Detoxification processes are used to reduce the concentrations of toxic constituents in tailings streams and process solutions, either by dilution, removal, or conversion to a less toxic chemical form (sometimes referred to as“destruction” or “degradation” in the case of toxic cyanide species). The objective is to produce an effluent that meets limits or guidelines that have been set to conform with the environmental and/or metallurgical requirements of the project. This section discusses methods of detoxification which may be applied individually or as combinations of processes (e.g., with reagent and metal recovery processes) to achieve the detoxification objectives.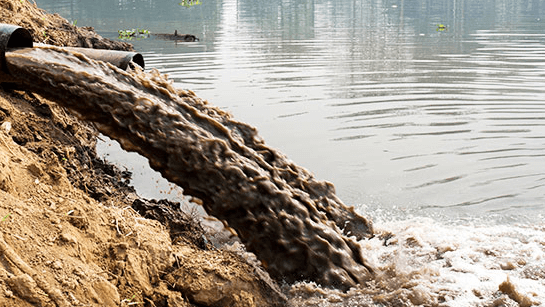
The most important constituents are cyanide species and heavy metal ions, which are considered in the following sections. The control of other solution components and conditions (e.g., sulfate, chloride, and nitrate concentrations, pH, conductivity, turbidity, etc.) may also be important under particular circumstances; however, specific methods for their control are not considered further here.
The methods available for cyanide detoxification can be grouped in the following categories:
Cyanide removal
– Natural volatilization
– Adsorption onto minerals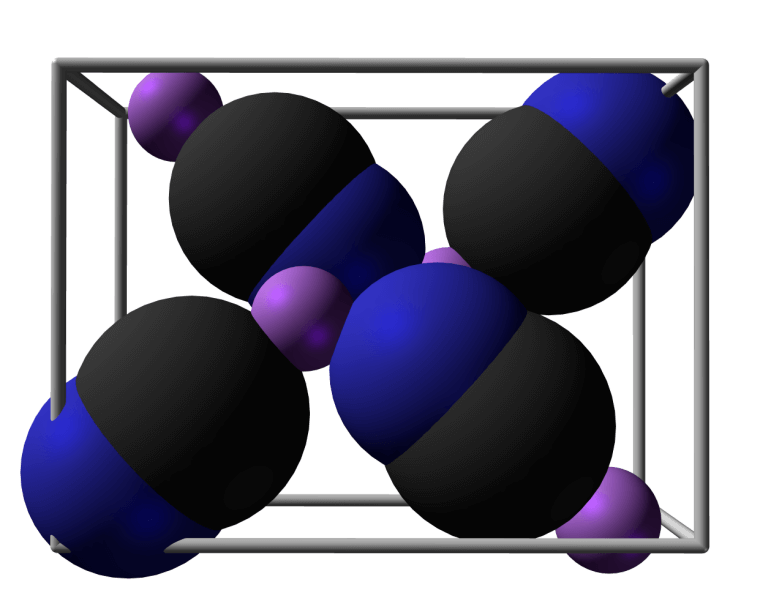
Oxidation to the less toxic cyanide species
– Natural oxidation
– Iron complexation
– Hydrogen peroxide process
– Sulfur dioxide–assisted process
– Alkaline chlorination process
– Biological oxidation
– Ozonation
Complexation to less toxic Fe(II) cyanide, with the potential for removal as an insoluble double salt.
