Table of Contents
The subject of stoping has been discussed at considerable length by Jackson and Gardner in a Bureau of Mines bulletin. Data in this bulletin were compiled principally from those presented in reports, dealing with methods and costs at about 75 individual mines, previously published in information circulars. The principal mining methods have been summarized in a series of information circulars as follows:
Inf. Circ. 6193.—Mining Ore in Open Stopes, Central and Eastern United States, by Chas. F. Jackson. 1929. 36 pp.
Inf. Circ. 6293.-—Shrinkage Stoping, by Chas. F. Jackson. 1930. 54 pp.
Inf. Circ. 6350.—Undercut Block-Caving Method of Mining in Western Copper Mines, by E. D. Gardner. 1930. 44 pp.
Inf. Circ. 6410.—Mining by the Top-Slicing Method with Some Notes on Sublevel Caving, by Chas. F. Jackson. 1931. 51 pp.
Inf. Circ. 6688.—Cut-and-Fill Stoping, by C. H. Johnson and E. D. Gardner. 1933. 58 pp.
Inf. Circ. 6691.—Square-Set System of Mining, by E. D. Gardner and William O. Vanderburg. 1933. 73 pp.
The following discussions of stoping have been condensed from the earlier bulletin, whereas the earlier cost data have been amplified by data from subsequent reports.
In this bulletin, the term “stoping” is employed in its broader sense to mean the operation of excavating ore by means of a series of horizontal, vertical, or inclined workings in veins or large, irregular bodies of ore or by rooms in flat deposits. It covers the breaking of ore and its removal from underground workings, except those driven for exploration and development, and the timbering or filling of the stopes for the purpose of support.
Ore deposits vary greatly in their physical characteristics and with respect to the economic problems involved in their exploitation. Various methods of stoping have been devised for extracting the ore safely and economically from deposits of different types, and a nomenclature has been developed for use in referring to the various methods. Some of the terms are descriptive and require no interpretation, whereas others, particularly those applied to variations of the principal methods, are not. Among the variations are those bearing the names of mines at which they were devised or the names of the originators.
Basically, the stoping method or methods that can be applied to a given ore body depend on the requirements for support of the stope—the maximum area or span of back and walls that will be self-supporting during the removal of the ore; the nature, size, and interval between supports required to maintain the backs and the walls of the excavations; and the requirements for permanently supporting the overlying and surrounding country rocks and overburden to prevent their movement and subsidence. Variations of the principal methods of stoping may be based upon the direction or angle of working, sequence of operations, or methods of handling the broken ore.
Stoping Methods
A classification of stoping methods based upon method of support was adopted by the Mining Division of the Bureau of Mines in 1928. This classification has been used ever since as a basis for describing methods in its publications dealing with mining methods and costs and is as follows:
Classification of stoping methods
A. Stopes naturally supported.
1. Open stoping.
(a) Open stopes in small ore bodies.
(b) Sublevel stoping.
2. Open stopes with pillar supports.
(a) Casual pillars.
(b) Room (or stope) and pillar (regular arrangement).
B. Stopes artificially supported.
3. Shrinkage stoping.
(а) With pillars.
(b) Without pillars.
(c) With subsequent waste filling.
4. Cut-and-fill stoping.
5. Stulled stopes in narrow veins.
6. Square-set stoping.
C. Caved stopes.
7. Caving (ore broken by induced caving).
(a) Block caving; including caving to main levels and caving to chutes or branched raises.
(b) Sublevel caving.
8. Top slicing (mining under a mat that, together with caved capping, follows the mining downward in successive stages).
D. Combinations of supported and caved stopes. (As shrinkage stoping with pillar caving, cut-and-fill stoping with top slicing of pillars, etc.)
Forced caving (a method employed at several very large mines and therefore important) has heretofore been classed by the Bureau as a variation of shrinkage stoping. In reality it is intermediate between shrinkage (supported) stopes and caved stopes, as far as support is concerned. The ore is broken by large blasts, and considerable caving often follows the blasts, yet the operation is fundamentally quite different from natural caving induced by undercutting, as in block-caving or sublevel-caving systems.
