Table of Contents
The Problem with separating Copper from Zinc by flotation
The treatment of heavy sulphide ores of copper containing zinc and pyrite is often extremely difficult particularly if soluble copper and sulphates are present. This is usually the case in ore deposits near the surface or in tropical countries where the annual rainfall is quite high. The method of ore deposition is also a factor for usually we find such ores with the minerals very closely associated, thus indicating the necessity of very fine grinding to liberate the copper from the zinc and pyrite. This, coupled with the activating effect of copper sulphate on both the zinc and pyrite, presents a difficult selective flotation problem.
Typical of such an ore is the following analysis:
- Copper 3.78%
- Sulphur 42.38%
- Zinc 12.45%
- Gold 0.01 oz/ton
- Iron 32.84%
- Silver 1.50 oz/ton
- Insoluble 8.50%
In order to meet smelter requirements it is desired to produce at least a 20% copper concentrate with not over 8% zinc. The copper is present principally as chalcopyrite in extremely close association with both the sphalerite and pyrite.
The Copper Zinc Process Flowsheet
After extensive laboratory test work the above typical flowsheet was developed to meet the requirements for this type of ore. Removal of soluble salts as soon as possible is very important in order not to contaminate fresh mineral surface produced in crushing and grinding. About 2% of the total copper in this ore exists in soluble form so provision is also made for its recovery by precipitation on scrap iron. Two stage grinding with intermediate washing is used to remove soluble salts released between stages.
CRUSHING
Primary slimes are washed out ahead of the Jaw Crusher and also in the washing scrubber and trommel.
If the ore contains corrosive soluble salts, it is necessary to provide equipment resistant to corrosion. This applies in particular to the trommel screen section and the slime classifier and also the thickeners and diaphragm pumps. Thickeners with wood tanks and mechanisms rubber covered or fabricated out of stainless steel are satisfactory for this service. Type 304 stainless steel is usually satisfactory.
ROD MILLING
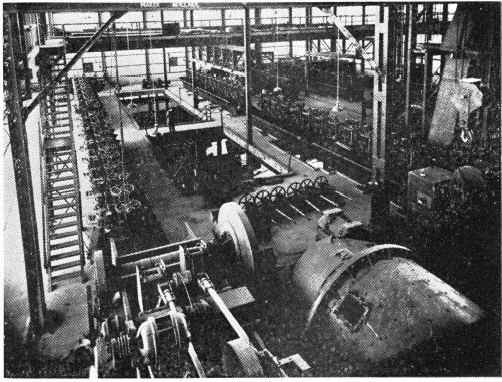
With ore crushed to about ¾” in the circuit as illustrated some soluble salts may still carry through in objectionable amounts. Open circuit Rod Milling is therefore incorporated in the grinding section to reduce the ore to about 10 to 14 mesh. No reagents are added at this point as the main objective is to remove soluble salts. The rod mill discharge after passing through a spiral screen to remove tramp oversize is diluted and pumped through a cyclone for further washing. Slimes and water pass on to a thickener in the manner as indicated. Note that the settled solids from the thickener return to the Classifier for density and classification control in the ball mill grinding circuit.
WASHING THICKENERS
The washed primary slimes are treated by flotation if sufficient recoverable value is present; otherwise, this may go direct to waste. Water overflowing the primary thickener will carry the copper sulphate. This should pass through rectangular concrete tanks filled with scrap iron for copper deposition. The reaction can be speeded up by bubbling compressed air into the scrap iron mass. Periodic clean-up for recovery of the cement copper is adequate.
BALL MILL GRINDING
Grinding the washed rod mill discharge to approximately 90% minus 200 mesh was necessary to get fairly good liberation of the copper and zinc from the bulk of the pyrite. Lime was added to the ball mill to give a pH of about 10 for depression of the pyrite. Zinc inhibiting reagents appeared detrimental to good copper recovery in the primary circuit probably due to close mineral association.
CONDITIONING AND BULK FLOTATION
The classifier overflow at 90% minus 200 mesh and approximately 20% solids with a pH of about 10 is conditioned with Dow Reagent Z-200. This reagent has both promoting and frothing characteristics favorable to flotation of the copper and zinc with a minimum of pyrite. Sodium isopropyl xanthate Z-11 and a light frother such as methyl isobutyl carbinol or Dowfroth 250 may be used as alternate reagents.
Bulk flotation under differential conditions to reject the pyrite into the tailings results in about one-third (1/3) of the total weight ending up in the bulk concentrate containing slightly over 90% of the total copper. Approximately 2% of the total copper was previously removed in soluble form in the primary washing stages ahead of the grinding circuit.
REGRIND AND SELECTIVE FLOTATION

The bulk copper-zinc concentrate after thickening is reground to all minus 325 mesh. Even at this grind microscopic examination shows inclusions of chalcopyrite in sphalerite grains. Zinc sulphate and cyanide are added to the regrind mill to effectively depress the sphalerite. Xanthate Z-11 or reagent Z-200 is added to the conditioner to promote the chalcopyrite and float it in the “Sub-A” circuit as shown. Note that a scavenger or middling product is taken at the end of the circuit and returned to the regrind section for further grinding. Final copper concentrate assayed approximately 28% copper with slightly under 8% zinc. Copper recovery was between 70-75% on this difficult ore. By lowering the copper grade and increasing recovery the zinc content would become excessive. The smelter did not permit copper with over 10% Zn.
FLOTATION MACHINES
“Sub-A” Flotation Cells of the cell to cell type are recommended for all the flotation steps in this treatment circuit. A high degree of selectivity is very essential in the roughing, scavenging, cleaning, and recleaning steps throughout since the bulk of the ore is pyrite, and it must be rejected into the final mill tailing. The final tailing from the regrind section will be high in zinc. When market conditions are favorable it can be converted into a shipping grade zinc concentrate.
Recommendations for Copper Zinc Separation by Flotation
On ores of this type it is very essential to carry out a comprehensive test program on representative samples taken from various zones of the mining operation. Samples should be shipped in sealed containers to retain the original moisture content and soluble salts and tested without delay. This minimizes the effects of surface oxidation and more nearly approaches the conditions under which the ore will be milled.
Source: This article is a reproduction of an excerpt of “In the Public Domain” documents held in 911Metallurgy Corp’s private library.