The Chemistry of Gold Extraction By John Marsden, Iain House
Oxidation Oxidation Effectiveness |
Remediation Process |
Free Cyanide |
Thiocyanate |
WAD Metal Complex
(weak acid dissociable) |
SAD Metal Complex
(strong acid dissociable) |
Near Further Treatment |
|
|
|
Cd/Zn |
Cu/Ni |
Fe |
Others |
|
Bio-Oxidation (Bacterial) |
yes |
yes |
most |
most |
yes |
yes |
little |
Catalysis |
yes |
|
yes |
yes |
no |
some |
yes |
Electro-Oxidation |
most |
yes |
most |
most |
no |
no |
yes |
Electro-Chlorination |
yes |
yes |
yes |
yes |
no |
no |
yes |
Alkaline-Chlorination |
yes |
yes |
yes |
yes |
no |
no |
yes |
Oxygen |
yes |
some |
some |
no |
no |
no |
yes |
Ozone |
yes |
yes |
yes |
yes |
no |
no |
yes |
Hydrogen Peroxide |
yes |
no |
yes |
some |
some |
no |
yes |
Hydrogen Peroxide/Cupric |
yes |
no |
yes |
yes |
yes |
no |
some |
Hydrogen Peroxide/Kastone |
yes |
no |
yes |
yes |
Yes(ppt) |
no |
some |
Caro’s Acid |
yes |
yes |
yes |
yes |
yes |
no |
Little |
Sulfur Dioxide (INCO) |
yes |
some |
yes |
yes |
Yes(ppt) |
most |
Little |
Direct Photolysis |
no |
no |
no |
some |
yes |
some |
yes |
Photolytic Ozonation |
yes |
yes |
yes |
yes |
yes |
yes |
no |
Photolytic Per Oxidation |
yes |
yes |
yes |
yes |
yes |
yes |
no |
TiO2 Photocatalysis |
yes |
yes |
yes |
yes |
yes |
yes |
no |

Comparison of processes for cyanide removal and detoxification for solution
Cyanide Removal and/or Detoxification Treatment Method |
CN-HCN |
Zinc and Cadmium Cyanides |
Copper and Nickel Cyanides |
Fe(II) CN |
SCN– |
Products |
Require Further Treatment |
Metals |
CN– |
Metals |
CN– |
Natural |
Y |
Partial |
Partial |
N |
N |
N |
Partial |
Decant Solution |
Probably |
Fe complexation |
Y |
Y |
Y |
Partial |
Partial |
N |
N |
Decant Solution |
Probably |
H2O2 |
Y |
Y |
Y |
Partial |
Partial |
Partial Precipitate |
N |
Treated effluent |
May |
SO2 |
Y |
Y |
Y |
Y |
Y |
Partial precipitate |
Partial |
Treated effluent |
May |
Cl2 |
Y |
Y |
Y |
Y |
Y |
N |
Y |
Treated effluent |
May |
Biological |
Y |
Y |
Y |
Y |
Y |
Partial |
Y |
Treated effluent |
N |
O3 |
Y |
Y |
Y |
Y |
Y |
N |
Y |
Treated effluent |
May |
AVR (acidification, volatilization, and
reneutralization) |
Y |
Y |
Y |
Y |
Y |
Y |
Partial |
Treated effluent or Recycle solution |
Y |
Ion exchange |
Au, CN as complexes |
Y |
Y |
Y |
Y |
Y |
Y |
Possible |
Recycle solution |
N |
CuCN-treated resin |
Y |
Y |
Y |
Y |
Y |
Y |
Possible |
Recycle solution |
Y |
Carbon
|
Granular |
Y |
Y |
Y |
Y |
Y |
Partial |
? |
Treated effluent |
N |
Powder |
Y |
Y |
Y |
Y |
Y |
Y |
? |
Treated effluent |
May |
Electrolytic
|
For CN recovery |
Most |
Y |
Most |
Y |
Most |
N |
Y |
Treated effluent |
N |
For CN destruction |
N |
Y |
N |
Y |
N |
N |
N |
Treated effluent |
May |
Flotation (ion precipitation) |
Partial |
Partial |
Partial |
Y |
Y |
Y |
? |
Treated effluent |
May |
Natural Attenuation
The natural degradation of cyanide is well established and has historically been the preferred method. In climates like Australia where cyanide degradation is enhanced by high temperature this is an appropriate strategy.
The downside is the negative impact on the environment particularly birds and fish or native animals such as kangaroos and emus. Seepage of cyanide water into groundwater is now causing authorities to insist on lined tailings dams (i.e. Boddington which also has DETOX).
Going forward, this is less likely to be the preferred method due to local environmental issues.
