Table of Contents
For evaporating moisture from concentrates or other products from plant operations, Rotary Dryers are designed and constructed for high efficiency and economy in fuel consumption. Whenever possible to apply heat direct to the material to be dried, Rotary Dryers of the Direct Heating Design are used. If it is not possible to apply heat direct to the material to be dried, Rotary Dryers of the Indirect Heating Design can be furnished so that the heated gases will not come in direct contact with the material.
Sizing a Rotary Dryer using a Capacity Table
Rotary Dryer is a simple, inexpensive unit for reducing the moisture content of flotation concentrates, as well as chemical and industrial products. Frequently the saving of shipping weight so effected will pay for the dryer in a few months. Difficulties from freezing while in transit are also eliminated. Many industrial projects are now using Dryers for control and production purposes on many materials.
Three main types of Rotary Dryers can be supplied. The direct heat unit is used when it is permissible for the drying gases to come in direct contact with the material being dried. Partition plates increase the heating surface. Drying may be by hot air or exhaust gases from other operations. If this drying gas has a deleterious effect on the product, then an indirect type of dryer can be supplied. A further derivation is the Tedrow Steam Dryer.
Rotary Dryer Capacity Table
ROTARY DRYERS, Direct-Heat Design
Size of Dryer |
Cap. Tons per 24 Hours |
Dimensions |
R.P.M. |
H.P. of Motor |
Shipping Weight Lbs. Motor Drive |
||
L | W | H | |||||
24″dx15’1 | 18 | 26’6″ | 3’8″ | 7’9″ | 7½ | 3 | 12,000 |
24″dx20’1 | 25 | 31‘6″ | 3’8″ | 8’2″ | 7½ | 3 | 13,000 |
36″dx20’1 | 55 | 33’0″ | 4’10” | 8’8″ | 5 | 5 | 14,400 |
36″dx30’1 | 85 | 43’0″ | 4’10” | 9’6″ | 5 | 5 | 17,000 |
48″dx30’1 | 150 | 44’0″ | 5’8″ | 10’0″ | 3½ | 7½ | 19,500 |
48″dx40’1 | 200 | 54’0″ | 5’8″ | 10’10” | 3½ | 7½ | 22,800 |
Capacity based on 10% moisture, wet weight, in material fed to dryer, and 3.26 pounds of moisture evaporated per hour for each cubic foot of the volume of the main cylinder.
ROTARY DRYERS, Indirect-Heat Design
Size of Dryer |
Cap. Tons per 24 Hours | Dimensions Outside Brickwork | R.P.M. | H.P. of Motor |
Ship. Wt. Lbs. Motor Drive Iron Work Only |
||
L | W | H | |||||
24″dx15’1 | 13 | 16’0″ | 11’9″ | 7’7″ | 7½ | 3 | 12,000 |
24″dx20’1 | 16 | 21’0″ | 11’9″ | 8’0″ | 7½ | 3 | 13,000 |
36″dx20’1 | 38 | 21’0″ | 12’9″ | 8’6″ | 5 | 5 | 14,400 |
36″dx30’1 | 55 | 31’0″ | 12’9″ | 9’4″ | 5 | 5 | 17,000 |
48″dx30’1 | 115 | 31’0″ | 13’9″ | 9’10” | 3½ | 7½ | 19,500 |
48″dx40’1 | 150 | 41’0″ | 13’9″ | 10’8″ | 3½ | 7½ | 22,800 |
Capacity based on 10% moisture, wet weight, in material fed to dryer, and 3.26 pounds of moisture evaporated per hour for each cubic foot of the volume of the main cylinder.
NOTE: The customer furnishes and erects the brickwork setting for the dryer in accordance with drawings furnished by Equipment Company.