Stopes Naturally Supported Open Stopes
Stopes naturally supported are those in which no regular artificial method of support is employed, although occasional props, cribs, or stulls may be used to hold local patches of insecure ground. The walls and roof are self-supporting. The simplest form of open stope is that in which the entire ore body is removed from wall to wall without leaving any pillars (fig. 85). It is applicable to relatively small ore bodies, as there is a limit to the length of unsupported span that will stand without support even in the firmest and strongest rocks. In sublevel stoping the ore is excavated in open stopes, retreating from one end of the stope toward an entrance at the other end (fig. 86) on each of a series of sublevels that are usually 20 to 25 feet apart vertically but may be 40 feet or more apart.
In open stopes with pillar support, the length of unsupported span is reduced by leaving pillars of ore. These pillars may be of the irregular or “casual” type, their position and size being determined by localized ground conditions (fig. 87, A), or may be regular in size and arrangement, conforming to a predetermined pattern (fig. 87, B).
Open stoping is applicable to deposits of strong, firm ore having strong, firm walls. In the narrower deposits (30 to 50 feet wide) the ore often can be mined the full width in one operation without the use of pillars. In wide deposits it usually becomes necessary to leave solid pillars to reduce the length of unsupported span and thus prevent the failure of back or walls. When “casual” pillars are used, it frequently is possible to leave low-grade ore within the ore body as pillars, at least in part, and thus make possible more complete recovery of the higher-grade ore. In general, casual pillars are used in the firmest type of ground and in deposits of variable thickness where their size and spacing can be proportioned to suit the conditions of the back and the height of the ore. Often a somewhat higher percentage of
the ore is recovered than where a regular room-and-pillar system is employed.
A regular room-and-pillar pattern is applied chiefly to relatively thin, regular, flat-lying beds, where the roof must be definitely and permanently supported, in other words, where it is not safe to rely on personal judgment of the foreman or boss as to the amount of pillar support required at individual local points.
In the sublevel variation of open stoping, the stope faces retreat from the end of the ore body or stope limit longitudinally or (where the stopes are run across the lode) from one of its walls. The miners are always working under solid backs and have a safe avenue of retreat through the subdrifts to the manway raises. Slabbing of roof or walls at the worked-out end of the stope does not endanger the miners and, if the stope is worked back rapidly, usually will not cause serious dilution of the broken ore with waste. This system is applicable to
wide, thick, irregular masses of ore that stand well without artificial support and that have firm walls and to thick, tabular ore deposits that dip 50° or more (and, by using scrapers for removing broken ore, to flatter deposits). It may be used successfully in weaker ground than could be worked safely by other open-stope systems, as the miners are always protected by solid ground overhead. Large open stopes are mined by this method where the ore is so soft that it can be drilled with auger steel, and the method can be applied where the ore is too weak to be safely minable by shrinkage stoping.
Stopes Artificially Supported
Shrinkage Stoping
In shrinkage stoping the ore is mined in successive flat or inclined slices, working upward from the level or the bottom of the block of ore. After each slice or cut, enough broken ore is drawn off from below to provide a working space between the top of the pile of broken ore and the back of the stope (fig. 88). Usually about 35 to 40 percent of the ore will be drawn off during active mining in the stope. The remaining ore serves as a floor upon which to work in drilling the back for the succeeding cuts and also provides some support of a temporary nature to the stope walls. For this reason shrinkage stopes are considered to be a form of artificially supported stope, although undoubtedly there are good reasons why some consider them to be open stopes.
In narrow veins or lodes and those of moderate width, the stopes usually are run longitudinally and are mined from wall to wall without leaving pillars, except locally, to support bad ground or where the ore is too low-grade to be mined profitably. In wide ore, to reduce the unsupported span of the stope back, it may be necessary to mine the ore in a series of transverse stopes between intervening pillars of ore. The stopes then end against the walls of the vein and the sides are vertical pillars of ore.
