Table of Contents
- Solvent Extraction Applied to Metallurgy
- Profitable Solvent Extraction Principle
- Hydrometallurgy Simplifies Chemical Engineering Theory
- Choice of Solvent
- The Phenomenon of Synergism
- Effective Use of “Shakeout Tests”
- Extraction
- Solvent Loading
- Counter-Current Mixer-Settler Units
- Analyzing the “S” Type Isotherm
- Determining Relative Extraction
- Stage Calculations
- Predicting Changes in Counter-Current Systems
- Determining Rate of Extraction
- Identifying Phase Separation
- Slime/Solids Problems
- Techniques in Determining Coalescence Rate and Settler Area
- Interpreting Data on Settler Area
- Determining Depth of Settler
- Electrical Determinations in Process Identification
- Capacity Increase By Coalescence
- Measuring Solvent Loss
- Stripping
- Solvent Extraction Design Problems
- Solvent Extraction Equipment
In recent years, the principle and theory behind solvent extraction has gained wide acceptance as one of the new tools of modern hydro-metallurgy. With the growing demand for metals of ever higher purity, the increasing use of unusual metals, and the necessity for treating ores of lower grade and greater complexity, solvent extraction has joined the ranks of other accepted recovery methods and has added certain unique characteristics of its own in the constant struggle to lower costs.
Analytical chemists have been using solvent extraction in the laboratory for many years for extraction of molecular species from aqueous solutions by organic solvents. However, the requirements and objectives of an analytical procedure are quite different from those of a profit producing mill flowsheet.
The chemical process industries have made use of solvent extraction as a unit operation for over thirty years. Oil refineries have made applications of liquid-liquid extraction. Technical literature is full of references covering the theory and application of this mass transfer principle to the chemical industries.
Solvent Extraction Applied to Metallurgy
The adaptation of the solvent extraction process to the metallurgical industry has been extremely slow up until recent years. As an operating procedure this process was initiated during the war years as part of the atomic energy effort. A large part of the uranium for use in nuclear reactors was recovered from ores by procedures using solvent extraction for purification of solutions. In addition, some of the man-made elements such as plutonium, americium and curium were purified in nuclear processing systems by the use of solvent extraction techniques. These operations were not concerned with making a profit but they did serve to stimulate research and development work which ultimately served as the basis of profitable recovery methods. Solvent extraction is now used in commercial plants for the recovery of uranium, vanadium, tungsten, thorium, and boron. It has been shown in pilot plant work that it may be used for recovery of tantalum and columbium, hafnium and zirconium, the rare earths, nickel and cobalt, and is even being explored actively in many different laboratories for the recovery and/or purification of phosphoric acid and other chemical compounds. It can be used to extract copper from ammonia solutions and iron from acids.
Profitable Solvent Extraction Principle
In principle almost any known metal and most of the non-metals can be separated and purified by a solvent extraction method. The question is not how to do it technically but how to devise a flowsheet which will result in a profitable operation. In order to do this it is necessary to understand clearly the nature of this new kind of process, its virtues and its limitations.
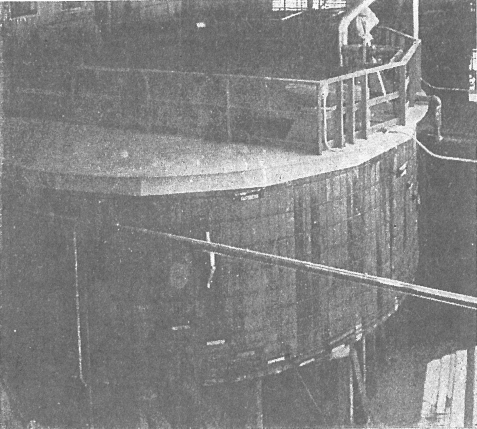
This five-stage commercial solvent extraction system eliminates all need for acid-proof pumps and piping. The mixing and settling and counter-current flows of both the aqueous and organic phases take place in the self-contained solvent extraction system.
The primary use of solvent extraction in hydrometallurgy is to purify and concentrate mineral values from solutions economically. Obviously, therefore, it cannot make a profitable recovery from an ore where the cost of initially placing the desired element or elements into solution is prohibitive. The solvent extraction method is merely a new tool available to the extractive metallurgist. There are probably many circumstances in which it need not even be considered. However, because it is a relatively new method, it is one which should be explored thoroughly whenever there is a need for purification and concentration from solution.
The purpose of this paper is to discuss the principles and practices of solvent extraction in hydrometallurgy from a rather particular point of view. This point of view is not that of the mill operator, but rather those of the technical staff who are faced with an extractive metallurgy problem, and who are not completely familiar with the research and development effort which provides the practical and theoretical foundation for a good flowsheet and successful plant design.
The underlying theory and basic laboratory techniques are discussed and methods of scale up to larger sizes are presented.
