Table of Contents
Disposal of the salt slag produced during the processing of aluminum dross and scrap is of particular interest to the secondary aluminum industry. Melting of these materials is carried out under a salt flux cover to dissolve the contaminants, mostly aluminum oxide, and to optimize the recovery of aluminum metal. Typically, dross and low-grade scrap are melted in rotary furnaces, using a sodium chloride flux with 2 to 5 pct cryolite. The salt slag generated ranges up to 35 pct of the melt charge in rotary furnaces. Higher quality scrap is melted in reverberatory furnaces, using a flux consisting of equal parts sodium chloride and potassium chloride with 2 to 5 pct cryolite. Dross from this type of furnace ranges up to 10 pct of the melt charge. As the flux becomes contaminated with aluminum oxide, it is removed and customarily disposed of in a landfill. However, because the soluble salts in the flux represent a potential source of pollution to surface and ground water supplies this practice is being discouraged.
Preliminary Bureau experiments indicated that although leaching the slag and evaporating the brine to recover the salt flux was technically feasible, the economics of such a method were not well defined. Therefore, as part of its mission to conserve mineral resources, the Federal Bureau of Mines undertook to generate the data required for an economic evaluation. This report presents the results of demonstration tests of a Bureau-developed hydrometallurgical process for recovering the components of the salt slag for reuse. Tests were conducted in a laboratory process research unit (PRU), of 100-pound-per-hour capacity. An economic evaluation of the process is projected to a commercial-scale operation.
Preliminary Experiments
As a basis for the design of the PRU, tests on slag leaching and brine evaporation were conducted on a laboratory scale. These tests indicated that the slag could be effectively separated into a coarse aluminum-rich fraction, fine aluminum oxide, and salt flux for recycling.
To facilitate leaching and handling, the incoming salt slags were crushed and sized to minus 0.5 inch by the processor. The slags processed in the PRU were generated in both rotary and reverberatory furnaces. Figure 1 shows the general appearance of the slag as received; table 1 shows the range of compositions.
To study the effect of water-to-slag ratios and stirring time on salt dissolution, several 200-gram samples of slag were leached at room temperature. After leaching, the slurry was filtered in a vacuum-type Buchner funnel, and the concentrated brine was removed and evaporated (table 2). After drying, the residue was screened at 28 mesh to separate an aluminum-rich oversize fraction. To remove residual salts, the aluminum oxide undersize fraction was releached, and then filtered, rinsed, and dried. The dilute rinse solution from this step was used to leach the next slag sample. Composition ranges of the fractions for several tests are summerized in table 3.
Note.— Releaching the undersize removed approximately 85 pct of the remaining salts, reducing their level to 0.3 to 1.1 wt-pct chlorides.
Material that is mostly aluminum oxide could be used by the steel industry as a hot-topping compound if the chloride content were less than 1 pct and the metallic aluminum content were 2 to 5 pct. The oversize fraction contained sufficient metal to be recycled, while the salt content of the undersize was reduced to acceptable levels by releaching. These laboratory test results were reported in greater detail by Caldwell, Hogan, and Elkins, and on that basis, it was decided to build a PRU capable of leaching 100 pounds of slag per hour in 50-pound batches.
Principles of Operation
The process is hydrometallurgical and consists of four stages: (1) leaching, (2) screening, (3) slurry filtration, and (4) evaporation. Figure 2 is the general flowsheet for the PRU.
Leaching
The leaching section of the PRU was operated on a batch basis with slags obtained from commercial sources. Fifty pounds of slag were charged to a polyethylene leaching vessel and leached, at room temperature, with a dilute salt solution from a prior rinsing step. The amount of solution used was pre-determined by the amount of salt in the slag. Volume-to-weight ratios were 10 to 11 gallons of solution per 50 pounds of slag.
