Table of Contents
Specific placer mining equipment is needed for each of the methods which can be classified according to the several methods of excavating and transporting the gravel, or they may be designated to correspond with the various ways of saving the gold. The actual moving of the gravel from place is always the principal concern of the miner, and often the gold-saving is entirely incidental to the working of the deposit. The following classification, therefore, seems the most logical and is the one generally used by placer miners:
- Hand-shoveling;
- ground-sluicing;
- hydraulicking;
- excavating by teams or power equipment;
- dredging;
- drift-mining.
Combinations of methods 1, 2, 3, and 4 may be used, and one method may graduate into another. The methods may be defined as follows:
Hand-shoveling.- Hand-shoveling comprises picking and shoveling surface-placer gravels and washing the material excavated to recover the valuable minerals. The gravel may be washed at the “diggings” or transported by wheelbarrows, pack animals, carts, or trucks to the nearest available water. The general method of excavating varies little, but it may be subdivided according to the method of washing the gravel: (a) Panning; (b) rocking; (c) use of long torn; (d) shoveling into boxes (sluicing); and (e) dry washing.
Ground-sluicing.- Ground-sluicing consists of moving and washing gravel by water not under a hydraulic head. The action of the water usually is assisted by picking. Boulders may be removed by hand of by derricks. A minor part of the water under relatively low pressure may be used to assist in cutting the bank.
Hydraulicking.- This method of mining utilizes water under pressure from a nozzle for cutting the gravel and sweeping it into sluice boxes, through which it passes to a suitable dumping ground. Additional water not under pressure generally is used to assist in moving the washed material through the sluice boxes.
Excavating by teams or power equipment.- This heading includes mining by teams and scrapers, power scrapers, power shovels, and drag-line excavators but not dredges. The gold may be washed in standard sluice boxes or in more complicated power-driven screening and washing plants.
Dredging.- Dredging properly is confined to mining placer deposits by excavating and washing machinery mounted on boats. The so-called “land dredges” as well as floating washing plants fed by separate dry-land excavators are included under the previous method. The only type of gold dredge operating successfully in this country is the bucket type, which excavates by means of an endless chain of buckets, screens and washes the gravel, recovers the gold in sluices, and discharges the waste material into the water behind the boat.
Drift-mining.- Drift-mining consists of working buried strata of gold-bearing gravels by underground methods. The gravels are mined in much the same manner as flat lode deposits; the excavated material is taken to the surface and washed in sluice boxes or treated in other gold-saving devices. In some instances the milling practice resembles that used for extracting gold from lode ores.
Placer Mining Equipment for Sale
Selecting Placer Mining Equipment & Methods
The method that involves the lowest total cost is preferable for mining a given deposit. The method chosen, however, must be compatible with existing conditions; frequently only a relatively high-cost method will be practicable. Usually natural conditions restrict the selection of a method, The most important natural factors are the quantity and pressure of water available; the slope or grade of surface and bedrock; the depth, extent, and value per yard of the deposit the character of gravel and bedrock; and the thickness of the overburden.
For profitable exploitation of a mine the gold recovered must be of greater value than the cost of mining it. Although in the past extremely rich placer ground has been found and worked, present known surface placer deposits are of relatively low grade. For profitable operation, relatively large tonnages must be handled per man-shift; too much stress cannot be laid upon this item. All phases of the mining must be correlated, and delays must be reduced to a minimum. Complications in any part of the set-up are to be avoided whenever possible in order that no “bottle necks” may exist. The mine and plant must be so designed and laid out that operations can be maintained at full capacity throughout the season, especially where power excavators or mechanical washing plants are used. Often the difference between expected capacity and actual capacity has been considerable and has meant the difference between profit and loss.
Placer Mining Equipment for Sale BC
Deciding to invest in, buying and mobilise small-scale Gold Placer Mining Equipment BC requires professional, experienced evaluation. The essential criteria should be examined at the outset to see if the given parameters of size and tenor fit. Second, no final decision to mobilize the placer mining equipment should be made until the property has been competently evaluated. The selection of proper equipment and seeking professional help in running the operation, must be the next priorities if the investor/mining company is to make a profit in this scale of mining business.
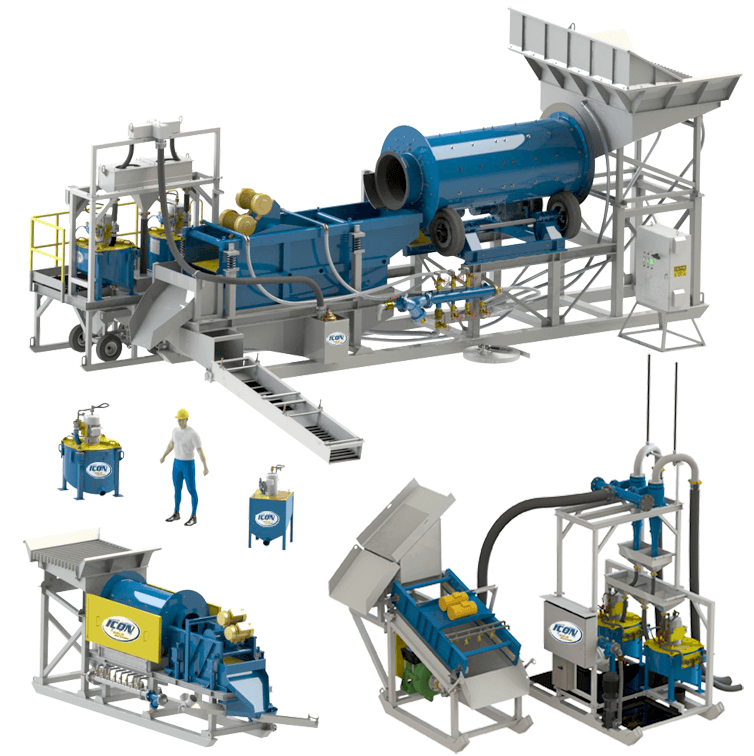
There has been a tendency to use lower cost equipment in small scale placer gold washing/processing plants with little regard -for its ability to recover the majority of gold. This includes using flat shaking screens for classification and riffles for concentration. Few have knowledge of amalgamation and thus will not have a continuous system for recovery.
