Some time ago, we had to decide the question whether it would pay to re-treat slime-tailings, and several machines were tested in order to ascertain the type of construction which would give the greatest saving. In previous tests on the ore of this company, several tables proved far inferior to Vanning and for this reason they did not receive any serious consideration. In the late tests, however, one table was found to surpass the vanner in the percentage of saving made.
The Frue vanner used in these tests had been adjusted approximately to the slope which the slime-vanners in the concentrator had at that time, about 2 in. between the inside of the wooden posts, or 0.272 in. per ft. It had not been determined, however, if this slope was the most economical one for treating the slime-feed in the mill, or for re-treating the tailings from the slime-vanners, and I was instructed to ascertain by test-runs, under different conditions, the best adjustments for the work to be done.
In order to determine if a change in the adjustments of the machines would improve the results, it seemed sufficient to continue running the tests between the vanner and the table before mentioned, keeping the feed and all other conditions the same, but varying the adjustments of the vanner from run to run.
I employed a vanner-man of long experience to operate these machines, who expressed the opinion that a slope between 2 3/8 and 2.5 in. between the posts (0.323 and 0.340 in. per ft.) would give the best results.
Some runs made this way gave a considerable improvement. While for a slope of 2 in. (0.272 in. per ft.) the saving had been only 40.5 per cent, of that of the table, it was 49.2 per cent, for 2.5 in. (0.340 in. per ft.) slope. A decrease of the slope to 1.5 in. (0.204 in. per ft.) decreased the saving to 32.7 per cent, of that of the table. So far, these tests had been made with a smooth belt and with 224 (1-in.) side-strokes per minute. A reduction in the number of side-strokes from 224 to 188 increased the saving several per cent., and an increase of the slope to 3 in. (0.408 in. per ft.) added 8 per cent, to the saving.
An old corrugated belt was then tried, starting with 2.5. in. slope (0.340 in. per ft.). The saving was 78 per cent, of the saving of the table; for 3.5 in. (0.476 in. per ft.) it was 97 per cent., and for 4.5 in. (0.612 in. per ft.) the vanner made a better saving than the table. A decrease in the number of side-strokes slightly increased the saving.
These results could be interpreted in two ways. It was possible that the pulp, which had once gone over a vanner with a somewhat flat smooth belt (all vanners in the concentrator had smooth belts at that time), was not fit for re-treatment on a machine with practically the same adjustments. To take out mineral that could not be saved on the first vanner, either the smooth belt might have to be set steep, or a corrugated belt might have to be used. On the other hand, there was a possibility that the vanners in the concentrator had been run too flat, and therefore did not save all that could be saved. In this case a steeper setting of the vanners would increase the saving and would possibly make a re-treatment of the tailings unnecessary.
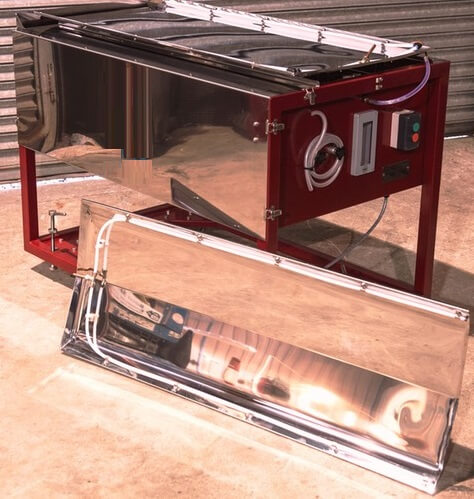
Since smooth belts only were in use, the first work was to determine the best adjustments of a Frue vanner with a smooth belt for treating fine feed. The second, to ascertain if a corrugated belt will do better on slime-feed than a smooth belt. Of course, any such difference in the saving for different adjustments, as reported above, could not be expected for the regular slime-feed, from which a large amount of concentrate can be easily extracted by almost any machine, while on a pulp which has already gone over a concentrating-table once, one machine may have hardly any effect, while another may save a considerable amount of mineral.
