The unseen factors in flotation are those which affect the economic recovery and are not shown by the assays or analyses. The fact that equal tailings and equal grade of concentrates can be produced with widely varying physical properties of the products recovered and rejected is unrecognised in most cases.
In the past, when studying the merits of various flowsheets, types of flotation machines, and reagent combinations, it has been common practice to compare only the assays or analyses of concentrates and tailings in many cases only the value of the tailings was considered. The theory has been that only one small elusive fraction was responsible for higher tailings and the combination most efficient in recovering this fraction was the one desired. In most cases a study of fractions separated by screening did not disclose the physical differences of the concentrates produced.
During the last few years developments and improvements in elutriation apparatus have taken the sizing of mill pulps in the low micron fractions from an inaccurate and delicate research laboratory procedure to a practical everyday step for plant control. The clear picture of the distribution of all mineral particles down to semi-collodial sizes has shown the way to higher concentrating efficiency and improved economic recovery.
In analyzing the performance of the “Sub- A” (Fahrenwald) Flotation Cells in comparison with other types of machines operating on identical feed, it has been found that approximately the same recovery can be made but with a marked difference in the type of concentrate produced. We are giving below a screen analysis of a “Sub-A” concentrate and a concentrate from a pneumatic (airlift type) flotation machine. The two circuits were running with identical reagents and with feed from a common distributor. The tailing from both machines was 0.12 percent copper:
It will be noted that the grade of “Sub-A” concentrate was higher than the pneumatic machine and that the ratio of concentration was also higher. This higher ratio of concentration slightly reduced the “Sub-A” recovery, but it is still apparent that the mineral recovered by the two machines was not identical and obviously the character of the mineral losses in the tailings was not similar.
A portion of these same composite samples were sized below 200-mesh and the analyses of these finer fractions shows clearly that each machine was recovering a distinctive product and that the major difference lies in the finest fraction:
In the “Sub-A” Flotation Machine (straight mechanical type), selectivity is carried down through all fractions to a much higher degree than in the pneumatic type. The “Sub-A” concentrate produced was much more desirable for thickening, filtering, and smelting, since a high degree of concentrating efficiency prevailed on the granular fractions and the semi-collodial gangue slimes were discarded into the tailing with a resulting lower alumina and magnesia content in the concentrate. The elimination from the concentrate of these undesirable gangue constituents produced a premium smelter feed.
The straight pneumatic machine showed a higher recovery of the finer fractions as evidently this product was carried over mechanically with the froth and with low concentrating efficiency. The fine mineral recovered had no economic value since the greater percentage of semi-collodial gangue matter in the concentrate offset the value of the mineral recovered. Analyses of composite samples of tailings covering the same period of operation are given below:
The conclusions that would be drawn from an inspection of the pneumatic machine tailing only, would indicate that finer grinding would be necessary to reduce the tailing losses. Since this machine does not favor the recovery of the coarser fractions, an appreciable percentage of the losses occur there. However, finer grinding will produce more minus 10-micron mineral particles and when the concentrate is analysed (see Table B) it is seen that values in this fraction yield no economic return.
When studying the “Sub-A” tailing it is apparent that this machine makes a higher recovery of the granular and coarser fractions and that finer grinding would not be the step necessary for improved recoveries. This machine has recovered 12 percent more plus 200-mesh mineral and by maintaining high concentrating efficiency in the minus 10-micron fraction, there has been a greater loss of the finest slimes.
A microscopic examination of the minus 10-micron fraction of the “Sub-A” tailing showed that practically all of the mineral lost was free and unattached. The approach to higher recovery in this case was to go to a coarser initial grind with more stress placed on improved classification to produce a smaller quantity of minus 10-micron sulphides in the flotation feed. In this particular case the tonnage through the “Sub-A” equipped unit was increased by about 12 percent and the tailing reduced to an average of 0.09 percent copper.
One’s first impression is that such a variance in character of mineral recovered and lost in the tailing is not reasonable and can only occur in isolated cases. However, it has been found in practically every case where there has been an opportunity to make these comparisons that the character of the concentrate produced is, within limits, controllable by the operator with the proper combination of flotation machine, reagents, grind, etc. Often recovery can be improved in attaining a concentrate which is more desirable for subsequent treatment. The figures given in tables A, B, and C do not represent the extremes encountered.