The history of placer gold recovery systems shows a slow development of technology until the bucket ladder mining dredge was combined with a processing plant as a single system. While mineral jigs were being actively developed for other minerals in the 1880’s, no application was made for placer gold on a dredge until about 1914, in California. Until that time and for some years after, only riffles were used and records have shown that as much as 4071 of the gold was lost to tailings. Adding jigs to the circuit recovered more and by the mid 1930’s our company and a small dredge operator in Idaho, took the lead and replaced riffles with jigs on our dredges. Today, gold jigs have been replaced by high gravity gold centrifugal concentrators like those shown herein.
In BC, the solution to environmental problems with small scale placer gold mining, is to adopt more modern methods using gravity concentrators along with recirculation of processing water. The Placer Gold Mining Equipment described here can offer a step forward in meeting those goals and to improved disposal reclamation methods.
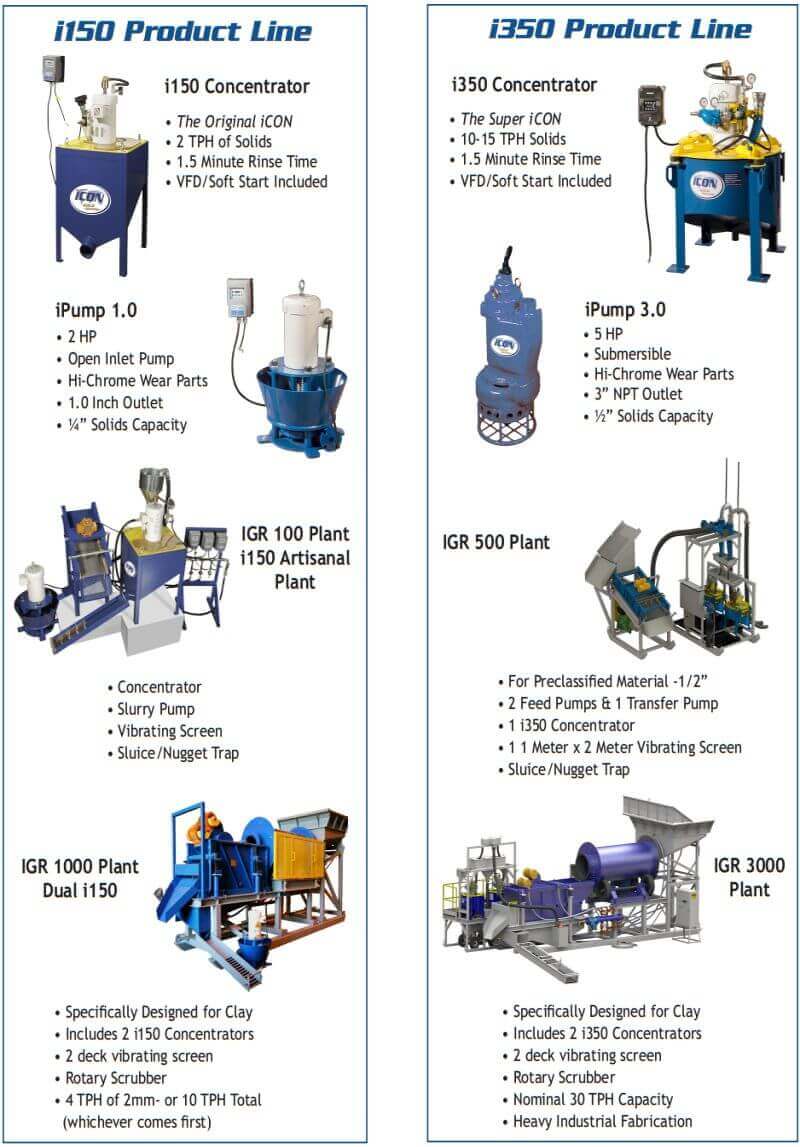
Hand-Shoveling
The first placer mining in the West was done by hand methods. As the rich surface deposits became exhausted other methods were substituted. Under normal economic conditions the hand-shoveling method is applied mainly to deposits that are too small to justify the capital expenditure necessary for working them by other methods. When work is scarce, however, any available gravel that will give a man a bare living may be worked in this manner. Because very little capital is required, men of small means can mine on their own account by hand-shoveling methods; in times of general unemployment, many such men go into the placer fields and search for and work surface gravels. This type of mining commonly is called “sniping.”
During the summer of 1932 thousands of men, most of them inexperienced, were mining in the placer districts of the West by hand-shoveling methods. They seldom earned a “going wage” but usually got enough gold to buy food. The average earnings of experienced men were estimated to be less than $1 per day and of experienced and inexperienced together less than $0.50. Occasionally a rich spot left by oldtimers would be found and as much as $100 might be cleaned up in a few days. These rare experiences, however, were offset by many days spent searching for a place to work or by wasted effort in digging to bedrock only to find it already cleaned or barren. During the autumn of 1931 many old bars in the rivers of the Pacific coast were exposed for the first time in years on account of the extremely low water of that season. Many snipers worked profitably on these bars until the fall rains raised the water level.
