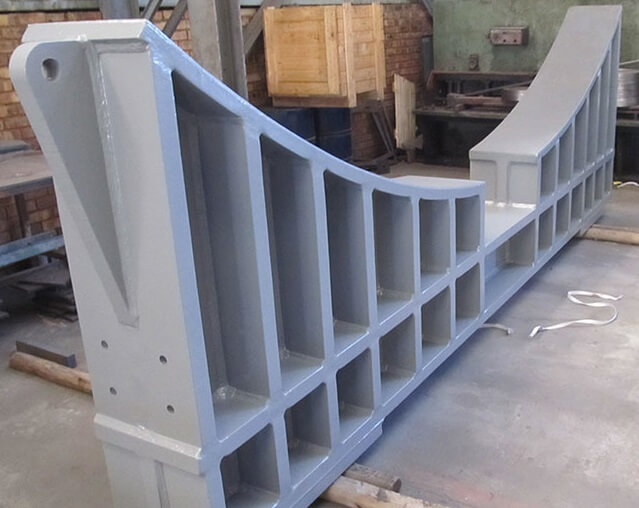
The mine is closed and now you need to know how to put the SAG or Large Ball Mill in care and maintenance does not have to be complicated to the point where you need bridge erection equipment for lifting a Mill (AG/SAG/Rod/Ball). You actually need to lift a car higher than a mill. All you need to do is jack the mill up about 1/2″. No need for a mobile crane for this job, all you need are heavy duty hydraulic jacks and support (lifting) cradles for this operation.
You get a jacking cradle that fits under each end of the shell near to the trunnions and then some big jacks.
You jack up the (emptied) mill and then drop some solid packers in place before letting the jacks back down.
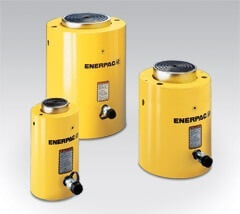
Enerpac are one manufacturer of large heavy-duty hydraulic jacks.
You can normally or rent those jacks from specialised companies. Sometimes the mine truck shop/mobile workshop have them on site too.
Typically 200 to 250 tonnes jacks are with electric hydropack to feed them. Then just set it all up and flick the switch to jack it up.
The mill only needs a few millimeter of lifting (6mm-20mm max).
- Do not jack directly on the shell or risk warping the mill.
- Cradles are positioned where the shell meets the mill ends.
- The mill needs to be raised only slightly so the cradles can be lowered and supported on shims (stack of steel plates) and the jacks are removed.
- Mill needs to be empty of media and preferably liners removed to minimize weight.
- Make sure the bearing caps are not bolted down.
ABOUT THE TRUNNION:
Remove all of the bolts as a precaution – no need to pull the bearing caps completely off. The mill needs to be jacked high enough to get the last shim in place so that when the mill is lowered onto the shims, it is no longer resting on the bearings.
If that amount of lift creates interference with the bearing cap, it could wreck the seal or damage the cap if it is bolted rigidly in place.Typically, the mill’s cradles would have been kept from the original installation and save you from buying new ones.
![]() |
![]() |
The cradles need to be lifted up to sit under the shell then jacks placed under the cradles. You sit the jacks on some big thick steel plate to dissipate the load a bit otherwise could punch through the concrete.
You will insert the jacks between the cradle and the shell and then if you lift the cradle up off the concrete plinths the same gap.
The concrete plinths are not normally for jacking off the mill, they are only there to keep the cradle out of the dirt on the ground.
You need to move cradles longitudinally, i.e: towards the feed or discharge end of the mill and still be relatively centred on the shell.
Alternatively if the plinths are engineered to take the weight you can use jacks like below as they are only 150mm to 250mm high.
In some cases (as above) it appears the floor is angled.
![]() |
![]() |
![]() |
![]() |
![]() |
![]() |
![]() |
![]() |
![]() |
![]() |
![]() |
![]() |
![]() |
![]() |
![]() |
![]() |
![]() |
![]() |
![]() |
![]() |
![]() |
![]() |
![]() |
![]() |
![]() |
![]() |
![]() |
![]() |
![]() |
![]() |
![]() |
![]() |
![]() |
![]() |
![]() |
![]() |
![]() |
![]() |
Thanks to Rob Taylor and Craig Lockhart.