Some tests with different adjustments (mainly different slopes) convinced me that on this feed a higher slope also increased the saving. Since, however, this view was diametrical to the former practice in the concentrator of the Detroit Copper Co., according to which slime-feed was treated on belts set as flat as possible (with the idea that the slimes should get a very small chance to run off), my views found opposition, and it was decided to have a contest, in which an experienced millman ran a vanner according to the established practice, while I ran another machine on the same feed according to my ideas. Two vanners were set side by side and fed by slime-pulp from a revolving distributor, so as to send the same amount of feed of the same quality to the two smooth-belt vanners. Four runs were made, averaging about 7 hr. each, from which the concentrates were collected, weighed, and assayed. One time the contestants changed machines between two runs. On an average of the four tests, the machine with the higher slope saved 10.1 per cent, more copper than the machine with lesser slope. One other point brought out by the contest was that, in order to effect a high saving, a certain amount of water, probably in excess of what is generally used on slime-vanners, is required.
The results of this contest indicated that it is possible to save a considerable part of the copper that heretofore has been lost, and that it would probably pay to determine accurately and systematically the most economical adjustments of a vanner in treating this feed.
The right way to find the best adjustments of a vanner for a certain feed is to vary all the elements that can be varied, and to determine the saving resulting from different combinations of adjustments. Since there are several variations possible, this scheme requires a large number of tests.
The principal elements which can be varied on the Frue vanner are : (1) the slope of the belt, (2) the amount of dressing-water, (3) the number of side-strokes, and (4) the speed of the belt. If each of these elements has a certain value, the machine will for a certain quality and quantity of feed produce a certain grade of concentrate. In practice, however, the grade of the concentrate which has to be made on the vanners will be a given quantity. It will be stipulated, for instance, to make a grade with only 10 or 20 per cent, of silica. This condition makes the above mentioned adjustments interdependent. For instance, with a given number of side-strokes per minute, and a given slope of the belt, the vanner-man can either use a certain amount of dressing-water and regulate the speed of the belt, or he can give the belt a certain speed and regulate the dressing-water so as to produce the desired grade of concentrate.
In most of these experiments the former way was chosen— namely, a certain quantity of dressing-water per minute was used. For this purpose a funnel was constructed, Fig. 1, having the opening, A, closed by a wooden plug, B, with an inserted glass tube, C. At the wide end of the funnel a tube, D, branches off. The funnel is set on a nipple, E, screwed on the pipe, F, which carries the dressing-water to the water-distributing box of the vanner. The water enters the funnel
through its upper end. The inflow is so regulated that it fills the funnel and gives a small overflow through the pipe, D. As long as this small overflow is maintained the water running through the glass tube, C, is always under the same pressure, and the quantity passing through is constant. By changing the glass tube the quantity of dressing-water can be varied.
The quantity of feed was regulated in a similar way by passing the pulp through a short piece of iron pipe under a given head. In the later runs special efforts also were made to keep the consistency of the pulp uniform by using a separate settling- tank having a spigot-discharge controlled by a plug with an inserted iron tube, while the tank itself was supplied with the same kind of pulp up to the settling-capacity for a clear-water overflow.
In order to get good results, it was found necessary to use a speed of the belt much more rapid than the ordinary adjustments allow. This was accomplished by replacing the cone-pulleys which regulate the belt-speed with larger ones.
The relative saving made on the two machines was determined by weighing, sampling, and assaying the concentrates produced in each run. Hand-samples of feed and tailings also were taken at regular intervals, but only the saving, based on weight and assay of the concentrates, was used for a comparison of the work of the machine under different conditions. In the present case this method of determining the saving is evidently the most reliable one. As a rule, the whole concentrate was dried and sampled so as to avoid errors due to faulty moisture-samples. At the start the concentrates were assayed by the cyanide method, but later these assays were used for preliminary work only, the calculations being based on electrolytic assays.
To eliminate errors due to the impossibility of keeping two machines in equally good condition all the time, the adjustments were reversed when practicable. For instance, when one machine had been run with a 3-in. slope and another with a 4-in. slope for one day, the next day the slopes were reversed, but since this called for frequent changes in both machines, which at times could not be easily effected, another method was generally followed. One machine, kept running in the same way for a whole series of runs, was called the standard vanner, and all the variations were made with the other machine. As an example, the results of one series of tests are given in Table I.
The data in Table I. were obtained under the following conditions: dressing-water used, 2.7 gal. per min. (per 6-in. belt); average quantity of ore treated per 24 hr., 8.95 tons; average amount of solid, 18.58 per cent.; average number of strokes per min., 188 (1-in. strokes); corrugated belt. The results are given in percentages of the results obtained by the standard vanner having a smooth belt, a 5-in. slope between posts (0.680
in. per ft.), using 1.66 gal. of dressing-water per min., and operated at 229 (1-in.) strokes per minute.