Snipers look mainly for unworked ground in or around old workings, or they extend old workings that have been discontinued as being unprofitable. They reclean disintegrated bedrock in old workings or clean out crevices in bedrock in river channels. They work old bars in the rivers where, reconcentration may have occurred since the early days of placering. Most of the ground worked by snipers, however, is ground that has been left by oldtimers as being unprofitable.
In dry sections of the country old channels, dry creek beds, or other gold-bearing deposits are worked, and the gravels are cleaned with dry washers.
Most of the ground in the Western States known to contain placer deposits is owned privately or held under mining locations. A newcomer into a field generally has to obtain permission from the proprietor of the land before he can begin placer mining. Sometimes a royalty is charged; at other times hand mining is permitted free, the owners of the gravel doubtless considering that the prospecting value of such work equals the small amount of gold taken from the ground.
The water of most western streams has been appropriated for irrigation or power purposes., Placer miners should consider the previous rights of others in a stream before diverting any water for placer mining. The antidebris law of California prohibits uncontrolled discharge of placer tailings into any tributaries of the Sacramento River.
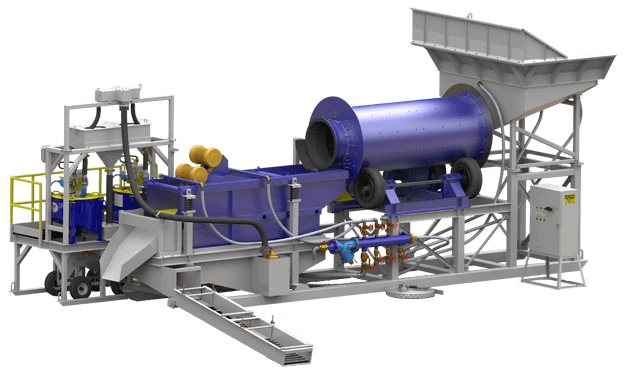
Gold Panning
Panning is both the simplest and most laborious method of washing gold from placer gravel. With a little experience almost any one can recover most of the gold in a pan of ordinary placer dirt; an experienced man can wash about 10 pans per hour. As a man can dig gravel with a pick and shovel many times faster than he can pan it only the highest-grade gravel is washed. The top dirt usually is thrown aside, and a few inches of gravel on bedrock or material scraped from crevices is panned.
The standard gold pan used in the Western States is made of stiff sheet iron; it is 16 inches in diameter at the top and 2½ inches deep. The rim is flared outward at an angle of about 50° from the vertical. Smaller pans are used for testing. Frying pans or other cooking utensils may also be used for washing out gold. Before any kind of a vessel is used for panning it should be cleaned thoroughly; all grease should be burned out. New pans generally are greasy and should be heated over a fire until all grease is burned off. A rusty pan if clean can be used satisfactorily; the roughness due to the pitting of the rust maybe of assistance in holding back the gold.
The pan usually is filled even with the top, or slightly rounded, depending somewhat upon the nature of the material being washed and the personal preference of the panner; it is then submerged in the water. Still water 6 inches to 1 foot deep is best. While under water the contents of the pan are kneaded with both hands until all clay is dissolved, and lumps of dirt are thoroughly broken. The stones and pebbles are picked out. Then the pan is held flat and shaken under water to permit the gold to settle to the bottom. The pan is then tilted and raised quickly so that some of the lighter top material is washed off. This operation is repeated, occasionally shaking the pan under water or with water in it until only the gold and the heavy minerals are left; this material concentrates at the edge of the bottom of the pan. Care must be taken that none of the gold climbs to the edge of the pan or gets on top of the dirt.
Nuggets and coarse colors can now be picked out readily. Cleaning the black sand from the finer gold is more difficult but can be carried nearly or entirely to completion by careful manipulation of the pan as described above, always watching carefully to see that none of, the colors are climbing toward the edge. This part of the operation usually is done over another pan or in a tub so that if any gold is lost it can be recovered by repanning.
The concentrates can be dried and the black sands removed by a magnet or by gentle blowing on a smooth flat surface. If there is an excessive quantity of black sand the gold usually is amalgamated by putting about a teaspoonful of mercury in the pan. In sampling work; great care is necessary that no fine colors are lost, but in mining by panning the extra time needed to make sure that no fine colors escape probably would not be justified. The loss of 50 or 100 fine colors in a day might not amount to more than 1 cent.
A standard 16-inch pan level full of dry bank gravel contains, on an average, 22 pounds. The quantity will vary with the moisture content and nature of the gravel. By allowing 3,300 pounds to the cubic yard (in place), 150 pans, would be equivalent to 1 cubic yard. The senior author has been accustomed to using this factor in sampling placer deposits. At 3,600 pounds to the cubic yard and 22 pounds to the pan, 164 pans would be required to wash a cubic yard of gravel. At 10 pans per hour a man could pan about ½ cubic yard in a day. With exceptionally clean gravel a man will sometimes pan as much as a cubic yard in a day.
Rocker Box
More gravel can be handled, per man-day by rocking, or cradling as it is sometimes-called, than by panning. Moreover, the manual labor of washing a cubic yard is less. The same method of excavating the gravel is used whether it is panned or rocked. The rocker like the pan, is used extensively not only in small-scale placer work but also in sampling and for washing sluice concentrates and material cleaned by hand from bedrock-in other placer operations.
