasting
The first tub of slime was shovelled into, and divided between, four muffles, thus each contained about 50 lb. of moist slime per charge. The charge was spread evenly on the muffle hearth in a layer 1½ in. thick, using a hand rake, and the door was then closed to conserve heat to drive off moisture before roasting proper commenced. No attempt was made to rabble the slime until it was dry, because clouds of dust would be raised at one stage during drying. When the slime glowed red in a number of places, it was carefully turned over until it was certain that the risk of losing dust was past, when it was rabbled steadily for about 10 minutes.
The exact point at which roasting was deemed to be complete was determined by the appearance of the hot mass. Soon after rabbling commenced, the slime glowed brightly in spots, and the temperature of the whole charge gradually rose to a maximum. Once this peak had been reached, further rabbling produced little effect, the slime quickly cooled on the surface, giving it a dead appearance, and very little further oxidation of the base metals took place.
The roasted slime was then ready to be raked into a tray for weighing. It was weighed hot, tipped on to an iron mixing table, and flux in the appropriate proportion was weighed out and mixed with it, using a small household-type ash shovel. Roasting time for one muffle charge was about 1½ hours, half of which was used in drying off water.
Smelting
Faber du Faur tilting furnaces, coke fired, with No. 9 Salamander retorts were used initially to melt down a charge of fluxed slime, consisting of:—
Roasted slime………………………………………………120 lb.
Borax glass……………………………………………………36 lb.
Silica sand…………………………………………………….24 lb.
Coke firing was later replaced by oil firing, using Major 2 in. low-pressure air, crude oil burners. These burners were so readily manipulated and controlled that they have been installed on several other furnaces since, giving complete satisfaction.
For lighting a furnace, a fairly good wood fire was first set to prevent any danger of an explosion due to delayed firing of the oil, the air was turned on slowly, then the oil, which should take fire immediately and burn steadily.
Using the No. 9 tilt furnaces, about 60 lb. of fluxed slime at a time was charged into a red hot retort, and allowed to run down partially before adding the next charge. Three such loadings, containing up to 120 lb. of roasted slime, were usually as much as one retort would hold without any chance of slag boiling over. If a boil-up did occur, a handful of common salt was thrown in to prevent slag overflowing.
Time required to run down a charge of 120 lb. of slime, from the commencement of charging was approximately two hours. Completion of melting was judged by stirring with a warmed iron bar, to feel whether the slag was free from lumps and sufficiently fluid; also by the quiescent appearance and colour of the top of the molten mass.
Slag was poured into a conical mould permanently mounted on wheels, and having a long handle for tipping purposes. This mould, as with all other metal equipment that might come into direct contact with molten slag or matte, was preheated with a light wood are before use to evaporate moisture from the surface, and so remove any hazard of hot molten material spattering or exploding. Matte is particularly dangerous in this respect. To prevent slag sticking to the mould, it was given a lime wash immediately after use.
When most of the slag had been poured off, the large slag mould was removed and replaced by a smaller, deeper conical mould, which could be removed by hand from the trolley into which it was placed. This mould received the remnant of slag in the retort, together with the bullion. Oil poured into the mould just before pouring prevented sticking.
A new charge was fed into the furnace immediately after pouring. By that time, the slag in the large mould was ready to granulate by pouring slowly into a pit filled with water. No trouble was ever experienced in this operation because the slag was carefully watched for any signs of matte towards the end of the granulation. The slag remaining as a crust over the sides of the mould was easily broken out with a bar and pushed into the water pit. The mould was then given a lime wash while still hot, so that it would be coated and dry ready for the next pour.
The bullion pour was allowed to cool off for some minutes, to allow it to set, the actual time depending on the size and grade of the button. The mould was then lifted from the trolley, tipped over on the concrete floor and the bullion button separated as far as possible from slag before quenching it in acid and water. Remnants of slag were then chipped off.
Barring Furnace
Bullion buttons produced in this way were melted again in a Salamander No. 60 lipped crucible built into a special small tilting furnace usually referred to as the “barring furnace” A borax cover only was used at first, but when small quantities of matte began to occur in the smelt, extreme difficulty was experienced in cleaning the final bar. Experiments resulted in the use of half a Battersea G assay crucible of soda ash on the button when it was just run down, followed, when the bullion was red hot, by a full Battersea G crucible of a mixture of soda ash and borax, in the proportion of 1 to 1. Sometimes the half-crucible of soda was unnecessary, depending on the amount of matte adhering to the plug.
