Table of Contents
The simplest grinding circuit consists of a ball or rod mill in closed circuit with a classifier; the flow sheet is shown in Fig. 25 and the actual layout in Fig. 9. This single-stage circuit is chiefly employed for coarse grinding when a product finer than 65 mesh is not required, but it can be adapted for fine grinding by substituting a bowl classifier for one of the straight type so as to enable the W/S ratio of the overflow to be kept below the 4/1 limit usually necessary for flotation. On account of the greater efficiency of the bowl classifier the trend of practice is towards its installation in plants grinding as coarse as 65 mesh.
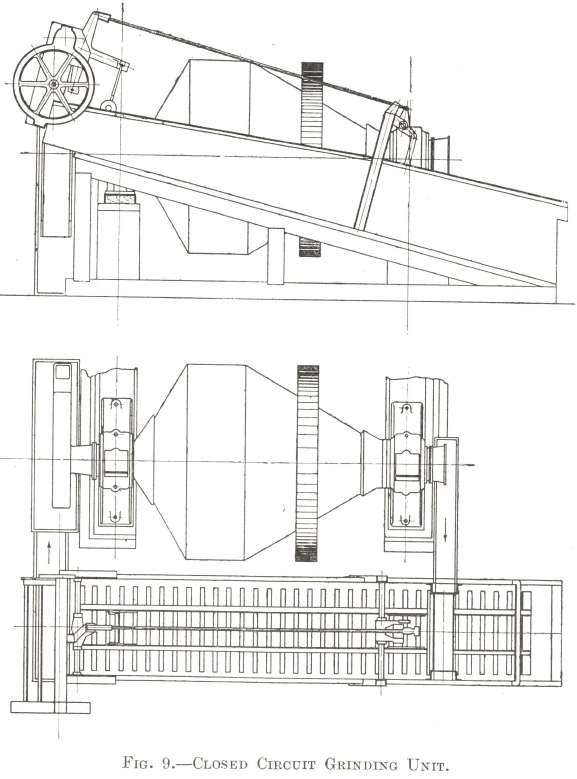
Single-stage grinding is generally to be recommended for small plants on account of its simplicity. Variations in the size and character of the ore are unavoidable in most plants, but they are, as a rule, very much more noticeable when operations are on a small than when they are on a large scale. Multi-stage grinding as practised in large installations may, therefore, prove impossible to control on a very small scale, and for this reason the simplicity of single-stage grinding is likely to result in a greater overall efficiency than would be obtained with a multi-stage arrangement. When, however, the capacity of a plant approaches or exceeds 1,000 tons per day, two-stage grinding becomes preferable because the effect of normal variations of the ore is less marked and control becomes correspondingly easier.
The usual type of two-stage circuit is shown in Fig. 26, and is one that can be employed for any degree of grinding, although a straight must be substituted for a bowl classifier in the second stage when a 48-mesh product is required. It used to be the practice at one time to omit the first classifier and to pass the feed straight through the primary mill to the secondary circuit, but it was not a good method because either the secondary mill received pieces of ore that were too big or else the primary mill overground a large proportion of the feed. Much better results are obtainable by keeping the coarse ore circulating round the primary circuit, which is set for the efficient grinding of such material, until it is fine enough to be sent to the secondary circuit where the machines are set to grind fine ore more efficiently than coarse. It should be noted that the overflow of the primary classifier is sent to the secondary classifier, not direct to the mill, in order that all material which has been ground fine enough in the primary circuit can be discharged immediately without any chance of its entering and being overground in the secondary ball mill.
So important is it from the point of view of efficiency to get the undersize out of the circuit at the earliest possible moment, whether it is produced in the primary or in the secondary mill, that a special intermediate bowl classifier is often installed between the two stages. Such an arrangement has been found very useful in plants in which improvements in dry crushing practice have resulted in a reduction in the size of the feed to the grinding mills with the result that they have been able to take larger tonnages; the classifiers have then become overloaded, especially in the case of older installations in which both stages were equipped with straight classifiers.