Fig. 2, showing the results obtained on a vanner with a smooth belt, expresses the saving in percentages of the maximum saving obtained in this series of tests. The figures represent this saving, the slope and the dressing-water being used as co-ordinates. This diagram shows that, in order to make a good saving, it is necessary to set a vanner much steeper than is done in common practice. The best saving was obtained with 5-in. slope between the inside of the posts (0.680 in. per ft.), and 1 2/3 gal. of dressing-water per 6-in. belt. Under these conditions it was necessary to give the belt a speed of 120 in. per min., which is probably three times the rate of travel used in most mills, and far in excess of any speed that I have ever seen quoted. Both the large quantity of dressing-water and the high slope of the belt tend to produce a high speed. The results of these tests show that, in order to make a good saving on slime-feed with a vanner, it is necessary to give the belt a high speed, which can be done by using either a high slope or a large quantity of dressing-water. On a given feed the best combination can only be decided by experiment.
The details of Fig. 2 are not very complete, but since the determination of even these few figures took a long time, and since it was the expectation to discard the smooth belts should corrugated belts be found more economical, the data collected were considered sufficient.
Richards mentions as extraordinarily high the rate at which the belts move forward in the Gates canvas-plant, operated at Jackson, Cal. At this plant very fine canvas-table concentrates are re-dressed on an end-shake vanner which has the extremely high slope of 1.5 in. per ft. I have tried repeatedly to use slopes approaching this one, but in every case with negative results, which may be due to the fact that the feed was not as fine or that an end-shake vanner will stand a higher slope. The amount of shaking-motion also is much larger in my tests, which may help to explain the difference. The shaking-motion is probably stronger than is practical in view of the difficulty of keeping the machines in good order, but as far as the saving is concerned, not much could be gained by reducing the strength of the motion, as will be seen later in this paper.
The question arises, why, if a high belt-speed gives so much better results, it is not used in some mills? Certainly, some one must have tried high speed before, but I am inclined to think that no one ever investigated thoroughly the question of belt-speed. Most millmen trust a good deal to the eye, and a fast-traveling belt does not show the concentrate very plainly. Every one viewing two belts side by side, one at a fast speed and one at a slow speed, will feel certain that the slow-speed belt produces much more concentrate. The reason for this is, that in the case of the fast belt the concentrate is spread out over a larger surface in so thin a film that sometimes it is hardly perceptible. Other tests in the mills give misleading results. For instance, the belt which shows very little mineral behind the feed-box is frequently considered to make a good saving, but in some of our runs this test failed entirely. Belts showing mineral almost down to the tail-end often made much cleaner tailings and a better saving than did belts which looked clean over the entire length. Panning the tailings is more satisfactory; but the only safe way to determine the saving seems to be by actual assay.
One objection which has been raised against this way of running vanners is, that variation in the power would influence a fast-running belt more than a slow-running one. Whenever the driving-power loses speed a vanner begins to carry sand, into the concentrates, on account of the gentler shaking-motion. And if a vanner be adjusted to the slower motion it will make too clean a concentrate as soon as the power recuperates, which means a loss of mineral, unless the vanner-man immediately re-adjusts the machine to the changed condition.
In other words, the losses will be heavier on a fast-traveling belt, on account of the higher slope. It has been found by experiment, however, that a machine with a high slope requires less regulation to meet changed conditions of power than a machine with low slope, and from this fact I infer that the losses due to lack of attention to the changes in power will be reduced, and not increased, by giving the vanners a high belt-speed. This condition, therefore, recommends a high belt-speed, particularly in places where the power is not very constant.
It may also be mentioned that a violent shaking-motion makes a vanner more independent of changes in the power, so that for plants having poor power it is advisable to use a rapid belt-speed and shaking-motion. While high speed will cause a belt to wear out faster than a slow speed, the results obtained at the concentrator of the Detroit Copper Co. show that the cost of increased wear will be made up many times by the increased saving.
The feed treated on the vanners in the tests shown in Fig. 2 averaged 13 per cent, of solids. Screen-analyses made at different times showed between 6 and 14 per cent, of residue on. a 200-mesh screen of the Fire Clay Co. The average load was 9.5 tons (dry) per 24 hours.