Fluxed bullion was poured into cast iron bullion moulds of 600 oz. capacity. The moulds were previously coated with carbon black internally, by burning kerosene underneath them. Bars so formed were taken, while still red hot, brushed with a wire brush to remove slag, rubbed over with nitre, which melted with the heat of the bar, then quenched by plunging into a small lead-lined tank fitted with a hood and stack, and half-filled with dilute sulphuric acid. The bar was then immersed in a wooden tub filled with water, to cool it completely before hand polishing by scraping and brushing with sand and water on a table in front of the water tub.
Both the acid and water tubs were cleaned out at intervals of about three months. Prills and chips of gold could then be panned off from the sand and sludge, which were bagged and sent to the flotation or cyanide plant, the pannings going directly to the barring furnace.
Gold bars produced by this method averaged:
Gold……………………………………………840
Silver………………………………………….100
Base metal…………………………………..60
and were sent to the Royal Mint, Perth, for further refining.
About 1935, however, copper content of the mine ore began to rise, and in 1937 copper sulphate was introduced as a conditioning agent in the flotation plant. These two factors caused a marked increase in the copper content of the Merrill slimes. For a time copper was held in the slags by adding up to 20% of manganese dioxide to the fluxes, but in January, 1936, the bullion grade had fallen to: —
Gold……………………………………600
Silver……………………………………90
Base metal…………………………..300
Mint refining charges were too high and were increasing, so that efforts were made to prevent the copper entering the bullion.
Aciding of raw slime was reverted to for a short time, but was quite inadequate.
Small scale tests proved that using a silica-borax flux with or without an oxidising agent, carbon from the retorts reduced the copper out of the slag into the bullion; nothing but a clay-lined pot was found to give a satisfactory smelt in these circumstances. The quantity of slimes being handled at that time would have required large clay liners, which were considered impracticable for the No. 9 Salamander crucibles. Hence, in February, 1936, the practice of granulating and sulphuring all bullion from the primary smelt was introduced.
Granulation & Sulphuring of Bullion
Plugs of bullion weighing up to 900 oz. were granulated as follows:
The plug was melted in a No. 60 Salamander crucible in a well furnace, the temperature, just before pouring, being brought up to a bright red to insure that the metal would not freeze before all of it had been poured. The crucible was lifted from the furnace with a pair of tongs to which a rope block and tackle (“handy billy”) was attached and raised to a height of about 4 ft. from the tank of water into which the bullion was poured slowly in a thin stream. Speed of pouring and grade of the bullion affected the size of granule produced, the slower the pour and the lower the grade, the finer the size. The tank used was 2 ft. in diameter by 4 ft. high.
After pouring, the water was emptied from the tank and the bullion tipped into a flat iron tray, 2 ft. 6 in. square with 2 in. sides, in which it was dried by heating over the well furnace. When cool, the granulated bullion was stored in a tin marked in chalk with its weight, ready for mixing with sulphur.
Not more than 900 oz. of granulated bullion was taken and mixed with 20% of its weight of flowers of sulphur for each sulphuring. Mixing was done as thoroughly as possible on a table, working the sulphur into the bullion with the two hands. Then the mixture was transferred to semi-cylindrical shaped scoops, 2 ft. 6 in. long, for pouring directly into the same No. 60 pot as had been used for the granulation.
The pot was in the furnace, red hot, with oil turned off just before charging. Oil was turned on again immediately afterwards and the charge began to melt down. Three quarters of an hour to an hour was required to complete the reaction. At the end of this time the mixture was stirred with an iron bar to make sure no lumps remained, when the furnace was stopped and the melt poured into four bullion moulds. When it was judged the bullion had set, the matte was poured away from it by tipping the mould gently on the floor, and adhering matte was quickly barred off the bullion while still hot, as it was most easily removed then and not later after cooling. Bullion so obtained varied in grade considerably, the best being: —
Gold…………………………………………880
Silver…………………………………………40
Base metal…………………………………80
but an average figure would be:
Gold…………………………………………840
Silver…………………………………………30
Base metal…………………………………130
Effectiveness of the sulphuring operation appeared to depend greatly on the initial grade of bullion granulated; the lower the initial grade, the higher the finished product, within limits. Fineness of the granulation also appeared to play a minor part.