Hydrometallurgy Simplifies Chemical Engineering Theory
Although solvent extraction utilizes the same basic theory whether it is used in a metal recovery plant or any other chemical process there are certain restrictions in hydrometallurgy that simplify the solvent extraction calculations. These simplifications have made it easier for the hydrometallurgist to guide his experimental work and to calculate from his laboratory results the proper scale up factors for large plant design. For example, many of the complications of solvent extraction applications in the chemical industry arise from the fact that the solvent is soluble to some extent in the solution from which the extraction is being made. For most conceivable hydrometallurgical applications the solution from which the extraction is being made is water and the solvents selected must be insoluble and immiscible with aqueous solutions to avoid prohibitive solvent loss. Therefore, marked simplification can be made in the chemical engineering theory.
First Step: Extraction
Fundamentally, solvent extraction (S-X) starts with a mass transfer operation in which a constituent of one solution is transferred to another solution through an interface between the two. Since we are concerned here only with application to extractive metallurgy, the first solution is always a water solution of the desired element and the second is the organic solvent.
This first step in the process is called the extraction. It is governed by the laws of chemistry applicable to the reactions involved and by the practical aspects of mixing two immiscible liquids in such a way as to make the transfer of the desired constituent feasible from both the technical and economic standpoints.
Second Step: Stripping
The second major part of the S-X operation is the recovery of the desired material from the organic solvent in a purified and concentrated form in such a way that the organic solvent can be recycled to the extraction operation. This second step is usually called “stripping.”
In general, the extraction step does the largest degree of purification because of the selectivity of the solvent used while the major part of the concentrating is done during stripping.
Regardless of how complex a circuit may be with wash steps, reflux, regeneration and so forth, the two basic parts: extraction and stripping, can always be identified.
Choice of Solvent
In order to be used profitably the organic material which serves as the extractant must have a variety of properties. Of prime importance is the specific reactivity of the solvent with the particular element desired. Some properties are the same for all solvents, i.e. stability, low toxicity, high flash point; others are strictly dependent upon the particular element and solution involved. In fact, the complexity and multiplicity of choices facing the extractive metallurgist are almost bewildering and sometimes it is difficult to know how to start the development work. Here the basic chemistry of solvent extraction must serve as a guide.
There are two types of solvent extraction processes which must be considered. The first of these is sometimes called liquid ion exchange because of its similarity chemically to the ion exchange resin type of extraction which is well known to the extractive metallurgy industry. In this kind of extraction a small quantity of an organic chemical is dissolved in a second organic liquid called the diluent. This diluent may be a material such as kerosene or some other inert hydrocarbon, but its essential function is to serve as a carrier for the active solvent component. During the extraction operation the active component reacts chemically with the desired ions in the aqueous feed forming a new compound which is soluble in the inert diluent, or carrier.
Large propeller type agitators are used for leaching in the dissolution step preparatory to the subsequent solvent extraction of values. Acid-proof equipment is used throughout Large diameter leaching agitators reduce the number of units required and permit a compact high-tonnage plant.
View or leaching, precipitation, filtration and repulpings section in a modern solvent extraction mill. Construction of this mill provided one-level operation with elevated walkways.
One might almost form a mental picture of the active organic material “reaching out” of the kerosene into the aqueous phase attaching itself to the desired metallic ion and then retreating back into the kerosene dragging the metallic ion with it. In this way a great deal of selectivity can be achieved by changing the nature and characteristics of the organics involved. Extraction of uranium by amines is an example of this kind of solvent extraction. The second type of solvent extraction is one in which the entire organic phase acts as a solvent for some component of the aqueous phase which is soluble in both water and in the organic. This is sometimes called ion pair extraction. An example of this is the extraction and separation of tantalum and columbium from hydrofluoric acid solution with hexone.
The chief reason for drawing the distinction between these two mechanisms for extraction is that one extracts an ion by compound formation with the active part of the solvent mixture and the other extracts a neutral molecule (ion-pair) by preferential solubility.
This latter type of solvent extraction should be considered in situations where it is possible to add to the aqueous solution some material such as thiocyanate which will form a compound with the desired metal ion making it soluble in certain types of organic solvents, this type of solvent extraction has some different properties than the ion exchange type, particularly the chemistry of the reactions involved.
The ion exchange type of extraction so far has been confined to the use of an inert carrier usually comprising 75 – 95 percent of the total organic phase and containing either an amine, an alkyl phosphate or a sulfonate. The large number of choices facing the metallurgist makes the preliminary “shake out” tests very important in solvent extraction work. It is precisely this complexity and variety that is part of the
strength of the solvent extraction method because it offers the metallurgist such a wide choice of variables to use in achieving the highest degree of selectivity and concentration at the lowest cost. Of course, if the metallurgist has a flare for organic chemistry, he is at liberty to invent his own active ingredients.
