The concentration of mica is an unusual problem due to sheet-like, flaky structure of the minerals. Premium grades of mica demand a sufficiently high price that the ore can be hand-sorted and trimmed. However, the “punch” and “scrap” mica does not demand such handsome prices, so a method of concentration must be used. This system must have high capacity and be as nearly automatic as possible. Many different processes can be used and this study is limited to a specific problem and its solution.
Mica is usually associated with minerals which must be eliminated in order to produce an acceptable product for the market. The occurrence of mica, although usually restricted to pegmatite deposits, is rather spotty within the pegmatite. So the problem resolves into one of sorting out small and large pieces of mica from comparably sized gangue minerals.
The following grades of mica are given as reference. Clear ruby India muscovite mica has been the accepted world’s standard of quality, although in recent years other types have been used more and more in the higher types of electrical equipment. These tables point out the comparisons of United States grading system as compared with the grading system of India, used on larger sizes of mica than the small sizes covered in this study.
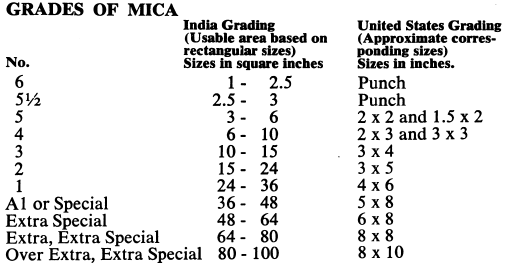
These gradings fall mainly into the hand sorting class. The flowsheet under consideration is for producing smaller particles than these gradings for particular markets. Saleable products taken from this arrangement, are separated into +1″; —1″ + ½”; — ½” +¼” and —1/8″ material which can be further treated for very fine filler materials for paint, roofing and lubricants.
The Mica Recycling Flowsheet
This flowsheet is designed for handling approximately 12½ tons per hour of feed which will contain approximately 25% mica. Elevators and conveyors have been added so that the plant can be installed on level ground. The equipment selected for the job is of common sizes for ease in maintenance and a minimum of repair parts to be carried in inventory. Also, the sizes are large so that surges in the grade of material handled can be readily absorbed in the system so that a minimum loss will be realized.
The fundamental principal involved in making the separation is the fact that with a comparatively slight compression, the mica minerals will not be broken, although the quartz, feldspar and allied minerals will be broken. This leaves the mica minerals intact so that they can be screened away from middlings and waste rock. This procedure is carried through the entire process, to produce a maximum amount of salable mica with a minimum loss.
Coarse ore is delivered by dump trucks to the ore bin. The ore is then fed onto a conveyor belt by means of a 24″ x 48″ F-44 Vibrating Feeder. The vibrating feeder will do a good job of giving a uniform feed to the belt, and it is considerably lower in initial cost than an apron type feeder. The feed rate is very easily and readily controlled by means of a rheostat which varies the intensity of the vibrations. One modification to a simple pan type vibrating feeder is a grizzly mounted on the end of the pan. This gives a more definite segregation of the material in that the fine material will drop onto the belt first and the coarse material, which passes over the grizzly, will then be dropped on top of the fine material, thus prolonging life of the belt.
The long conveyor belt is used merely to give elevation to the product before beginning the concentration process. The conveyor belt discharges onto a 24″ x 12′ Picking Belt moving at a slow speed (approximately 10′ per minute) where coarse high grade, and waste, are removed. The feed material is then dropped onto a stationary grizzly with the undersize by-passing directly to the bucket elevator. The grizzly has a 1½” opening and the plus 1½” material is then crushed in the 10″ x 20″ Type “H” Forced Jaw Crusher to -1½”.
The 10″ x 6″ Bucket Elevator discharges onto a 3′ x 6′ double deck Dillon Vibrating Screen equipped with a 1″ top screen and a 1/8″ opening lower screen. The plus material produces a coarse concentrate which goes directly to a bin. The -1″ + 1/8″material is further reduced in a 27″diameter x 14″ Type “M” Crushing Rolls, and the -1/8″ material is discharged onto a collector belt. Notice the collector belt for this —1/8″ material is common to all screens and delivers this product to a stockpile for further treatment.
The discharge from the crushing roll is then elevated in a 10″ x 6″ Belt and Bucket Elevator where it is passed over a 3′ x 6′ double deck Dillon Vibrating Screen equipped with a ½” opening screen cloth on the upper deck. The plus ½” material is a final product and is stored in a separate bin. The — ½” + 1/8″ material is further reduced in another 27″ diameter Type “M” Crushing Rolls and the — 1/8″ screened product is discharged onto the collector belt.
The discharge from the 27″ x 14″ Type “M” Crushing Rolls is then picked up by the third 10″ x 6″ belt and bucket elevator and the material then passes over a 3′ x 6′ double deck Dillon Vibrating Screen equipped with a ¼” opening screen cloth on the top deck and a 1/8″ opening lower deck. The plus ¼” product is a final concentrate and it is sent direct to a separate storage bin. The —¼” +1/8″ material is passed through a 24″ x 18″ hammermill and recirculated by means of the third bucket elevator over the Dillon Vibrating Screen. The —1/8″ material is then discharged onto the collector belt. The hammermill reduces the —¼” + 1/8″ material to all —1/8″ size since the interlocking minerals at this size did not indicate sufficient value to warrant separate treatment.
All of the -1/8″, material is stock piled for further treatment in which it will be reduced by special processes to the various grades of fineness required for the industry. Three concentrates are removed; plus 1″; minus 1″ plus ½”; and minus ½” plus ¼”. These are stored in separate bins for market so that blending of products so produced can readily be done as required by market specifications.
A more elaborate plant would salvage the -1/8″ mica by means of “Sub-A” Flotation or spiral concentrators. Mica responds readily to treatment by flotation even in the very fine sizes.
Various grinding methods are used to obtain the very fine ground mica products which range from – 200 mesh on down in fineness. The final specifications required by the final customer determines to a large extent the manner that the grinding will be done. In general, dry grinding will leave the bright sheen, whereas wet grinding tends to dull the luster of the mica particles.
Source:
This article is a reproduction of an excerpt of “In the Public Domain” documents held in 911Metallurgy Corp’s private library.