The value of an assay depends largely on the care with which a sample of the ore is selected. Sampling should be, as far as possible, automatic, and independent of the will or judgment of the assayer. The sampling of ore in place in mines is described in books on mining. The taking of running samples is referred to in the section on stamp mill practice.
Heaps of ore, placer deposits, and impounded tailings are sometimes sampled in the same way as vat of bin charges by driving-in iron pipes or cheese-taster samplers at regular intervals, and mixing the samples withdrawn in the pipes. A form of sampling iron suitable for very dry material is described by Richards. It consists of two iron tubes, each with nearly half its circumference cut away. One tube fits inside the other, and is fixed to a wooden handle by a T-piece, so that it can be rotated inside the outer tube. The lower part of the outer tube is not cut, and is sharpened at the end or drawn out to a point. The tubes are driven into the ore with their openings arranged as shown in the cross-section, a (Fig. 91), and the inner tube is then rotated, passing through the position b (Fig. 91), until it is filled with ore. It is then replaced in its original position, and both tubes withdrawn. The outer tube must also be clamped to a cross-handle, to facilitate its withdrawal.
When the ore to be sampled can be moved, it is reduced in bulk either by hand or by automatic machines, and is generally crushed finer between each successive reduction of bulk.
If the ore is in course of removal by shovelling, every second, fifth, or tenth shovelful may be set aside as a sample, or the whole heap may be piled up to form a perfect cone, each shovelful being thrown as nearly as possible on the exact apex of the cone, so that the ore runs down on all sides. The heap may be made into a new cone to ensure thorough mixing, or may be at once flattened into a circular cake, and divided into four quarters, along two diameters at right angles to each other. Two opposite quarters are removed and mixed, and the operation repeated if the ore is fine enough. Coning and quartering is usually preferred to the method of setting aside particular shovelfuls (see, however, Argall, op. cit. infra).
Automatic samplers give better results than hand sampling, and their working costs are smaller. They are divisible into two classes:
- those which continuously take a part of a moving stream of ore, and
- those which momentarily take the whole stream of ore at regular intervals of time.
The former class of machine is the cheaper, but is considered by Richards and Argall to be useless, “ because the values are never evenly distributed across the stream.” In many machines a narrow scoop passes steadily across the stream of ore at regular intervals of time, and this is considered to be equivalent to the method used in the machines of class (2). The Bridgman, M‘Dermott, Vezin, Collom, Brunton, Snyder, Johnson, and Foster- Coolidge samplers are all well known.
The Vezin sampler is one of the few machines that give accurate results, and is stated by Argall to be almost universally employed in Colorado. It consists of two sheet-steel truncated cones, b, c (Fig. 92), with their bases bolted together. The ore falling from a shoot, a, into a hopper, d, is carried outside the cone, c, and is delivered from the hopper through another shoot, e. A scoop, f, made of sheet-steel, with a sector-shaped opening above, is riveted or hooked on to the cone, b. The angle of the sector may subtend any desired portion of the circumference of a circle, such as one-tenth (36°), or one-sixteenth (22½°). Both cones and the scoop arc rotated at about 25 or 30 revolutions per minute by bevelled gearing, and when the scoop comes below the shoot, a, the whole stream of ore falls into the scoop, and is led into the interior of the cone, c, and thence to a separate truck or bucket. In this way a sample is taken about every two seconds. A Vezin sampler of about 3 feet in diameter, and requiring a fall of about 6 feet, is trifling in cost, and treats 30 or 40 tons an hour.
Argall recommends the following course of procedure in sampling telluride ores containing 10 or 15 ozs. per ton:—From 100 short tons crushed to 1 inch cubes, take 20 tons. Crush this to ¼ inch, and take 2 tons. Crush this to 8 mesh (= 1/16 inch), and reduce by “riffling” to 250 lbs. Dry and crush the sample to 30 mesh (= 1/60 inch), and riffle down to 15 lbs. Crush by a sample-grinder to 90-100 mesh, and riffle down to 1 lb. This is crushed on the buck-board to pass 120 mesh ( = 1/250 inch), and divided for assay. Poorer and less “spotty” ores may be sampled somewhat more simply, and without such fine preliminary crushing.