After active mining has been completed to the level above or to the floor pillar, the rest of the broken ore is drawn off from below, leaving the stope empty. It may be filled with waste later to prevent general movement and subsidence or to permit mining of pillars left between stopes during the first mining.
Stulls may be employed during active mining to support local patches of insecure ground. Where the width is not too great, they often are employed when the stope is being emptied to protect the miners from falls of loose ground while cleaning down broken ore that has hung on the footwall and recovering ore that was left in the walls during stoping. Stulls 30 to 40 feet long have been used for this purpose, but the safety and adequacy of this type of support are questionable for widths as great as this. While stuffing from the top down during drawing of the stope, the miners stand on the top of broken ore while placing the timbers to support patches of insecure wall rock. After the ground has been secured thus, drawing and cleaning down are resumed.
Shrinkage stoping is applicable to bodies of strong, firm ore enclosed between firm walls that will not slab or slough off to any great extent after standing for a considerable time. The method is applied most frequently to relatively thin, tabular deposits dipping at angles greater than 50°, in which few waste inclusions occur and which have fairly regular walls. By carrying transverse stopes separated by pillars, it may also be applied to wide, tabular deposits as indicated above.
The “forced-caving system” may be considered a variation of this method and is employed for the non-selective mining of large, thick masses of ore at the Alaska-Juneau, Beatson, Climax Molybdenum, Britannia, and other mines. Figure 89 depicts the mining cycle used at Alaska-Juneau and figure 90 that at Beatson. In both cases the ore is broken down by large blasts into stopes that are kept partly full of broken ore (as in shrinkage stoping). The large blasts break ore directly into the stopes and have the further effect of shattering additional ore, part of which then caves. At both mines the miners
come down through raises from the level above. At Juneau, small powder drifts (sometimes termed “coyote” drifts) are driven from the raises. Charges averaging 4,000 pounds of 40-percent dynamite are placed in the powder drifts segregated in two piles 35 or 40 feet apart. Three to five such piles make up the usual blast. At Beatson, however, a similar result is accomplished by drilling, from enlarge-
ments in the raises, a large number of long holes, which are loaded and fired in one blast.
For the successful use of the ordinary shrinkage-stoping method the ore must be strong and stand well, as the back of the stope under which the men must work is unsupported except for occasional props or stulls that may be set to hold local patches of loose ground. Although the broken ore left in the stope affords support to the walls until drawing begins, unless the walls are firm they may slough or even collapse during and after drawing and cause serious dilution of the ore.
Cut & Fill Stoping
In cut-and-fill stoping the ore is excavated by successive flat or
inclined cuts or slices, working upward from the level as in shrinkage stoping; but after each cut, all the broken-ore is removed and waste rock, sand, or other filling material is run in and the excavation filled to within a few feet of the back, thus providing permanent support to the walls (fig. 91) and a working floor for the next cut. The term “cut-and-fill” implies a definite and characteristic sequence of operations:
- Breaking a slice of ore from the stope back,
- removing the broken ore,
- introducing filling; then (1) breaking again, and so on.
The filling is employed primarily to support the walls of the stope and may consist of waste sorted from the ore in the stope, waste blasted from the walls of the lode adjacent to the stope, waste rock from development work or special waste stopes, rock from surface quarries or glory holes, sand and gravel, mill tailings, or slag. Stulls, props, and cribs may be erected on top of the fill to support local patches of loose or insecure ground.
https://www.youtube.com/watch?v=XhI0IPZmniY
Cut-and-fill stoping is applicable to the mining of firm ore enclosed within walls, one or both of which are weak and heavy. The deposits may be tabular in form, dipping at angles steeper than the angle of repose of the broken ore (or flatter, if scrapers are employed for moving the ore in the ore passes), or to wide, thick ore bodies or masses. Generally speaking, it is suitable for mining deposits too irregular for shrinkage stoping and deposits in which shrinkage could be employed were it not for the fact that the walls are too weak.