One to three cubic yards, bank measure, can be dug and washed in a rocker per man-shift, depending upon the distance the gravel or water has to be carried, the character of the gravel, and the size of the rocker. Rockers usually are homemade and have a variety of designs. A favorite design in the Western States consists essentially of a combination washing box and screen, a canvas or carpet apron under the screen, a short sluice with two or more riffles, and rockers under the sluice. The bottom of the washing box consists of sheet metal with holes, about one half inch in diameter punched in it. A rocker in use at Greaterville, Ariz., was.3 feet 4 inches long and 1 foot 9 inches wide on the inside and had a slope of 5 inches. The screen box was 6 inches deep and 20 inches square inside and had a bottom of sheet iron with ¼- to ½-inch holes punched about 2 inches apart. The baffle was 28 inches long and consisted of a piece of canvas. A single riffle ¾ inch high was used at the end of the rocker. Figure 3 is a drawing of a prospector’s rocker made by W. B. Young of Tucson, Ariz. The bottom of a rocker should be made of a single wide board, if one can be obtained, and planed smooth. This will greatly facilitate clean-ups. The cost of building rockers ranges from $5 to $15, depending mainly upon the cost of lumber.
After being dampened the gravel is placed in the box 1 or 2 shovelfuls at a time. Water is then poured on the gravel while the rocker is swayed back and forth. The water usually is dipped up in a long-handled dipper made by nailing a tin can to the end of a stick. A small stream from a pipe or hose may be used if available. The gravel is washed clean in the box and the oversize inspected for nuggets and dumped out. The undersize goes over the apron, where most of the gold is caught. Care should be taken that too much water is not poured on at one time, as some of the gold may be flushed out. The riffles stop any gold that gets over the apron. In regular mining work the rocker is cleaned up after every 2 or 3 hours, or oftener when rich ground is worked, if gold begins to show on the apron or in the riffles. In cleaning up after a run, water is poured through while the washer is gently rocked the top sand and dirt are washed away. Then the apron is dumped into a pan. The material back of the riffles in the sluice, is, taken up by a flat scoop, placed at the head of the sluice, and washed down gently once or twice with clear water. The gold remains behind on the boards, whence it is scraped up and put into the pan with the concentrate from the apron. The few colors left in the sluice are caught with the next run. The concentrate is cleaned in the pan.
With skillful manipulation of the rocker and a careful clean-up nearly all the gold is recovered. Violent rocking, is avoided so that gold will not splash out of the apron or over the riffles. The sand, behind the riffles should be stirred occasionally, if it shows a tendency to pack hard, to prevent loss, of gold. If the gravel is very clayey it may be necessary to soak it for some hours in a tub of water before rocking it.
When water is scarce two small reservoirs are constructed, one in front and the other in the rear of the rocker. The reservoir at the front serves, as a settling basin; the overflow goes to the one at the rear where the water is used over again.
Power rockers.- The capacity of rockers may be increased by using power drives. The use of such a machine was illustrated by the operation of George Graves in the Lynn district, Eureka County. Nev., during the summer of 1932. The rocker was 49 inches long, 27 inches wide at the top, and 21 inches wide at the bottom. It was 24 inches high in front and 21 inches at the rear. The screen had 5/8-inch round holes. The gold was caught on three aprons of canvas and wood. Riffles of ½- by ½-inch wooden strips were used on the aprons. The undersize from the screen passed over each-apron in turn. Nearly, all the gold was caught on the first apron. The slope, of the aprons was 3 inches to the foot.
The device was rocked by an eccentric arm at the rate of forty 6-inch strokes per minute. The capacity of the machine with two men working, was 1 cubic, yard per hour. Where gravel was free of clay the capacity was said to be as great as 3 cubic yards per hour. The cost of the rooker and the engine for driving it was $160. At $4 per 8-hour shift and 1 cubic yard per hour the labor cost of washing the gravel would be $1 per cubic yard.
A number of small, machines patterned more or less after the power rocker are on the market. They usually are built of iron, or steel and driven by small gasoline engines. Although of various designs they generally consist of a trommel or a shaking screen to remove coarse material, a short shaking sluice to save, the gold, and a pump to circulate, the water. Some of them contain a settling tank from which the solids are removed by a rake or drag. These machines have an advertised capacity of ½ to 2½ cubic yards per hour and cost $225 to $700. No operating data are available.
Long Tom
A long tom usually has a greater capacity than a rocker and does not require the labor of rocking. It consists essentially of a short receiving launder (see fig. 4), an open washing box 6 to 12 feet long with the lower end a perforated plate or a screen set at an angle, and a short sluice with riffles. The component boxes are set on slopes ranging from 1 to 1½ inches per foot. The drop between boxes aids in breaking up lumps of clay and freeing the contained gold.
A good supply of running water is required to operate a long tom successfully. The water is introduced into the receiving box with the gravel, and both pass into the washing box. The sands and water pass through the screen, which has about ½-inch openings into the sluice. The oversize is forked out. The gold is caught by the riffles. The riffle concentrates are removed and cleaned in a pan. Quicksilver may be used in the riffles if the gravel contains much fine gold.
The quantity of gravel that can be treated per day will vary with its nature, the water supply, and the number of men employed to shovel it into the tom and fork out the stones. Wilson states that 2 men, 1 shoveling into the tom and 1 working on it, can wash 6 cubic yards of ordinary gravel, or 3 to 4 cubic yards of cemented gravel, in 10 hours. At times the tom is operated by 4 men, 2 shoveling in, 1 forking out stones, and 1 shoveling fine tailings away. Toms are rarely used now in the United States; where running water and grade are available a simple sluice is generally as effective and requires less labor.
A modified form of long tom has been employed for washing beach sands at Nome, Lituya Bay, Yakataga, and Kodiak, Alaska. For saving fine gold the box is set at a high gradient, 3 to 4 inches per foot, and the screened material is passed over riffles and amalgam plates. The water for sluicing generally is bailed with a large dipper. The average duty per man per 10 hours for long-tom or rocker work’on beach operations is 3 to 5 cubic yards.
