Table of Contents
The following is not offered as an extended paper on the subject of shaft sinking, but more as a description of the present practice of shaft sinking in the Butte district. The Anaconda company is sinking at present the following shafts: Badger State, Moose, Mountain Consolidated, Mountain View, Pennsylvania and Tropic. At the High Ore and Leonard mines the shafts are being deepened by sinking two compartments and will subsequently be enlarged to the full working size by raising alongside the compartments which are now being sunk.
Shaft Timbering
The shafts of the Butte district, generally speaking, are of three compartments arranged in a straight line, and the pump compartment is usually arranged for the use of an auxiliary hoisting cage, as well as for carrying pipe lines and electric wires. The Rainbow shaft is practically square, and of three compartments. The length of the shafts outside of timber will vary from 17 to 22 ft., and the width from 6 ft. 6 in. to 7 ft.
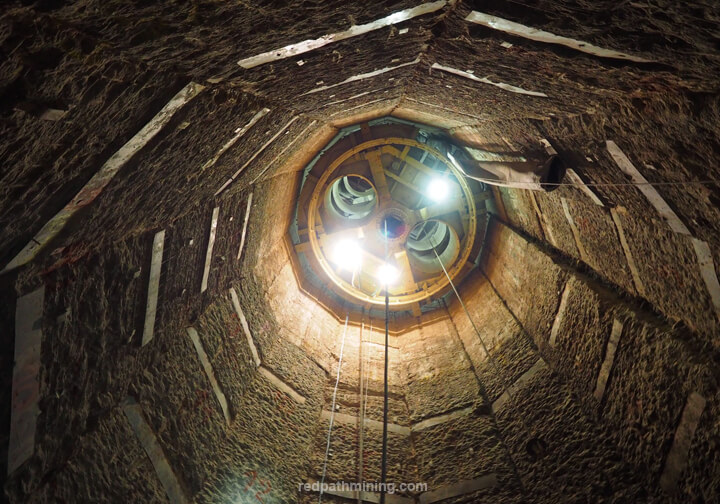
Fir timber is used in all shaft work. This may be obtained from the Coast, when it is known as Coast fir, or from Idaho or Montana, when it is known as native fir. The native fir seems to be the tougher wood, but it is hard to obtain clear lumber in the lengths and sizes necessary for shaft work. Some of the shaft timber of the Anaconda company has been treated with creosote as a preservative, but this practice has not come into general use, as the ground of the camp is so heavy that the timbers usually crush before they rot. The size of timber most used for shaft work is 12 by 12 in., while 10 by 12 in., 10 by 14 in. and 12 by 14 in. are used for some of the special pieces around the shaft. The new Leonard shaft is timbered with 14 by 14 in. wall plates throughout.
No machinery has been introduced here as yet for the framing of shaft timbers, although the North Butte company is considering such a machine, and all of the timbers are therefore hand-framed. It may be of interest to note that ½ to ¼ in. is generally held off the wall plate and end plates at each end in the framed part to make the mitre draw close together when the set is being blocked; thus the wall plate for a shaft 20 ft. long would be 19 ft. 11 in. long. In order to hold the set together when it is being blocked, 1-in. wooden pins are driven at each corner, in holes bored for that purpose. These pins are made by driving 1-in. square blocks of wood through a 1-in. round hole in iron 1 in. thick.
