To accomplish this reduction in size takes several steps or stages of crushing and grinding. Primary crushing is the first of these stages. Generally speaking there are two types of primary crushers, lets compare them: GYRATORY CRUSHER or a JAW CRUSHER. Although they don’t look anything like they do have similarities that put them into the same class of crusher.
Their CRUSHING SPEEDS are the same, 100 to 200 revolutions per minute. They both break the ore by COMPRESSION. That is they both break the rock by squeezing it until it breaks. On the average their final product will measure about seven inches at its widest point. And finally they both can be built to accept a rock up to sixty inches across.
Discuss the difference between crushers.
Even if they are much alike, each of the two types of crushers has its own uniqueness. Because of this difference each type of crusher has its own environment that it operates best or at least better in, than the other. As an example, a gyratory crusher can be fed from two sides and handle ore that tends to slab. Also its design allows a higher speed motor with a high reduction ratio between the motor and the crushing surface. This is an important consideration as it means money saved in energy costs. A jaw crusher on the other hand requires a flywheel to store energy but can be used on the tougher ores due to its box frame construction. To be effective it must be fed from one side only but it handles square block-like ore well.
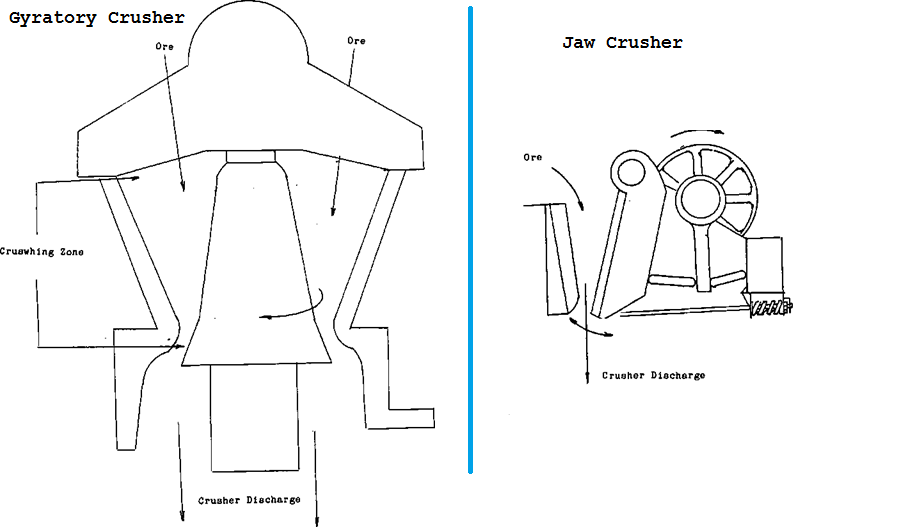
There is another comparison that should be taken into consideration, that is the amount of space that each takes. The Jaw crusher is the smaller of the two and its single feed point will make it a logical choice for underground workings.
In the actual operation of the crushers, they both have similarities as well as differences so let’s take each one separately and discuss its design and its problems. Considering the title of this chapter is Primary Crushing (Gyratory) we should discuss that one first.
In the introduction I mentioned that the purpose of a concentrator was to produce a concentrate of which ever mineral was being mined.
To be able to recover this mineral it is necessary to reduce the ore in size until the mineral is LIBERATED. This means that the ore must be reduced in size until it is fine enough to be able to separate the mineral from the unwanted rock. In the Vocabulary of the metallurgist, at this point of the operation the unwanted rock will be termed the GANGUE material. You will notice that the terminology used for the ore will change depending upon the stage of concentration. The reason for this is to keep technical communication accurate.
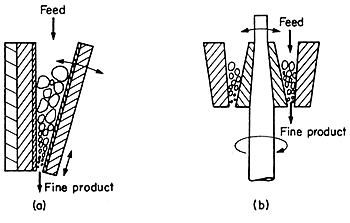