Table of Contents
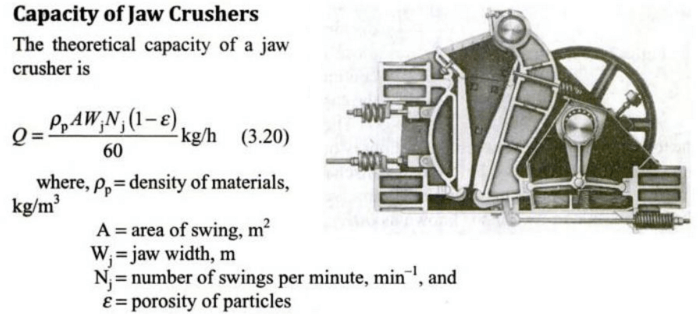
Example capacity calculation of a 10″ x 20″ (250 mm x 500 mm):
- Pp = 2800 (2.8 SG)
- e = 0.2 (halfway between dolomite and sandstone)
- A = 250/1000 x 500/1000
- Wj = 0.5
- Nj = 225
= 2800 x 0.25 x 0.5 x 0.5 x 225 x (1-0.2)/60 = 525 kg/hr = 13 TPD vs 300 to 420 TPD —> I can’t make this work!
My friend Alex the SAG Mill Expert, says this equation you picked up doesn’t look right. The numerator is calculating the volume of one swing of a jaw, times the density of material in the chamber, times the number of cycles per minute. This should give you the mass of material crushed per minute.
The denominator looks wrong; to convert to mass per hour should be multiplying by 60, not dividing by 60. Dividing by 60 should give mass
per second, which isn’t what you want.
The example you’ve given is missing information needed to calculate the “A” term – it doesn’t tell you the height of the crushing chamber. The
two measurements you’ve got are the top opening width and top opening length; “A” should be the jaw throw (not given) times the crushing
chamber height (also not given).
Will’s Textbook (8th ed) gives a better equation (here on the right):
Q = W*S*s*cot(a)*k*N*60
- The Q is vol throughput, m³/h
- W is inner width of crusher, m
- S is open side setting, m
- s is jaw throw, m
- a is the nip angle
- k is a material factor, 1.5 to 2.0 (includes your epsilon param)
- N is RPM
This form works out volume of one motion of the jaw, multiplies by RPM then multiplies again by 60 to give volume/hour. This looks better, but it still doesn’t work.
Example, Metso C80 jaw crusher, 2″ CSS:
Q = 0.8*(0.05+0.025)*0.025*cot(10°)*1.75*350*60 = 111 m³/h
(I have to guess the throw, the catalogue doesn’t say)
Q × 1.6 t/m³ = 240 t/h (versus catalogue value of 75-100 t/h)
Still out by >100%, but at least the right order of magnitude.
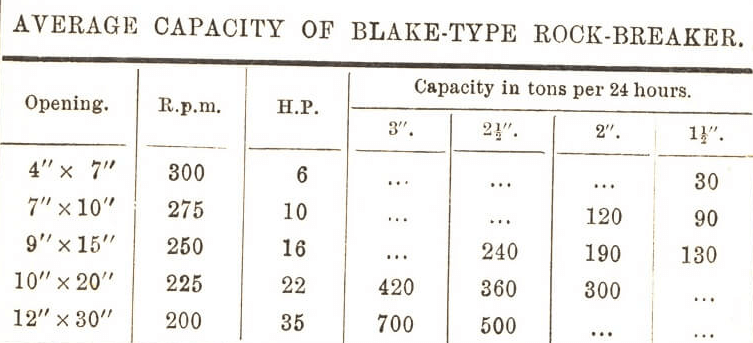
Porosity is the percentage of void space in a rock.
Tables herein contain information that is typical of output from crushers discussed above. The capacities are based on the crusher receiving full, continuous feed of clean, dry, friable stone weighing 100 lb/cu ft.
These capacity tables show several significant differences between the two common types of primary crushers. A jaw crusher has a wider range of settings—generally, a maximum of two to three times the smallest setting. The tables also show that for a comparable maximum size of feed and setting, a gyratory crusher has a much greater capacity than a jaw crusher. The gyratory crusher obtains this advantage only at the cost of greater power to drive the crusher.
Capacities and Horsepower of Jaw Crusher (tons/hr)
Crusher Size (in.) |
Power Required (hp) |
Closed side setting (in.) |
||||||||
2 |
3 | 4 | 5 | 6 | 7 | 8 | 9 | 10 | ||
2036 | 75 | 45 | 70 | 100 | 125 | 150 | ||||
2042 |
75 | 60 | 85 | 120 | 150 | 180 | ||||
2436 |
100 | 55 | 80 | 110 | 145 | 175 | ||||
2448 |
100 | 115 | 155 | 195 | 230 |
260 |
315 |
|||
3048 | 150 | 180 | 220 | 260 | 315 |
365 |
||||
4260 | 200 | 285 | 350 | 420 | 480 | 540 |
600 |
Single-toggle jaw crusher specs
The selection of an appropriate primary crusher for a given use has to be based on a consideration of several factors. These are not limited to the design features of the crusher. If the feed is blasted rock from a quarry, the size and method of handling the feed influence crusher selection. For instance, a power shovel is limited by the dimensions of the dipper in the maximum size of rock it can handle well. It may be that the bucket of a 1½- yd shovel would be too small to load the maximum size rock allowed in a jaw crusher with a 42-in. opening.