At the present there are only a few commercial solvents which are widely used. These are the secondary, tertiary and quaternary amines and some alkyl phosphoric acids. The amines act by forming an organic soluble salt with the anions whereas the alkyl phosphoric acids react with cations. The choice of the proper reagent and the possibilities in the use of complexing agents added to the solution are subjects of much interest in laboratories throughout the country. They offer the hope for the extension of the solvent extraction technique to situations which are not dreamed of today. Lists of the various kinds of solvents available commercially can be found in technical literature.
The Phenomenon of Synergism
In addition to the carrier and the active reagent in the liquid ion exchange type of solvent, there is usually added a third reagent called a modifier. This modifier is added for a number of reasons. One reason is that it sometimes increases the extracting power of the solvent through synergism. Synergism is the phenomenon where simultaneous action is greater than the sum of the individual actions. In other words, the whole is greater than the sum of the parts. For example, the addition of tributyl phosphate to di-2-ethyl-hexyl phosphoric acid will vastly increase the extractive power of the alkyl phosphoric acid for uranium from sulfate solutions whereas tributye phosphate by itself will not extract uranium from the same solution at all. The phenomenon of synergism is not well understood and it also constitutes a fertile field for further research.
Many compounds such as di-butyl-butyl phosphonate, phosphine oxide, and others have been found to enhance markedly the extracting power of certain solvents.
In addition to this improvement in extractive power and sometimes in selectivity, the modifiers are often added to improve phase separation. Isopropyl alcohol, for example, is a common additive which is used to improve phase separation characteristics, although its use must be treated with caution as it sometimes depresses the extraction coefficient.
A third reason for the addition of modifiers is to prevent the formation of some insoluble compounds in the organic phase. For example the addition of alcohol will help depress the formation of molybdenum amine solid precipitates in the organic phase in molybdenum extraction. The addition of tributyl phosphate to dimethyl hexyl phosphoric acid will prevent the formation of the insoluble sodium di-2-ethyl-hexyl phosphate during the stripping operation of some uranium extraction circuits.
Effective Use of “Shakeout Tests”
Because of the many combinations which are available it is not always possible to give precise directions for the preliminary exploratory work to select the proper solvent. S-X test work is analagous to flotation test work where certain classes of collectors are available for sulfide ores and others for oxides, but the optimum combination can be determined only after many flotation tests.
The best advice for starting the study is to make what are called “batch shake out tests.” A solvent chosen from the proper class (amine, phosphate, sulfonate, etc.) is shaken in a separatory funnel with some of the solution from which the extraction is to be made. After about one minute of vigorous shaking the phases are allowed to separate (if they will) and each phase is analyzed. This gives a guide as to what solvent combination to investigate more thoroughly. The visual observation made in this step regarding speed of phase separation, interfacial scum, insoluble compounds, etc., are very important.
This procedure permits the test engineer to make a basic choice of solvent system, but it is still a long way from being a process.
Extraction
Regardless of what solvent is chosen, the metallurgist is then faced with the question of doing the laboratory work to develop a flowsheet upon which plant design and operating cost estimates may be made. His first questions are logically: how complete is the extraction, and what kind of information must be developed in the laboratory to use as the fundamental design basis.
This introduces two basic concepts used in solvent extraction technology:
- distribution coefficient and
- solvent loading
The distribution coefficient (K) is a measure of how well a given solvent will extract and hold in the organic phase a constituent from the aqueous feed liquor. It is a measure of the over all chemical driving force, analagous to the equilibrium constant of an ordinary chemical equation. It is therefore dependent on all the chemical concentrations involved. In the present state of the art there is no way to calculate from theory the magnitude of this coefficient but it can be measured quite easily. In its simplest form it is defined as follows:
K = Concentration of metal in organic phase./Concentration of metal in aqueous phase.
The concentrations referred to are those which are measured after the organic and the aqueous have been shaken together for a long enough period so that whatever is going to happen has happened. The aqueous phase after such an extraction is called the raffinate.
The laboratory metallurgist therefore can take a small sample of his aqueous solution containing the metal which he has in some way dissolved from the ore and shake it up with the organic solvent that he wants to test. After the shaking has gone on long enough so that he feels that no more extraction will take place, he permits the phases to separate and analyzes them separately. The expression of the concentration in the organic divided by the concentration in the aqueous is then called the distribution, or sometimes the extraction coefficient. The bigger this number is, the greater is the tendency of the metal to extract into the solvent.
https://www.911metallurgist.com/solvent-extraction-plant-design/
Solvent Loading
In the case of the liquid ion exchange solvents there is only a limited amount of the active ingredient in the solvent phase, therefore it can only hold at saturation a limited amount of any given element. After the concentration of metal in the solvent has reached this level no more will go into the solvent regardless of what the concentration is in the aqueous phase. The amount of metal which a given solvent will hold is called the maximum loading and is an important characteristic that must be determined about any solvent system since it governs the total amount of solvent flow necessary to do a certain amount of extraction.