We also investigated the consistency of pulp best suited for
treatment on vanners. The experiments made were similar to those described above, except that the feed was thickened in a settling-tank with clear-water overflow before it reached the distributor. Alternating daily, extra water was applied to one of the two machines, and in this manner the saving determined which corresponded to different percentages of solid matter in the pulp. The curve in Fig. 3 shows the saving obtained under different conditions, and proves that thickening the pulp beyond a certain limit decreases quite rapidly the economy of a vanner. It should be observed that in these experiments the settling of the pulp has been carried much further than would be done in practice. A pulp of this material containing 24 per cent, of solid has almost the consistency of syrup. To convey an idea of the thickness of the feed, the curve, Fig. 4, has been drawn, showing the settling in a cylinder 22.25 in. high. It proves that it takes a long time to settle pulp to this consistency; consequently, if this were carried out in practice it would require a very large settling-capacity.
The adjustments of the vanners in these experiments having been kept the same, the question arises, is it right to assume that the adjustments found the best in the former tests will also be the best for thickened feed ? In other words, may not a very
thick feed require a different adjustment? This question was investigated by the tests represented in Fig. 5, with a pulp averaging 25.5 per cent, of solids. At first, two chances for improvement seemed to exist: one, the use of a higher slope, in order, as far as possible, to spread out the thick pulp and effect a greater contact with the belt; the other, the use of much dressing-water in order to counteract the deficiency of water in the pulp. The outcome of the experiments showed that spreading out the pulp by increasing the slope does not counteract the harmful effects of the deficiency of water in the pulp, but it also showed that an increase of the quantity of dressing-water off-sets the disadvantages of a too-thick pulp.
Since the data for the saving in Fig. 5 are expressed by the saving of another vanner with equally thick pulp, the high saving of 107.4 per cent, means only so much more saving than can be made on a vanner running with 4-in. slope (0.544 in. per ft.) and 2.2 gal. of dressing-water treating feed of the same thickness. However, the results show that an extremely thick
feed can be treated fairly well with a large quantity of dressing-water. The tests, Figs. 4 and 5, are also shown in Fig. 6, together with the results of other test-runs. It seems from Fig. 6 that the best results can be obtained with a slope of 5 in. and a pulp-thickness of about 16 per cent, of solid.
Fig. 6, the saving effected, is represented in its relation to the three variable quantities which determine it—namely, the percentage of solids in the feed, the slope of belt, and the amount of dressing-water. The saving made by each combination tested is expressed by the figure attached to the point representing this combination. The distance of each of these points from the base-plane, indicated by the length of the per-
pendiculars (the dotted lines), expresses the slope; the position of the foot-point of these perpendiculars in the base-plane shows the corresponding figures for the quantity of dressing-water and for the percentage of solid in the feed.
These results, so far as the percentage of water in the feed is concerned, cannot be applied to other ores, since the consistency best suited for treatment on concentrating-machines depends largely on the composition of the ore (the percentage of clay, etc.). I think, however, that a pulp of the same degree of fineness which will settle with the same velocity as the samples treated would give nearly the same results; also, that results for pulps of equal settling-velocity would yield a better comparison than pulps of equal percentage of solids.
Other tests were made to determine the best adjustments for a corrugated belt treating this slime-feed in the same way in which the smooth belt had been tested before. Since these experiments were carried out before the preceding series, no use was made of the fact that the saving could be improved by slightly thickening the pulp. Otherwise, it might have been more logical to conduct these experiments with the corrugated belt with a somewhat thickened feed. The results of these tests are represented in Fig. 7, in which the saving is expressed in percentages of the saving made on the vanner with the smooth belt, which was taken as the standard. The corrugated belt used was an old one, the corrugations of which were much worn and rounded by long use.
From the results given in Fig. 7, it follows that the best slope for this belt is 6 in. between the posts, or 0.816 in. per ft. The belt-speed which had to be used in each run is added in parentheses to the figures representing the saving. The speed necessary for a good saving is not quite as high as that of the smooth belt, probably on account of the lower number of side-strokes used. The figures show also that a far larger amount of dressing-water was necessary than for the tests with the smooth belt.
All the tests had shown that a high belt-speed is most advantageous in saving slime. Experiments were then tried to ascertain the possibility of increasing the belt-speed, and accordingly the saving, without giving the belt, as a whole, too much fall or applying too much dressing-water, simply by raising the front part only of the belt. The higher fall of the front end was gained by raising the front roller about 1 in. and the second roller enough barely to support the belt. The resulting increase in the rate of belt-speed amounted to about 10 in. per min. In every case, however, the effect on the saving was less than 1 per cent. In one case there was a small gain, in two cases a small loss, so that it seems safe to conclude that the effect of this change is very small and hardly larger than the errors connected with these tests.