The method is also used for mining high-grade veins that are less than minimum practicable stoping width and therefore require the breaking of wall rock to provide working room. When the ore and walls are broken separately, the method is termed “resuing” or “stripping.” In resuing, one wall may be drilled and shot down first and the rock left in the stope for fill, after which the vein is “stripped” from the side of the resulting excavation; or the vein may be shot down first, the broken ore removed, and the wall then stripped to provide working room and filling for the stope.
Since the filling material does not directly support the stope back, but only the walls, the ore itself must stand well for a short time, at least so as to apply this method without the use of timber for auxiliary support. In veins of moderate width a stringer-set cut-and-fill variation (fig. 92) of the general method is employed sometimes where the walls are heavy; the ore itself is fairly strong, but the ground is not so heavy as to require the use of square-set-and-fill stoping.
In fairly wide ore the back may tend to slab off, and temporary stringers supported by posts resting on the fill may be employed to afford back and wall support above the filling (fig. 93).
If both the walls and the ore itself are heavy and weak, square-set stoping or a caved-stope method would be indicated rather than cut-and-fill stoping.
Stulled Stopes in Narrow Veins
Casual stubs may be used locally in open stopes or in other forms of supported stopes, as already indicated, and in such instances are only incidental to the mining method. In some narrow or moderately wide lodes, however, a regular arrangement of stub timbers is employed to support the immediate hanging wall and constitutes a rather distinct method of mining. It is especially applicable where the ore is separated from the solid or true wall (or walls) by one to a few feet of barren rock that loosens and slabs off after being exposed for a short time unless held in place by stulls—in other words, where only nominal rather than great weight develops. Where a weak hanging wall extends back a considerable distance from the vein, the weight usually will be too great to be held in this manner and cut-and-fill or square-set stoping must be employed. Figure 94 shows a stull-supported stope.
Square-Set Stoping
In square-set stopes the walls and back of the excavation are supported by regular framed timbers forming a skeleton enclosing a series of contiguous, hollow, rectangular prisms in the space previously occupied by the ore and providing continuous lines of support in three directions at right angles to each other (fig. 95).
The ore is excavated in small rectangular blocks just large enough to provide room for standing a set of timber. The essential timbers comprising a standard square set are termed, respectively, “posts,” “caps,” and “girts” (or “ties”). The posts are the upright members and caps and girts are horizontal members. The ends of each member are framed to give each a bearing against the other two members at the corners where they meet.
Ordinarily the stopes are mined in floors or horizontal panels, one above the other, and the sets of each floor are framed into the sets of the preceding floor (fig. 95, at B). Sometimes, however, the sets are mined in a series of vertical or inclined panels. Square-set stoping usually is accompanied by filling, and often in heavy ground the sets are filled with waste promptly after they are installed, leaving only a small volume of unfilled stope at any time. It has come to be accepted quite generally that unless the ground is heavy enough to require filling for permanent support, the expense of square-setting is not warranted and some other method should be employed.
Square-setting is adapted to mining regular or irregular ore bodies, commonly on dips steeper than about 45°, where the ore and/or walls are too weak to stand even over short spans for more than a brief time, and where caving and subsidence of overlying rocks must be prevented. From the viewpoint of support alone, both temporary and permanent, the method is applicable to conditions no other method has yet been devised to meet. Where the overlying strata may be allowed to cave, and where the loss of some ore or some dilution with waste would not be a serious drawback, caved-stope methods are adaptable to as bad or worse ground conditions and cost less.
Square-set stoping often is used in combination with other methods for extracting pillars between or over filled stopes. It is also employed as an auxiliary method, as for supporting the sill and first floors of some cut-and-fill or shrinkage stopes.
