Table of Contents
In-depth research on gold recovery in the Yukon conducted in 1990 by Randy Clarkson concluded that the “reliability, inexpensiveness and operating simplicity of sluice-boxes are hard to beat”. The same still applies, although sluice design has progressed since.
Author: Jonas Boehnke |
![]() |
Shop for a Gold Wash Plant with Hydraulic Riffles here
Water injection into the capture zone of a sluice box, marketed as hydraulic riffles, represents the latest major development. After L.G. Heron filed a patent in 1987 for the technology it remained poorly understood or implemented by 1990 when Clarkson commented on early North American adopters that the technology requires “more testing”. Continued improvements to the riffle design and a practical fluidization water filtration solution were key to solving major roadblocks in the technology’s widespread roll-out. Robust instrumentation such as flow meters and pressure gauges allow fine-tuning of the fluidized bed to meet individual operating conditions. While still reliable, relatively inexpensive, and simple, today’s hydraulic riffles have become technology equipment adding another dimension of operational control.
Early installations incorporated hydraulic riffles only over a short section of the sluice run, either before or after conventional angled riffles or expanded metal riffles. More recently operators have called for retrofits in additional sluice sections to expand on the benefit of hydraulic riffles. Hydraulic riffles allow for prolonged operating time between cleanouts due to increased active riffle capacity and maximized gold recovery in a protective fluidized-bed that prevents gold loss due to scouring.
The principles in sluice design are best visualized as material bodies obstructing the flow of slurry. Depending on the shape and size of the obstruction (riffle design) and the water velocity (solids content & slope) a turbulent flow is established, with eddies forming around the obstruction. Such eddies create pockets of low velocity in which gold can deposit. Below is an exemplary visualization from a fluid dynamics model (CFD) of water flowing around an object.
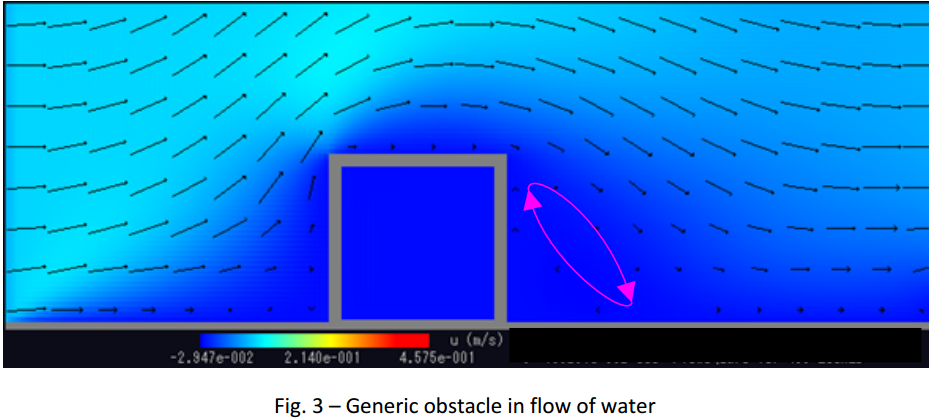
Conventional “Hungarian” Riffle Designs
These rely entirely on inducing eddies in order to generate pockets for gold deposition. Larger riffles create deeper, more turbulent pockets and vice versa. The sluice run is therefore often composed of multiple sections: Angled riffles (angle iron or Hungarian style) generating deeper pockets in which coarse gold can deposit and expanded metal creating shallower pockets, more suitable for fine gold. The underlying Nomad matting (“Miners Moss”) induces even smaller eddies between its randomly woven mesh. The flow profile determines which particles preferentially settle or get rejected. Since flow characteristics are strongly governed by the velocity of the water, changes in velocity can either “pack” the bed or eject previously recovered particles. The velocity changes when the sluice angle is changed or when the volume of water/solids or the ratio of water/solids changes. An example is running the sluice with water only (no solids), which is when the water velocity increases, possibly ejecting previously recovered gold values.