Alkaline Chlorination
Alkaline chlorination is the oldest chemical process for the treatment of cyanide wastes. Nowadays it is used primarily in the plating industry because it has recently fallen out of favour due to the environmental complications of the process. In alkaline chlorination, hypochlorite ions oxidize cyanide to form CO2 and N2 gases according to the following reactions:
CN- + H+ + ClO- → CNCl + OH- (1)
CNCl + 2OH- → CNO- + Cl- + H2O (2)
2CNO- + 3ClO- + H2O → 2CO2(g) + N2(g) + 3Cl- + 2OH- (3)
All these reactions are dependent on pH, which must be over 10 in reactions (1) and (2). The optimal pH for reaction (3) is 8.5. Oxidation destroys free cyanide and cyanide complexes, except for iron cyanide complexes. One of the major disadvantages of this method is the potential for forming chlorinated organics. Some of the products (e.g. cyanogen (CN)2) are even more harmful and toxic than cyanide itself. This was an issue at the Henty gold mine causing them to switch to the INCO process.
INCO SO2/Air
Inco of Canada developed a specific cyanide destruction process which is used around the world to detoxify cyanide plant tailings.
The SO2/Air process is no longer proprietary technology and no longer requires a license prior to its use. It uses an agitated tank into which SO2 (in liquid, as metabisulfsulfite, or in gas form) is added with air to work on the cyanide remaining in any type of total tailings, and water recycled from an impoundment area. A very small amount of soluble copper must also be present to serve as a catalyst. The process offers continuous single-stage operation. Despite being a simple process, optimisation is different for each cyanide tailings tested.
As a fail safe operation the tailings are often processed in batches using two storage tanks with the tailings from a tank only being pumped to tails after measurements have determined that no cyanide is present.
The oxidising agent consists of air or liquid oxygen for the O plus SO either in gaseous or liquid form. Other reagents normally include CuSO, and lime or NaOH for pH control. The oxygen via air sparging and the reagents are dispersed in the effluent using a well-agitated mixer. Retention times are variable, depending on the composition of the solution to be treated, but generally range from 20 minutes to 2 hours.
Stoichiometrically, the reactions, as described in Table 1, require about 2.46g of SO per gram of WAD cyanide. After treatment, cyanide levels are reduced to between 0.1ppm (0.00001%) and 0.5ppm. The process does not produce any toxic intermediaries.
A WAD laboratory cyanide analysis unit is used to monitor the process.
The INCO process is robust and widely used throughout the gold industry.
Hydrogen Peroxide
The hydrogen peroxide treatment process chemistry is similar to that described for the INCO process, but hydrogen peroxide is utilized rather than sulfur dioxide and air.
With this process, soluble copper is also required as a catalyst and the end product of the reaction is cyanate.
H2O2 + CN- → OCN- + H2O
The primary application of the hydrogen peroxide process is with solutions rather than slurries due to the high consumption of hydrogen peroxide in slurry applications. The process is typically applied to treat relatively low levels of cyanide to achieve cyanide levels that may be suitable for discharge. The hydrogen peroxide process is effective for the treatment of solutions for the oxidation of free and WAD cyanides, and iron cyanides are removed through precipitation of insoluble copper-iron-cyanide complexes.
The theoretical usage of H2O2 in the process is 1.31 grams H2O2 per gram of CN- oxidized, but in practice the actual usage ranges from about 2.0 to 8.0 grams H2O2 per gram of CN- oxidized. The H2O2 used in the process is typically provided as a liquid in 50% strength. The reaction is typically carried out at a pH of about 9.0 to 9.5 for optimal removal of cyanide and metals such as copper, nickel and zinc. However, if iron cyanide must also be removed to low levels, then the pH is lowered somewhat to increase the precipitation of copper-iron-cyanides at the expense of lowering the removal efficiencies of copper, nickel and zinc. As indicated, copper (Cu2+) is required as a soluble catalyst, which is usually added as a solution of copper sulfate (CuSO4-5H2O) to provide a copper concentration in the range of about 10% to 20% of the initial WAD cyanide concentration.
This process is capable of achieving low levels of both cyanide and metals. Solutions treated with this process may be of suitable quality to permit their discharge. The cost of hydrogen peroxide is high.
Ferrous Sulfate
Free, WAD and total cyanides will all react with ferrous iron to yield a variety of soluble and insoluble compounds, primarily hexacyanoferrate (III) (Fe(CN)3-), Prussian blue (Fe[Fe(CN)]) and other insoluble metal-iron-cyanide (MFe(CN)6) compounds such as those with copper or zinc (Adams, 1992).