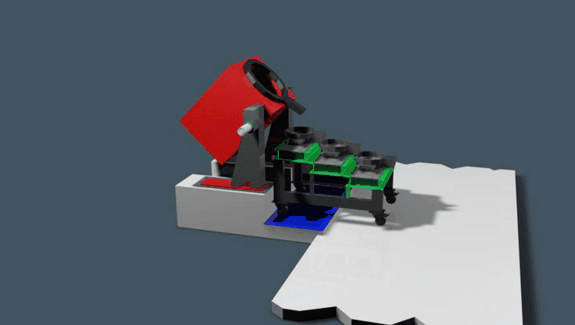
Matte from the sulphuring was fed back to the tilt furnace with the addition of 20% of its weight of soda ash and remelted, on the second day of the clean-up. Up to 200 lb. would be run in one pour, taking about one hour.
Three products were obtained: slag, matte, and bullion.
Slag was poured off into the large conical mould until just before matte appeared. The remainder of the melt was then run into the small conical mould. Slag was granulated as before, but the matte-bullion mould was allowed to cool until the bullion solidified, after which the still molten matte was carefully tipped on to the concrete floor. The bullion button was tipped out and quenched in water. Adhering matte was broken off with a 7 lb. hammer, and the button added to the bullion from sulphuring for barring.
Secondary matte from the foregoing operation, containing some slag, was melted again with a further 20% of soda ash, and yielded secondary matte bullion, tertiary matte and slag. Slag was granulated as before; the matte was set to one side for crushing and sampling before shipping in bags to the Electrolytic Refining and Smelting Company’s works, Port Kembla, New South Wales.
Secondary matte bullion was allowed to accumulate until sufficient was obtained for granulation and sulphuring, after which the bullion was barred with bullion from the main sulphuring. Matte was returned to the secondary matte remelt.
Combined, the bullion from matte retreatments assayed:—
Gold……………………………………………..760
Silver……………………………………………..80
Base metal……………………………………160
so that final bars containing it approximated the assay previously given, viz.:—
Gold…………………………………………………..840
Silver…………………………………………………..30
Base metal…………………………………………..130
Slags from all the sources described were amalgamated after granulation. A fuller description of their treatment is given later under “Amalgamation.”
Best Gold Refining Methods
Clean-up procedure remains much the same to-day as in 1930, although some minor changes have been made. One of these is that chipping the Merrill tank has been rendered unnecessary by reversing the direction of rotation of the impeller in the tank, thereby throwing solution downwards and preventing any accumulation of zinc from occurring. Previous trouble in starting flow of solution and slime through the bottom valve also disappeared when this change was made.
After clean-up, the zinc and lead nitrate are set at an abnormally high rate for four hours to assist precipitation by coating the cloths quickly. Then it is reduced to slightly above normal for 24 hours, or until the assay of the tails solution shows 0.05 dwt. per ton, or less. Solution flow rate is held almost constant between clean-ups.
The only modification in roasting has been the building of an oil-fired roasting furnace with six muffles to replace the old four-muffle furnace that burned wood. The new furnace has a layer of diatomaceous earth, insulating fire-brick between the inner refractory and outer ordinary red brick wall. The insulation has resulted in much cooler working conditions for the operators and lower heat losses from the furnace. Kyanite and silicon carbide bricks were used to line the fireboxes.
Granulation and sulphuring of bullion was practised for about two years. Towards the end of 1938, the amount of bullion that had to be so treated had risen to 15,000 to 16,000 oz. per month. The work became too heavy and exhausting, and attention was therefore directed towards a simpler and less laborious method.
Preliminary trials introducing pyrite-containing flotation concentrates into the flux gave highly promising results. Tested on a plant scale, the method overcame the problem of copper in the bullion and the work of granulating and sulphuring simultaneously.