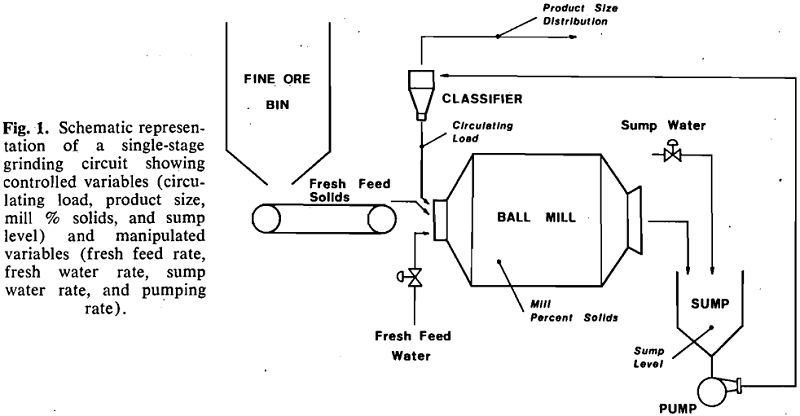
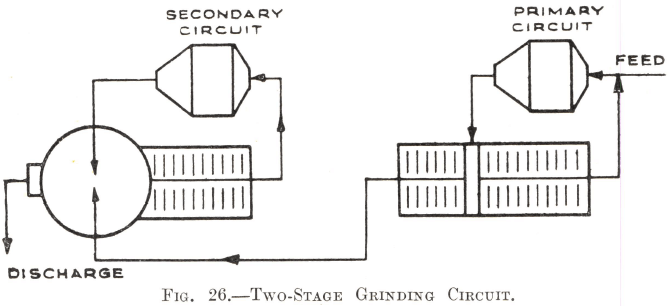
The method of installing a bowl classifier to overcome the difficulty is shown in Fig. 27. This circuit is usually adopted in modern practice, but with a bowl instead of a straight classifier, if necessary, in the closed circuit of the secondary ball mill.
Any increase in the efficiency of classification gives greater economy of power by reducing the amount of ore that is overground, so making a larger proportion of the power required to turn the mill available for grinding the particles that are still too large. From a theoretical point of view, the ideal method of grinding would consist of a series of ball mills, each in closed circuit with a classifier and each so short that the ore in its passage through the mill would be struck only two or three times by the balls, any undersize produced being removed at once by the classifier ; in this way the chance of a particle being struck again after it had reached the required size would be reduced to a minimum. Practice circuit design approaches the ideal:
- By making the length of a grate mill and of the cylindrical portion of a conical mill smaller than the diameter,
- by increasing the circulating load round the closed circuit so as to pass the ore more rapidly through the mill,
- by adopting two- and even three-stage grinding, each stage having its own system of classifiers, and
- by installing intermediate classifiers, where the gain in efficiency is worth more than the extra cost.
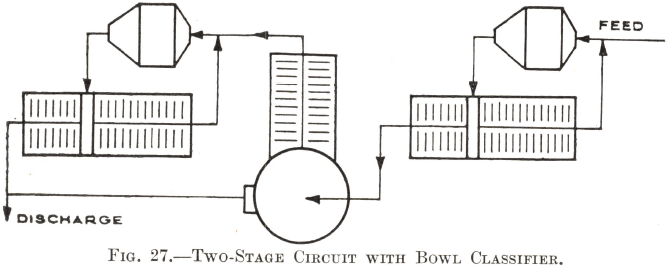
Open Circuit Grinding
Open circuit grinding consists of one or more grinding mills, either parallel or in series, that discharges a final ground product without classification equipment and no return of coarse discharge back to the mill. Some very simplistic examples of open circuit grinding are see below and are made of a Rod mill, Ball Mill or a Rod mill, ball mill combination.
Not all ores can be ground in an open circuit type of arrangement. Some conditions which do favor open circuit grinding such as small reduction ratios, reduction of particles to a coarse, natural grain size, recirculation of cleaner flotation middlings for regrinding and a non-critical size distribution of the final ground product.
Some advantages of operating in the open circuit mode vs closed circuit are the minimum equipment requirements, high pulp density discharge and the simplicity of operation.
