Table of Contents
It is fairly easy to separate the capital cost for SX from that for EW. For this reason one might choose to categorize the operating costs in the same way. However, because of the way SX-EW plants are designed and operated and the manner in which costs are allocated this can be a difficult task. The approach of this paper is to treat labor and power requirements for SX-EW as a whole but to assign most other costs to either SX or EW.
Reagent Consumption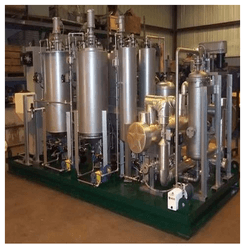
When SX-EW technology was first introduced two of the major concerns of the copper producers were the possibility of high reagent losses and reagent contamination. The authors are not aware of any case where reagent contamination has been a severe problem in the type of SX plants under discussion. This is due primarily to two reasons:
a) The operating companies practice good circuit hygiene. They generally do not add anything to the circuit without first talking to reagent suppliers and if needed, either run themselves or have the reagent supplier run, compatibility tests;
b) many contaminants wash out of a circuit with time.
Generally reagent losses in most operating circuits are not excessive. Table 5 shows reagent usage data for many of today’s operating plants along with specific flow per unit of settler area. Of particular interest is the column showing reagent consumption per unit of copper produced. Note that this number for steady state operating plants ranges from a high of .0078 Kg reagent/Kg Cu to a low of .0015 Kg reagent/Kg Cu with an average of .0046 Kg reagent/Kg Cu.
Reagent losses can be classified as physical or chemical. Physical losses include:
- Entrainment of organic in exiting streams (raffinate and electrolyte)
- Loss of organic in circuit crud
- Leaks and/or spills
Entrainment losses are usually caused by very small organic droplets in the aqueous phase which do not have a chance to coalesce into larger drops and float out of the aqueous phase. Factors which should decrease entrainment are: 1) longer settler residence time, 2) proper emulsion distribution so that even flow down the settler is obtained, 3) proper mixing, 4) the correct phase continuity, 5) avoiding a high viscosity in the feed solution, 6) steady state flows, and 7) higher staging. This discussion assumes the settlers are of sufficient size so that emulsion is not passing beneath the aqueous underflow weir. If this happens organic losses become excessive and immediate action is necessary.
Organic losses by leaks and/or spills should be insignificant in a welt operated and maintained plant.
The major chemical loss of reagent is by hydrolytic degradation. This topic has been discussed by several authors and there is some disagreement on how serious the problem is. Analyses of circuit organics show that in most plants running at steady state the concentration of degradation product reaches a certain level and then holds fairly constant. At this point the rate of formation of degradation product is equal to its rate of loss. Assuming that the majority of the degradation product is lost via entrainment and knowing reagent usage in the plant the amount of reagent lost by degradation can be calculated. These calculations show that degradation losses are .001 Kg reagent/Kg Cu or greater for some plants but much less for others. Factors which result in increased reagent degradation are higher acid concentration and higher temperatures in stripping.
The structure of the reagent is also important. Laboratory experiments suggest that:
- Ketoxime extractants are more stable than aldoxime extractants.
- Aldoxime extractants based on 5-dodecylsalicylaldoxime are more stable than those based on 5-nonylsalicylaldoxime.
- The use of equilibrium modifiers with aldoxime extractants enhances the rate of reagent degradation.
In looking at the data in Tables 5, 10, and 11, it is very difficult to find trends and draw any conclusions about the relationship of reagent usage to specific flow in the settler, tankhouse acid, and staging. Reagent usage in plants B, D, and M appear to be higher than normal while that for plants A, C, E, F, and N are lower than normal when staging, tankhouse acid and settler size are considered.
Kerosene Usage
The selection of a proper kerosene is important since the organic phase in the copper SX plants under discussion is 80% or more diluent. Kerosene usage is a function of the entrainment of organic phase in the exiting stages with some diluent loss also due to evaporation. Of interest is the fact that several operating plants do not cover their settlers (D, G, I, L, and N). It might be expected that this would result in a significantly higher diluent use because of evaporation. Table 5 shows the volume % of reagent reported in each of the operating circuits and the volume % of reagent added along with kerosene for the past year or more.
Major Tankhouse Costs (Table 6)
Anode Consumption
The data received on anode consumption was not as complete as much of the other data but it does show a wide range of anode usage; from a high of .171 anodes/tonne Cu to a low of 0.013 anodes/tonne Cu with an average of 0.067 anodes/tonne Cu. The data suggests that Pb-Sb anodes are consumed faster than Pb-Ca but this conclusion is tenuous since it is based on a very small sample. A recent presentation suggests that the method of manufacture may have more to do with the anode stability than the alloy. Research on anodes is continuing and anode usage is expected to lessen as anode quality increases.
Electrolyte Bleed
The only way to control impurity levels (primarily iron) in the recirculating electrolyte stream is to bleed the electrolyte at whatever rate is required to hold the impurity at the desired concentration. With the excellent copper over iron selectivity displayed by today’s reagents tankhouse bleeds are normally less than 5% of the electrolyte advance flow. Since the bleed reports either back to the extraction section or to the raffinate the copper is recycled and in most cases the acid is consumed in leaching. Cobalt in the electrolyte, used to reduce lead contamination in the cathodes, is lost but the cost is not a major one. In the rare case where the bleed is not recycled the costs associated with it are much more important.
Power Consumption
The electrowinning process is power intensive, thus, current efficiency is very important, especially where power costs are high or where a more efficient use of power yields increased copper production. Current efficiencies in the high 80 to low 90% range are normal and most EW plants surveyed operate in this range. High current efficiency and superior quality copper go hand in hand with a well run tankhouse. The small costs associated with running a tankhouse well are normally far less than the resulting savings in power and increased price for copper. Overall power consumption in EW should be a little less than 7.92 KJ/Kg Cu (1 Kwh/Lb Cu).
Miscellaneous Tankhouse Costs
Electrolyte filters to remove entrained organic, mist suppressants, smoothing agents and maintenance supplies all add to the EW costs. Normally these combined costs are not high, amounting to less than 3-4 U.S. cents/Kg Cu, and some plants run quite well without any of these items other than maintenance supplies.