In this paper on the recovery of mercury as sulphide, from the residues from the amalgamation and cyanide treatment of high-grade ores and concentrates, I will not discuss the many reactions, chemical and otherwise, that take place in the general process, but confine myself more particularly to the methods of recovering the mercury.
I submit charts of two amalgamation-barrel charges, Figs. 1 and 2, which are self-explanatory. The flow sheet of the high-grade and the mercury extraction plants is shown in Fig. 3.
In the amalgamation of high-grade silver ores and concentrates in strong cyanide solution, as practiced in the Cobalt district, considerable mercury is retained in the residues from the amalgamation process. The greater part of this mercury is in the form of mercuric sulphide, from 5 to 10 per cent, only of the total mercury content being in the metallic state.
Attempts to eliminate this loss in the amalgamation process were made, but all resulted in a low extraction of the silver in the ore, and attention was then directed to the recovery of the mercury from the residues.
The process developed at the Buffalo Mines, T. R. Jones, General Manager
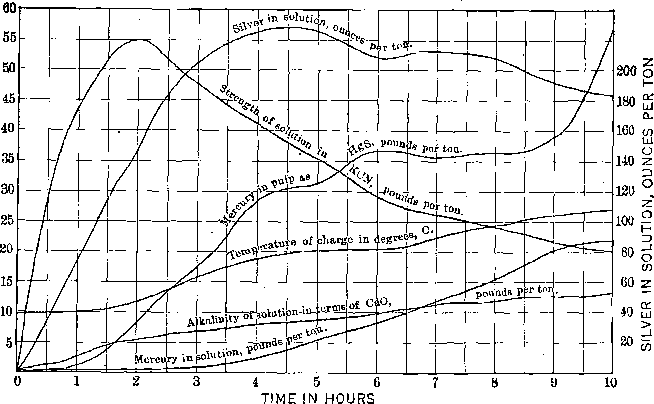
for this purpose consists briefly in leaching out the mercuric sulphide with a caustic, alkaline sulphide solution, then precipitating the mercury from solution with metallic aluminum. The equations for solution (1) and precipitation (2) are:
HgS + Na2S = HgS.Na2S (1)
3HgS.Na2S + 8NaOH + 2A1 = 3Hg + 6Na2S + 2NaAl02 + 4H20 (2)
Small-scale experiments showed that a complete extraction of the mercuric sulphide could be made by an 8 to 10 min. treatment of the residues with the alkaline sulphide solution. Advantage was taken of this fact in the commercial plant, by applying the solvent to the residue on the filter leaf, as no agitation of any sort was required.
The operation of the commercial plant is essentially as follows: The residue in the pregnant cyanide solution is caked on a Moore filter leaf of the usual construction and the cake washed free of silver solution with water. The basket is then lowered into the sodium sulphide
solution and this solution drawn through the cake until the effluent shows only a trace of mercury. Usually 1 ton of solution per ton of residue is sufficient. This mercuric sulphide solution is pumped to a precipitating tank and the mercury thrown down by adding granular aluminum to the agitated solution. Agitation is then stopped, the precipitate allowed to settle, and the clear solution decanted. The precipitate of mercury is then run into a small wash tank by sweeping it through a hole in the bottom, by means of a raking mechanism, pieces of old rubber belting being riveted to the bottom of the rakes. The precipitate is then washed with water by decantation and drawn off into a steam drying pan. After drying, the fluid mercury and the powdered metallic portion are separated by raking the latter off with a hoe. The fluid is strained through canvas and is ready to return to the circuit. The powdered material, containing approximately 75 per cent, mercury, is then retorted, and the mercury condensed in the usual manner.
The strength of the solvent used is kept up to 4 per cent, sodium sulphide and 1 per cent, sodium hydroxide. Weaker solutions can be used with equally good results, but the quantity of solution required was found to be directly proportional to the strength; that is, with a 4 per cent, sodium sulphide solution, 1 ton of solution would extract the mercuric sulphide from 1 ton of residue, but if a 2 per cent, solution were used, 2 tons would be required per ton of residue treated. The concentrated solution offers the advantage of less solution to handle and an economy of aluminum in the precipitation. The sodium sulphide used is the commercial salt costing $1.25 per cwt. in barrels f.o.b. cars Toronto.
The precipitant used is a waste product of aluminum casting foundries, containing 75 per cent, aluminum, the impurities consisting of varying proportions of copper, silica, wood, waste, grease, etc., the grease being burned off before using the aluminum. About ¼ lb. of this material is used per pound of mercury precipitated.
