Table of Contents
The following may be said to be essential characteristics of a furnace for determining the melting point of refractories: It should be capable of easily reaching a temperature of 1800° C., since most refractories melt below 1800° C.; for those materials melting over 1800° C., special procedure and technique are usually required. The atmosphere in the furnace should not react chemically with the specimen to any appreciable extent. Facilities should be provided for making temperature measurements with, an optical pyrometer. Good control of the rate of heating should be possible. The type of furnace chosen depends, to some extent, on the original cost, the cost of operation, and the number of melting-point tests to be made.
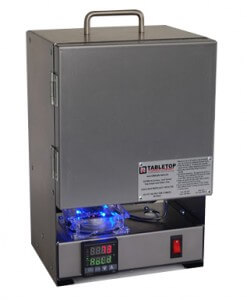
The two general types of furnaces in use are the electric-resistance furnaces and the fuel-fired furnaces. They may be classified as follows:
Electric Furnaces
Some form of carbon as resistor; such as graphite tube in air, crushed carbon or Kryptol, carbon plate resistor, graphite resistance vacuum furnace. Metal as resistor; such as iridium tube or wire and tungsten or molybdenum wire or tube.
Fuel-fired Furnaces
Coal, coke, or oil, and gas-air or gas-air- oxygen.
Graphite or carbon-tube furnaces, with or without water-cooled electrodes, have been constructed in many forms. When operated under atmospheric pressure, the tubes do not last long on account of oxidation; they are somewhat protected from oxidation by passing a neutral or reducing gas through or around them. This gas may serve to carry away smoke so that optical temperature measurements may be made. With the graphite resistor, the atmosphere in the furnace is strongly reducing; many refractories are greatly attacked in a carbon and carbon-monoxide reducing atmosphere.
By simple inspection of the melted sample, it is usually not possible to tell whether the reduction has reached appreciable proportions, thereby introducing great uncertainty into the melting-point determination. In many instances, the surface of the sample is attacked and a shell of higher melting point than the inner portion is formed. Thus, while the inner material may have been melted, no outward evidence of this fact is shown. Whenever possible, it is much safer and more desirable to protect the sample from the strongly reducing atmosphere (provided this type of atmosphere does not exist in actual (use of the material) with a refractory tube of low porosity; and a slight current of air through this tube will serve to oxidize the reducing gases and drive off smoke. Porcelain tubes of Marquardt, or those approximating the composition of sillimanite Al2O3.SiO2 (melting point, 1810° C.) may be used for this purpose up to temperatures as high as 1800° C., although they become soft and do not last long at this temperature. Well-sintered tubes or crucibles of alumina or magnesia of mixtures of the two may be used if they are thick enough. Unfortunately protection tubes for use at higher temperatures are not readily obtainable, although they undoubtedly could be made.
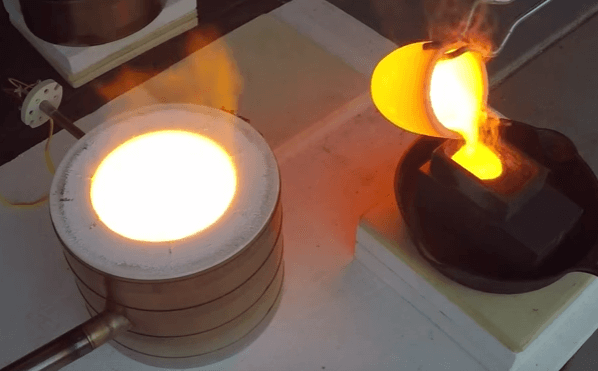
Crushed-carbon, graphite, or kryptol, and carbon-plate resistor furnaces, in addition to the above difficulties, do not allow very accurate regulation. Also, some forms make it difficult to take optical temperature measurements. While a graphite-resistance vacuum furnace presents the difficulties of greater initial cost, of producing a vacuum, and of opening and closing large vacuum-tight joints, the atmosphere is kept free from smoke and good temperature uniformity can be maintained, thus facilitating optical temperature measurements. Higher temperatures can be more conveniently reached in the vacuum furnace.
