ALLUVIAL AND DREDGING
- Primary Process when you know your Gold is too fine for a sluice
- Daily Upgrading of Sluice Concentrates
PROSPECTING, DRILLING, SAMPLING
- Analysis of Samples in the field. iCON is mobile and easily cleaned from sample to sample.
- Confidence in the full size distribution of your Gold
ENVIRONMENTAL REMEDIATION
- Recovery of Mercury from Tails
HARD ROCK GOLD MINING APPLICATIONS
Hard Rock miners around the world have historically recovered as little as 30% of their free gold using mercury amalgamation. The iCON process is being used to scavenge/reprocess old tails without using mercury. These miners are now recovering more gold reprocessing tails with iCON than the original miners recovered. They are also recovering significant quantities of Mercury.
Hard rock miners must first understand some definitions:
- Free Gold has been liberated and depending on its size will be visible in a pan.
- Free Milling Gold is the gold that can be liberated by a standard rotating ball mill or other locally available milling methods.
- Refractory Gold is that which is not recoverable by standard milling and/or leaching processes. This may be ‘entrapped in sulfides.’ A standard ball mill may grind your ore to 75 microns.
- Gravity Recoverable Gold (GRG) refers to how much gold you can recover based on how fine you are grinding/milling your ore.
The GRG (Gravity Recovery Gold) testing is available.
The number 1 application for iCON i350 worldwide is Hard Rock. The 10-15 TPH capacity and the ability to recover fine, flat milled gold are ideal for iCON. The major mines of the world use gravity concentration in their grinding circuits. The concentrators can recover over 90% of the overall production of major/professional mines.
A typical Hard Rock application would involve a crusher and ball mill. The material would be size classified using a cyclone in closed-circuit or simply a screen in semi-closed circuit milling. After the mill the material will pass through the concentrator. The major mines have a ‘recyclic load.’ Their processes are designed for the feed to pass through a concentrator multiple times before passing to the tails.
A Hard Rock operator may choose to run 15 tons per hour of a high grade ore. He may choose to rinse the bowl every 20 minutes. Here, he would have run 5 tons in 20 minutes and collected 10 kg of concentrate. That is a concentration ratio of 500 to 1.
The concentrate will still need to be upgraded or cleaned to have a sellable product. Some miners around the world are choosing to collect the concentrates from multiple mine sites and clean the cons at a regional secure facility. This is known as ‘pre-concentration’.
When scavenging old tails the operator must understand that there is a reason the first miner missed this gold. It may be that it was poorly milled and needs to be re-milled to liberate more gold. In order to recover what another team missed the operator must pay attention to the details and be prepared to adjust their process as required. To understand your ore and how much gold you can expect to recover, IGR recommends testing your samples at lab.
ALLUVIAL/PLACER & DREDGING
The i350 is impacting the world of Alluvial Mining and Dredging the way the i150 has done for hard rock.
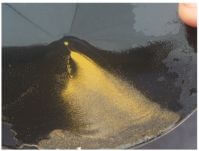
Alluvial miners often ignore the fine gold because sluices and jigs can’t catch it. Depending on the size and shape of your gold a sluice may begin to lose gold at 40 mesh. Some alluvial deposits have 90% of their gold finer than this. This is where enhanced gravity, iCON, is the only solution.
Concentrators are being tested on the ends of sluices and dredges. In this case the operation is still capturing the same amount of gold in the sluice. The added value of the concentrator becomes very clear.
After seeing the additional recovery of the concentrator some operators are choosing to redesign their process. An efficient plant design would include a screen (typically 2mm or 10 mesh) where only the coarse material will be routed to a sluice and only the fine material will be routed to your concentrator.
WHAT IS ICON
iCON is a family of products specifically designed to recover fine gold and provide the correct modular process to various regions of the world. iCON was designed by the professional engineers at Falcon Concentrators and uses the same patented technologies used at the largest mines in the world.
The heart of the iCON family are the world famous i150 and i350 Concentrators. iCON uses classification and enhanced gravity in its centrifugal concentrators to ensure that you are recovering the most gold possible.
In addition to concentrators iCON offers a line of complete modular plants for Alluvial and Eluvial operations. We offer scrubbers plant for clay and screen decks for clean gravel.
iCON is supported by governments around the world due to its ability to recover gold without the use of mercury. iCON was designed for the United Nations’ Global Mercury Project to bring professional techniques to small miners throughout the world. iCON uses the same proven technology as the Falcon brand of professional mining products: it was designed by Falcon’s engineers and is now a product of iCON Gold Recovery Corp.
Features that make iCON Concentrators ideal for small scale applications include:
- Low machine weight
- Ease of Installation
- Only one moving part
- Use of wear components readily available in developing areas
- Rigid structure conducive to running at high speeds
- Low acquisition and operating costs
- A proven, robust and simple mechanical/electrical platform
- Efficient clean out
- High concentration ratios
- All iCON products include a VFD/Soft Start
- Value priced well below the competition
- Short 1 minute rinse times
- Simple push button start/stop
HOW IT WORKS
The iCON Concentrator is designed to capture all heavy minerals including Gold, Silver and PGMs and Mercury. It uses enhanced gravity to concentrate very fine, free minerals that are not recoverable using the traditional techniques of small scale and artisanal miners. The technology is based on the batch-type Falcon concentrator and designed by the same Falcon engineers that design concentrators for the largest mines in the world.