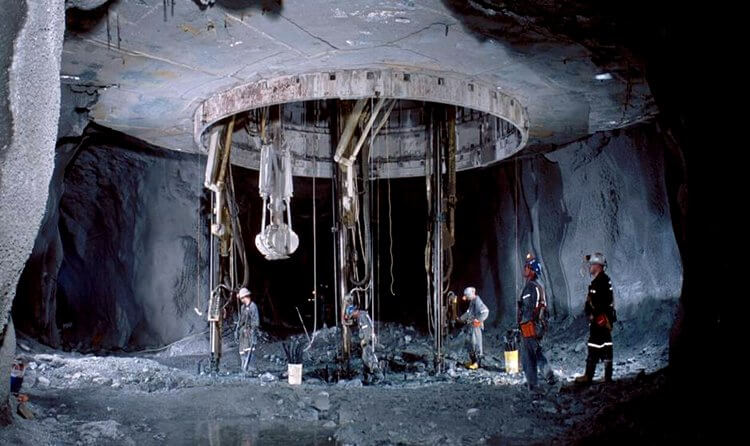
To keep the shafts vertical, blocks nailed together (Plate I, Fig. 2), made of boards 15/16 in. thick are used, so that half the width of the line will bring the center of the line 1 in. from the corner of the set both ways. While the timber is being framed, the carpenter marks with his scratch awl a line on the timber 1 in. from each corner, as shown in Fig. 1, Plate I, and this line saves a great many rule measurements in the early blocking of the set. At about every 50 ft. these lines must be lowered to new blocks. A set is selected at a point about 50 ft. below the blocks, and measurements are taken each way from the corner line to determine how far the line is from the timbers. The new blocks are then nailed in place and the lines suspended from them. If the measurements to the timbers do not correspond to the old measurements, the block is cut with a pocket knife to bring the lines exactly to their former position. It is well to measure diagonally across between lines at about every 100 ft. to see if the shaft remains square.
A transit should be taken down before reaching a station, and readings taken from the corners down to the level of the instrument. Posts are then cut to bring the shaft timbers level. This is called a leveling-up set; this leveling may be done with a carpenter’s level, but not as quickly nor as accurately.
The placing of the collar set is the first thing to be done in starting a shaft. Its height above the ground is determined by the amount of room available for the dumping of waste rock from the sinking operations. In a level place it is generally raised about 20 ft. The wall plates of the collar set are usually made 10 ft. longer than the shaft set, projecting 5 ft. at each end. This set bears the weight of the shaft sets below, and usually of the gallows frame. Posts resting on blocks are placed under each end, and diagonal braces are then placed around the shaft to carry part of the weight and prevent the set from moving. Figs. 3 and 4, Plate I, show the collar set of a two-compartment shaft, with the diagonal braces and posts.
The size of the guides varies greatly. At first 4 by 6 in. guides were used almost universally in the camp, but lately the size has been
increased to 4 by 9 and 5 by 9, held by 7/8 by 8 or 7/8 by 9 in. lag screws. The larger size guide can stand heavier loads and greater shocks, and two lag screws are used in each timber; the holes, two in number, are placed diagonally across the guide, and, after a number of years, they are placed diagonally across in the other direction, giving fresh timber for the screws to hold to.
Guide posts are vertical posts running behind the guides to give them more support. They may be seen in Plate III. They are framed into the centers and end plate of the shaft. Where used they are carried in the main hoisting compartments, and sometimes in the auxiliary hoisting compartment, but not in the pump compartment. They are the same width as the center, and usually 12 in. in the other direction.
Guide girts are girts running horizontally between posts and equidistant between the centers of the shaft. They are framed into the posts of the shaft, as seen in Plate II, giving support to the guide and also helping to take the side weight of the shaft. They are being used at the Granite Mountain shaft of the North Butte company, and will be used in the retimbering of the Neversweat shaft of the Anaconda company. In heavy ground the guide girt would seem to be more satisfactory than the guide post.
To allow for the end plate of the shaft pushing in, 2 in. is often allowed in the outside hoisting compartment. To make the distance between guides the same size in the two compartments, a 2-in. block of wood is placed between the guide and the end plate of the shaft. As the end plate comes in, the block is cut down or removed until the guides are again the right distance apart. This is called a filler. Sometimes, as at the Badger State mine, the filler may be a vertical post carried up the shaft against the end plates, and bolted with 7/8-in. bolts to the guide posts. At this mine a 10 by 12 in. post, in 20-ft. lengths, is carried up alongside the guide posts, and a 6 by 12 in. post is carried up in the other hoisting compartment on the opposite side. At the Moose shaft these fillers are carried behind each guide, the same size for both sides of the hoisting compartment, and are, I believe, 4 by 12 in.
