Problem with gold recovery from sulphide ore: How may a mill get the maximum recovery of gold from a sulphide ore, at the least capital cost and at the same time obtain the highest net return. This latter point is most important. In many cases a gold mill using an all-cyanide flowsheet with fine grinding of all the ore will report very low gold content in the tailings particularly on an oxidized ore. A neighboring mine may have a higher tailing loss but still make more money due to lower milling costs.
For many years, after introduction of the cyanide process for dissolution of gold, the usual practice was to grind all the ore with little or no concentration before cyanidation. There were two general cyanidation flowsheets; sand leaching and all sliming. The latter ultimately has almost completely replaced sand leaching.
With the advent of flotation and the fact that gold either free or finely disseminated in pyrite, etc., could be floated, many possibilities opened up for the treatment and concentration of gold ores. It also provided the means of working ore bodies hitherto considered unprofitable or metallurgically impossible for cyanide treatment. Two examples are the large low-grade ore bodies which require very fine grinding and refractory sulphides which have to be concentrated and roasted to expose gold to cyanide action.
A Flowsheet to recovery gold from sulfide ores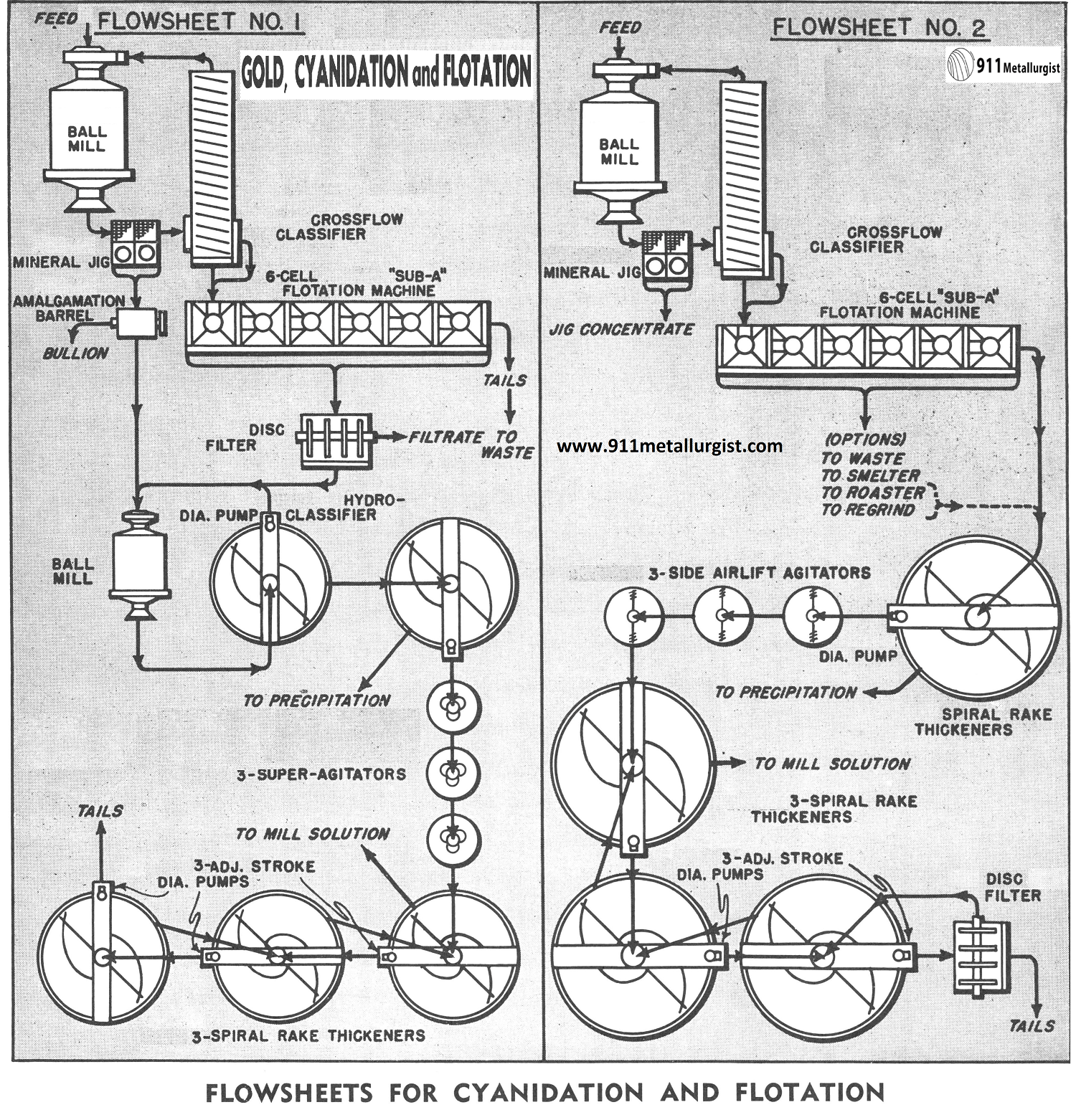
There are many arrangements and combinations using flotation in conjunction with treatment of gold ores. The two gold process flowsheets shown, with some variations, are probably the most commonly used.