A concentrated brine solution of sodium and potassium chloride contains approximately 24 to 26 wt-pct salts at room temperature. The volume of leach water used was adjusted to yield a solution of just under 24 wt-pct salts to insure rapid dissolution and to keep all salts in solution during subsequent processing. Figure 3 shows the average concentration versus time results for tests run to determine rate of dissolution. These data demonstrated that a leach time of approximately 30 minutes was required to reach the desired concentration.
Screening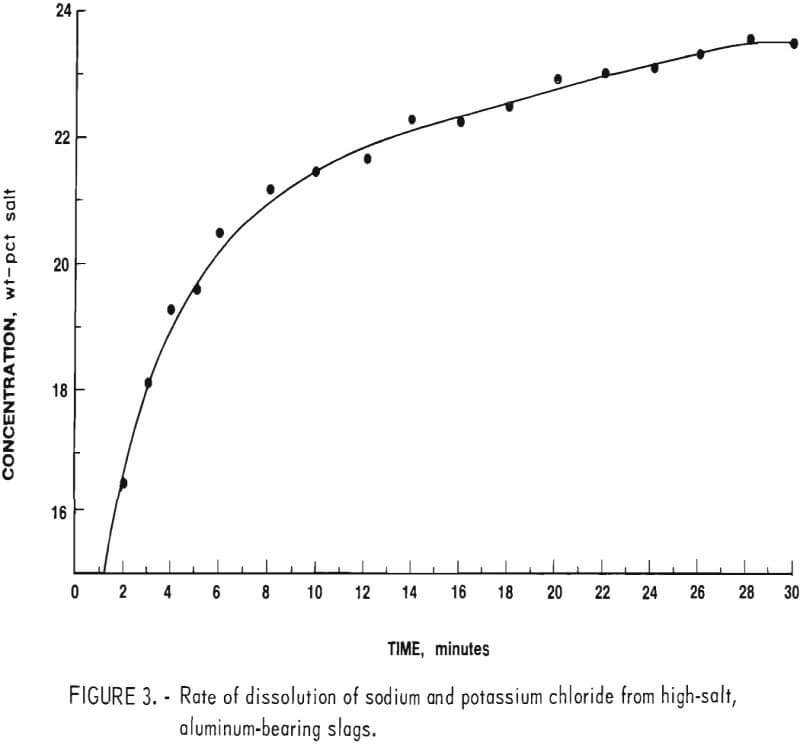
During leaching, relatively small particles of metallic aluminum and aluminum oxide were liberated. Because the aluminum particles were generally larger than the oxides, the leached slurry was gravity fed to a vibrating screen to separate an aluminum-rich fraction. The metallic contents of these oversize fractions, screened at 28 mesh as in the preliminary tests, were below 30 wt-pct owing to entrained oxide particles. Subsequent tests showed a 14-mesh screen to be the optimum size for use with the vibrating screen.
Slurry Filtration
Aluminum oxide in the minus 14-mesh screen undersize was separated from the concentrated brine by a vacuum pan filter, with a 10-square-foot filtering area. The oxide fraction formed a spongy cake, ¼-to-½-inch-thick, with a dry, flaky surface. The resulting clear brine solution was stored for later evaporation. After filtration, a volume of fresh water equivalent to that used for leaching was added to the aluminum-rich fraction on the vibrating screen to rinse off remaining fines. This solution then passed to the pan filter where the cake was flood washed, under vacuum, to remove residual salts. This produced a dilute brine solution of approximately 3 to 6 wt-pct salt used to leach the next batch of slag. The filter cake contained 20 to 25 wt-pct moisture and less than 1 wt-pct salt. Figure 4 shows the leaching (upper right corner), screening (right center), and filtering (lower right corner) sections of the PRU.
Evaporation
The submerged combustion evaporator, used to vaporize approximately 350 pounds of water per hour from the brine at 95° C, consisted of a 100-gallon fiberglass tank with a conical bottom. A propane-fired burner, rated at 400,000 Btu per hour, was suspended vertically inside a downcomer, which in turn was immersed below the surface of the brine. Evaporator steam was exhausted to the atmosphere. Figure 5 is a diagram of the submerged combustion evaporator.