Capacities of a Gyratory Crushers (tons/hr)
Crusher Size |
Power max° hp | Open Side Settings of Discharge (in.) | |||||||
2 |
2.5 | 3 | 3.5 | 4.5 | 5 | 5.5 |
8 |
||
Primary Crushers |
|||||||||
30-55 |
300 | 420 | 510 | 570 | 730 | 810 |
900 |
||
42-65 |
400 | 880 | 1000 |
1120 |
|||||
48-74 |
500 | 1700 | 1850 |
2700 |
|||||
60-89 | 600 | 2500 tph at 6 in., 3600 at 9 in. max. |
3260 |
||||||
Secondary Crushers |
|||||||||
13-36 |
125 | 200 | 250 | 300 | |||||
16-50 |
150 | 350 | 400 | 430 | 480 | ||||
24-60 | 300 | 480 | 540 | 600 |
730 |
||||
30-70 | 400 | 700 | 810 | 930 | 1220 | 1350 |
1500 |
From Allis-Chalmers’ Superior Primary and Secondary Crushers.
° Actual required depends on stone hardness, reduction ratio, and so on.
If a 60-in. gyratory crusher is to process material from a quarry where a shovel loads the raw material, the shovel would probably have to have a dipper capacity of at least 5 cu yd to be compatible. It may be more economical to change the blasting pattern to produce larger rock that can be handled by a larger loader-hauler combination and still fit in the primary crusher. Generally, a large reduction ratio will be required of the primary crusher.
Typical Capacities of Twin-Roll Crushers (tons/hr)
Crusher Size (in.) |
Power Required (hp) | Space between Rolls (max. size of feed) (in.) | ||||
1/8 (3/8) | ¼ (3/4) | ½ (below) | 1 (below) |
1 ½ (below) |
||
24 x 16 |
30 | 12 | 24 | 48 (1 ¼ ) | 96 (1 ¾ ) | |
30 x 18 |
40 | 13 | 26 | 52 (1 3/8 ) | 103 (1 7/8) | 156 (2 3/8 ) |
30 x 26 |
100 | 19 | 37 | 75 (1 3/8 ) | 149 (1 7/8) |
223 (2 3/8 ) |
40 x 22 | 60 | 15 | 31 | 62 (1 ½ ) | 125 (2 1/8 ) |
187 (2 5/8 ) |
40 x 30 | 200/250 | 21 | 42 | 85 (1 ¼ ) | 170 (2 1/8 ) |
255 (2 5/8 ) |
Telsmith Handbook
If gravel has relatively small maximum particle sizes, a large feed opening is not needed. It may be more economical to feed all of the pit-run material into the primary crusher rather than to remove the part that is already smaller than the crusher setting. That calls for a crusher with a higher capacity. There are many feasible solutions to the crusher selection problem, so the aggregate producer must select crushers with total operations and economics in mind. The selection of reduction crushers is also a complex problem.
The economic selection of any particular crusher depends on the ability of the crusher to handle the maximum size of feed, reducing this at the highest possible reduction ratio and least cost for the original installation, maintenance, and power. For any particular aggregate production plant, it is advisable to make preliminary determinations of the types of crushers needed. If most of the feed is coarse and stage crushing is required, primary crushers that meet the requirements of reduction and economy and have straight crushing surfaces may be most economical.
Typical Capacities of Cone Crushers
Crusher Size (in.) |
Power Required (hp) | Capacity at Closed Side Setting, tons/hr (in.) | |||||||
1/8 | 1/4 | 1/2 | 3/4 | 1 | 1 ½ | 2 |
2 ½ |
||
Open Circuit Operation (with coarse bowl liner) |
|||||||||
28 |
40-50 | – | 22 | 32 | 44 | 57 | 88 | ||
36 |
60-75 | 56 | 81 | 107 | 160 | 220 | |||
51 | 125-150 | 115 | 155 | 195 | 275 |
360 |
|||
66 | 200-250 | 235 | 315 | 435 | 565 |
710 |
|||
Closed Circuit Open (with fine bowl liner) |
|||||||||
28 |
40-50 | 8 | 16 | 31 | 44 | ||||
36 |
60-75 | 35 | 60 | 85 | |||||
51 | 125-150 | 60 | 110 | 165 | 200 | ||||
66 | 200-250 | 185 | 265 | 325 |
Specs from Kue-Ken cone crushers
Where only a very small percentage of the feed approaches the size of the feed opening of the crusher, nonchoking crushing surfaces in a high capacity crusher may be advisable for the sake of economy. If the plant requires several stages, and several different types of crushers could be used for each stage, the costs of each feasible combination must be analyzed to find the crusher plant with the least total cost.
Typical Capacities of Hammermills
Feed Opening (in.) |
Max.
Feed (in.) |
Power
Required (hp) |
Approximate Capacity, tons/hr (in.) |
|||||
1/8 |
1/4 | 1/2 | 1 | 1.5 |
2.5 |
|||
9 x 12.25 |
3 | 25-60 | 5-8 | 8-10 | 10-12 | 15-18 | 22-26 | 27-35 |
11 x 21 |
4 | 50-125 | 12-16 | 10-20 | 18-25 | 32-39 | 44-50 | 55-75 |
12 x 33.5 |
6 | 125-250 | 25-34 | 30-40 | 42-54 | 85-100 | 105 + |
125 + |
17.5 x 43.25 | 10 | 175-350 | 41-54 | 50-70 | 65-85 | 140 + | 160 + |
185 + |
17.5 x 64 | 10 | 250-600 | 60-80 | 85-100 | 110-140 | 210 + | 260 + |
290 + |
Telsmith Handbook
[/fusion_builder_column][/fusion_builder_row][/fusion_builder_container]