It was anticipated that the sodium aluminate would accumulate in the solution to such an extent that some special means would have to be taken to remove it. This, however, has not been the case. Some aluminum as the hydrate, falls with the mercury on precipitation, and some is removed during the process of leaching, presumably as calcium aluminate, which collects on the filter cake. This precipitation of the aluminum regenerates caustic soda so that the consumption of this chemical is reduced to 1/10 lb. per pound of mercury recovered, instead of ½ lb. as shown by the theoretical equation for precipitation. Sodium sulphide is also regenerated in precipitation, but there is also a mechanical loss of approximately 20 per cent, of the solution used in leaching, as no water is used to recover the retained sulphide.
From May, 1914, to March, 1915, 37,650 lb. of mercury have been recovered at a cost of approximately 13c. per pound for labor and chemicals.
The laboratory methods of determining the mercury in the different products of the process may be of interest. To determine the total mercury (both metallic and sulphide) 0.5 g. of the material is well mixed with cast-iron filings, free from grease, and placed in a hard-glass tube, sealed at one end, with a contraction at about 2 in. from the sealed end. The mercury is distilled off, by heating the bulb containing the charge, and condensed in the tube just beyond the contraction. After the distillation is complete, the contracted portion of the tube is heated, the bulb portion pulled off and the end of the tube sealed. The tube containing the condensed mercury is allowed to cool, filled one-half full of 0.1 per cent. KCN solution, and 10 to 15 100-mg. gold beads added. Each bead will amalgamate with about 1 mg. of mercury. The tube is shaken until all the mercury is amalgamated; the beads are transferred to a small porcelain cup, washed with water, dried with alcohol and weighed. After retorting off the mercury, they are again weighed. From 10 to 12 determinations can be made in one hour by this method and it is accurate enough for control of operations.
When it is necessary to know the proportionate amounts of mercury as metallic and sulphide two 2-g. samples are weighed out. One sample is digested with concentrated nitric acid and the other with a 10 percent, solution of sodium sulphide. The mercury in the residue from each is then determined by the method just given.
The strength of the sodium sulphide solution is determined by titrating against a standard zinc chloride solution, using sodium nitro prusside as an outside indicator.
The mercury produced by this process is of exceptional purity. A. R. Ledoux & Co. report that 0.25 oz. silver is the only impurity in determinable quantity.
Discussion:
D. B. Huntley, Oakland, Cal.—About 15 years ago it chanced to be my lot to cyanide some mill tailings, assaying about $5 per ton in gold and a few cents in silver. It was in southern Idaho, a desert region where costs are nearly as large as in central Nevada. We knew that we had a lot of tailings that had been amalgamated and contained about 1 lb. of quicksilver per ton. We knew that we would dissolve some of the quicksilver when we cyanided them with say 0.25 per cent, cyanide solution. We figured (optimistically) that the cyanide would dissolve all of the quicksilver, and we thought to capture all of that, 1 lb. per ton; and we figured out profits as partly gold, partly silver, and partly quicksilver from the recovery in working those tailings. Actually, however, we did this: We had a battery of three large, old-fashioned silver- mill retorts. We retorted our zinc-dust precipitate, recovering about ¼ lb. of quicksilver per ton treated. That was only a loss of 75 per cent, of what we originally had, but still it was profitable by virtue of the conditions. I mention it partly to call attention to the crude old way of doing it, and partly to call attention to how chemical methods for recovering quicksilver have developed in the last 15 years.
H. G. S. Anderson, San Francisco, Cal.—It may be of interest to mention, in reference to what the previous speaker has said concerning his experience in southern Idaho, that we tried for a while to precipitate silver from solution with zinc shavings, but we had five compartments in each box; after 30 min. there would be no precipitation in the first compartment at all; the mercury, precipitating before the silver, would cover the shavings in the second compartment in about ¾ hr., and in from 3 to 4 hr. there would be no precipitation taking place in the entire precipitation box. Then we turned to zinc dust, and zinc dust did not give us as clean a silver bullion as aluminum did, so finally, although the cost was a little higher, aluminum was accepted as the precipitant and the bullion was in much better condition and easier to smelt than it was either in the case of zinc shavings or of zinc dust.
Recovery of Mercury from Amalgamation Tailing, Buffalo Mines, Cobalt E. B. THORNHILL.