The concept of the distribution coefficient is most useful for comparing extraction systems when measurements are made at such low concentrations that the quantity of metal which has been extracted does not use up more than a few percent of the total extracting power of the solvent, i.e. where the solvent loading is only a few percent of maximum. Under these circumstances the comparison of distribution coefficients between various systems is a useful measure of the comparative extraction power. The numerical value of the distribution or extraction coefficient will change as the concentration of metal in the aqueous and the organic changes for liquid ion exchange types of solvents. In general they are higher at low concentrations. This is not so true for the ion-pair type of extraction.
The distribution coefficient has a very practical use in addition to comparing relative solvent strengths. It is the basis for the calculation of the efficiency or percentage extraction of a total system composed of many different stages. If a single extraction is made and the raffinate from that extraction is treated with fresh solvent, more material will extract. In this way ultimately all the metal can be transferred to the organic and therefore separated from the other impurities associated with it originally.
Counter-Current Mixer-Settler Units
For many reasons, to be discussed later, the counter current mixer – settler unit has become the favorite mechanical system for achieving counter-current extraction in ore treating mills. Therefore the following discussion refers to mixer-settler stages but the principles are applicable to other types of extraction equipment.
In conducting laboratory tests to develop a particular system; several different samples of the aqueous feed are added to different volumes of the solvent and thoroughly mixed.
The phases are then allowed to separate and are analyzed. Different quantities of the metal will have been transferred from the aqueous to the organic phase depending upon the relative volumes of the phases and on the extraction coefficient. If these data are then plotted and a graph drawn of the concentration of metal in the organic phase versus the concentration in the aqueous phase, the resulting plot is called the distribution isotherm. An example of one such isotherm for uranium extraction is shown as Curve I in Figure 1.
For a good extraction system the graph drawn in this way shows three parts. The first one close to the Y axis should show a steeply rising curve where the concentration in the organic rises very swiftly for small concentration changes in the aqueous.
The value of having a steep curve in this particular region means that in operating the system it would be possible to achieve very low raffinates and therefore high percentage recoveries at the tail end of the system. The second part or middle portion of the curve is one in which the distribution coefficient is changing rapidly with increasing change in concentration of the aqueous.
The third part of the curve is almost flat and is the portion representing the situation when the solvent is fully loaded and cannot hold any more metal no matter what the concentration may be in the aqueous phase. This concentration in solvent represents the maximum loading that could be achieved in any operating system and therefore fixes the minimum amount of solvent which must be used to transfer the desired amount of metal.
Analyzing the “S” Type Isotherm
Curve II in figure 1 shows the isotherm for a system where real trouble could be predicted in achieving good recoveries. This is the so-called “S” shaped isotherm which is encountered in some extractions, for instance in extraction of oxidized vanadium with an amine solvent, and in the extraction of molybdenum. This “S” shaped curve comes about when there is some trouble with the chemistry of the extraction at very low concentrations. For example, there may be a second molecular species present in some concentrations which does not extract, so that after the major portion of the metal has been extracted all that remains is the non-extractable species. Other explanations for the “S” type isotherms such as polymerization in the organic phase have been suggested. When a distribution isotherm such as this is
encountered it means that the aqueous cannot be extracted down below certain levels and thereby represents a loss of the desired metal in the raffinate. This is one reason for doing a complete isotherm rather than merely determining maximum loading.
It can be seen from this that the distribution isotherm, which can be obtained quite easily in the laboratory, is a most useful diagnostic tool to predict the kind of metallurgical behavior to expect.
Of course the percentage extracted is the final criterion of the usefulness of the process and this also can be determined for any given ratio of organic to aqueous from the distribution isotherms.
Determining Relative Extraction
For any single stage of extraction the percentage extracted is related to the distribution coefficient by the following equation:
% extracted = P K/1 + P K x 100
Where P is the phase ratio, i.e. the volume ratio of organic to aqueous, and K is the distribution coefficient.
When the distribution coefficient measured at low aqueous concentration is as high as 10 or higher very complete extraction can be obtained with a small number of stages. Even if the number is only 1 to 2 it can still be used successfully although more stages are needed. Coefficients of 50 to 500 are common in uranium extraction.
The relative extraction of two elements from the same solution can be compared by calculating the ratio of their individual distribution coefficient. This ratio is called the selectivity or separation factor. It defines the purification that can be achieved.
Stage Calculations
A second important use of the distribution isotherm is in predicting the number of counter-current stages which would be needed to achieve any given percentage extraction of the desired metal. This is done by the use of a McCabe Thiele diagram. In such a diagram the distribution isotherm is plotted in the standard manner and then a second line called the “operating line” is drawn on the same graph. The slope of the straight “operating line” is numerically equal to the ratio of aqueous to organic phases and as a first approximation starts at the origin of the graph. This “operating line” merely expresses graphically the material balance of the system; in other words the fact that when something is extracted from the aqueous phase it must then be in the solvent phase.
Another way to say this is that the operating line expresses the mathematical fact that during extraction in any stage the increase in concentration of metal in the solvent is equal to the decrease in concentration in the aqueous multiplied by the relative volume of aqueous and solvent.