Fe2+ + 6CN- + ¼O2 + H+ → Fe(CN)63- + ½H2O
4Fe2+ + 3Fe(CN)63- + ¼O2 + H+ → Fe[Fe(CN)6] + ½H2O
The iron-cyanide precipitation process is limited in its suitability to situations where the precipitation reactions can be controlled and the precipitated solids can be separated and properly disposed. The process has fallen out of favour. The process is optimally carried out at a pH of about 5.0 to 6.0 and iron is added as ferrous sulfate (FeSO4-7H2O).Ferrous sulfate usage ranges from about 0.5 to 5.0 moles Fe per mole of CN- depending on the desired level of treatment.
Caro’s Acid
Peroxymonosulfuric acid (H2SO), also known as Caro’s acid, is a reagent used in a recently developed cyanide treatment process that has found application at a few sites.
H2SO + CN- → OCN- + SO42- + 2H+
Caro’s acid used in the process must be produced on-site using sulfuric acid and hydrogen peroxide since Caro’s acid decomposes rather quickly. Caro’s acid is used in slurry treatment applications where the addition of a copper catalyst is not desirable, which is typically only in situations where the sulfur dioxide and air process is not suited. In solution applications, other destruction processes, such as the hydrogen peroxide process, are preferred to the Caro’s acid process.
The theoretical usage of H2SO in the process is 4.39 grams H2SO5 per gram of cyanide oxidized, but in practice 5.0 to 15.0 grams H2SO5 per gram of cyanide oxidized is required. Acid produced in the reaction is typically neutralized with lime.
Ozonation
Treatment of cyanide bearing wastewater has been carried out with ozone.
Advantages of ozone oxidation include:
Extremely effective against all free and complexed cyanides either alone or in combination with UV light
Does not form any undesirable by products such a chlorinated organics or ammonia
Does not require the purchase, storage or handling of dangerous chemicals on site
Ozone is produced on site from air using an ozone generator
The reaction with ozone does not require high temperatures or pressures
Ozone, with an electrode potential of +1.24 V in alkaline solutions, is one of the most powerful oxidizing agents known.
Cyanide oxidation with ozone is a two-step reaction similar to alkaline chlorination. Cyanide is oxidized to cyanate, with ozone reduced to oxygen per the following equation:
CN– + O → CNO– + O2
Then cyanate is hydrolyzed, in the presence of excess ozone, to bicarbonate and nitrogen and oxidized per the following reaction:
2 CNO- + 3O3 + H2O → 2 HCO3- + N2 + 3O2
The reaction time for complete cyanide oxidation is rapid in a reactor system with 10 to 30 minute retention times being typical. The second-stage reaction is much slower than the first-stage reaction. The reaction is typically carried out in the pH range of 10-12 where the reaction rate is relatively constant. To complete the first reaction requires 1.8 – 2.0 gram of ozone per gram of CN-.
The metal cyanide complexes of cadmium, copper, nickel, zinc and silver are readily destroyed with ozone. The presence of copper and nickel provide a significant catalytic effect in the stage one reaction but can reduce the rate of the stage two reaction (oxidation of cyanate).
Electrolytic Oxidation
Electrochemical oxidation is an alternative process for destroying cyanide ions at the anode and collecting heavy metals from the cathode. Free cyanide, cyanide complexes and concentrated cyanide solution can be handled with the electrochemical oxidation method.
First cyanide and cyanocomplexes become oxidized to form cyanate ions at the anode. The ions are then decomposed into carbon dioxide and nitrogen gas. Dissociated metal cations are reduced at the cathode.
Biodegradation
Cyanide is produced in the environment by plants, fungi and bacteria. Therefore, a number of micro-organisms and their enzymes have the ability to degrade cyanide and metal cyanide complexes (also stable iron cyanide complexes) into less toxic compound like ammonia, formic acid and formamide. Microbes can utilise these compounds as a source of nitrogen and carbon for their own growth. Reed beds are particularly effective in using cyanide and taking up heavy metals. In Finland cyanide solution was used to irrigate pine trees which flourished on the cyanide.
NaCN Detox Experts
Hydrogen Peroxide Cyanide Destruction Plant