Surf Washers
Surf washers are similar to long toms but are wider and shorter. They can be used only when the surf is of proper height. They are set so that the incoming surf rushes up the sluices, washes material from the screen box or hopper, and on retreating carries it over the riffles and plates. One man can attend to two surf washers, and in one instance 8 cubic yards was handled per 10 hours.
A simple surf washer used about 1902 at Topkuk, Alaska, was a riffled sluice 3 to 4 feet wide and 8 to 10 feet long, set on the sand at the water’s edge so that the incoming waves washed through it to the upper end yet retreated below the lower end. The sluice was made of boards nailed to sills at either end which could be weighed down with rocks or otherwise. The sides were only 4 or 5 inches high. The riffles, similar to those used on dredges, were made in sections of about 1- by 1-inch strips and were spaced about an inch apart. The end sections were transverse riffles the center section was longitudinal. The box preferably was set on a grade of 8 to 10 inches per 12 feet. Best results were obtained by using quicksilver in the riffles. It was stated that when the surf was strong the washer would treat as much as two men could shovel, but that at other times it had to be fed very slowly.
Dry Washers
Dry washers have been used for many years in the Southwest where water is scarce, especially in New Mexico where probably 3 or 4 million dollars in gold has been produced during the last century by dry-washing, A small steady production by dry washers still comes from, the Cerrillos, Golden, and Hillsboro districts each year. In years when other employment is scarce the production increases. During 1931 and 1932 a considerable number of men also used dry washers in Nevada, southern California, and Arizona.
Gravel to be treated successfully by dry washers must be completely dry and disintegrated. With dry washers operations must be stopped after rain storms until the ground dries out again. The only successful dry washing up to 1932 has been on a small scale. Plants with mechanical excavators and extensive power-driven dry-washing machinery have been tried, but in the United States none has been commercially successful, partly because in large-scale work the gravel is dug faster than the sun can dry it out. Even in very dry climates the gravel is slightly damp below the surface and must be dried before it can be treated in a dry washer. Spreading the material to sun-dry or putting it through driers adds to the cost of mining. In small-scale work the gravel dries out as fast as it can be treated.
Individual workers select the material they treat with regard to both dryness and probable gold content; it is difficult to do this on a large scale with hired labor. In large-scale work, particularly with mechanical excavation, the cost of sizing the material is an important item; clay and cemented gravel introduce further difficulties.
Dry washers usually are run by hand and have about the same capacity per day as rockers of a corresponding size, but the work of operating the dry machine is much harder. When the gold-bearing material is completely dry and disintegrated, panning tests of the tailing show that a good saving can be made, except perhaps with extremely fine or flaky gold. Completely disintegrated material, however, seldom is obtained. The tops of clay streaks in the gravel are likely to be richer in gold than the gravel itself. Clay or cemented gravel seldom can be broken up sufficiently by hand to free all the gold without the use of some form of pulverizer. In a dry machine all gold included in a lump of waste passes out of the machine. As water usually breaks up all the gravel and separates the gold from the other material a better saving generally can be effected by rocking or in sluice boxes than in a dry machine.
The basic principle of the dry washer is separation of the gold from the sand by pulsations of air through a porous medium. The screened gravel passes down an inclined riffle box with cross riffles; the bottom of the box consists of canvas or some other fabric. Under the riffle box is a bellows by which air in short, strong puffs is blown through the canvas. This gives a combined shaking and classifying action to the material; the gold gravitates to the canvas where it is held by the riffles, while the waste material passes out of the machine.
The gravel is shoveled into a box holding a few shovelfuls at the head of the washer whence it runs by gravity through the machine. A screen with about ½-inch openings is used over the box; all stones over about 1 inch in diameter generally are discarded in mining. One man working alone fills the box, then turns a crank which runs the bellows until the gravel is run through the process is then repeated. With two men working, one shovels and the other turns the crank. One man can treat ½ to 1 yard per day with a hand-operated washer where the gravel is handy to the machine. Some dry washers are run by a small gasoline engine which saves the labor of one man the capacity of such machines is considerably greater than that of hand-operated machines.
In cleaning up, the material back of the riffles usually is dumped into a pan and washed out in water. If water is very scarce the accumulated material from the riffles may be run through the machine a second time and then cleaned further by blowing away the lighter grains of sand in a pan.
Dry washers usually are handmade and have a large number of designs and sizes. Figure 5 is an isometric drawing of a machine built and run by E. C. Spurr on Goler Gulch near Randsburg, Calif., in June 1932. The bellows of the machine is made of 36-ounce duck and the bottom of the riffle, box of 8-ounce single-weave canvas. Spurr has found by long experience that the 8-ounce material is the best for the purpose. Silk or rayon permits a good extraction of gold, but too much dust goes through into the bellows. Heavier canvas is too tight for good separation. Copper-wire fly screen is used under the canvas. The riffle box is 11 inches wide and 40 inches long and contains 6 riffles. The type of riffle is shown in figure 5. The slope of the riffle box is 5½ inches to the foot. The gravel and sand are shoveled onto a screen with 3/8-inch square openings at the top of the washer. The machine is run by a ¾-hp. gasoline engine. The bellows is operated at 250 pulsations per minute; the stroke is 3 inches. The capacity of the machine was 1 cubic yard in 1¼ hours or 0.8 yard per hour. This probably would correspond to 1½ or 2 cubic yards, bank measure, on account of the plus 1-inch material having been thrown out in mining. The gravel had been collected in an old drift mine, and carried out in buckets; 3 hours were spent by one man in getting out the gravel.
