Table of Contents
A small gold mine flowsheet is shown below together with cost data which clearly shows the results that can be ‘obtained when handling a low grade ore by a simple process. There are many commendable features in such a set up and no complicated machines or practices are embodied in this plan. In fact, its simplicity is appealing and the results obtained prove the practicability of this flowsheet.
The rod mill product passes over a roughing table where a high grade gold concentrate containing most of the free mineral is sent directly to a Clean-Up Pan. The middlings from the table are sent directly to an 8-cell “Sub-A” Flotation Machine from which a high grade concentrate is obtained. The tailings from the flotation machine are sent over a pilot concentrating table for visual examination. A middling pump and a dewaterer can be installed to take care of the middlings for regrinding, should enough value be found in them to warrant such a treatment. In this concentrating mill, however, it has been found that the middling product is of so little value that it would not be economically profitable to regrind and retreat this product. The cost data above referred to has been compiled from actual operating results and shows the cost of milling both for the old 50-ton plant and the new 100 ton concentrator, as is now in use. Note the reduction in milling costs through the use of the new flowsheet which includes an 8-cell “Sub-A” Flotation Machine. The savings made in lower operation costs and lower maintenance costs are noticeable and this saving was also made in the face of a 12.5% increase in wages made when the new plant was started.
![]() |
|
Many of our so-called small gold mines or low grade deposits could well take this simple and inexpensive flowsheet for an example and be rewarded by a good profit per ton of ore treated, if the owners or operators would adhere to these principles. These are namely a simple crushing, grinding, concentrating, and flotation circuit without frill or fancy theories, but with a constant supply of ore through the mill at a nominal profit per ton, operating continually 24 hours per day. In other words, it may pay to have a lower recovery with a higher net profit than a higher recovery with an actual loss.
You will note from the above chart, the fairly high cost of marketing concentrates, but with the addition of the Clean-Up Pan a large portion of the free gold can be recovered in the form of amalgani and then reduced to bullion for shipment direct to the mint. The treatment of concentrates even of a complex nature is now standardized and should result in additional profits.
Operating Costs Data on Mill
Only rough estimates of milling costs can be made without study of each individual case, as these are determined largely by local conditions that are peculiar to each problem.
To aid in arriving at approximate operating costs, we are giving four charts with curves showing operating costs for the different standard methods of treating ores. These charts show the costs compiled from actual operating figures secured from a number of mills operating under varying conditions. These figures show that operating costs do not increase greatly as one would naturally suppose when smaller tonnages are handled.
In studying the various factors affecting milling costs, the one point that is most noticeable is the effect of operating time on these costs. Plants that have mechanical difficulties show costs greatly in excess of those with full operating time working under comparable conditions, and this demonstrates clearly the importance of having fool proof and ruggedly designed machinery that will run 24 hours per day. Modern milling equipment must be able to take care of overloads and handle oversize material without choke-ups and the resulting shut-downs. One must always keep in mind that after all a machine, a mill, or a process is only as strong as the weakest link.
Gold Mine Operating Manual
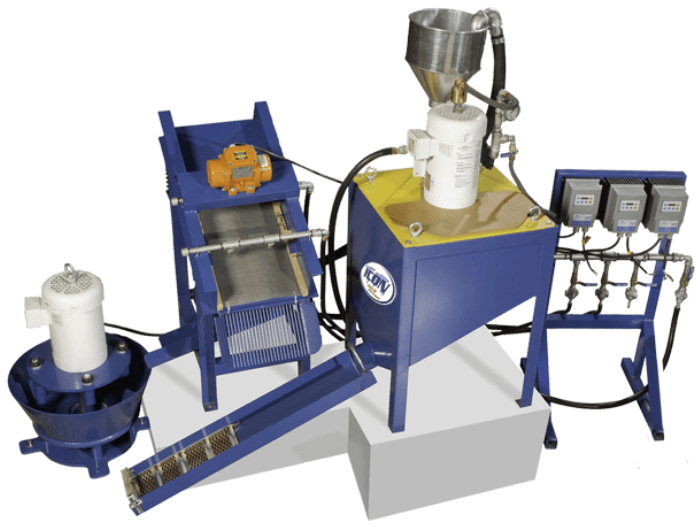
The EXAMPLE Gold Mine Operating Manual has been prepared to provide a practical reference for operators in the EXAMPLE Gold Mines Processing Plant. This manual contains basic information about the process and equipment used in the process. Each unit is identified by name and equipment number. The function of each unit, a process and control description, and operating information is discussed. The last two sections deal with general plant safety and the definitions of terms used in the context of the processing plant.
This manual is intended as a general guide to plant operations. It is NOT intended to supercede, contradict or in any way negate manufacturer’s instruction manuals, which contain detailed information about each piece of equipment. In the case of uncertainty or requirement for clarification and/or further details, readers are to refer to the manufacturer’s manuals.
The EXAMPLE Gold Mill is designed to process 500 tonnes per day of ore. The flowsheets are conventional and consist of two stages of crushing, single stage ball mill grinding, cyanidation and a Merrill-Crowe precipitation circuit for gold and silver recovery. In addition to the cyanide circuit, gold leach residue is treated in a flotation stage to recover un-leached silver (Argentite) minerals. This circuit is followed by a small cyanidation circuit for recovery of silver (and remaining gold) from the flotation concentrate. Precipitated gold and silver are refined in an induction furnace to produce dore bullion.
The crushing plant will operate independently of the mill. In addition, whereas the mill will be primarily run from local start/stop stations, the crusher is designed to be run from its control panel. The dividing point between the two plants lies at the fine ore bin; all equipment prior to this bin is considered in the Crushing Plant and all equipment subsequent to it in the mill.
General Design Criteria:
Milling Rate = 500 tonnes/day (550 sptd)
Crushing Rate = 2 x 12 hour shifts/day 7 days/week x 350 days/year.
Head Grade = Au 7 gms/tonne (0.21 Tr.oz/ston) + Ag 260 gms/tonne (7.6 Tr.oz/ston)
Metal Recoveries = 95% Au and 75% Ag
https://www.911metallurgist.com/gold-process-description
https://www.911metallurgist.com/small-crushing-plant-operating-guide
https://www.911metallurgist.com/small-crushing-plant-operating-guide