ROTARY DRYERS, Tedrow Steam Design
Size |
Cap. Tons per 24 Hours |
Dimensions |
R.P.M. |
H.P. |
Approximate Ship. Wt. Lbs. |
|||||
Cyl. Dia. | L | W | H | |||||||
Belt | Motor | |||||||||
No. 1 | 8 | 18″ | 11’0″ | 4’8″ | 3’10” | 4 | 2 | 5100 | 5650 | |
No. 2 | 26 | 25″ | 15’0″ | 5’0″ | 4’4″ | 3 | 5 | 6350 | 7000 | |
No. 3 | 54 | 36″ | 19’6″ | 6’0″ | 5’6″ | 2½ | 7½ | 8450 | 9300 |
Capacity based on 10% moisture, wet weight, in material fed to dryer, and 3.26 pounds of moisture evaporated per hour for each cubic foot of the volume of the main cylinder.
Rotary Dryer Direct Heat and Indirect Heat Type -Capacity and Sizing Table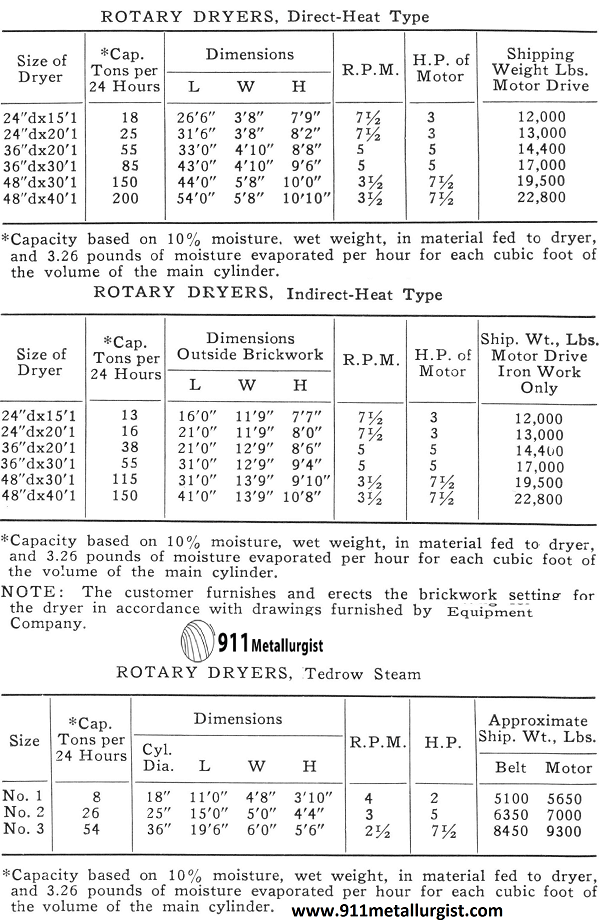
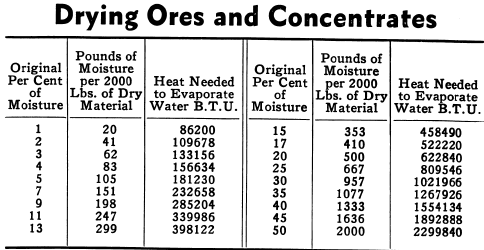
Rotary Dryer – Kiln
Of the different types of dryers that there are the most common is the ROTARY DRUM DRYER/Kiln, This type of drier is common not only in the mining industry but you will find them in fertilizer plants, Cement plants, and peat hogs to name but a few.
The theories behind these machines are very simple, heat an air space up, and then tumble the material to be dried through this space until it is dried. All though it sounds simple there are problems that have to be solved before the required results are met. But first, so you know what we are talking about lets go through the design of a drier.
First is the KILN, this provides the heat, The BURNER is inside this portion. The fuel for the burner is usually diesel although heavy crude oil could be used in some cases. To be able to generate enough heat to dry the concentrate air must be added by way of a BLOWER.
In front of the kiln is the point that the wet concentrate enters the drier. It is put into the revolving SHELL. The shell is on a slight incline. As the Concentrate is tumbled through the hot air mass of the drier it travels down this incline to the exit of the drier.