In cleaning up after running a cubic yard through the Spurr washer the riffle box was lifted out and turned over on a large, flat, baking tin. The concentrate from the upper three riffles was first panned and the gold removed; both coarse and fine gold were saved, the total being worth about 75 cents. The lower four riffles had one good-sized color and a few small ones. Nearly all the gold was caught in the upper riffles; this indicated that a fair saving was being made of the free gold.
Hand-operated machines, however, are usually much smaller and have the riffle box set at a steeper angle.
Shoveling-into-Boxes
Mining.- Shoveling-into-boxes is a small-scale placer-mining method in which the gravel is loosened by picking and is shoveled by hand into sluice boxes. It is particularly adapted to small, shallow, moderately rich deposits where only a little water is available or where the grade is insufficient to allow room for disposing of the tailings unless the gravel is elevated. If the water supply is adequate the ground-sluicing method (described later) should be considered, and if the deposit is large enough to justify the required capital in¬vestment some other method such as hydraulicking or dredging would be preferable.
The method of shoveling-into-boxes has its chief application in the working of small deposits by men with little capital but a willingness to work hard.
The quantity of water available will influence the scale of operations and the size of sluice used. A minimum flow of 15 to 20 miner’s inches (170 to 225 gallons per minute) is required for a 12-inch sluice box with a steep grade. Smaller flows than this can be utilized by reservoiring the water and using an augmented flow. A common practice followed where the quantity of water is limited is to place a grizzly or screen over the sluice and thus increase the duty of the water. A head box with sloping sides and a grizzly near the bottom may be used for receiving the gravel. In this case the oversize is forked out. In one Nevada operation the gravel first was run through a trommel to wash it and screen out all coarse material. Puddling boxes may be used if the gravel contains much clay. If the ground is of good grade it may be practicable to pump water for the sluice the feasibility of obtaining a gravity flow, however, should first be investigated, as the mining expense due to pumping may be.more than the cost of a ditch distributed over the yardage moved,
Water usually is conducted in a ditch to the sluice which is set up in the most advantageous position to begin work. Boxes are 8 to 24 inches wide and range from 3 to as many as may be required to transport the tailings to a suitable dumping ground; they are laid on sills at approximately the mean elevation of the surface of the deposit. If enough water is available 6 or 8 inches per 12 feet, is a good grade with most types of gravel. If water is scarce or the gravel angular a steeper grade will be desirable; the grade should be uniform. The best type of riffle depends on the nature of the gravel and the gold rather than on the method of extraction. An end shake was given to the box at a mine in Arizona to increase its capacity. Water was hauled for washing. Riffles are discussed in a subsequent paper.
The cost of boxes depends chiefly on the cost of lumber delivered to the property, which may range from $15 to $60 per 1,000 board-feet. A 12-foot box, 12 inches wide, constructed of three 1- by 12-inch boards with three sill frames of 2 by 4 lumber, requires.about 45 board-feet of lumber. If clear lumber costs $35-per 1,000 board-feet the cost of a set of five boxes would be about $8.00. Material for riffles may cost little or nothing or as much as $1 per box.
After the boxes are set, shoveling begins at an advantageous point. All material of a size that will run. through the sluice is shoveled in and the oversize is thrown to one side. Boulders from the first cut should be stacked outside the pit, on barren ground if possible. The width of a cut usually is limited to the distance a man can shovel in one operation. When shoveling from any distance it is best to set boards above and on the opposite side of the box; these increase the efficiency of the shovelers. The greatest height a man can shovel into a box is 7 to 8 feet above 5 or 6 feet the efficiency of the shovelers is reduced markedly. If over 3 or 4 feet in depth the gravel usually is excavated in benches to facilitate digging and at the same time to permit the upper layers of gravel to be raised a minimum height. Where the gravel is shallow wheelbarrows may be used. At a Nevada mine the gravel was shoveled onto a conveyor belt which discharged into a trommel. The oversize was discarded, and the undersize ran through a sluice. Where two or more men are working in the same cut the heights of succeeding benches are governed by the character of the material being dug and the distance the gravel has to be lifted. Work may begin at one edge of the deposit and proceed across it by regular cuts. The sluice may be maintained on the surface of the unworked ground or on bents on the opposite side of the cut. After the first cut the boulders are thrown onto the cleaned-up bedrock. Where cuts are run on both sides of the sluice the boxes are supported on bents, as the ground underneath them is dug out. At other places the boxes may be set on bedrock and all dirt shoveled into the head of the sluice from short transverse cuts at the upper end of the pit. Work visually begins at the lower end of a deposit so that bedrock maybe kept drained. The length and order of making the cuts will depend upon local conditions.
The method of working a deposit near Oroville, Wash is shown in figure 6, A, and at Blewitt, Wash., in figure 6, B.
Experienced miners, work out the ground in regular cuts and in an orderly fashion. Enough faces are provided so that shovelers will not interfere with one another. Provision is made to keep bedrock drained, and boulders and stumps are moved a minimum number of times. Cuts are taken of such width and length as to make the shoveling as easy as possible. The boxes are kept, at such a height, that the minimum lift, of the gravel is required consonant with, enough fall for the gravel to run through the boxes with the water available and to allow dump room at the tail, end of the sluice. Leaks in the sluice are stopped promptly, and shoveling is done in such a manner that the sluice does not become clogged or water splashed out. Water in the pit hampers shoveling.
Several times as much gravel, can be washed per man-shift by this method as by the use of rockers or long toms. Under the best conditions a good workman can shovel 15 cubic yards
of gravel per shift into boxes 3 or 4 feet above bedrock. Where the gravel is tight and coarse and the bedrock rough, he may be able to shovel only a yard a day. The time necessary to construct, set up, and clean the sluice boxes and to clean bedrock reduces the average performance of men shoveling into boxes to about 4 yards per shift.