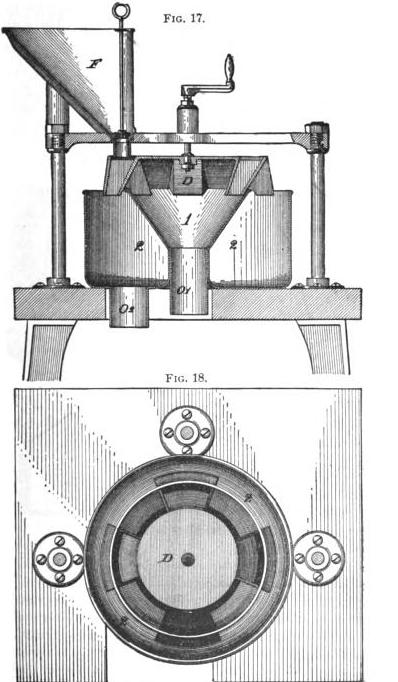
In the assay office the sample, however obtained, is further reduced in bulk by an automatic machine, similar in principle to the large samplers, such, for instance, as the Bridgman laboratory sampler, or by the implement known as the riffle or sampling tin. This consists of a series of troughs arranged side by side and fastened at equal distances from each other (the width of the spaces being equal to that of the troughs) by strips of metal soldered on to their ends. An even stream of ore being let fall from a shovel on to this sampler, half is retained in the troughs, while half passes through. Careful experiments have proved that each half is representative of the whole. A repetition of the process reduces the sample to any required extent. A sampler with troughs 1 inch wide is suitable for treating materials which include lumps of not more than ¼ to 1/3 inch in diameter. For finely ground materials a convenient width for the troughs is 3/8 inch.
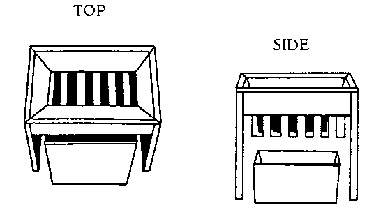
The split shovel is similar in principle to the riffle, and in the Jones sampler, instead of troughs and spaces, two sets of troughs are substituted sloping at a high angle in opposite directions. The troughs clear themselves, discharging half the ore at each end of the machine.
When the sample has been reduced to about 20 lbs. in weight it is crushed through a 20-mesh sieve, and from 1 to 5 lbs. selected for the assay sample. This sample is used for the estimation of moisture, and is then dried and finely crushed. Opinions differ as to the fineness of the sieve to be used. No one is in favour of a sieve coarser than 80-mesh, and 100-mesh is more common, but some assayers use a 200-mesh sieve. The author’s experience is that all ores require crushing to 100-mesh, and that finer crushing may be dispensed with in the case of simple ores; but that complex ores, such as tellurides, should be crushed as finely as possible.
The implements employed for crushing samples of ore are various. A small rock-breaker, with reciprocating jaws, similar to those used on the large scale, and worked by hand or steam power, is useful for breaking down large lumps, which otherwise may be broken by a hammer. For finer pulverisation a small pair of steel-faced high-speed rolls may be used if steam power is available. The sample-grinders, resembling coffee mills, sold by makers of mining machinery, are more widely used. Such machines are adopted at large smelting or sampling works, where great numbers of samples are crushed daily. In smaller works or offices the buck-board (Fig. 93) is most suitable. It is a smooth plate of iron about 2 feet square with a 1-inch rim surrounding it on two or three sides. On this a bucking hammer is worked—a heavy piece of iron 15 to 20 lbs. in weight, with a large smooth curved face and a handle 30 inches long. It is moved about on the iron plate (on which the ore is spread) with both hands, one holding the handle, the other pressing the head downwards, the curved face being below, while an oscillatory movement is imparted by the handle. The instrument is very effective if the ore is previously broken down to the size of coarse sand in a mortar. The pestle and mortar are of value in breaking down samples from the size of nuts to that of coarse sand. In grinding down siliceous material, so as to enable it to pass through a fine sieve, the pestle and mortar is far inferior to the buck-board.