Table of Contents
It sometimes falls to the lot of the assayer doing commercial work or working in a mining camp to retort the amalgam taken from the plates of a stamp mill and melt the resultant sponge of gold and silver into a bar, and assay the bar so the value of the product may be known.
Description of Process
Retorting consists in distilling off the quicksilver from the amalgam and is done in a cast-iron retort (Fig. 58), a vessel having a cover which can be fastened on so tightly that no fumes of mercury escape except by the vapor pipe which leads from the cover to a vessel containing water, where the fumes of quicksilver are condensed to a metallic state. The vapor pipe must either have a water jacket (Fig. 59) surrounding it, through which a small quantity of cold water is continuously passed during the operation, or, if that is not practicable, it can be wrapped with cloth and the cloth soaked with water to keep cool the pipe through which the quicksilver fumes are passing.
The open end of the vapor pipe must be much lower than where it emerges from the cover of the retort,
and its open end is sometimes submerged in water during the distilling operation but removed from water as soon as heat is taken from retort, otherwise water rushes back into retort and forms steam and is liable to explode. The joints between the retort and the cover should be luted or filled with a paste of moist wood ashes and common salt or moist bone ash, and the cover must be clamped firmly in place. Before putting the amalgam into the retort, either coat the inside of the retort with plumbago, common white chalk or line with paper. This prevents the remaining bullion from sticking to the retort. The retort should not be filled much over half full of amalgam, as room is required for the vaporized mercury. It is good practice to make the amalgam into several small balls, thus allowing the mercury to vaporize more rapidly.
Distillation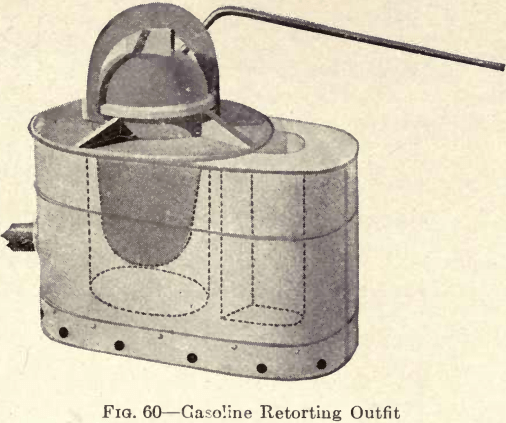
The distillation is performed at a very low temperature and heat applied very gradually. When the operation is finished the iron retort where exposed to the heat should not be more than at a low red heat. At the beginning when the heat is applied the air is driven out of the retort, which may
be seen by the bubbles arising through the water from the submerged end of the vapor pipe. Soon globules of quicksilver will begin to run out of the vapor pipe into the water. Tap the vapor pipe lightly from time to time to jar out the mercury that may be lodged or clinging to the sides of the pipe. When the iron retort is at a low red heat and no more globules of mercury come out of the vapor pipe, it is safe to assume that the operation is completed.
Modern Retorting Apparatus
Retorting is most conveniently done in a gasoline bullion furnace (Fig. 60). The furnace for this purpose should have a cast-iron cover (Fig. 61) which has at its center an opening like those in the top of a stove. The retort should be placed in this hole, supported by the edge of the hole which should touch the retort at a point about an inch below where the cover joins. The heat applied from a Cary gasoline burner is at all times under control, and may be increased or diminished by opening or closing the needle valve which supplies the gasoline to the burner.
When the mercury ceases to come over, shut off the burner, and when the furnace and retort have cooled off to some extent, remove the cover from the retort while the latter still remains in the iron lid of the furnace. If the retort leaks the operator should be careful not to inhale the fumes of the mercury, as
salivation might follow.
Melting Bullion
When the retort is cool remove the sponge of bullion, and melt it in a graphite crucible of sufficient size (Fig. 62).
Flux for Bullion
Borax glass makes the best flux for bullion melting, but it is rather expensive. Soda ash is also a good flux for this purpose. Should the bullion be base or contain much iron it can be fluxed with nitre to good advantage. Use enough flux so that when the bullion is poured into an ingot the top of the bullion will be covered with flux.
The bullion when thoroughly molten should be stirred with a graphite stirring stick (Fig. 63), which has previously been heated in the furnace so that it will not chill the molten bullion or cause it to splutter. The stirring stick is held with a pair of tongs and the
bullion thoroughly stirred just before pouring. It is necessary to stir the bullion so that the brick may be of uniform fineness throughout in order to obtain a fair sample of the whole when drilling into the bar.
Muffle and Furnace Maintenance
Cover the bottom of the muffle with bone ash to a depth of about an eighth of an inch. This is to absorb any lead that may spurt into the muffle. Use cupels of good height, as the lead soon passes through a shallow cupel and is absorbed by the floor of the muffle. This is destructive to the muffle, causing the unnecessary expense of replacing and the loss of time attendant thereto.
Heavy roasting dishes and scorifiers when set in the middle of a hot muffle soon cause the bottom to sag. Place the heavy loads as near the sides of the muffle as possible. Keep all the joints between the bricks of the furnace well luted, also lute with fire clay any and all checks that may open in the bricks. The life of the furnace may be long and useful, but its span of life is governed by the condition in which it is kept. An excellent luting for checks and cracks in the bricks may be made of good fire clay and wood ashes in the proportion of 10 parts clay, 1 part wood ashes and 1 part common salt. These parts are measured by the volume of the dry ingredients. The muffle should be luted in with good fire clay with plenty of long fibre asbestos. The long fibre asbestos prevents the clay from cracking and falling out of the cracks.
Should a large button be cupelled, the cupel containing the button should be set on top of another cupel to prevent the absorbed lead passing into the muffle.