Silver & Gold Smelting Practice
Two distinct classes of gold slime are treated at present in the gold-room at the Chaffers plant:
- Main ore treatment plant slimes that form the principal subject of this report;
- Smaller quantities of lower grade slimes from the Chaffers re-treatment plant operated by the Lake View and Star Ltd. This plant recovers gold by cyanidation from residue dumps derived from a previous all roasting and cyanidation plant, mixed with early flotation tailings from the present treatment plant. Their history makes clear that no complications arise from copper content. Hence they can be smelted simply, without roasting, or even drying, by using a flux containing nitre to oxidise the base metals.
No details beyond the actual flux used will therefore be given; most attention will be focussed on the matte smelt of the main treatment plant.
Retorts for the Faber du Faur tilt furnaces were recognised as being expensive in first cost, as well as short-lived. With the possibility of replacing them with a furnace in which the slime could be smelted raw, i.e., without roasting, it was decided in 1937 to try a Wabi Monarch-Rockwell type semi-rotary furnace with silicon-carbide liner. Two were purchased originally, followed by two more at a later date.
Smelting of raw slimes was attempted for a short time, using the following fluxes:—
Bullion, however, was low in grade, giving bars assaying:—
Gold…………………………………..710
Silver………………………………….60
Base metal…………………………230
The method was quickly abandoned for the main slimes, but was adopted and has been used ever since for the re-treatment slimes, which are fluxed as follows:—
Fusion takes place readily, slag is very fluid, and bullion grade quite acceptable:—
Gold…………………………………….570
Silver……………………………………340
Base metal……………………………..90
Matte Smelting
Slimes from the Merrill-Crowe are cleaned-up at intervals of about 10 days, as previously described, and roasted in the oil-fired muffle furnaces.
Table 1 gives the analyses of both raw and roasted slimes, together with analyses of the various products from the matte smelt.
Each roaster charge when ready, is taken out, weighed, and fluxed while hot on the mixing table, using the following fluxes:—
Dry pyrite concentrates come from the flotation plant and contain approximately 35 to 38% sulphur. Formerly 5% of fluorspar was added to the charge, but as it appeared to have no effect on fluidity, it is not now used.
Although composition of the roasted slime does vary somewhat from time to time, it has not been found necessary to analyse it before each smelt, nor to alter the flux proportions.
A full charge for one Wabi furnace containing between 100 and 115 lb. of roasted slime, is added to the red hot furnace. With the tilt furnaces, dividing the charge into three separate additions was found to increase the speed of melting, but no advantage could be obtained in this way with the Wabi furnaces.
Time required between charging and pouring is about 1¼ to 1½ hours. To begin, the furnace is left for ¾ to 1 hour in the upright position. Then it is rolled through 35 degrees to one side for five to 10 minutes, rotated back to a similar position on the other side for the same time, and the procedure repeated until the melt is ready for pouring, judged by the colour and quiescent appearance of the surface.
Pouring follows a similar course to that already described except that care is taken to ensure that all the matte goes into the second smaller conical mould, which is capable of holding 80 lb. of matte when full. After cooling sufficiently for the bullion to freeze, the still molten matte is tipped on to a cast iron tray, and the bullion button cleaned as far as possible before quenching in water. The bullion is later barred from the barring furnace, either with similar initial smelt bullion, or admixed with bullion derived from the primary matte.
Primary matte is melted with 12 to 15% by weight of soda ash, after the smelting of the slimes has been completed. From this melt are obtained: Primary matte bullion, primary matte slag, and secondary matte. A complete separation of primary matte slag and secondary matte is obtained by allowing the contents of the large mould to freeze overnight, when the two products break cleanly from each other. The small mould containing the bullion button is poured while the matte is still molten to recover the bullion, but no slag is present in this mould.
Formerly, the practice was to melt the secondary matte once more with 20% of soda ash, yielding secondary matte bullion, secondary matte slag, and tertiary matte. Fig. 12 shows diagrammatically the process in use up till this time. Even so, the tertiary matte still retained comparatively large amounts of gold and silver. Tertiary matte could not be considered as a satisfactory end-point to the matte smelting process, because it had to be sent to a smelter for final recovery of the precious metals.
Since 1943, however, by melting the secondary matte with 7% of flour and 50% by weight of soda ash, a base bullion is obtained in which is concentrated nearly all the gold, silver, lead, and some of the copper. Whether the final mattes are worth treating or not depends largely on the value of the copper they contain compared with the cost of recovering it. The value in any case is small.