In sinking a shaft spliced wall plates are often used. In heavy ground the ground cannot be kept open to a depth to allow a full length wall plate to be turned in a shaft so as to be brought into place and, as long length timber is hard to obtain, the splice is coming into more general use. Four hanging bolts must be used on a side with spliced wall plates. The splice, shown in Plate V, Fig. 1, is the one which finds most general use. In this the center is supported by the wall plates while the set is being blocked. Fig. 2 shows the splice when one side of the shaft is to be raised. It will be noted that the mitre is left out and the framing is straight. This is because dirt getting into the straight joint will not throw it out of line
as much as it would the mitred joint. When the shaft is being sunk a block of wood is placed in the opening under the center, and, when the other half of the shaft is raised, this block is chopped or picked out and the other half of the wall plate placed in position.
Fig. 3 shows a spliced joint very easy to frame. The center in this case, however, has to be supported while the set is being blocked. This is usually done by nailing it to the wall plate before the posts have been placed in position. At the Tropic shaft the set is blocked on both sides of this center temporarily; the end blocks are then set, and the blocks on each side of this center are then taken out and the set brought to line and blocked permanently. A temporary post is sometimes placed under the center to hold it up while being blocked. This method of splicing is cheaper to frame, but a little more expensive to put in place.
Fig. 4 shows the method of splicing at the High Ore mine. A 2-in. block is nailed to the center before it is sent down into the mine and the corners of this set are held together with pins. The other half of the wall plate can be easily pushed in, as the distance is small. This is not as strong a splice as the one shown in Fig. 1, but would be excellent where a small shaft is being sunk and there is a possibility that more compartments will be added. On the whole, it may be said that it is cheaper to sink the whole shaft than it is to sink part of it and raise the balance. In soft ground where it is not desired to open up too much country at once, the Anaconda company finds it an advantage to sink and raise.
The timbering takes place from the top of the muck pile whenever possible. That is, the dirt, after blasting, is mucked down to about 10 ft. below the last set. The new set is hung and blocked; then mucking is continued. The men do not have to build any staging to drive the wedges, which are driven from below. If the timber is kept close to the bottom it is sometimes found after blasting that the muck is pushed up to within a few feet of the last set of timbering. If the men could work only in one compartment mucking would be very slow; so, to avoid such a possibility and to aid in turning the timbers to get them in place, one of the centers of the shaft on either side of the hoisting compartment is left out on the bottom set. A 2-in. strip is cut from the post and the center is pushed in through this opening and hammered down into place when the set below is put in. A block made to fit the opening in the post is then nailed into place, completing the set. This may be seen in the Rainbow shaft set, Plate IV, and the Granite Mountain set, Plate II. In the Granite Mountain shaft it will be noticed that the guide girt is also left out. The guide girt is slipped in from the side; then it is wedged on the end and the side weight of the shaft soon makes it solid. The center and girt are always kept within one set of the bottom timber; this style of center is framed with a dovetail.
Where the guide post is framed into the center with a mortise and tenon, the center cannot be slipped in from the top. It is then framed with straight sides and is pushed up from the bottom and held in place by the posts of the set below when they are being placed. This may be seen at the Mountain View mine. This method of pushing the center up from below is sometimes used at other shafts on account of the cheaper framing. The first method is considered the best for holding out the center. It sometimes happens that the wall plates of the shaft have been
pushed in so that the center is hard to put in place. A small bar of 3-in. pipe, similar to a stoping bar, is then used to spread the timber.
