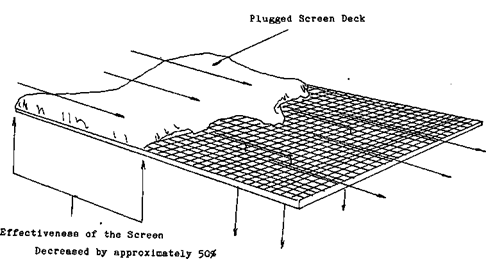
When you are supervising a set of screens these are the variables that you have to watch for:
- SPEED OF VIBRATION:
- DEGREE OP SLOPE:
- TONNAGE:
- WETNESS or Moisture OF THE ORE:
- MECHANICAL CONDITION:
The operator will have two or three indications that
As an operator you have control over two of these variables, mechanical condition and Tonnage. The speed of vibration and the degree of slope are pre-set. The range of vibration is 1000 to 3500 RPM and the degree of slope works best between 15 to 35 degrees. The last one, degree of ore wetness is effected by forces outside the confines of crushing. This is controlled either by nature or by the method of dust control. This last one affects the screening performance by clogging the screen deck so nothing will go through the grid pattern.
The first is that the amount of fines in the coarse ore discharge will visibly increase, the vibration of the screen will become more erratic or violent, and if there is an AMPERAGE GAUGE connected to the screens drive motor it may begin fluctuating wildly.
The violent vibration and fluctuation is caused by the same thing. The build-up of material on the screen deck. Having this extra weight unbalancing the screen is like pushing a wagon up a hill. A lot of work until you get to the top, then the wagon will go like mad down the other side. That is what the electric drive motor is doing. Having to work very hard to get the weight of the screen to the top of the eccentric, then a free ride when the screen deck is on the down stroke.
Wet fines will also cause a problem with build-up in chutes and transfer points. If this isn’t checked constantly then the operator is running the risk of plugging chutes and creating down time for the equipment. The extra fine rock that is in the coarse rock discharge is of course caused by the holes in the screen deck being blanked off. The fine material will then have to escape with the bigger rock.
As you can imagine, all of this vibration and ore movement causes a lot of wear on the metal and mechanical parts of the screens. The main area that you will have to watch is the decking itself. These screens have a lot of wear on them. The holes that are in the grid pattern become larger as they wear. It is one of the operator’s chores to check the condition of the screens. When a hole in the screens appear
it will have to be repaired. How this is done will depend upon the type of screen that is in the deck.
Image #2 is a schematic diagram showing how the screening effect varies along the screen deck. Stratification takes place within zone 1, screening of fine undersize particles (75% of the size of the screen apertures) takes place within zone 2 and screening of “critical” undersize particles, i.e. particles of a size close to the size of the screen apertures, takes place within zone 3. It therefore leads to the conclusion that slurry thickness/density is the starting issue.
Whether the above hypothesis is correct or not, what is observed is a thick doughy slurry passing over the screen deck and thick doughy slurries do not screen (image #1).
Screening is best done using 0.7 to 1.1 ton of water for every 1 ton of rock.
The objective is not spraying water on the screen, it is to dilute the feed to the screen. An alternative to trying to spray on water is to install a simple measured ‘water blade/fall’ at the front of the screen deck. This water addition point would replace most of the ball mill cyclone feed water.