The precious metals are readily separated from the base bullion by cupellation, yielding high grade gold-silver bullion, and oxides of lead and copper. The copper is recovered, together with any small amounts of precious metal retained by the oxides during cupellation, by smelting with a flux to slag off the litharge, the lead not being considered worth recovering.
Fig. 13 shows diagrammatically the process being used at present, and Fig. 14 the distribution of values in the various stages.
Full details of this recent addition to the matte smelting process, which brings it to a satisfactory end-point, are given in Part II, where treatment of slag is also discussed.
Until 1943, subsequent treatment of slag was to recover coarse gold by amalgamation in a barrel, after which it was dried and allowed to accumulate. It was then mixed in one lot, sampled by coning and quartering, and finally bagged ready for shipment to Port Kembla.
Present practice retains the amalgamation step, but thereafter the ground slag is agitated with cyanide solution for eight days, or until assays show that solution is practically complete.
Barring follows former practice closely, but one improvement has been made in the bullion moulds used. For some years past, cast iron bullion moulds developed an indentation at the point where the molten bullion first touched the mould during pouring. This sometimes happened during the first time of use. Surface cracks in some of the older moulds added to the imperfections on the bottom of the resulting bar, which made it difficult to clean, and handle during drilling, as well as detracting from its appearance.
Alloy cast irons were tried to overcome the trouble, but none was successful.
Eventually, the bottom of the mould was machined off, and replaced by a false bottom fixed to the sides with countersunk screws. A layer of Carbolox (silicon-carbide cement) about 1 in. thick was tamped in and smoothed off.
Bars poured in these moulds are now regularly smooth, and can be so maintained because the lining can be replaced as soon as defects occur.
Treatment Times and Quantities
On clean-up day, solution flow to the Merrill-Crowe plant is stopped at 7.30 a.m. The first tub of raw slime, approximately 200 lb. wet weight, is available for roasting by 10 a.m., and is roasted and on the mixing table by 11.30 a.m. The roasters are lighted at about 4 a.m., so that the temperature of the brickwork can be brought up slowly, thereby minimising stresses due to expansion.
Those two of the four Wabi furnaces to be used for the day’s smelt have had wood fires in them since 8 a.m., oil is turned on at 10.45 a.m., and at 11.15 a.m. ashes and charcoal are cleaned out so that the whole furnace is red hot to receive the first charge by 11.30 a.m.
Wet weight of raw slime treated for a nine to ten days’ run varies between 450 to 600 lb., yielding 300 to 400 lb. after roasting. These figures are for the present milling rate of 25,000 tons of ore per month.
Smelting proceeds continuously as slime comes forward from the presses and continues until all the slime and the primary matte have been smelted, usually about 3.30 p.m. Work for the day is then finished.
Smelting time for one Wabi furnace charge of 100 to 115 lb. of roasted slime is 1¼ to 1½ hours; for one primary matte charge of 200 to 240 lb. the time required is 1 to 1¼ hours.
Next day, bullion buttons produced on the first day, as well as gold derived from the retorting of amalgam on the second day, are cast into bars, one at a time, from the barring furnace. This operation commences at 8 a.m. and lasts till about midday. In all, four to five bars are made.
During the afternoon shift, slag is shovelled out of the pit on to the floor, allowed to drain, and stacked. Once a month, it is crushed, sampled, and transferred to an amalgam barrel.
Amalgamation
Half a ton of slag is the maximum load taken by the amalgam barrel reserved for slag amalgamation. The slag is charged into the barrel through the manhole in the top, sufficient water is run in to make a thin pulp after grinding, then 30 lb. of mercury and about 30 lb. of slaked lime are added. This amount of mercury is enough to ensure that the resultant amalgam will remain fluid and not form hard lumps that might not separate easily from the rest of the pulp after amalgamation. One barrel of slag usually yields about 100 oz. of amalgam after pressing, but the amount of mercury added could cope with 300 oz. and still fulfil the above mentioned condition.
Billets of cast iron, 3½ in. dia. by 10 in. long, 60 in number, are fed in to grind the slag and work the gold into the mercury. The barrel is then closed up without further additions, and rotated for a period of two days. At the end of this time, the barrel is stopped, with the manhole on top, and the 2 in. outlet plug on the underside.