After the feed solution was concentrated by evaporation so that salt began to crystallize, the salt slurry was pumped from the evaporator to a settling tank. An equal volume of clear supernantant solution was drawn off the top of the settling tank and recycled back to the evaporator to maintain the liquid level of the evaporator. After settling, the salt crystals were dewatered in a vacuum filter pan with 4- square-foot filtering area.
The mother liquor collected in a filtrate receiver and was returned to the settling tank; 100 to 125 pounds of salt per hour were recovered.
Products
Three separate products were obtained from this process: an aluminum-rich fraction (plus 14 mesh), a fine aluminum-oxide fraction (minus 14-mesh), and a salt mixture suitable for reuse as a flux (fig. 6).
Composition of the aluminum-rich fraction is shown in table 4. As with the small-scale tests , this material contained sufficient aluminum to be recycled to the dross treatment furnace for aluminum recovery.
Composition of the aluminum oxide product is shown in table 5. The secondary aluminum industry has indicated that this material has potential use as a raw material for the cement industry. Another possible use for this fraction is as a hot-topping compound in the steel industry. The market potential in both cases may be limited, however, because relatively inexpensive raw materials for these purposes are currently available.
Table 6 shows the composition range for recovered salt flux. The flux consists of approximately 50 wt-pct each of sodium and potassium chloride, and trace amounts of aluminum, copper, iron, calcium, and magnesium. This salt flux, with the addition of a small amount of cryolite (2 to 5 pct) is suitable for reuse in the dross treatment furnace.
Product distribution as a pct of the incoming slag is shown in table 7. The recyclable fluxing salts and metallic aluminum fractions represent up to 25 and 65 pct, respectively, of the incoming slag. Sale or reuse of these fractions accounts for the major source of revenue generated by this process.
Process Evaluation
To generate data for an economic evaluation, the critical operating parameters were determined. Average values of data such as specific gravity, bulk density, angle of repose, moisture content, and percent of charge for all solids and solutions are tabulated in tables A-1 and A-2 in the appendix. Compositions of the various process streams at equilibrium were required to evaluate the evaporation section. Samples of the salt slurry pumped from the evaporator to the settling tank, the clear supernatant solution recycled from the settling tank to the evaporator, and the mother liquor obtained by filtering the salt product and the salt cake were taken at 30-minute intervals throughout each evaporation test. Temperatures and specific gravities of these solutions were measured at the time of sampling. These samples were subsequently analyzed for NaCl and KCl. A saturated solution at 95° C should contain 17.1 wt-pct NaCl and 21 wt-pct KCl. Figure 7 shows the approach to equilibrium for this system, using the settling tank samples.
During the experimental investigations, the slag was crushed to minus 0.5 inch to facilitate leaching. In the process evaluation, this crushing step was eliminated by replacing the leach tank with a drum capable of leaching large-size slag. This is similar to the horizontal leach drum arrangement described by Newell Dunford Engineering Ltd. It was assumed that the slag would be cast in small bars no longer than 12 inches and be fed directly to the leach drums. Casting such small bars or ingots is common practice in various industries and is not expected to increase the operating cost at the secondary smelter.
Data used in this evaluation for the preparation of the material balance are based on results from the 100-pound-per-hour PRU. Commercially available equipment was used in the full-scale plant designed for the process evaluation. Cost data are from published sources updated by the use of inflation indexes. It is assumed that the plant is an addition to an existing aluminum dross treatment plant. Figure 8 shows the flowsheet used for this process evaluation.