Cleaning bedrock.- When a sufficient area of bedrock is exposed it is cleaned up carefully. If the bedrock is easy to clean this may be done as the work progresses up a cut. In such ground if the gravel is shoveled in benches by two or more men the man who takes up the lower layer of gravel may clean the bedrock as he goes along. If the bottom is difficult to clean a full cut may be taken before the bedrock is given the final clean-up.
Cleaning bedrock is perhaps the most laborious and painstaking task of the placer miner; his success or failure often depends on the thoroughness of this operation.
After all loose gravel is shoveled into the boxes the bedrock should, if possible, be taken up with pick and shovel to a depth of 6 inches or more and likewise put into the sluice. Any large rocks near bedrock should be washed off before they are thrown aside, because clay adhering to them may contain gold. If the bedrock is decomposed or soft, or if there is a false bedrock, this process will recover practically all the gold.
If bedrock is hard, cleaning it is more difficult, as some material is bound to be left on the bedrock in shoveling, and the crevices in bedrock will contain gold.
If water can be taken from the sluice or ditch through a hose under low pressure all loose material missed in shoveling will be washed down to a hollow where it will be collected and placed into the boxes or in a rocker. The bedrock then is scraped and swept, and the crevices are cleaned out finally it may be washed a second time.
If it is not convenient to use water the bedrock may be cleaned up dry. The bedrock is swept, scraped, then swept a second time; the crevices are cleaned out as before. The sweepings and scrapings, together with the material from the crevices, are washed either in the sluice or in pans or rockers. Large colors or nuggets are picked up as found.
The tools used for the hand work are picks and shovels, brooms, small stiff brushes, perhaps a sponge to dry out hollows, and hand scrapers of various sizes and shapes, ranging from sections of old frying pans to knives, spoons, or bent wire for cleaning narrow crevices.
In small operations, such as the typical 3- or 4-man ground-shoveling venture, cleaning bedrock is carried to greater extremes than in larger mines where labor is hired, as the incentive to careful work is greater and the yield necessary to encourage further cleaning is less, Skilled and careful “crevicers” have been known to make fair wages on bedrock abandoned by organized mining companies. The miner should therefore be sure his cleaning operations have been carried to the point where he is no longer getting enough gold to recompense his efforts.
The concentrates from the sluice usually are panned or washed in a rocker for the final separation of the gold.
Ground Sluicing
General Features and Application
As previously defined, ground-sluicing is a placer mining method, in which gravel is excavated by running water not under hydraulic pressure. In some cases water is stored in reservoirs, and greatly increased flows are discharged during short periods. This variety of ground-sluicing is termed: “booming” by placer miners and is so called in this paper. The action of the ground-sluice water may be augmented by hand work or by a jet of water under pressure. However, if hydraulic monitors or giants perform most of the work the method becomes “hydraulicking”, described in a later paper.
With a few exceptions ground-sluicing is used in small operations by miners with little capital. Otherwise it is used only where water under a substantial head is not available or where the gravel deposit is too small to justify building ditches or installing pipe lines for hydraulicking. The chief application of ground-sluicing is to deposits in or near stream beds. If applied to higher gravels pipe lines, flumes, or ditches are necessary, and the method loses one of its chief advantages, a low initial cost.
Ground-sluicing is not adapted to mining large deposits of tight or cemented gravel these demand the tearing, disrupting force of giants. Gravel containing large boulders can be ground-sluiced, but more labor is necessary than if hydraulicking is used; the ground-sluice water seldom loosens and transports as large boulders as a giant or as large ones as will run through the sluice.
At many places no preliminary development work is necessary at others long cuts must be run to reach bedrock under the deposit. If booming is to be done a dam must be built for a reservoir and perhaps an automatic gate. A sluice box is always used, although in many mines for little more than as a race to carry away the tailings. In bouldery ground derricks or drag lines may be needed to remove boulders.
A large number of small ground-sluicing operations were being carried on during the 1932 season by groups of 1 to 4 men working for themselves. Enough gold to pay regular wages was obtained at very few of the operations. Usually the miners received less than $1 per day for their efforts. A few larger operations have been carried on for a number of years; some of them have been profitable. Essential data concerning the larger mines and representative smaller ones operated in 1932 are shown in table 7. These mines are described in more detail later. They illustrate the applications of the method and general ground-sluice practices.
Types of Placer Deposits Worked
Except for the Osborne lease at Superior, Mont., gravels of moderate thickness along stream beds were being worked by ground sluicing at the mines listed in table 7. The depths of gravel ranged from 5 to 22 feet. Except at two placers very little of the gravel was tight, and none of it was cemented. At these, the Rundle and Morgan placers, Blackhawk, Colo., the gravel was tight and had to be loosened by picking; however, most of the material mined was overburden which was easily ground-sluiced,
Water Supply
The water supply was limited at most of the mines worked by ground-sluicing. At the Rundle and Morgan placers more water was available in the creek than could be used to advantage, because the gravel had to be loosened by picking. As noted in table 7, 60 to 500 miner’s inches were used at the various mines listed. The natural flow of the streams ranged from 10 to 500 miner’s inches.
Sluicing
Operations at all ground-sluicing mines listed in table 7 consisted of running cuts preliminary to mining or mining as contrasted to developing.