An amalgamator’s enamel-lined bucket containing water, and about 20 lb. of retorted mercury, is placed centrally in a 16 in. panning-off dish, and the assembly set up immediately below the outlet plug.
The amalgamator’s mate opens the manhole and places a wooden plug on the end of an iron rod in the plug hole, so that he can regulate the rate of outflow when the amalgamator carefully unscrews the plug. While the barrel empties, the amalgamator lifts out any coarse material from the surface of the mercury and transfers it to another bucket. Fines overflow the bucket and panning-off dish, and run down a launder into a batea, thence to a pump which delivers into an agitator reserved specifically for cyanidation of slag residues.
Liquid amalgam in the enamel-lined bucket is cleaned off with a sponge, using fresh water to wash the surface clean from any particles of slag. The sponge is wrung out into the second bucket containing coarse particles. When the amalgam has been thoroughly cleaned, it is poured into a small amalgam press, and left there until the remainder of the amalgam has been separated from the second bucket. This is done by washing a portion into the panning-off dish, and panning until the mercury has collected at the bottom. Breaking the surface at the right place discloses a globule of mercury, which is then poured into a small enamel-lined bowl. Sand left in the dish is washed into a wooden trough over which the amalgamator works. This material is returned later to the barrel for further amalgamation.
Panning-off is continued until all the contents of the bucket have been treated. Liquid amalgam that is collected in the bowl is further cleaned by pouring into another bowl and washing the first in a tub of clean water. Five such washings from bowl to bowl are usually sufficient, when the amalgam is poured into the press with the main amount recovered earlier.
The amalgam press consists of an iron pipe about 4 in. dia., bored with a slight taper at the filtering end, so that the hard amalgam, after pressing, will either fall out of the press into a bowl placed in readiness, or can be eased out by pushing gently with a stick from the opposite end. Nine pieces of fine calico cut to shape and formed into a pad about 1/8 in. thick, are used as the filtering medium and are held in position by a removable plate bored with 140, 1/16 in. holes. Two thumb screws hold the plate to the cylinder. The press is mounted on a copper table coated with mercury, which will take up any spillage of amalgam or mercury, above a funnel let into the table. Compressed air is supplied at 50 lb. or more, pressure to the top of the press through a rubber hose that is screwed to the press with a nut and tail having extended wings.
When the air is turned on, mercury filters through at a fairly fast rate into the funnel and is collected in an enamel-lined bucket below. Amalgam remains in the press.
On completion of pressing, the air is turned off, the press is tilted forwards away from the funnel so that when the plate and filter pad are taken off, the amalgam drops into an enamel bowl placed to receive it. Tilting the press is possible because it swings centrally between the two supporting plates, and can be locked in any position in a vertical plane.
Finally, the amalgam is weighed, using a counterweight for the bowl, on a pair of gold scales used for all rough weighing of bullion or amalgam, then it is transferred to the safe to be retorted later.
Amalgam weighing about 100 oz. per half-ton of slag, usually contains about 20 % of fine gold.
Flotation Strakes
It will be recalled that in the general flow sheet, strakes covered with corduroy cloths are used to recover gold liberated during fine grinding of ore by ball and tube mills. This gold is recovered by amalgamation in much the same way as the slag treatment after granulation.
Cloths are changed once per shift. They are folded inwards so that no pulp or gold can escape, and are carried in ordinary buckets to a special two-storey room for washing. In the centre of the upper floor is mounted a square tank with a square cone bottom terminating in a 3 in. pipe fitted with a plug cock. Directly below the pipe is a small amalgam barrel which receives the washings from the cloths.
Before washing begins, the tank is filled with fresh water, which may be warmed in winter for comfort, to within about a foot of the top. The tank has a removable wooden grid, made in two sections, that rests on angle irons welded to the inside of the tank, 2 ft. from the top. This supports the cloths during washing and prevents their being dropped into the cone.
The amalgamator and his mate wash each cloth once in the tank, then throw it over a wooden horse to drain into a wooden trough. This work is all done under supervision.
When all the cloths have been washed, the floor of the room is mopped by hand with sponges, using a bucket of water to clean the sponges, and the buckets are then emptied into the tank.