Hydraulic Riffles
These have a similar geometry to conventional angled riffle designs, but actively inject filtered fluidization water through a series of small holes (3.2 mm diameter) into a relatively deep concentrate bed. The principle of fluidized beds is well established as a feature of centrifugal concentrators such as batch type Falcon or Knelson concentrators where the technology was introduced to prevent packing of concentrate in the riffles and protect recovered gold values from the scouring action of material flowing up the riffled rotating bowl. Hydraulic riffles apply the same working principle in a stationary sluice box design more suitable to semi-mobile placer / alluvial gold environments than centrifugal concentrators. Due to its design geometry and depth, hydraulic riffles hold more concentrate than conventional riffle designs, producing larger volume cleanouts. It has been demonstrated, however, that the time interval between cleanouts can be extended without gold loss. While centrifugal concentrators require to be rinsed every 2 hours for example, hydraulic riffles can be operated for up to multiple days before requiring a cleanout.
Since its adaptation by Macon in 2012 the company has optimized the hydraulic riffle geometry to create an evenly fluidized bed – a result of riffle design, i.e. spacing, bed depth and control of fluidization water injection.
Upgrades were made to the supply of fluidization water: A self-cleaning filter system was introduced in 2020 to guarantee maintenance-free operation without plugging the water distribution routes. Although requiring fluidization water to be filtered from grit/organics, hydraulic riffles can operate with suspended clay/silt in the process water, a common issue with centrifugal concentrators having more stringent water quality requirements.
Consistent water supply controlled via flow instruments and pressure gauges is essential for optimum gold recovery. When correctly adjusted, the fluidization water disperses into the concentrate bed downstream of the riffle and dilates the bed just enough that it’s bearing capacity is reduced, allowing the concentrate to rest in a calm, loosely packed bed. Under such condition gold particles of high specific gravity can settle deep into the bed. Once having reached the bottom of the riffle those particles are protected from scouring even under changing flow conditions in the sluice run. Nomad matting installed as a bottom layer creates a seal between riffle sections. The benefit of save retention especially over long periods between cleanout cycles materializes for the collection of both coarse and fine gold.
The following CFD models visualize the effect of fluidization water injection. Conventional (unfluidized) riffles rely on downdrafts and low-velocity zones to deposit gold. These agitated zones form eddies and are characterized by sharply changing velocity profiles (i.e. at the boundary between light blue and dark blue colors).
Hydraulic riffles show more even velocity profiles due to supplemental water injection close to the bottom of the riffle creating a live fluidized bed between riffles that allows dense particles to settle deep into the concentrate bed. The injected water disperses to form a gentle upcurrent acting on the concentrate bed. The downwards orientations and high velocity directly at the water injection hole (red color profile) prevents material migrating into the diamond shaped water distribution channel. The operator has the ability to increase or decrease the flow of fluidization water to counteract packing. Macon specifies a suggested flowrate which has proven optimal for most applications.
Macon Self-Cleaning Filter For Hydraulic Riffle Operation
Although hydraulic riffles were invented in the 1980s, application success of the technology only came with the introduction of reliable water filtration. Macon’s self-cleaning filter technology was introduced in 2020 as a response to the struggle that many operators had with hydraulic riffles plugging up from organics or other debris. The self-cleaning filter, designed for harsh mining environments to be simple and without moving parts, is located in the main water supply line and divides the flow into two streams – (1) the unfiltered stream continuing to the wash water manifold at the screen deck or trommel and (2) the filtered water supplied to the hydraulic riffles. The filter mesh is typically about half the size of the holes in the hydraulic riffles. The filter principle harnesses the high velocity of washwater passing by the filter surface to constantly wipe the media from any collected debris, ensuring maintenance-free operation. No motors, no moving parts. Since it’s introduction in new Macon washplants, and multiple retrofits, the system has provided thousands of hours of blockage-free hydraulic sluice operation.