The method of blocking and lagging the set may be seen in Plate VI. Where the distance is small,—say, not over 1 ft.,—a single block is placed between the set and the wall, the wedging being done between the block and the wall. When, however, the ground breaks back farther, a block of about 5 in. thickness is placed back of the center and toe-nailed from above. Blocks of the same size are placed along the side and toe-nailed. A stringer the length of the shaft is then placed along the side and nailed to the blocks. Blocks are again placed, and then stringers as needed. The wedging is then done between the blocks and stringers. The wedges should be driven from below as well as above. An upright post is then put in place and wedged to the blocking above to prevent the blocking below from being knocked out by the blast. After the set has been hung and the posts are all in place, the set is generally raised up by placing a pinch bar under the hook on the hanging bolt; then the set is raised and the nut run down as far as possible by hand. In case blasting chains are used the bar may be supported by hooking the chains around
the hanging bolt above. In case bolts are used a U-shaped bar of ¾-in. iron, with hooks on the side, is made for this purpose. The top end of such a bar may be seen in Plate X, on the right-hand side of the bucket.
Two-inch fir is used for lagging. A strip is placed horizontally, back of where the lagging will come and about half-way between wall plates. The shaftman uses his ingenuity to find some method of support for this stick. The lagging timbers are then placed in and wedged from the back, the shaftman leaving one plank out for this purpose. This last lagging is wedged from the inside of the shaft. Two-inch square strips support the lagging and are nailed to the wall plates before they are sent into the mine.
Blasting logs protect the timber from being cut up by the blasting. They are fastened to the bottom set with bolts or chains, as shown in Plate XI, which was taken in the bottom of the Rainbow shaft. Timber 8 by 12 in. is often used for this purpose; or a 14-in. stull, split lengthwise, makes an excellent blasting piece, as the round surface tends to throw off the rock. One-quarter inch iron and 3 by 3 in. angle iron, placed along the edge of the shaft timber, are also used. The iron blasting pieces, however, are twisted out of shape by heavy blasting and must be sent to the surface frequently to be straightened by the blacksmith. Where bolts are used to hold blasting pieces, they are of 1-in. size, and the head of the bolt is always placed down. Plate VI, Fig. 3, shows the method of tightening a blasting log held with a chain. The blasting log is held up, the chain is hooked over the timber, and a block is then slipped under the chain. Wedges are then driven under the block; a few blows with an ax makes them tight, and a side blow loosens them again when necessary. This is probably the best and most reliable method of holding blasting logs.
Figs. 1 and 2, Plate VI, show what is known as a shaft bearer. About every 400 or 500 ft. the shaft is widened; sills are laid along the side of the shaft as shown, and cross pieces are then bolted under the end plates and centers of the shaft, resting on the sills. The shaft set is then blocked and wedged on top of these cross pieces. Regular posts are then placed under the bearers when sinking is resumed. Shaft bearers have not come into general use, although they may be seen at the Leonard and Badger State shafts of the Anaconda company. The object of the bearer is to prevent the shaft from sinking on one side and to give additional support to the shaft below when sinking.
I will not enter into a description of any particular shaft, as it is hoped that the drawings will make themselves clear.
Sinking Equipment and Methods
The No. 3 Rand, E 44 Sergeant, and jackhamer drills are the ones most in use in shaft sinking. With the reciprocating drill the tendency is toward long rounds, 10-ft. rounds being broken where the rock is hard; with the jackhamer drill a 5-ft. round is drilled. All sinking is done with cross bars where the reciprocating drills are used, and these bars are generally made 6 in. longer than the width of the shaft timber, while a longer bar and a shorter bar are used for special set-ups. The bars are made of extra heavy 4-in. pipe.
For cleaning the holes sand pumps are used. (Plate XII.) These are made of ¾-in. pipe with a bend near the end. The shaftman places his hand over the end as the pipe is raised, causing a suction, taking it away as the pipe is pushed down. When this is done rapidly it lifts the sand out of the bottom of the hole. The sand pumps are made in different lengths and sizes to suit conditions. Blowpipes are used for blowing out the holes before blasting, and are usually made of ¾-in. pipe, so that small rocks will have a chance to pass.