At this exit point the concentrate is either deposited straight into a storage area or taken to the storage area by a conveyor. It is also at this point that there is an EXHAUST HOOD. This provides a controlled escape passage for the fumes and water vapor that is generated by the concentrate drying. This is a very important function and the operator will have to be sure that it is open at all times. If it should become blocked the water vapor will not be able to escape. The concentrate will become wet and sticky which will result in the discharge plugging. The wet sticky concentrate will also lower efficiency level of the drier for an extended period of time.
This happens because inside the drier shell are what are termed FLIGHTS these are flat pieces of metal that are bolted onto the shell.
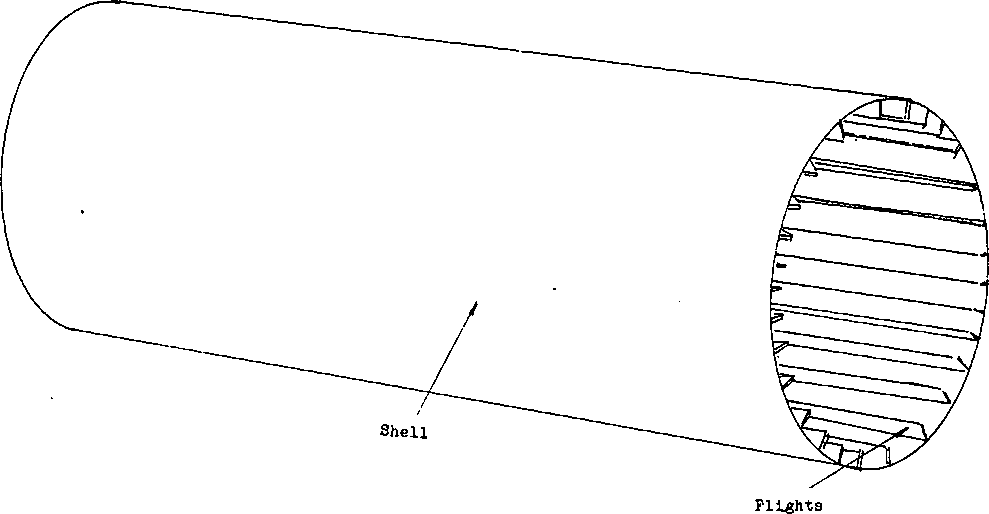
They are there to lift the concentrate up to the top of the shells rotation and drop the concentrate through the hot air. If the water vapor isn’t taken away, the concentrate becomes sticky from reabsorbing the water.
This sticky concentrate will fill the spaces between the flights.
The concentrate will not be lifted and dropped through the hot air. This results in a long term condition of poor performance even after the initial problem has been cured. These flights will remain buried in concentrate.
This removal of the water vapor is one of the functions of the blower. It assists the natural process of air movement as the hot air mass expands.
To prevent the buildup of concentrate on the flights there are often CHAINS attached to them. As the drier revolves the chains slap the flights preventing concentrate from building up on dryer’s walls.
Outside of the drier shell as well, we use hammers to knock the cake clean.
These have the same purpose as the chains. As the drier revolves, the hammers (formed by grinding balls) will fall against the side of the drier as it passes the top of the drier’s revolution.
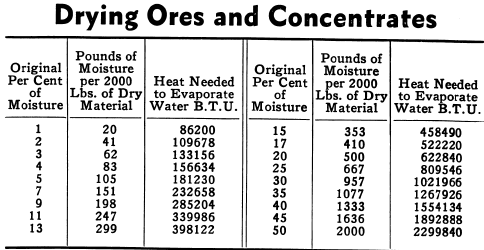
The drier shell is rotated separately from the stationary kiln section. To achieve the rotation a BULL GEAR is attached around the shell section. There are also two flat rings attached to the shell. These provide surfaces for support rollers to roll on. There is another problem that the inclined shell has, the incline causes the shell to want to slide in the direction of the incline. To prevent this additional rollers are attached to the last set of rollers.