Table of Contents
The Problem with Calcite Processing & Flotation
The availability of high lime rock is often limited and it becomes necessary to use lower grade sources from quarries favorably located to cement plants. Beneficiation of the lime rock in such cases is necessary to remove impurities and to secure the proper ratio of calcite to other constituents for cement specifications.
Flotation has been very successfully applied to the cement industry in correcting the composition of the finely ground lime rock slurry prior to its introduction into the cement kiln for making cement. In many cases it is only necessary to divert a part of the slurry through flotation in order to meet requirements for the kiln feed. Flotation will provide a means for obtaining a consistent feed and a more uniform final product. Specifications vary, but generally 77-78% CaC03 is desired in the kiln feed.
The Calcite Flotation Flowsheet
In all cement plants it is necessary to crush the lime-rock and grind it down to the desired fineness for the kiln feed. In some operations specifications call for a grind of 90% minus 200 mesh and others to, all minus 50 mesh. This procedure follows even though no beneficiation is necessary, so the introduction of flotation into an existing plant is not a major investment. The grinding is usually done wet. A typical analysis of a lime rock treated by flotation is represented by the following:
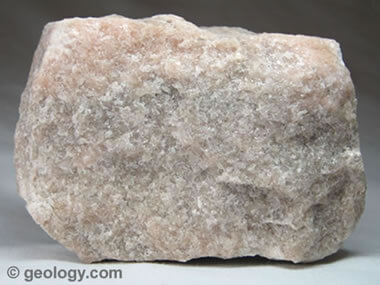
Calcite (including dolomite)………………………….. 69.5%
Silica (quartz) ………………………………………………. 10.3
Graphitic carbon ………………………………………….. 0.8
Iron pyrite …………………………………………………… 2.5
Sericite mica ………………………………………………… 16.7
Crushing Calcite Ore:
In the flowsheet a 2-stage open circuit crushing section is provided to reduce the lime-rock to approximately minus ¾” for feed to the ball mill. The size of the crushing equipment depends largely upon the quarrying operation and the size of the largest pieces delivered to the crusher. This depends also on the mining method used at the quarry and the size of the power shovel used for loading the trucks transporting the rock to the plant receiving bin. The Type “J” 32″x40″ or 36″x48″ Forced Feed Antifriction Jaw Crushers are ideal for primary crushing of lime rock, and the larger size has a capacity up to 300 tons per hour when reducing rock to 4″ size.
Grinding Calcite:
Crushed lime rock minus ¾” is fed to a Ball Mill in closed circuit with a spiral or rake classifier for reduction to final size for kiln feed or flotation. The flowsheet shows a circuit for grinding to approximately all minus 50 mesh. For very fine grind (90% minus 200 mesh), it may be necessary to use a Hydroclassifier in closed circuit with the primary classifier and mill. In such cases it is necessary to thicken the slurry prior to flotation treatment for the overflow from the hydroclassifier will be quite dilute.
Desliming Calcite:
In many cases it is possible to deslime ground lime rock and obtain an enrichment of calcite in the slime fraction. This is due to the calcite being softer than quartz; such practice is followed in treatment of certain marine deposits high in lime and silica, but low in other impurities such as graphite and sericite mica. A Hydro-Classifier is used for this purpose, although centrifuges and cyclones may also be employed under favorable conditions. The slime fraction, if enriched in calcite, can be combined with the high grade calcite flotation concentrate.
Removal of the slime fraction will generally make the flotation operation more positive and reduce the reagent costs.
FLOTATION OF IMPURITIES
If the ground lime-rock contains graphitic carbon and/or pyrite, these impurities are floated off and discarded to waste. Fuel oil or kerosene and a frother such as pine oil or methyl amyl alcohol are used to float the graphite. In case pyrite is present and it is desirable to remove it, a xanthate is added to float the sulphides into the froth waste product. The loss of calcite in this product will be very low. Flotation reagents are added to the conditioner and the “Sub-A” Flotation Machine, keeping them out of the grinding and desliming sections. Flotation density will vary between 20 and 30% solids, depending upon the degree of grinding required to liberate the impurities and to meet the kiln feed specifications.
FLOTATION OF CALCITE
The tailings from the impurity flotation section is conditioned with fatty acids such as oleic and reagent 708, the latter a vegetable fatty acid. Calcite is activated and floated into the froth concentrate while the sericite, quartz, and other silicates are depressed and rejected into the flotation tailing. The froth from the last 2 or 3 cells of the “Sub-A” calcite flotation circuit may be recycled, if desired to maintain grade and provide a final refuse low in calcite.
FLOTATION REAGENTS
In the flotation of calcite it may be desirable to depress and disperse any graphitic carbon carrying through from the impurity flotation section. Calcium lignin sulphonate has been used successfully for this requirement.
Saponifying the fatty acid with sodium hydroxide and feeding the resulting mixture as a 10% solution in warm water often improves the flotation selectivity on some lime-rock ores. A good grade of oleic acid may also be necessary although in certain cases a low- grade tall oil or a mixture of tall oil and oleic acid have been used with success. Typical reagents and quantities used are as follows:
Fatty acids are generally saponified and stage added to the flotation cells in an amount sufficient to give the desired grade of calcite in the froth product A 10 to 12 minute flotation time for the calcite is usually adequate.
THICKENING AND STORAGE
The flotation froth concentrate analyzing 80 to 85% CaCO3 is thickened along with the hydroclassifier slimes if the latter is high in lime. In some cases only a portion of these slimes can be blended back into the froth product for the final product must contain 77 to 78% CaCO3. Thickener underflow at 50 to 55% solids is drawn off by a Adjustable Diaphragm Pump and transferred to slurry tanks for further treatment and blending if necessary before introduction into the kiln for conversion into cement.
Summary
“Sub-A” Flotation provides a very effective and simple way for beneficiating limestone for use in cement. The flowsheet is simple, yet flexible, and provision is made for alternate flows in case a portion of the ground slurry can by-pass the beneficiating step. A uniform feed to the kilns can be provided by including flotation in the operation. It is a very successful method for breaking the lime-rock down into its component parts for blending back together in order to meet specifications.
Source: This article is a reproduction of an excerpt of “In the Public Domain” documents held in 911Metallurgy Corp’s private library.