When both the distribution isotherm and the operating line are drawn on the same graph, calculation can then be made for any desired counter-current multiple stage system.
Figure 2 shows how this is done graphically.
A vertical line is drawn starting from the feed aqueous concentration. Where this line intersects the operating line a horizontal line can be drawn until it intersects the distribution isotherm. A vertical line is then drawn down to the operating line from this intersection. In this way a series of steps can be drawn between the operating line and the distribution isotherm.
At each intersection with the distribution isotherm, the corresponding values of organic and aqueous concentrations will be the actual assays that will be found in a counter-current system operating with the number of stages shown as the number of steps. Adjustments must be made in the starting point of the operating line in case the solvent entering the bottom stage is not completely barren. In this way one can lay out from laboratory data the number of stages that are required to obtain any desired raffinate concentration and thereby calculate the percentage extraction to be expected.
Predicting Changes in Counter-Current Systems
It is possible by changing the slope of the “operating line” to make a prediction as to what would happen in a continuous counter-current stage extractor if the organic flow were changed relative to the aqueous flow.
The assumption underlying this curve is that each stage arrives at a true equilibrium. However, the curve can be corrected for any desired stage efficiency and in fact a comparison of these data with operating data from a continuous counter-current extractor permits an evaluation of the real stage efficiency of the extractor, or the number of theoretical stages if the extractor is not of the discrete stage type.
Determining Rate of Extraction
As well as making a determination of what extraction to expect based upon distribution coefficients, the laboratory metallurgist needs to assess the rate at which the extraction takes place. This is done rather simply by agitating the aqueous and the organic together, withdrawing samples at time intervals, and analyzing each phase for the extracted constituent. By drawing a plot of the percent extracted as a function of agitation time it is possible to determine the mixing time required to reach equilibrium. As would be expected it is usually found that the speed with which equilibrium is reached is affected by the turbulence of the agitation (specific power input), by the temperature and by the other factors which affect the rate of mass transfer, such as viscosity, etc.
Mixing times of a minute or so are entirely adequate for the ordinary type of uranium extraction. For vanadium, however, mixing time must be carefully determined and may be as long as five minutes. In such cases the short-circuiting factor becomes important and consideration must be given to using a number of mixers in series for each stage.
Identifying Phase Separation
Once the laboratory work has shown that it is possible to extract the desired constituent from the aqueous feed into an organic solvent, the next problem is to separate the aqueous-organic mixture and make some evaluation of organic losses and system operability. The separation of the organic and the aqueous, called phase separation, or settling, is frequently done in mixer-settler systems by flowing the mixture of organic and aqueous from the agitator mixing device into a large quiet tank where the phases separate. In the terminology of solvent extraction the use of the word emulsion is ordinarily reserved for situations where the mixture of aqueous and organic are exceedingly slow to separate.
Technically the mixture in the mixer is an emulsion, but by custom in hydrometallurgy it is not referred to as an emulsion unless it is a problem. In any event the sharp separation of the organic and aqueous is of fundamental importance to the practicability of the process and its economic success. It is important to know how to deal in the laboratory and pilot plant with phase separation problems so that the test work will give valid data. Phase separation takes place in two steps. The first one is called the primary break. In this primary break the bulk of the mixture separates by a process of coalescence and settling into the two component phases. This primary break is the one which really controls the size of the settler to be designed. It is followed by a gradual clearing of both phases where ultra-fine droplets settle out. If this final clearing does not take place within the settler in a counter-current system it does not materially harm the efficiency of the system. However, the final raffinate must have all the fine solvent removed to avoid excessive solvent loss and the loaded solvent should be free of fine aqueous droplets to avoid contamination of the strip liquor.
Slime/Solids Problems
The speed of the primary break is influenced strongly by the presence of fine solids such as ore slimes. There is at present no adequate way to predict the seriousness of this effect. There are cases where solvent systems have tolerated large quantities of fine ore slimes without apparent harm and other cases where small amounts gave large solvent losses.
Sometimes slimes will accumulate at the interface in the settlers and have to be removed periodically through special skimming methods.
There is little doubt that as more knowledge is gained, additives will become available to combat the effect of solids in the feed but for the present it is safest to provide for clarified feed liquors in the design.
The rate of coalescence and therefore the speed of the primary break is faster for systems with high interfacial surface tension. Therefore, surface active agents which lower the interfacial tension slow the rate of coalescence and slow the separation rate.
The settling rate is slower the higher the viscosity of the continuous phase, the less the density difference between phases and the smaller the size of the droplets of the dispersed phase.
The aqueous-organic mixture when it flows into the settler is a dispersion of one phase in the other. This collects in the settler tank as, a dispersion band at the interface between aqueous and solvent. The capacity of a settler is reached when the flow rate is so large that this dispersion band swells up and is thick enough to flow out of the organic or the aqueous discharge port.