As to the placing of holes, Plate VII will show the general method, as there are no ironclad rules. If the ground is breaking out too far on one side the holes are drawn in, or perhaps one may be cut out altogether. It is generally arranged so that each machine has the same number of holes to drill, and this often causes rivalry among the different runners. Both 40 per cent, and 60 per cent, gelatine powder are used, the 60 per cent, being usually used in the cut holes only. In some shafts the whole round is blasted together, but, with 10-ft. rounds, generally the cut holes and one or two rows on either side are blasted first; thus making sure the round will do its work. The cuts are sometimes mucked clear to bottom and the bottom of the cuts blasted with the rest of the round. At other places it is customary to muck down far enough to see that all of the holes have gone and then shoot the rest of the round. The men in this way are twice on the top of a fresh muck pile, and only pick bottoms once to a 10-ft. round. Sometimes a set of timber is placed after the cut holes are blasted and then another after the rest of the round, making both very nicely from the top of the muck pile.
The jackhamer drill is finding its application in certain kinds of rock. The air is blown out through the hollow drill, keeping the holes free from cuttings; in soft ground the holes are likely to plug. At the Pittsmont mine a hole is drilled in the steel sidewise about 1 in. from the lower end of the drill, so that, if the hole in the end becomes clogged, the air blows out through the side, keeping the hole clean above the last inch of the drill. In soft ground the drill bits are enlarged to take 1.25-in. powder. In hard rock, if the bits are enlarged sufficiently to make the hole large enough for 1.25-in. powder, the drilling becomes too slow, while the 7/8-in. powder will not break to the bottom cleanly, and then picking bottom is a slow process. The application of these drills seems to be in rock which is neither too hard nor too soft. A heavier drill of this type might overcome these difficulties if it bored a hole large enough for 1.25-in. powder fast enough in hard rock.
The fuse is doubled for blasting the holes; two nails or hooks are set the right distance apart and the fuse is wound tight around them, and then cut at one of the nails. Caps are put on both ends of the fuse; the crimp in the fuse, made by the other nail, marks the place where the fuse is
to be spit, and the fuse is not cut until that particular fuse is spit. The fuse for the different rows of holes is not cut in different lengths, since the work of spitting gives plenty of relay between fuses.
In the larger mines sinking takes place under a working shaft, the shaft being bulkheaded under the hoisting compartments and several hundred feet above under the auxiliary compartments. A lining of 2-in. or 3-in. plank is run, separating the auxiliary and main hoisting shafts between these two bulkheads. The sinking engine is then placed so it may be served by the main hoisting cages. This bulkhead is often made by crossing the shaft with several layers of 10 by 10 in. timber, removing the shaft lagging for several sets above and filling it with rock. Sometimes a timber bulkhead is placed, as in Fig. 4, Plate VIII. A good method is shown in Fig. 2, Plate VIII. A block of ground is left under the hoisting compartments for about 30 ft., when the shaft is lengthened out to the full. When sinking is finished this portion is raised, completing the shaft. This may be seen at the Badger State and Mountain Consolidated mines of the Anaconda company.
Handling Shaft Water
Some of the shafts of Butte, where the ground has been drained, are being sunk without pumps. In this case the water is bailed into the sinking buckets with pails. The bucket is then hoisted and dumped into a car. The car can be run out away from the shaft, and the plug pulled out; it will empty itself by the time the next bucket of water is ready to be hoisted.
The 10-7-5-10 Knowles and the 9 b Cameron pumps are generally in use in sinking work. It is becoming the practice, where pumping with compressed air, to force the exhaust air back into the water column. A check valve is used to keep the water from running back into the cylinder of the pump when the pump is shut down. A valve is placed so that the air may be exhausted into the atmosphere. A valve should be placed in the water column, to allow the column to be drained in case the water pressure is too great to allow the pump to start. A pump so rigged, but for a short lift, and without the column valve, is shown in Plate XIII. It is shown with the 6 to 4 in. nipple on the suction, to make the flanges standard, and with the expansion joint on the water column.