Tests were made to determine the influence of the shaking-motion on the saving made by a vanner. Some attempts had been made before to gain information on this question. But at that time the power for the experimental machines was quite variable, and the only result obtained was that any considerable reduction in the shaking-motion was practically impossible, because the machines were influenced too much by the changes in the power. Later, better power was secured, and although variations of 2 per cent, to either side in the number of strokes still occurred frequently, it seemed to be improvement enough to consider a reduction in the speed of the shaking-motion. The results, Fig. 8, do not show a great improvement to be
gained by reducing the speed, but indicate that a reduction of the number of side-strokes to about 150, with a considerable increase in the amount of dressing-water in order to gain high belt-speed, would be an improvement. A reduced side-motion requires more dressing-water to produce the same belt-speed.
Very probably such an extensive reduction would prove im-practicable with our power-conditions, as one man has to operate a large number of machines; but doubtless some reduction would be beneficial, especially with our high rate of shaking-motion, which, in spite of continuous attention, shakes the machines loose very soon, and this, of course, means loss.
As already mentioned, Fig. 7 shows the saving made by the corrugated belt in percentages of the saving made by the smooth belt. These runs were originally not intended to determine which belt made the best saving, but only to find the best setting for the corrugated belt, using the smooth belt as a standard in all these tests. The saving made on the corrugated belt was, however, in all these tests so much higher that it seemed safe to conclude that the corrugated belt was better than the smooth belt for the treatment of slime-feed. This result was doubted by many experienced in the concentration of copper-ores, and a second contest was arranged in which I operated the corrugated belt against several experienced concentrating-men using a smooth belt. The smooth belt was nearly new, having served in the concentrator for some months: The corrugated belt was the one used in the former tests, and before this had been in constant use for a long time in another mill, so that it was not in first-class condition. In some places the riffles had been worn away almost completely, while in others they still stood out prominently. Besides, there were numerous bad places, due to rough handling in shipping and repeated putting on and taking off the belt. At the bottom of the riffles the canvas was exposed.
In the first test of the new series the slope of the smooth belt was the same as before, 2 in. (0.272 in. per ft.). The results obtained were:
In the following tests no limitations were set to the adjustments; 12 days were devoted to these tests, including work with the table mentioned before, which received feed from the same feed-distributor. The average results were :
Lower Vanner Feed
8.81 per cent, on 200-mesh screen; 11.91 per cent, of solid matter; 1.49 per cent, copper ; 8.99 tons (dry) per 24 hr. ; running-time, 83 hr. 30 min.
For a further comparison between the work of the corrugated and the smooth belt, a test was made using as feed the tailings from the slime-vanners (smooth belts) in the concentrator. The results of this test were:
Tailings from lower vanners, running with smooth belts, about 3.5 in. slope between posts (0.476 in. per ft.); 9 per cent. on 200-mesh screen ; 10.73 per cent, of solids ; 0.77 per cent, of copper; 6.90 tons per 24 hr. ; running-time, 10 hr. 30 min.
This result confirmed the experience gained in the first tests, that the saving effected by the corrugated belt on these slime-tailings far exceeds the saving made by the smooth belt.
The tests with the corrugated belt had been made using the old belt, the corrugations of which were greatly worn down. Since the results were so very encouraging, a new belt of the same pattern and having sharp corrugations was secured and tested. The saving effected was extremely disappointing. It was not possible to get even as good results as with a smooth belt. Later, a large number of belts were made with exactly the same shape of riffles as had been formed by the wear.
With one of these belts tests were run against both the smooth and the old corrugated belt, which showed that the new belt, after it had been on the machines for a couple of weeks, was just as good a saver of mineral as the old one, and was considerably superior to the smooth belt, One difference existed— namely, that the old belt, probably on account of its roughness and of the exposure of the canvas at the bottom of the riffles, carried some very fine slimes into the concentrate, which, however, was of rather low grade, and did not influence the saving very much.
For a test on a larger scale, 10 machines, equipped with the new corrugated belts, were run against 10 machines with smooth belts. The concentrate from each group of machines was caught in a wooden tank large enough to hold all the concentrate produced in the course of a week. Five tests were made, the first one lasting seven days, the others five days each. The results of the first test (which favored the corrugated belt) were not accepted, since there was some doubt of the correctness of the work. In the fourth and fifth tests, the feed-pipes which had been supplying the feed for the smooth belts in the first and second tests supplied the corrugated belts, and vice versa, in order to eliminate possible inaccuracies of the distributor. The smooth belts used for the tests had been running in the concentrator for some time. The rubber was worn off from the back surface of some of the belts and the canvas exposed. To prevent the removal of mineral from the vanner-box on this rough surface, spray-water was used to keep the surface clean.