In Gold Flowsheet No. 1 the ore is ground in water to such a size as to free the minerals sufficiently to produce a tailing by flotation low enough in value that it may be discarded.
Here a Mineral Jig is used in the Ball Mill Classifier circuit. This recovers coarse and fine free gold preventing any build-up in the circuits especially in the grinding circuit. It also efficiently removes any oxidized or tarnished non-floatable gold. The jig thus operates as a safety valve. If the quantity and grade justify, the jig hutch product may be amalgamated in a Amalgamation Unit or sent to subsequent cyanide treatment with the flotation concentrates.
Flotation concentrates are dewatered and finely ground for maximum exposure of gold and sent to the cyanide plant. The grinding is preferably done in cyanide solution.
Standard practice is followed as shown; the slight difference usually being more intense agitation as supplied by Super-Agitators with maximum aeration. The following advantages may be claimed plus others not enumerated:
- Coarse primary grind on bulk of ore means a saving by using smaller grinding and classifying equipment, etc.,
- Lower operating grinding costs for balls, liners and power.
- Very fine grind on small amount of concentrates is possible if required.
- Small tanks, etc., due to lesser quantity of materials to be treated.
- Smaller building required for smaller tanks and other equipment. Less initial cost and less maintenance, heat, etc.,
particularly in colder climates. - More profit earned.
The second flowsheet is another application of flotation as applied to a gold ore. In this case the flotation tailings are cyanided for gold recovery. The Jig is again employed in the grinding circuit as in Gold Flowsheet No. 1 for the same reasons.
This scheme would be used where it is not possible to make a flotation tailing low enough in gold to be discarded but flotation is warranted for one of the following reasons:
- Sulphides require very fine grinding for maximum extraction, then are returned to circuit.
- Gangue carries some gold that is easily recovered at coarse mesh.
- Sulphides such as copper or zinc, etc., are present which can be recovered and sold at a profit for specific metal content by shipping direct to the smelter.
- Removal of refractory material by flotation ahead of cyanide plant.
Each of the above gold process flowsheets lend themselves to variations. Briefly, some of these are:
The concentrate from either plant could be roasted for the elimination of high cyanide consuming arsenic from arsenopyrite ores. The calcine is then quenched, ground and returned to the plant. In fact, flotation has made possible the treating of such ore bodies for the recovery of gold. It was never possible to treat these direct by cyanide and difficult to roast ore alone because of the large amount of extraneous heat required. Flotation concentrates are usually self-roasting.
One particular plant uses a flowsheet similar to No. 2. Here flotation concentrates are reground. The flotation tailing is deslimed, thickened and joins the reground concentrates for treatment. This requires smaller tanks and building. In other mills concentrates will be reground, given extra agitation and decanted before joining bulk of ore.
Lastly, and something to be avoided if possible, is the flotation of sulphides carrying gold from cyanide plant tailings. The cyanide-lime (depressant for pyrite) must be counteracted before flotation either by reagents such as acids or by open circuit grinding to remove the lime coating. This scheme finds its greatest use where a cyanide plant is already in existence with the plant paid for, then the flotation is added on the end. The concentrate is further ground and cyanided. This brings us to an example reported some while ago where a conventional cyanide plant was revised by the addition of a “Sub-A” Flotation Machine. The ore was ground in water, floated, concentrates reground and cyanided in the existing plant. The only additional equipment was the flotation cells. They reported an 8% increase in recovery due to finer grind, 15% increase in tons per day treated, and a 3% reduction in cost.
Flotation in a gold concentrator should be considered not only when building a new plant based on results of a thorough ore test but also in an existing plant when:
- Ore changes in character.
- Recovery drops due to need for finer grind.
- Daily tonnage is increased. Often this can be accomplished by concentrating with flotation at coarse grind using one of existing ball mills for regrind. The existing tanks should be ample to handle the smaller bulk of concentrates.
Many new applications using flotation are now possible due to the use of the “Sub-A” Flotation Machine with its flexibility, low cost and simplicity of operation and most important, its ability to treat coarse as well as fine material.
Source: This article is a reproduction of an excerpt of “In the Public Domain” documents held in 911Metallurgy Corp’s private library.