The stopes usually are worked upward from the level either in horizontal or inclined floors or in successive vertical panels, one along-side the other, but in some instances, especially in loose, running ground, may be worked from the top downward (underhand square-setting, fig. 96).
Caved Stopes Mining Method
When caved stope methods are employed, breaks to and subsidence of the surface will occur ultimately if caving is continued over an area wide and thick enough in relation to the depth of cover. Hence, caved-stope methods are applicable only where there is no objection to caving the overlying strata or to surface subsidence.
Caved stopes are of two distinct types: In the first, the ore is broken by caving induced by undercutting a block of the ore and isolating it from or weakening its connection to the surrounding ore or walls; in the second, the ore itself is broken by conventional drilling and blasting methods in a series of horizontal or inclined slices, and the capping is allowed to cave into and fill the space occupied previously by the ore. The first type embraces the caving methods of mining, whereas the second comprises the top-slicing method.
Mining by Block Caving Mining
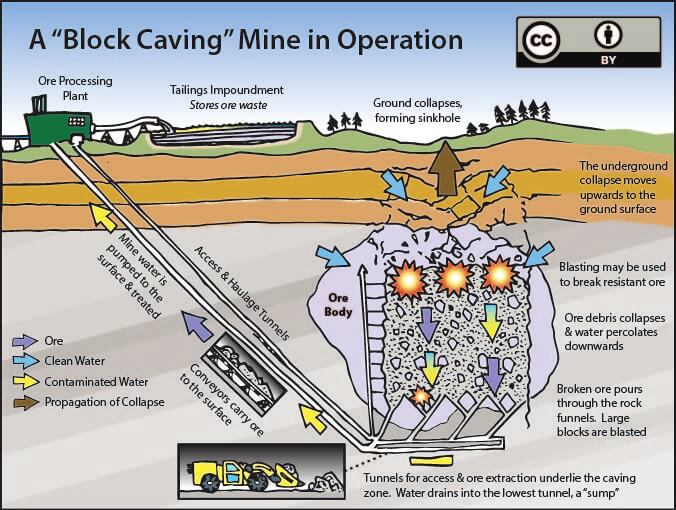
In block caving (fig. 97) a thick block of ore is partly cut off from surrounding blocks or the walls of the ore body by a series of drifts, one above the other, or by boundary shrinkage stopes; it is then undercut by removing a slice of ore or a series of slices separated by small pillars underneath the block. The isolated, unsupported block of ore breaks and caves under its own weight. The ore so broken is drawn off from below; and, as the caved mass moves downward owing to continued drawing from below, it is broken further by pressure and attrition. The capping finally caves also and follows the column of broken ore downward.
In the earliest applications of this method the block was undercut on or immediately above the haulage level, and the caved ore was shoveled into cars in drifts driven under or spiled through the cave. This system entailed the driving and maintenance of a large number of drifts to recover the ore and has been superseded by caving to a system of chutes or branched raises extending from haulage drifts at some distance below the bottom of the undercut and with an intermediate grizzly level on which chunks of ore too large to pass through the grizzlies are broken by sledging and bulldozing. With this system, hand shoveling is virtually eliminated.
Natural forces are utilized to the highest degree possible for breaking the ore, transferring the broken ore to the haulage levels, and filling the mined-out areas.
The method is a nonselective one, and lean sections of the ore body and even barren horses of waste are broken up and drawn with the ore. It is applicable to the wholesale mining of masses of ore large in three dimensions that will cave readily when support is removed by under-cutting, and which, after caving, will break up fine enough to pass through the extraction raises as the caved mass is drawn downward. This condition occurs when the ore is friable enough to break up readily or the ore body is traversed by a multiplicity of closely spaced seams, fracture and joint planes, or invisible planes of weakness that strike and dip in various directions.