In order that the carbon atmosphere in the vacuum furnace may have no appreciable chemical effect on the specimen, it is usually necessary to keep the pressure below 1 or 2 mm. Even then it is safer to protect the sample with a refractory porcelain tube closed at one end and suspended from the cool part of the furnace. This prevents the carbon vapor or particles shooting off from the resistor from gaining access to the specimen. Practically all the gases in the tube must come from the cool part of the furnace; and these gases consist of nitrogen and carbon monoxide in low concentration. It is also possible that the tube largely diminishes the convention of the reducing gases past the specimen and consequently the reducing action is not so great as without the tube. To prevent the sample or its container from sticking to the tube, they may be separated by a layer of powdered alundum.
For a laboratory in which a large number of melting-point determinations are made, a graphite-resistance vacuum furnace of the Arsem type is the most desirable electric furnace; the lasting operation of the resistor, the clarity of the atmosphere, the rapidity of action and excellence of control and the good black-body conditions afford, with suitable protection for the sample, the most convenient and precise method of melting refractory materials in an electric furnace, see Fig. 1.
Several furnaces with metals as the resistor and capable of attaining temperatures of 1800° C. or higher have been constructed. Iridium in the form of tubes or wire has been used by a number of investigators; but this metal is so expensive and volatilizes so readily that it is ordinarily outside the range of metals accessible for a practical furnace. Tungsten
and molybdenum have been used considerably in the form of wire wound on refractory tubes. For lasting operation, it is requisite that the wire be protected from oxidation by surrounding it with a reducing atmosphere, preferably with hydrogen. Obstacles in the way of general adoption of these furnaces are the danger of hydrogen explosions and the difficulty of obtaining hydrogen in sufficient quantity. Even in the reducing atmospheres, the resistors do not have a long life as they become brittle.
Furnaces with tubes of tungsten, molybdenum, or similar high melting point metals are still in the experimental stage. They should be run in a vacuum or hydrogen and, apart from the absence of a carbon or carbon monoxide reducing atmosphere, they are not so advantageous as graphite resistance vacuum furnaces. Coal, coke, or oil-fired furnaces have been used for melting refractories, but they are unsuitable for laboratory furnaces in which small masses are placed and for which accurate control is an essential. They are too large and are inconvenient on account of dirt, smoke, and possibly a strongly reducing atmosphere; besides it is not easy to obtain the requisite high temperature.
Gas furnaces offer, besides the electric furnace, the only other practical means of attaining high temperatures. In the case of furnaces using illuminating gas made from coal and air at 2 or 3 lb. (0.9 or 1.4 kg.) pressure, the maximum temperature reached in an ordinary furnace is about 1400° C.; when burning natural gas, temperatures 100° or 200° higher may be attained. With air pressures at 10 lb. (4.5 kg.) and over and illuminating gas, it is possible to obtain temperatures as high as 1650° C.; and in the case of natural gas, as high as 1800° C. By recuperating the waste heat or by preheating the gases, these temperatures could be raised considerably; also, by the addition of oxygen, temperatures over 2000° C. have been maintained. These statements are very general and may not hold in the case of a number of furnaces; they are not intended as a complete statement of the problem of attaining high temperatures in gas furnaces.
It is quite a different matter to obtain a temperature, say, of 1750° C. uniformly over a space of several cubic inches than it is to reach this temperature in a small spot. For melting refractories one should be able to obtain a uniform, high temperature over a sufficient volume to procure reliable results. In order to do this, it is usually necessary to enclose the specimen in a refractory crucible or muffle. At present, one of the difficulties is that of refractories for the lining and crucibles to contain the specimen—a problem that is, perhaps, more difficult of solution for gas furnaces than for electric furnaces.
The Bureau of Standards has been working on the problem of designing a gas furnace suitable for the determination of the melting point of refractories but has not yet perfected it. Gas furnaces can be made in convenient laboratory form and, on account of their simplicity, low initial cost and cost of operation, and the comparative ease with which high temperatures are obtained, probably will offer, after considerable development, the best solution of the problem.
The question of the atmosphere in the furnace is intimately bound up with the type of furnace used. Probably most refractories used in industry are heated in a reducing atmosphere. But it is not possible to reproduce exactly these conditions in the laboratory. Carbon-resistance furnaces are very liable to have a strongly reducing atmosphere; means for avoiding tins have been described before. Gas furnaces, on the other hand, which are intended for use at the higher temperatures usually have oxidizing atmospheres. Since a refractory would ordinarily have its lowest melting point in a slightly reducing atmosphere, such a one may be preferable. At the present stage of development of furnaces, however, the question of the best type of atmosphere must be left unsettled.