Below is given the screen analyses from another plant where “Sub-A” Machines were operating in parallel with a combination pneumatic-mechanical unit on split feed, and where the screen analyses and assay figures were made on composite samples representing a 14-shift operating period:
Here ordinary screening disclosed an almost unbelievable difference in the tailings of the two circuits, and the concentrates. A continual repetition of this condition in the minus 325-mesh fraction of the tailings with as high as a 16-point difference led to a close study of the finer fractions, and it was seen that the pneumatic-mechanical unit was making a bulk recovery of practically all the minus 10-micron fraction in the ore without any concentration or selection. The high percentage of alumina in this fraction of the concentrates not only made this product extremely difficult to handle in the plant dewatering equipment, but also highly undesirable from a smelting point of view as capacity was reduced and high slag losses resulted.
It has been demonstrated that semi-collodial mineral particles can be concentrated by flotation with a remarkable degree of efficiency when treated alone. The reagent combinations and the degree of dispersion or flocculation that favors their treatment is seldom the same as one would use for the more granular fractions. Since the major percentage of the recovered minerals are in the granular fractions the circuit should be operated under conditions which favor their recovery. Thus, the bulk of the tailing loss is usually in the semi-collodial sizes and this has created the impression that these finest mineral particles cannot be recovered.
There are rarely sufficient values in this finest fraction to warrant individual treatment, and this leads to a more practical viewpoint which is produce less slimes and lose less fines. This thought has been generally accepted and has led to improvements in grinding and classifying techniques and the use of a recovery step in the grinding circuit.
No longer is it necessary to take the attitude that “here is the concentrate that our ore yields”. Not only can the minerals be recovered in the concentrate, but also the chemical analysis of the insoluble fraction can be controlled. Today one sees operations where the concentrator superintendent is given the specifications of the concentrate that he is to produce in the interest of highest efficiency for the entire unit operation. Through intelligent study and research these certain specific requirements are met and often bettered.
A few short years ago such control would have been thought impossible, and while today we find it in only a few cases, we predict that the next decade will see this as a universal practice. Progressive management now appreciates that the mine, the concentrator, and the smelter must all work together for the greatest economic return. With the concentrator in a key position, they must have their own research facilities or use those of outside test laboratories who make a specialty of ore testing and cost analysis.
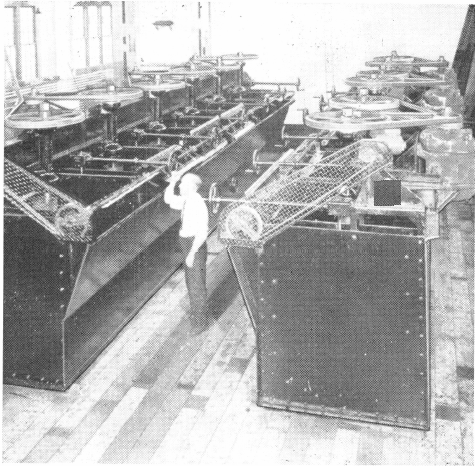
In our own experience, we have advocated “coarse concentration” and “take out your mineral when free” since the inception of Equipment Company. Through trial and error it was found that in the vast majority of cases recoveries could be increased and grade of concentrates improved, either through the use of the Flash Flotation Cell or the Mineral Jig, by removing freed mineral ahead of final fine grinding. Like many operators, we often thought that pure chance played a part in this. The scope of laboratory research has been limited because of the inability to duplicate actual plant closed-circuit grinding conditions, and it has only been since the engineer could actually examine and study products from the operating plants that he could see that “chance” is not a factor.
Now it is being recognized that with the correct flotation machine and reagents even coarser minerals can be recovered and a casual inspection of a screen analysis does not bring the conclusion that the high values in the coarser fractions are attached minerals, and with the knowledge that these minerals can be recovered, we are assured of a trend towards “coarser flotation” in the future.
The operators who are uncovering these “unseen factors in flotation” are finding that the concentration step is one that can be controlled to improve the final cost of finished metal by making a product which can be smelted at lower cost and with lower slag losses.
Source: This article is a reproduction of an excerpt of “In the Public Domain” documents held in 911Metallurgy Corp’s private library.