We will help you create an operating system/environment that maximizes the production of a product that is marketable and returns sustainable revenues while reducing the costs of production.
How:
- Determine ore resource and mining variability.
- Evaluation of the process flow-sheet.
- Seek limiting factors that constrain production.
- Determining available resources that impact production, maintenance and operating capabilities.
- Investigate ‘at hand’ resources to effect changes if required.
- Analyse consumption and type of consumables.
- Audit process accounting and analytical practices, including sampling procedures.
- Never-ending pursuit of process stability.
- Ensure that adequate planning capabilities exist towards achievement of goals.
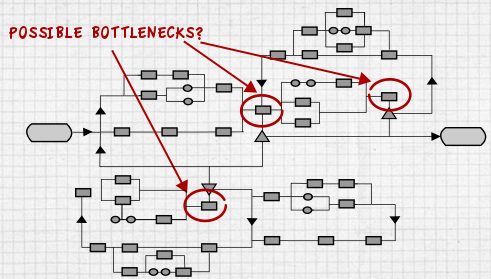
Although improvements to the process(s) have been made over the years the fact is that the unit operations involved have not changed since they began. Ore is reduced in size, chemicals are added and minerals separated and upgraded to produce a marketable product.
The most important aspect of an operating process is stability. This is simple to say, but it is one of the ongoing battles in mineral processing. Linked unit operations require each to be stable, and each contains a different set of variables that have to be contended with. With a degree of stability: operating changes can be made and evaluated; increases in throughput can be undertaken; and equipment performance improved. The more complicated the processes become the more difficult it is to achieve and maintain stability.
Invariably, the ability to solve problems can be confusing due the large numbers of variables that may impact the processes. In most cases problems are not metallurgical in nature but rather operational and mechanical. Problem solving is a process and in many operations this ability is absent. All too often, many changes are made together without a solution resulting.