Block caving is employed principally for mining low-grade ores where the inevitable loss of some ore and some dilution with capping and wall rock are permissible and where mining must be done on a large scale and at a lower cost than can be obtained by the use of supported-stope or other selective mining methods.
https://www.youtube.com/watch?v=MVDAw56s5dU
Mining by Sublevel Caving
In sublevel caving, relatively thin blocks of ore are caused to cave by successively undermining small panels. The ore body is developed by a series of sublevels usually spaced at vertical intervals of 18 to 25 or 30 feet (more recently, intervals of 50 feet or more have been
used). Figure 98 (A, B, and C) shows complete development of a block or panel. Customarily all of this work is not done before stoping begins, but usually only one or, at most, two sublevels are opened at a time, beginning at the top of the ore. Sublevels are developed by first connecting the tops of the raises with a longitudinal drift from which timbered slice drifts are driven right and left to the ore boundaries or to the limits of the panel. Usually, alternate drifts
are driven first, and caving back from them is begun and continued toward the raises while the intermediate slices are being driven. The bottoms of the slices or crossdrifts are covered with poles or plank, laid on cross timbers to form a good floor over which to scrape and to hold back the gob when caving the next sublevel below.
Caving is begun at the ends of the slices by blasting cuts, as shown in figure 98, D, and is continued in successive stages, working out toward the raises. The broken ore is dragged by power scrapers into the raises.
More recent practice in at least one mine is to cave back two adjacent slices at a time, using a 50-foot instead of a 25-foot sublevel interval and an entrance manway to the cave, as shown in figure 99. When the top sublevel or a section of it has been mined out work is begun on the next sublevel below.
Sublevel caving may be employed for mining smaller deposits than would be suited to block caving, but is also applicable to large ore bodies and to soft ores, which will stand fairly well for a brief time over short spans but will cave over wider openings. The capping (and later the gob) must be of such character that it will hang up long enough to permit removal of the caved ore from beneath it in safety and without serious attendant dilution with waste. Schaus has summarized the conditions necessary for successful sublevel caving in the iron mines of the Gogebic range, as follows:
The determining conditions to which this method is adapted are (a) a dipping and pitching irregular ore body, which does not lend itself to top slicing; (b) a medium-soft ore which breaks fine yet stands well and is not free-caving; (c) a hard capping which caves in medium-sized blocks without much fines and which is easily controlled.
The method is also employed successfully in hard ores and may be used under conditions where top slicing would be dangerous because of the hanging up of the gob. For successful block caving the ore should be free-running; that is, it must be of such a nature that it will not pack and form a semisolid mass that cannot be drawn off through the draw raises. Due to the relative thinness of the slices and the small size of the units caved in sublevel caving, packing is not so serious an obstacle and the method can be used for mining softer and somewhat stickier ores than can block caving.
https://www.youtube.com/watch?v=-9BDHl_acrU
Top Slicing Mining Method
The term “top slicing” is applied to the method of mining whereby the ore is extracted by excavating a series of horizontal (sometimes inclined) timbered slices alongside each other, beginning at the top of the ore body and working progressively downward; the slices are caved by blasting out the supporting timbers or allowing them to crush, bringing the capping or overburden down upon the bottoms of the slices, which have previously been covered with a floor or timber mat to separate the cave from the solid ore beneath and prevent admixture of waste with the ore (figs. 100 and 101). Successive slices are mined in a similar manner up to the overlying gob or mat, which consists of an accumulation of broken timbers, flooring, and lagging used in the overlying slices and of caved capping or overburden. As the slices are mined and caved, this mat follows the mining downward, filling the space formerly occupied by the ore. The mat also serves to control the movement of the caved overburden and to prevent dilution of the ore with barren capping.