Pulp in the tank is allowed to settle for a few minutes, after which a drain cock, set in the side of the tank, is opened to a pump to drain off excess water. The offtake for this drain line is welded to the tank at a point which allows all the contents, plus wash water subsequently used, just to fill the amalgam barrel without overflowing it.
While water is draining off, the amalgamator removes the manhole from the barrel, feeds in ten 5 in. steel balls, followed by 30 lb. of retorted mercury and about 30 lb. of slaked lime. This quantity of mercury is sufficient to cope with 350 to 450 oz. of pressed amalgam. The amount normally obtained on present tonnage is 90 oz. per day, which contains about 40% of fine gold.
The amalgamator then opens the 3 in. plug cock and his mate, on the floor above, breaks a hole through the sand with a piece of ½ in. rod, so that the contents of the washing tank run through into the barrel. The tank is carefully hosed out, using a minimum amount of water.
Later in the day, the amalgamator’s mate returns, fills the tank again with water and rewashes the cloths. The washings are left in the tank until next morning, when the whole procedure is repeated.
After closing the manhole of the barrel, it is set in motion and rotated for about four hours. Cleaning out the flotation barrel is done in much the same way as the slag barrel, the pulp overflowing the bucket and panning-off dish directly to a Wilfley pump that delivers to the batea, thence to the flotation concentrates thickener. Recovery of amalgam from the grit and sand in the bucket is done in the gold-room by the amalgamator, the final amalgam being weighed and set aside in the safe for retorting.
Roasted Concentrate Strakes
Concentrates from the roasters are pulped with fresh water, and pass over a set of strakes covered with long corduroy cloths, before being filtered and repulped with cyanide solution. Because fresh water and not cyanide solution is used on this section, there is seldom any trouble from cloths becoming coated with a hard gypsum layer. They are therefore comparatively easily washed in a wooden vat in the gold-room.
Washings are transferred with a bucket to a third amalgam barrel, to which 30 lb. of mercury and about 30 lb. of soda ash are added. Lime is not suitable for this class of material; caustic soda is the most effective alkali to use, but soda ash is chosen because it is less difficult to handle than the caustic. Alkali has the effect of cleaning dirty gold particles and hastening their amalgamation.
Mercury used is sufficient to cope with 200 oz. of pressed amalgam. The amount usually obtained at present is 150 oz. daily, containing about 30% of fine gold before retorting.
An important factor, not yet mentioned, that applies to all types of material in amalgamation, is that grease or oil must be prevented from entering the barrel. It causes the mercury to “flour” and in extreme cases may result in all the mercury being so finely divided that none settles in the bucket when draining the barrel, but overflows and is carried away to a point in the plant where it cannot be conveniently recovered.
Retorting of Amalgam
Amalgam accumulated from the three sources is retorted twice a week. The weight of each bowl is checked against the weight recorded in an amalgam book when it was weighed before going into the safe, then placed in a rectangular-shaped mould according to its source. This separation is made as a check on the value of gold obtained from each set of strakes daily, so that the value can be entered on the metallurgical record sheet by calculation, in advance of the retorted results. Minor corrections to the sheet can be made weekly so that the final monthly figure recorded is correct.
Trays containing the amalgam are loaded into a special retort, the door is screwed into position, and oil turned on the burner. The retort is slowly brought up to a red heat. Mercury volatilises from the amalgam after about two hours’ heating, and is condensed in a water-cooled coil, dropping into an amalgamator’s enamel-lined bucket that has been weighed previously. When no more mercury distills, usually about three hours after lighting the furnace, the bucket is weighed and the net weight of mercury obtained is recorded. This weight, added to the weight of gold obtained from the retort, should equal the total weight of amalgam placed in the furnace. Shortages indicate cracks in the retort, which must then be replaced.
Retorted gold in the trays is lifted out with tongs, transferred to tared tin dishes, and weighed according to source. It is then ready for barring, the procedure for which is much the same as described previously, except that the cover used is borax only.
Bulked amalgam gold from the two sets of strakes usually averages:
Gold………………………………….955
Silver………………………………….40
Base metal……………………………5
It is barred separately from all other bullion, and is termed an amalgam bar.