Capital Costs
This is a capital cost estimate of the general type called a “study estimate” by Weaver and Bauman. It was prepared from a flowsheet and a minimum of equipment data and can be expected to be within 30 pct of the actual cost. Capital cost estimates are shown in table 8. The fixed-capital cost on a fourth-quarter 1977 basis (Marshall and Swift index of 518.4) for processing 100 tons per day of salt slag is $3,274,900. The plant, divided into three sections, is designed to operate three shifts, 7 days per week, 330 days per year. Although statistics are not available on the quantity or distribution of salt slag in the United States, only a few secondary aluminum companies would be able to support a plant this size. In a study of the secondary aluminum industry in the United States, Siebert shows that six companies produce approximately 60 pct of the secondary aluminum. Based on 1977 production of almost 800,000 tons, these companies would thus account for approximately 480,000 tons. The amount of the slag produced can be crudely estimated by using the estimated flux consumption of 20 pct of the metal weight treated and assuming an average of 50 pct salt in the slag (table 1). The average salt slag generated for each of the six largest companies is thus estimated to be approximately 32,000 tons per year. For the rest of the industry, central processing facilities supported by two or more plants would be required to support the size plant projected in this economic evaluation.
Capacity-cost data of the type presented by Bauman, Mills, and Peters and Timmerhaus are used as the principle sources of equipment costs. The costs of the major items of equipment and their accessories are tabulated for each section in the appendix. In developing the plant capital costs, corrosion-resistant materials of construction were used where appropriate.
Because the proposed process is designed as a plant addition, the costs of plant facilites and plant utilities are estimated as 2 to 4 pct each, rather than the conventional 10 to 12 pct.
Working capital is defined as the funds in addition to fixed capital, land investment, and startup costs that must be provided to operate the plant. Working capital, also shown in table 8, is estimated from raw material and supplies inventory (cost of raw materials and operating supplies for 30 days), product and inprocess inventory (total operating cost for 30 days), accounts receivable (total operating cost for 30 days), and available cash (direct expenses for 30 days). Land investment and startup costs are not included in this estimate.
Salt Slags Processing Operating Costs
The estimated annual operating cost for a plant capable of processing 100 tons per day of salt slag is $1,368,700, as shown in table 9. This corresponds to a cost of $41.48 per ton of slag processed.
The estimated operating costs are based on an average 330 days of operation per year over the life of the plant. This allows 35 days downtime per year for inspection, maintenance, and unscheduled interruptions. The costs for this downtime are included in the figures shown in table 9. The operating costs are divided into direct, indirect, and fixed costs.
Direct costs include raw materials, utilities, direct labor, plant maintenance, payroll overhead, and operating supplies. The raw material costs do not include transportation costs because the plant location is not considered. Raw material and utility requirements per ton of salt slag are shown in table A-3. The direct labor cost is estimated on the cost of operating the plant 24 hours per day, 7 days a week, and staffing it with three workers per shift.
Plant maintenance is separately estimated for each piece of equipment, the buildings, electrical systems, piping, plant utility distribution systems, and plant facilities. Payroll overhead includes vacation, sick leave, social security, and fringe benefits.
The indirect costs include the expenses of control laboratories, accounting, plant protection and safety, plant adminstration, marketing, and company overhead. Research and overall company administrative costs outside the plant are not included.
Fixed costs include the cost of taxes (excluding income taxes), insurance, and depreciation. Depreciation is based on a straightline, 11-year period that includes debt retirement.
Credit for reduced slag disposal costs is not included in the operating cost.
Profitability
Because of the variation in market values with both time and location, each potential process user must develop his or her own set of product values. Figure 9 correlates the interest rate of return on investment after taxes (assumed 50 pct tax rate) with the net value of products.
Table 10 illustrates the effect of product value on the process economics. The assumed value of each of the products and the estimated product value per ton of slag are given. No credit is included for a reduction in disposal cost, but each potential process user should consider this cost saving when assessing the economic potential. From the assumed values, an interest rate of return after taxes of about 9 pct is indicated.
Salt Slag Processing Problems
During this research, several problems were encountered and the modifications or procedural changes employed to alleviate them are described below.
Distinct odors were detected during the operation of the leaching section. Gas samples were taken from the leach tank, the filter pan, and the drying oven and analyzed at the Pittsburgh Energy Research Center of the Department of Energy. The results of these analyses are listed in table 11.