Techniques in Determining Coalescence Rate and Settler Area
There are two useful laboratory techniques to determine the coalescence rate. One is a static method and the other a dynamic method. In the first system the mixture of aqueous and organic is first agitated intensely and then is allowed to settle quietly in a graduated cylinder. The distance of the top and bottom edges of the dispersion band are measured as they coalesce to one interface line and these are plotted as a function of time. This plot is used to calculate what volume of the mixture can be permitted to flow into a quiet tank for each square foot of the tank area. Figure 3 is a succession of photographs taken at intervals showing the change in dispersion band thickness obtained in this manner.
A second way of arriving at the settler area is through the use of a dynamic system in which a miniature mixer-settler is established with a continuous flow of both organic and aqueous phases. The dispersion band is then measured at different flow rates of the components and this thickness is plotted as a function of the flow rate. It is found that ordinarily the thickness of the dispersion band will vary in logrithmic ratio to the volume flow of the dispersed phase. As a practical matter the flow rate at which the dispersion band is four or five inches deep can be used as a measure of the design capacity of a settler.
In the usual case this rate is about one-half of that required for a dispersion band two feet deep.
The flow rate of the dispersed phase is usually the most critical in determining settler area requirements.
Of course the thickness of the dispersion band will be markedly affected by the temperature of the solutions so that the test work should be done at approximately the temperature expected in the operating circuit.
The virtue of the dynamic system of measuring settler area is that it permits a quick visual as well as quantitative measurement of the variation in settler capacity with changes in the circuit variables such as pH, phase ratio, etc.
Interpreting Data on Settler Area
It is pertinent to comment that the figures which have come to be accepted as customary in the uranium industry for settler areas such as 1 gallon per minute per square foot of settler area, only hold true for these types of systems. A translation of this sort of number to a system such as phosphoric acid solvent extraction might be in error by a factor of 5. Therefore it is vital to make the determinations of the required settler area on the actual system under consideration and not to use any arbitrary figures which have been developed for other systems. It has also been observed in most uranium and vanadium applications that the phase separation characteristics are not particularly altered by the intensity or the duration of the mixing. This also may be true only for these systems and might not be the case at all when solvent extraction is applied to other uses.
The secondary break, which is the settling of the final small droplets of material out of each phase need not necessarily take place in the settler itself. It can be done in separate tanks at each end of the counter – current system. The secondary break is more concerned with the loss of organic in the raffinate and with entrainment of aqueous in the loaded organic than it is with settler area as such. The easiest way to make a measurement of these entrainment losses is by centrifuging small samples.
A picture of a dynamic system for measuring phase separation characteristics is shown in Figure 4.
Determining Depth of Settler
In addition to the area of a settler the depths must be specified also. This is based upon hydraulic and inventory considerations. The depth must be enough so that the change in interface level with changes of flow rates and densities will not permit aqueous to flow out the organic discharge line or vice versa. The inventory of solvent in the settler is a cost item but it also acts as an operating stabilizer to keep changes in feed concentration from affecting the efficiency too swiftly. Sometimes the depth of aqueous is important because it may constitute too large an inventory of a valuable material.
All these factors and others influence the choice of settler depth. Solvent depths in hydrometallurgical operations are customarily between four inches and two feet while the aqueous depth may be between two feet and six feet.
The characteristics of phase separation are altered by the type of mixing which takes place in the mixer.
There are two types of dispersions; one is a dispersion of aqueous droplets in organic and the other is a dispersion of droplets of the organic in aqueous. These two types of dispersions are fundamentally different in character. The type of dispersion in which the oil droplets are dispersed in the aqueous phase (called “aqueous continuous”) are very prone to have stable emulsions. The aqueous phase raffinate when it leaves the extractor may still have entrained in it tiny droplets of organic and thereby have substantial solvent losses. Particularly if there are any solids present or if there is an appreciable amount of colloidal silica in the aqueous phase, very tight non-breaking emulsions may form which can render a system inoperable. Conversely, the water in oil type of mixing in which water droplets are dispersed in a homogeneous organic phase (called “organic continuous” mixture) are much better from a standpoint of loss of solvent in the raffinate. They are much less inclined to promote stable emulsion formation and they are far less sensitive to the presence of solids. Ordinarily the continuous phase will be the one which is present in greatest volume although this is not always true. In
fact, it is possible in some instances to have two volumes of aqueous dispersed in one volume of organic. This is a matter, therefore, not only of relative volumes of the phases but of the presence of other constituents, surfactants, and also the way the mixing is started.
Electrical Determinations in Process Identification
It is particularly important in test work on settling and phase separation that a determination be made during mixing as to whether it is an organic continuous or an aqueous continuous kind of dispersion. This can be done very simply in the laboratory by determining whether the dispersion in the mixer is electrically conducting or not through the use of a Simpson meter or other conductivity measuring device. A simple instrument can be made by using a milliammeter and one flashlight battery connected so that when probes are immersed in the mixer they will complete the circuit. If the solution is aqueous continuous a current flow will be shown by the milliammeter. If the dispersion is organic continuous it will be non-conducting.
