In mineral processing or metallurgy, the first stage of comminution is crushing. Depending of the type of rock (geometallurgy) to be crushed, there are 2 largely different techniques at your disposition for crushing rocks. In principle, compression crushing is used on hard and abrasive rocks by placing them between a high wear-resistant plate/surface. Less abrasive and softer rocks or stones are crushed by impact and shear but also compressive mechanisms produced by Rock Crushers.
After the mine has blasted the ore, the first reason why we crush rock is really to be able to transport it onto the next same. Conveyors and transfer chutes are limited in size and I say AMEN! to that as if you are left to the mining engineers, they’d blast and send 60″ rock to the SAG mill 😉
Since each size reduction stages of crushing is limited to around 6-to-1 (average), you need to blast as fine as possible to minimize the number of stages in crushing and crushers needed to reduce the run-of-mine’s hard-rock most economically as you can. Typical hard-rock crushers like jaw, gyratory and cones break rock by nipping the ore between a fixed/stationary and a moveable wear-resistant surface/liner.
How much reduction each crushing stage is capable of infliction of rocks (reduction ratio) is driven by the angles between the 2 surfaces on each side and holding the rocks-to-be-crushed as the move towards and away from each other.
Too large an angle will not grip the rock presented, while to small an angle will reduce the use of the potential size reduction that’s available to the operator. As gravity pulls the rock down from the top of the crushing chamber (feed) to the discharge (close-side-setting), all rocks undergo multiple impacts causing them to get crushed.
After TNT explosives, crusher are the most effective or efficiency rock size reduction hammer the mineral processing industry has. The more you crusher, the less grinding power and the smaller the grinding mills you will need. Since there are not that many small SAG mill operations of under 2000 TPD, and most sub-2000 TPD mills are built with rod mills and/or ball mills only; the upstream crusher plant needs to have sufficient crushing power to provide a P80 to grinding of typically <1.5″ (40 mm) and often as finely crushed as <3/8″ (9 mm). Producing such a fine crush generally requires multiple crushing stations of up to 4 being but as a minimum of 2 being oversized. The gape determines the maximum size of material that can be accepted. Primary crushers are designed so that the maximum size that can be presented to the crusher is approximately 80% of the gape. Jaw crushers are operated to produce a size reduction ratio between 4 :1 and 9 : 1. Gyratory crushers can produce size reduction ratios over a somewhat larger range of 3 :1 to 10 :1.
To feed a rod and/or ball milling circuit, you need to crush as follow:
Crushing Stage |
Crusher | Feed Size |
Product Size |
||
Primary |
Jaw/Gyratory |
Up to 60″ (1.5m) | 6″-12″ (150-300mm) | ||
Secondary |
Cone/HPGR |
|
|
||
Tertiary/Quaternary |
Cone/HPGR |
|
1/4″-1″ (5-25mm) |
Crushers for large giant process plants >2,000 to 200,000 TPD using semi-autogenous mills only require primary crushing and are selected as well as designed based on:
- Expected Throughput
- F80 Top Feed size distributions
- Desired P80 Product size distributions
- Feeding method
- Ore work index
- Ore bulk density
- Ore abrasion index (abrasivity)
- The rock’s compressive strength
- The ore clay content
- The ore’s fragmentability.
Soft and low abrasion rocks are offered a large selection of crushing machines to choose from. Not mentioned so far it the fact that because of the ‘no nipping angle restriction’ impactors and hammermills produce a much greater size reduction ratio. Impact crushers are commonly used to crush rocks with a silica contain under 5% such as coal, limestone, and phosphate. The only reason why you would use an impact mill/crusher or a hammer mill on a high-silica rock is because it might be sticky in nature and rich in clay. Such high abrasion/high silica impact/hammer crusher operation see extremely high maintenance costs having to be endured.
Common work index terms you need to review and understand as they relate to crushing:
The (Ai) Abrasion Index measures the abrasivity of rocks during its crushing. There are several ways or test methods at your disposition to obtain this number including the Angeles Abrasion Test and the Deval Abrasion test.
The most common abrasion test however, is the Bond method where a 76x25x6mm (3x1x0.25″) piece of 500 Brinell SAE 4325 chrome-nickel-molybdenum steel rotates in a falling stream of rocks under standard predetermined conditions to measure its weight loss. The resulting Ai is used to predict crusher liner wear rates.
The Compressive Strength of rocks is measured by crushing cylinder shaped (drill core) ore samples of 2″ x 2″ (51mm X 51mm). This techniques allows for a rock-to-rock relative comparison.
The Bond’ Crushing Work Index is common to calculate the power needed to crush rocks from a given F80 size to a resulted P80 product size. Bond’s impact method comes from a double mirrored pendulum impact crusher test on <76mm but >51mm (3″ and 2″) square rock pieces. The resulting consumed power is calculated using Bond’s standard equation. See how BWi relates to Ai.
A Crusher’ Settings 3 main parameters are changed to obtained a targeted P80 product size:
- Open-side settings OSS, often ignored is the maximum distance between the crushing surfaces in the open position.
- Closed-side setting CSS, most hyped but misunderstood and underutilized as the minimum distance between crushing liner surfaces/plates in the fully closed position.
- The Crusher throw is defined as the distance in the direction of compression the moving crushing surfaces/plates travel from OSS to CSS.
Throw = OSS – CSS.
OSS and CSS will define a crusher’s performance. The throw of the crusher is the distance that moving jaw moves in going from OSS to CSS. The capacity is a function of size and OSS. Manufacturers publish tables of capacity for their crushers of various size as a function of the open-sid
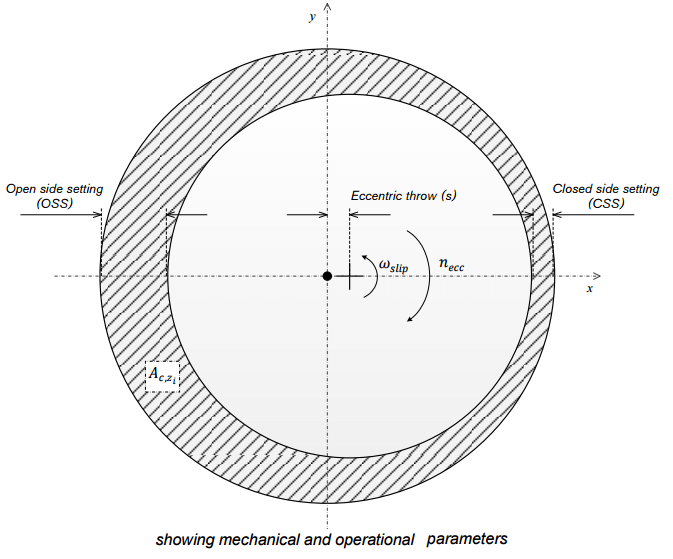
Modeling and Simulation of Mineral Processing Systems By R. Peter King and https://www.metso.com/