In operation, material is fed as a slurry of minerals and water into a rotating bowl that includes special fluidized grooves or riffles to capture the heavies. Periodically, a rich concentrate is rinsed out and requires further upgrading to be turned into a final gold product.
GENERAL COMMENTS ON MINERAL PROCESSING
Throughout history gold processing has been plagued with inefficiency and contamination. Millions of dollars of fine gold have been discarded in the tails or “washed down the creek” due to inadequate processing. Other operations have long put the health of both workers, and our planet at risk with the use of mercury, cyanide and other dangerous chemicals. iCON technology successfully addresses both issues, ensuring that the highest percentage of gold is recovered and no hazardous chemicals are needed.
The most important factor in mineral processing is classification; the relative size of the gold you are processing must be known. Mineral processing is expensive and time consuming. Processing large material that is known to have no value, costs both money and time. With classification, time, energy and money will not be wasted processing excess material that is known to have no values. For example, if you know that your largest gold is .5mm then there is no reason to put 10mm material through your process. Also, the large feed will affect the efficiency of any process. The large material will hinder the recovery of the finer materials. For example, one miner improved his recovery from 40% to 70% simply by screening his feed from 8mm to 2mm. No gold was lost, because his largest gold was around 0.5mm. The iCON method will improve your process by screening your feed to the proper size (reducing the volume of feed) and increasing the percentage of gold that you recover.
iCON uses a 2 step process; classification and concentration. Your feed will be screened to 2mm (or less based on your results) before processing in the concentrator. Any material larger than the screen will pass over the nugget trap. This will give the user confidence that they are collecting the BIG gold while minimizing the feed to the concentrator and maximizing its efficiency.
I350 CONCENTRATOR INSTALLATION
In order to install your iCON you will have to consider the following: suitable footing, electrical supply, clean/pressurized water supply, feed method, tails removal method, concentration collection. You will also need to consider the height of the concentrator relative to the slurry input and tails output.
Suitable Footing /Vertical Height
- For ground level operation it is common to leave the concentrator on the pallet on which it arrives.
- For installations above ground level, the feet have mounting holes and each foot should be bolted to secure the concentrator in place.
- The concentrator does not have to be perfectly level. It is recommended to keep it within +/- 5 degrees of level.
- A common installation error is to set the equipment at ground level and then to find out that the tails run onto the ground or that your tails piping does not have enough vertical fall to discharge the material.
- Generally, you will need ¼ inch of fall per each foot of tails piping: 1 cm per meter.
ELECTRICAL CONNECTIONS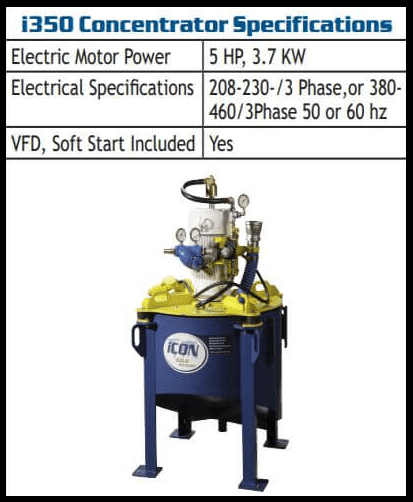
The direction of rotation of the concentrator’s bowl is not important. It can spin either clockwise or counter-clockwise.
Slurry pumps are directional and must rotate such that material is thrown in the direction of the discharge.
Connect the white, black and red wires from the VFD to L1, L2 and L3 of your generator. The order of connection is not important. Connect the green wire to ground.
The most common installation issue is connecting to the incorrect supply voltage. It is recommend that you use a voltmeter to confirm the proper voltage before switching the power on.
Power Generator Recommendations
For the reliability of your generator we recommend that your generator has double the capacity required by your equipment. For connection to line power, only the actual power consumption is needed.
Clean Water Connection
The user will have to supply clean pressurized water to the concentrator. Connect your clean pressurized water supply to the hose barb on the plumbing manifold on the concentrator.
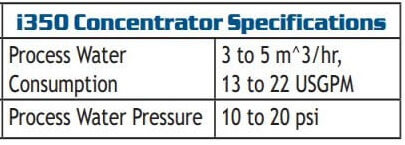
It is important to use the same size hose as the barb to supply this process water. A smaller hose, long hose or hose with bends/restriction will restrict the water flow and limit the pressure to the concentrator.
The process water should be fed from a dedicated supply line and pump. Connection to a manifold where other people may be using this same supply may cause wild fluctuation in the pressure and lead to unpredictable gold recovery.
The water does not have to be perfectly clean. Murky water is acceptable. The water should be clean enough to pass a 50 mesh screen.