The sample identification letters L, F, and 0 correspond to the leach tank, the filter pan, the drying oven, respectively. While the odors seemed to consist mainly of HgS and NH3, these gases along with CO, C2H2, and other hydrocarbons were below the 0.1 vol-pct detection limit of the gas chromatograph and mass spectrometer used. These data indicate that no special pollution control equipment is needed to control these gases , but adequate ventilation should be provided to prevent the accumulation of the trace amounts of H2, present.
It was also observed during leaching that some slag particles did not dissolve completely. These insoluble nuggets, which are mostly aluminum oxide, reported with the aluminum-rich fraction and lowered the metallic content to 45 wt-pct. Rod milling before leaching, however, produced metallic contents ranging from 55 to 65 wt-pct after screening. Leaching combined with some form of milling is more efficient than leaching in a stirred vessel.
Metallic contents of 70 to 85 wt-pct have been reported using a combination leaching-milling system.
Salt plugging problems in the gas outlet of the submerged combustion evaporator caused unstable burner operation and premature shutdown. On several occasions, the downcomer assembly of the evaporator was dismantled for manufacturer-specified design modifications. Figure 10 shows the details of the original configuration and several modifications. The salt-bridging problem appeared to be related to the following: (1) The back pressure plate was too hot, and the solution flash evaporated on its surface, (2) the supports for the back pressure plate were serving as nucleation sites for salt crystallization, and (3) the solution in the vicinity of the gas outlet was becoming supersaturated.
By increasing the distance between the gas dispersion nozzle and the back pressure plate from one-half to 1 inch, salt bridging across the gap was minimized. At the same time the thickness of the plate was increased from one-eighth to one-half inch. The inlet feedline was then piped through the center of the plate and served as its support (fig. 10D). The increased mass and the cool dilute feed solution discharged over the surface eliminated the salt-bridging problem.
Other problems encountered during operation of the evaporation section of the PRU included:
- Plugging of inlets to the centrifugal pumps when pellet-sized salt crystals became lodged in the pump’s impeller.
- Abrasion and corrosion due to accumulation of salt crystals between the pump housing and the impeller and shaft sleeve.
- a gradual buildup of salt deposits on the inner walls of vacuum lines which eventually restricted the flow and prevented filtration.
Although solutions to these problems were not thoroughly investigated, a partial solution may be periodic flushing with fresh water. Some carryover of salt occurred with the steam exhausted directly to the atmosphere. Although no absolute determination of the quantity was made, a sample of condensate from the exhaust contained less than 1 wt-pct salt.
Aluminum Dross Furnace Summary
The secondary aluminum industry annually disposes of large tonnages of salt slag produced in aluminum dross treatment furnaces, thus wasting valuable mineral resources and creating environmentally unacceptable conditions. An alternative exists by which the constituents of the slag can be recovered for recycling or sale and any residual waste can be safely disposed of, through the leaching and evaporation technique described in this report.
The estimated fixed-capital cost of a plant designed to process 100 tons per day of salt slag is about $3,300,000 based on fourth-quarter 1977 costs (Marshall and Swift index of 518.4). The operating cost for this plant is estimated to be about $41 per ton of slag processed. Credit for reduced slag disposal costs is not included in the operating cost. To obtain a 10-pct return on investment after taxes, the combined value of the products must be $55 per ton of slag processed.
The Federal Bureau of Mines has developed a hydrometallurgical method to recover aluminum, aluminum oxide, and fluxing salts from aluminum salt slags. The slag is leached with water at room temperature to produce a saturated brine slurry. Screening of the slurry yields an aluminum-rich fraction that can be returned to the dross furnace. The remaining slurry is vacuum filtered, yielding a clear brine solution and an aluminum oxide filter cake. Evaporation of the clear filtrate produces a high-purity fluxing salt for reuse in the dross furnace. Over 80 pct of the metallic aluminum is recovered in the aluminum-rich oversize fraction, while essentially all the fluxing salts are recovered by evaporation. This report contains the final results of an investigation on a process research unit scale, an economic evaluation of the method, and recommendations to further improve the process.