The average result of these tests, occupying 20 days altogether, was that the corrugated belts produced 123.2 per cent, of the copper produced on the smooth belts. The grade of concentrate on the corrugated belts was 20.04 per cent, of copper, as compared with 19.39 per cent, on the smooth belts.
The corrugated belts were set with 4.92 in. slope (0.669 in. per ft.) and the smooth belts with 3.56 in. (0.484 in. per ft.), which is a little less than the slopes found best in the experiments. But the ordinary load in the mill is smaller than the load used on the experimental machines, so that a gentler slope may be justified. The results obtained are decisive enough to permit the statement that the corrugated belt of the form described above has proved a better slime-saver than a smooth belt.
It is often pointed out as an objection to a corrugated belt that it will make a dirtier concentrate, although it may make a better saving. Expressed so broadly, this statement is certainly incorrect. Since sand cannot be noticed as easily as on a smooth belt, it requires practice to produce a uniformly clean concentrate on a corrugated belt. But there is not the least doubt that, if the concentrate made on a given machine is not clean enough, it can be raised to any degree of purity by the ordinary adjustments of vanners. My tests show that the new corrugated belt produces a larger amount of concentrate of the same grade than does a smooth belt.
Calculations based on the result of the test determining the saving that could be made by re-treating the tailings from the slime-vanners on corrugated belts had shown that it would hardly pay to install additional machines for this purpose with copper at a price of 13 cents per pound. Replacing the smooth belts in the concentrator by corrugated belts will improve the saving of the vanners and make the re-treatment of tailings from the slime-vanners decidedly uneconomical.
Possibly it may be profitable to classify the tails thoroughly before attempting re-treatment, but since these slimes contain only a small percentage of material that will stay on a 200-mesh screen, it is not probable that this suggestion will lead to any improvement. Besides, if classification yields a better saving, it would be better to provide a thorough classification for the vanner-feed.
Another way of raising the saving of the slime-vanners is to lower the tonnage treated per machine, and with this end in view experiments were undertaken to establish the relation between the saving made and the load carried on these vanners. The feed-distributor was provided for these tests with compartments of unequal size, so that more feed could be sent to one vanner than to the other one. The proportion in which the feed was distributed was carefully determined. The results of these tests are represented graphically in Fig. 10, which shows that within the limits tested the vanner carrying the lighter load makes the better saving. The improvement resulting from reducing the load is not very great. For the present grade of milling ore, with copper at 12.5 cents, and with the present cost
of labor, power, repairs, etc., the most economical load for the new corrugated belts is between 8 and 9 tons, which shows that under existing conditions a reduction of the present load is not advisable. For higher copper-prices, however, a smaller load would be more economical. At 20 cents the greatest economy is obtained with a load of about 7 tons.
The slope which is to be given to corrugated belts depends very largely on the kind of material treated. Formerly it was the rule at the Detroit concentrator, and I suppose many others, to treat the finest feed with the lowest, and the coarsest feed with the highest, slope. That the contrary is rational has been
held by Richards and others. The experiments, graphically represented by Fig. 9, show that on a coarse feed the higher slope gives poorer savings than a lower slope. The fact that a feed not very different requires such a different treatment, seems to point to close classification as an improvement for vanner-work, and to proper adjustments of each machine to the pulp treated.
This question is still undecided, but I hope that some light has been thrown on a few points by the work described in this paper. If nothing else, it shows that it pays to study questions of this character.
Since writing this paper some additional tests have been made, in which the corrugated belts showed no marked superiority over smooth belts. These tests were made under mill conditions, 10 corrugated-belt machines running against 10 others with selected smooth belts, both sets of machines operated with high belt-speed. The feed was somewhat coarser than in the tests referred to in the paper. Although, therefore, the results are not exactly comparable, they could be interpreted as throwing some doubt on the correctness of the previous tests investigating this point. For this reason I have intended for a long time to repeat these tests. But as some changes in the operation of the mill have made it impossible so far to obtain the same kind of feed as used in the former tests, and as there may not be an opportunity of carrying out this plan for some time, I thought it better not to delay the publication any longer. I felt, however, that I should call attention to this apparent discrepancy.