Ground-sluicing has an advantage for running bedrock cuts in that a relatively small capital expenditure is required to test the gold content of the gravel and to ascertain the mining conditions. Cuts made in this manner also open up the deposit for mining. A relatively low yardage per shift is obtained in such work. A large part of the expense of running such cuts is the construction of the sluice, which will be used if the deposit is mined later. The work at the Rundle, Osborne, Kamloops, Willow Creek, and Magnus mines, at the time the authors visited them, consisted of running bedrock cuts.
At the other seven properties strictly mining operations were under way. Regular ground sluicing can be subdivided further according to the manner in which the water is used: (1) Water poured over the upper face of the cut and (2) water directed along the bottom of a straight or curved bank. Under (1) the cascading effect of the water is utilized to break down the gravel, or the fall of the water from a projecting flume or pipe is used to cut the bottom layer. Under (2) the current is used to undercut the bank and carry away the broken gravel at the face as it breaks down. The depth of the gravel has an important bearing on the practice followed; with thick deposits the cascading or falling of the water over the upper face is likely to give the best results; in thinner gravels the other method is usually advantageous. The width of the deposit is also a factor in narrow channels the first method would have an advantage over the other. As shown by table 7 the thickness of gravel at the Morgan, Bar No. 2, and Harvey placers where the water was brought over the face was 5, 6, and 22 feet, respectively. At the other four placers, Ravano, Bar No. 1, Camp Bird, and Bennet the depth of gravel was 6, 6, 10, and 15 feet, respectively.
Of the 12 mines listed in table 7 sluicing with the natural flow of the stream was followed at 3. At 5 properties a minor part of the water was used under pressure, and booming was practiced at 5 not counting the Ravano. In one placer (Camp Bird) a hose was used for cutting the bank and the broken gravel removed by booming.
The water may be directed against the bank in a channel made by piled boulders or by, boards. It can be diverted conveniently to any desired point or direction by means of what are called shears. These consist of 1- or 2-inch boards 12 feet long nailed to two tripods which slope back from the water flow at an angle of about 60°. The tripods are of pointed poles about 4 feet long and so constructed that boulders may be piled on the base to hold them in place. A row of “shears” may be used to direct the force of the water .against a bank, or two rows may be used to form a flume.
Sluicing With Natural Flow of Stream
Of the multitude of “snipers” working on the creeks in the summer of 1932 many washed their gravel by ground-sluicing with the natural flow of the stream. The only equipment essential for this type of work in shallow gravels is a few 12-foot sluice boxes and picks and shovels. Table 7 shows that 2 ¾, 9, 3, and 9 cubic yards, respectively, were handled per man-shift at the first four mines in the table where the natural flow was utilized. At the Morgan placer water running down the face of a narrow cut was used to carry the fine material in the gravel to the box after it was loosened by picking. At the Ravano a cut was made first down one side of the area to be washed during the season and then extended across the channel. The water was directed against the bank by means of dams. Although a reservoir was used and the stream of water was augmented for a half shift each day the mine is placed under this class, as it is representative of a large number of operations where only
the natural flow was utilized. At the Bar No. 1 the water was brought down over the face. At the Osborne deeper gravels were mined, and the water cascaded down the face of a cut. Boulders were removed by a power derrick.
Sluicing With a Minor Part of Natural Flow of Water Used Under Pressure
Where part of the water can be brought into the workings under pressure through a pipe the nozzle may be used to replace hand-picking in loosening and disintegrating the gravel. It may also be used to replace part of the hand labor in cleaning up bedrock. The ground-sluice water washes the gravel into the boxes; it also breaks down the bank to various degrees at different mines. The actual sluicing operations are quite similar whether or not water under pressure is used.
At the Rundle, Bar No. 2, and Kamloops mines, where pressure pipes were used the head of the water ranged from 6 to 60 feet, as shown in table 7; nozzles 1 and 2 inches in diameter were employed. The yardage moved per man-shift was 3, 12, and 18, respectively,
Booming
Booming utilizes the increased cutting and transporting power of water under flood conditions. As pointed out, water is stored in a reservoir and then released, flowing for relatively short periods. At the beginning of the season, when high water prevails, the booms may occur frequently, and each one may last relatively long. As the supply of water fails booms occur less often until finally there is not enough water to operate. Booming is the most important type of ground-sluicing. A much larger duty can be obtained per unit of water by booming than by other forms of ground-sluicing. The increased volume of water carries boulders into the sluice that otherwise would have to be moved by hand or by power and breaks down the banks against which a smaller stream would be ineffective. Larger sluice boxes must of course be used when booming than when utilizing only the natural flow of the stream.
Booming is used in running development cuts as well as in strictly mining work. Of the three strictly mining operations listed under this head a side cut was used in two and an overcast at the end of the pit in the third.
The average number of booms per day at the five mines (excluding Ravano) ranged from 2 to 24. The duration of booms was 1½ to 30 minutes.
The duration of a boom is governed by the size of reservoir and the flow of water. The capacity of the reservoir should be governed by the character of the ground. In heavy, rocky ground a short period with a correspondingly larger surge is more effective than a longer period with a smaller stream. In other ground, such as that at the Camp Bird mine, longer periods of washing, with correspondingly less water, give the best results. Reservoirs usually are constructed by building a dam across a narrow part of the stream bed or canyon and backing the water up behind it. Ordinarily, earth dams with a board facing on the upstream side are used. Reservoirs with capacities of ½ to 1¾ acre-feet (table 7) are used at the mines listed. Automatic gates have a double advantage in that no labor is required to operate them and the booming in the pit can continue 24 hours each day. Automatic gates are shown in figure 7. Although the water is not as effective when unattended as when the miners are on shift it accomplishes considerable work during off hours.
Table 7 shows that 4, 18, 17, 32, and 7 cubic yards, respectively, were washed per man-shift at the mines where booming was done.