Since there is an effect of some importance on phase separation dependent on whether the mixer is organic continuous or aqueous continuous in operation, it is important to be able to control this type of dispersion.
Ordinarily, the volume flow of solvent is less than the flow of aqueous so that the amount of organic which is present is not enough to keep an organic continuous dispersion in the mixer. This condition can be achieved however, if a sufficient volume of solvent is returned from the settler to its own mixer. This constitutes a recycle and provides enough organic in the mixer so that the organic phase may be made the continuous one, thereby getting the benefits of this type of operation. This throws a greater total load on the settler but it has been found that for systems of the type ordinarily encountered in the uranium and vanadium industry, the settler area is affected more by the flow of the aqueous than it is by the flow of the combined aqueous and organic within certain limits. As long as the phase ratio in the mixer (organic to aqueous) is in the neighborhood of 1 or 1½ to 1 the settler area requirements do not need to be increased over those which would be found necessary if the recycle were not used. Almost all operating commercial units of any magnitude use the recycle principle.
Capacity Increase By Coalescence
The coalescence phenomenon referred to before can be used to advantage to increase the capacity of a given settler. Since any solid material which is wetted by a liquid will increase the rate of coalescence of droplets of that liquid, insertion of material into the active area of the settler will increase the rate of coalescence of droplets which wet the material.
For example, if the dispersion coming from the mixer to the settler is of the aqueous-in-organic type, (organic continuous) then putting stainless steel mesh or other water wettable material in this dispersion area
will provide a surface for coalescence and increase the settler capacity materially. It is possible (at least in the laboratory) to double the capacity of a given settler in this way. Another phenomenon which may be of advantage is electrical coalescence, although this is confined to the removal of water droplets from the organic phase. Here the application of a very high voltage to the organic phase will cause coalescence of aqueous droplets until they reach a large enough size to drop out by gravity. This could be very useful in cleaning up a loaded solvent of entrained aqueous droplets in order to improve purification.
Measuring Solvent Loss
One of the measurements which must be made in the laboratory concerns the loss of solvent in the raffinate. Since this is one of the basic cost elements of the process its determination can be critical as regards the economic feasibility of the flowsheet. Loss of solvent in an operating circuit can occur by evaporation, by chemical attack or by entrainment or solubility in the aqueous discharge from the circuit. It is assumed that no solvent will be proposed for commercial use which has a very high rate of chemical attack by the components of the system, but of course this is something which must be determined by long continuous runs wherever a new type of solvent is proposed. The loss of solvent by entrainment in raffinate constitutes one of the large potential costs of the process. The measurement of this is rather difficult because a fine dispersion of organic which may render the raffinate cloudy is apt to represent a large cost but be very difficult to measure quantitatively. There are several analytical techniques available which are helpful in solving this problem. One of them is to run the raffinate through a column of activated charcoal until a large volume has gone through a rather small column of charcoal. The quantity of organic absorbed on the charcoal can be determined analytically. A second technique is to take a sample of the raffinate, filter it through a silica filter aid, treat the filter aid with concentrated sulfuric acid at a high enough temperature to char any organic material which has been filtered out, and estimate the quantity of organic present by the depth of the brown coloration. Although this is an empirical system and must be standardized, it has been applied successfully in laboratory work. A third method is a variation of the solvent extraction procedure itself in which a large volume of raffinate is collected and then agitated quite vigorously in a mixer with a small volume of clean diluent which does not have any of the active ingredient used in the solvent extraction system, This diluent is then permitted to separate from the main volume of raffinate and it is analyzed for the active ingredient used in the solvent system. Another technique is to use long stemmed centrifuge tubes and centrifuge raffinate samples. Perhaps the most suitable method is to have a small continuous extractor and run it long enough so that significant changes in solvent inventory can be determined.
The continuous extractor also provides information concerning solvent degradation and long term effects. Some problems may be slow to appear and only become obvious after a solvent has been used 25 or 50 times. In a continuous extractor a solvent can be recirculated indefinitely and all these effects can be determined.
Figure 5 is a photograph of a continuous mixer settler unit built for development work of this nature.
Since there is usually some slight entrainment representing a monetary loss in the raffinate, it has been customary in mills to have the raffinate held up in a large settling tank which has been designed in accordance with the principles established by the American Petroleum Institute.
It has been demonstrated conclusively that the loss of solvent in the final raffinate is much less when the final stages of the extraction are operated with an organic continuous type of dispersion in the mixer. Total losses of less than 0.2 gallons of solvent per 1000 gallons of aqueous solution extracted have been obtained in practice.
Pilot-plant size solvent extraction system with transparent plastic tank permits visual control of the process as flows advance counter-currently. This unit is a typical 4-stage system. Mixer compartments have a retention volume of two gallons and the settlers have an area of two square feet. Capacity of the unit depends on the specific problem but ranges up to one g.p.m. flow of aqueous.