Closed Circuit Grinding
Closed circuit grinding consists of one or more mills discharging ground product to classifiers which in turn return the coarse product from the size separation back to the mill for further grinding. In this circuit, grinding efficiency is very dependent upon the size separation effected so care should be exercised in selecting the type and size of classifier used to close the system.
This type of grinding is the most common circuit found in mineral processing facilities, mainly because a lot of ores and product requirements are not suitable for open circuit grinding. Some advantages presented by grinding in closed circuit are that this arrangement usually results in higher mill capacity and lower power consumption per ton of product, it eliminates overgrinding by removing fines early and it avoids coarse material in the final ground product by returning this material to the mill.
Although closed circuit grinding offers many choices for arrangement of the equipment as well as combinations of equipment, some of the more common circuits are rod mill/classifier, Ball mill/Classifier, Rod mill/Ball mill/Classifier and Rod mill/Classifier/Ball mill/Classifier.
![]() |
![]() |
![]() |
![]() |
![]() |
![]() |
Grinding Circuit Process Control Variables
The importance of the grinding circuit to overall production in any facility should be obvious by now. Because of the responsibilities assigned to grinding it becomes essential that a grinding mill accepts a certain required tonnage of ore per day while yielding a product that is of a known and controllable particle size. This leads to the conclusion that close control over the grinding circuit is extremely important.
There are many factors which can contribute to fluctuations in performance of a mill, but some of the most common found in industrial practice are the changes in ore taken from different parts of the mine, changes in crusher settings, wear in the crushers, screen damage in the crusher circuit.
These are a few things that operators should look for when changes in mill performance are noticed. Stockpiling of ore ahead of the mill can aid in smoothing out some of the fluctuations although it must be stored in such a manner that no segregation occurs.
In operating a grinding circuit, like any other unit process, variables key to the performance must be dealt with. Below are some of the principal variables affecting control of grinding mills.
Grinding Operating Costs
The reduction ratio in the grinding section is so much greater than in the crushing plant that labour becomes a relatively small item and the power and steel consumption the largest items of cost. Table 18 gives the average total consumption of power that may be expected in modern ball mill installations of various capacities up to 4,000 tons per day, the figures being based on an average medium-hard ore.
The cost of grinding is more difficult to predict than that of crushing because variations in the hardness and toughness of the ore produce proportionately wider variations in the consumption of power and steel. An approximate guide to grinding costs; they are direct costs and include no overhead charges. Power is assumed to cost 0.075 per kilowatt-hour in the case of the smallest plant and to decrease to a minimum per kilowatt-hour for the largest.
As the tonnage rises up to 1,000 tons per day the costs fall rapidly. In plants of greater capacity, however, they do not decrease in the same proportion with increase of tonnage, because the extra capacity is not obtained by increasing the size of the individual machines but by installing two or more similar units side by side, each of equal efficiency. Reduction of costs then becomes more a matter of organization than of plant design.
As already stated, the power and steel costs are the two largest items, those of labour and supplies being small by comparison ; it is on this account that recent progress has been mainly directed towards reducing the consumption of power and steel by means of greater efficiency in classification and by the use of mills of larger diameter.
The way in which the efficiency of classification has been increased has been described in the paragraph headed “Grinding Circuits”. An increase in the diameter of a mill gives greater economy in two ways : In the first place, the balls do more effective work in a large than in a small mill, because, falling from a greater height, they shatter the pieces of ore with greater force ; in the second place, the ratio of the deadweight of the mill to the weight of the ball charge decreases as the diameter increases and thus in a large mill the useless weight to be moved is distributed over a greater weight of useful ball load than in a small mill, with the result that a larger proportion of the total power consumption is available to give the balls the cascading and rolling action necessary to break up the ore.
It is essential for the grinding and flotation sections of a plant to be run continuously. It takes nearly half an hour to clear the circuit of even a small grinding unit preparatory to stopping it, and often an hour is necessary to get the circuit fully loaded after restarting ; most of the power required to keep the machines running during the stopping and starting periods is wasted. Moreover, the operation of the flotation machines is poor during these periods so that much of the power required to keep them running is also wasted. In addition, modern practice aims at the elimination of everything likely to cause fluctuating conditions. For these reasons it is the universal custom to run the grinding and flotation plants for 24 hours per day.