Temperature Measurements and Observation of Melting
For a very rough measurement of the melting temperature of a refractory, the temperature as indicated by the melting of a material the melting point of which is known—by a pyrometric cone—has often been taken. The refractory is then said to have a softening temperature corresponding to a certain cone number. The reason given in justification of this process is that cones are used in furnaces, or kilns, in which ceramic products are fired to measure temperatures, or at least heat effects. But the cones are used in the ceramic industry under quite different conditions than when softening points are determined. In the first place, the rate of heating of the cone is much slower in a kiln than in a laboratory furnace. Second, the cone is heated in the kiln over a short range of temperature. The cone serves in such a case as a sort of integrator of the time versus temperature curve of heating. When a small range of cones are heated under the same circumstances the practical ceramist can draw conclusions from the deformation of those cones, which serve to indicate the proper degree of firing of his products.
But in the laboratory, where a rather large range of cones is used and where the rate of heating is comparatively rapid and may vary from time to time, the determination of the cone softening point is not of much significance and serves no useful purpose in practice. What should be done is to determine the point at which the refractory softens on a uniform and reproducible temperature scale under properly specified conditions. This, we believe reduces the number of variables in the determination to a minimum and affords more reliable results.
It has repeatedly been shown and emphasized that the softening point of Seger cones depends on a number of factors and conditions similar to those affecting the melting of other refractories. That is to say, the softening point depends, to some extent, on the nature of the atmosphere but, most important of all, on the time and rate of heating. Usually the more rapid the heating, the higher is the softening temperature; 50° to 75° C. difference in softening temperature easily results from varying the rate of heating. Cones do not even measure heat effects with any semblance of precision when employed under different conditions; it is possible to subject a cone to different conditions of heating and still produce the same amount of deformation. As far as an approximate measure of a reproducible temperature or heat effect is concerned, the indication of a Seger cone is unreliable even for commercial precision, unless the nature of the atmosphere in which the cone is heated and the temperature versus time curve of heating are specified. Even though these conditions are specified, there is no way of accurately deducing a common basis of comparison of temperature or heat effect when the cones are used under different conditions.
To measure the temperature of melting with sufficient accuracy, it is necessary to use some form of optical or radiation pyrometer. With relatively slow heating, it is possible to use a Wanner or a Fery optical pyrometer by alternately watching the specimen melt and sighting through the pyrometer to measure the temperature. A more rapid and precise instrument, however, and one which permits the observation of the specimen simultaneously with the measurement of its temperature, is the Holborn-kurlbaum type of Morse optical pyrometer. In determining the temperature with any form of optical pyrometer, it is essential that sufficiently good black-body conditions exist in the furnace as it is impossible to apply any reliable emissivity correction. With electric furnaces and with gas furnaces containing muffles or crucibles in which the specimen is heated, it is not difficult to obtain good black-body conditions; even a slight departure from a perfect black body will, enable one to discern the specimen. To see the specimen with sufficient clarity, it is usually necessary to keep the eye constantly fixed on it and its surroundings.
In sighting on a melting specimen, it is sometimes important to sight on a surface that is rather oblique to the line of vision, for the surfaces that are more or less perpendicular to the line of vision may appear darkened in the field because they do not reflect any light from the surroundings into the pyrometer and because their emissivity is low. In this connection, one should guard against the condition of sighting on a surface reflecting light from a hotter spot for in such a case the measured temperature would be higher than the true temperature. The atmosphere between the pyrometer and the sample must be perfectly clear, that is, free from smoke or flames, because the latter act as an absorption screen, causing errors of an uncertain magnitude.
As a rule the flow of the sample can be observed a great deal more distinctly when sighted on sidewise rather than from above; that is, in the former case the change in linear dimensions and in position appears greater to the eye. In the Arsem vacuum furnace the sample is viewed from above, consequently the point at which a marked flow of the sample begins is rather difficult to observe, being subject to the personal equation of the observer. We see, then, that to measure the temperature of melting of a refractory material it is advisable to use a Holborn-Kurlbaum type of the Morse optical pyrometer; to be sure that sufficiently good black-body conditions are maintained; to sight on the proper part of the specimen; and finally, to be sure that the absorption of the atmosphere is negligible.