Metallurgists have many years’ experience in solvent extraction towards the solution of a nickel and chromium separation problem. Laboratory continuous mixer settler unit aids in the process development. Continuous extraction system provides information required for scale-up to commercial production.
Stripping
The stripping operation is the reverse of the extraction. In this step the loaded organic from the extractors is stripped of its valuable load and converted back to a form appropriate for return to the extraction step. The choice of solution to use as a stripping agent has almost as many possibilities as the original choice of solvent. It is possible to use water alone for some stripping circuits. Others use various concentrations of brines, sodium carbonate solutions, caustic, ammonia, complexing agents, reducing agents, etc. The fundamental point is that a chemical environment must be worked out which will cause the desired product to leave the organic phase and distribute into a concentrated aqueous solution from which it can be recovered.
It is not possible to cover briefly the many ways that stripping can be accomplished. Fundamentally the laboratory test work is concerned with the same general scope as the extraction studies. Mixing times and phase separation must be measured. In addition the stripping operation must restore the solvent to original activity for extraction.
Stripping test work must therefore include tests to check solvent activity and if necessary to develop regeneration methods.
Of particular interest are the possibilities for production of the final product as a solid precipitate in the stripping operation itself.
The distribution isotherm concept and stage calculations are similar to those described for extraction.
Solvent Extraction Design Problems
One of the scale-up problems in designing a solvent extraction circuit is the definition of adequate mixing in the mixers and the determination of the horsepower required for commercial size units. As far as uranium and vanadium extraction are concerned, it has been clearly established that scale-up can be made on the basis of geometric similarity, and equal power input per unit volume. This means that if the power input to a relatively small mixer (such as 25 gallons) is measured under mixing circumstances which give the extraction desired, this same power per unit volume of mixer can be used on a large scale and will give the same results.
Although this holds true for those uranium and vanadium plants where the appropriate measurements have been made, a word of caution should be given that this may not hold true for other systems. It has amply demonstrated in the chemical process industry that the scale-up of mixing devices on this basis may be very much in error, depending upon such factors as viscosity, density and so forth. It is strongly advised that if development work is being done on other systems, such as the extraction of relatively strong phosphoric acid, the appropriate scale-up parameters be determined before any translation to large scale units be attempted. The fundamental power equation for turbine type agitators states that the power required is proportional to the cube of the speed of the turbine and to the fifth power of its diameter. In order to make an accurate scale-up it would be necessary to determine, from the basic rate equation of the extraction, how the rate constant was affected by turbine speed, diameter and power input.
Solvent Extraction Equipment
In principle any system which achieves mixing and separation of phases, can be used for solvent extraction in hydrometallurgy. As a practical matter, however, the extractive metallurgy industry has pretty widely adopted the mixer-settler concept. There are a number of reasons for this, one of them is that the mixer-settler device is more amenable to handling slight amounts of solids which sometimes occur in operating mill solutions.
Fig. 6. Typical Mixer-Settler Solvent Extraction System comprises three circuits: Extraction, Washing and Stripping. Pregnant aqueous solution enters the system at the No. 1 Mixer (top of unit diagram) and advances through the system to leave the unit as barren aqueous, (top left). Barren organic solution enters the unit at the No. 4 Mixer (lower left) and advances counter-current to the flow of pregnant aqueous to leave the extraction circuit as pregnant organic. The pregnant organic solution enters the wash circuit and advances counter-currently to the flow of wash solution to enter the stripping circuit where the values are transferred to the strip solution. The values leave the system as the pregnant strip solution and the organic continues its counter-current advance to leave the system as barren organic (top right). The dotted lines in the diagram represent “recycle” of organic to permit greater loading and higher efficiency through reduced solvent loss.
Fig 7 Commercial application of solvent extraction to extractive metallurgy is demonstrated conclusively by this modern uranium solvent extraction system. The entire 8-stage mixing-settling system takes place in one square tank. This mill is treating 500 tons of ore per day.
Another reason for adoption of mixer-settlers is that they involve less capital cost and are very simple to operate and have a high degree of operating leeway without fear of flooding. With proper design all flows can be observed by the operator and sampled as required. They can also be started up or shut down without any particular control problem. The evolution of the mixer-settler systems for hydrometallurgical applications has gone through various phases. In some of the early applications both the organic and aqueous phases were pumped from stage to stage. Recycling where required was handled by airlifts or pumps. In a later development the aqueous or the organic phase flowed by gravity while the other phase and recycle was pumped. The latest evolution is the arrangement where the impeller in the mixer is of such design that it pumps both phases including organic or aqueous recycle if required. A diagram of how this is done in practice is shown in Figure 6. A photograph of an actual installation using this principle is shown in Figure 7.
With the development of new solvents, adequate laboratory techniques for working out new flowsheets, and the availability of practical commercial size equipment a bright future can be predicted for the use of solvent extraction in extractive metallurgy.