Top slicing is applicable to the mining of soft, weak ore that will stand unsupported for only a very short time, even over narrow spans, and that is overlain by an unconsolidated overburden or a weak capping that will break up and cave promptly after removal of support, tightly filling the space formerly occupied by the slice and leaving no open holes. It may be applied in tabular deposits lying at all angles of dip, from flat to vertical, or in wide, thick ore bodies. It is used successfully in deposits of very irregular outline and is employed for recovering pillars of ore from between filled or caved stopes and for mining broken ore or old caves that could not be worked safely from the bottom upward. The method is similar in some respects to sublevel caving—the ore is mined from the top downward by a series of slices, and the overlying strata cave and follow the mining downward with a mat intervening between the caved overburden and the ore beneath. The methods differ, however, in that in top slicing the slice is mined right up to the floor of the caved slice above, whereas in sublevel caving the sublevel interval
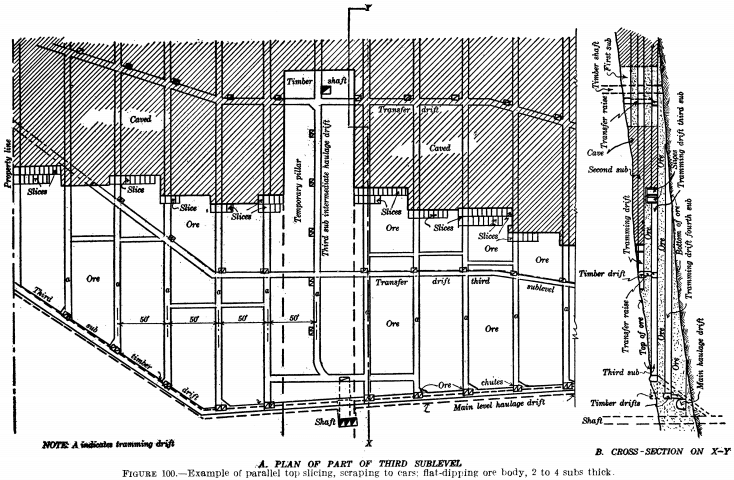
is greater (usually about twice), and in driving the slice drifts a back of ore is left over the tops of the drifts and below the mat of the slice above, which is extracted later by caving on the retreat. In sublevel caving the slice drifts are separated by intervening pillars, which are also mined on the retreat, whereas in top slicing they are driven immediately alongside each other.
The method has been applied most commonly in the mining of wide deposits of soft or weak ore overlain by a friable capping or unconsolidated overburden. A capping that breaks in large blocks that will wedge and arch over, leaving open holes in the gob, would be dangerous for top slicing. Hence, top-weight or vertical pressure is an essential condition for successful top slicing. The side walls may be either weak or strong.
Since top slicing requires the use of considerable timber and lagging, it is essential that there be a plentiful and cheap source of suitable timber available. Slice timber is required to stand for only a short time and is then blasted down or allowed to crush; a poorer grade is acceptable than would be required for more permanent supports, such as for drift timber. However, the timber should be tough and capable of standing considerable crushing before breaking.
A special application of the top-slicing method has been used for mining pillars between filled stopes under a capping that will not cave readily, even over large spans. In this instance, sand or waste filling is run in on top of the subsiding gob, keeping the hole filled. The filling will then act as a cushion to take the impact of any possible sudden collapse of the capping.
Combinations of Supported and Caved Stopes
The use of two or more stoping methods independently of each other in the same mine, or even in different parts of the same ore body because of differences in the physical characteristics governing the requirements for support, does not constitute a combination method.
A combination method does exist, however, when a stoping system is laid out in advance of operations wherein two different methods are employed as essential complements, one to the other. An example is furnished where a series of alternating stopes and pillars is laid out, the stopes to be mined by shrinkage and then filled, or by cut-and-fill stoping, and the pillars to be mined by top-slicing between the filled stopes. Each method, one a supported-stope method and the other a caved-stope method, is essential to the complete extraction of the block of ore. Again, a block-caving system in which a considerable part of the ore is mined by shrinkage in undercutting stopes and boundary cut-offs and the balance by caving in reality constitutes a combination method. (It should be noted, however, that in modern block-caving practice only a small percentage, perhaps 2 to 5 percent of the ore, is customarily mined by shrinkage stoping.)