Pumps run in this way are noiseless and will not freeze in a cold shaft because the air leaves the cylinders of the pump still under pressure. The advantages to be gained by this method are that the column is not under such heavy pressure and is less liable to breaks, and the pump will give less trouble with the packing. A 200-ft. lift can be made very nicely with a 10-7-5-10 Knowles pump. The column pipes are flanged in 10-ft.
lengths, and care should be taken to keep the flanges away from the wall plates. They should be started and held vertical about half-way between sets. Expansion joints should be placed every 200 ft. in the water and air lines. The pump has an expansion, as shown in Plate XIII, which is lowered with it. This takes care of any variation in the 10-ft. lengths
of pipe. The clamps on the water column should be kept 30 to 40 ft. above the pump. In case the pump is not lowered to a position exactly under the pipe, the pipe can be swung over to the pump.
There are several methods of lowering pumps, the favorite one being with chain block. The chain block is fastened to a cross piece several sets above, which is carried down along with the chain block. A hand- operated winch, set in the pump shaft usually at the first station, and a rope leading down to the pump, are used. A separate bell line gives the man at the winch the signal to hoist or lower the pump. The pump may be lowered with a large-size Manilla rope, as shown in Plate VIII, Fig. 1. This method is very fast. The rope is wound around the timber and tied after the pump is lowered, so that, if the pump is lifted off the wall plate by the blasting, it will not fall to the bottom.
To keep the pump from being blasted a bulkhead is carried along and kept under the pump. As these bulkheads have to be passed down by
hand every time the pump is lowered, the timber should be in as light pieces as possible, and 5 by 10 in. or 4 by 10 in. set on edge makes a nice size for this purpose. The bulkhead is designed by the pumpman to suit existing conditions. An end view of a typical bulkhead is shown in Plate VIII, Fig. 3. It is wedged tight in place, and, after the blast, it is loosened so that it may be easily taken out.
The suction of the pump extends through this bulkhead to the sump below; consequently the bulkhead is made so that it can be closed for each blast. Before the blast the suction is disconnected and pulled up above the bulkhead by a double block and tackle. One way to make this hole for the suction is to have the pieces below the pump wedged so they can be pulled up and out; or they may be kept loose so they can be spread. Another method is to take two 10 by 10 in. timbers and cut a 5-in. hole in each, so that, when they are placed under the pump, they make a 10 by 10 in. hole for the suction. During a blast a block is placed
over the hole and under the pump, to prevent rocks from flying up. In some places the suction is pulled just high enough to leave the strainer in the hole. The strainers for the suction hoses are made at the mines and consist of a piece of pipe of the same diameter as the suction, about 14 in. long, bored full of ¼-in. holes, with thread on one end, and flattened together on the plain end. Timbers 10 in. square are very heavy when they are waterlogged, and most pumpmen prefer the first method. The suction hoses are usually wound with ¼-in. Manilla rope, as in Plate XI, to prevent wear. Short lengths of flanged pipe are kept with the pump, and are placed between the suction hose and the pump as the rock is being mucked down. As the suction hose can be lowered with the block and tackle, this is an easy matter. A leak in the suction is a great annoyance, and about the only way to find it is to place the ear near the flanged joints and listen for the sound of the leak.
Rock Handling
Sinking engines have every possible speed, depending upon the depth they have to work. The type of cage shown in Plate XVII is generally
used for sinking; the long shoes along the side and the sinking shoes above can be seen. The corner bars of the cage are drawn in so that men can step off the cage on to the timber. In Plate XVII a regular mine cage is fitted for sinking, having sinking shoes. The sinking bucket with straight sides has come into almost universal use. These buckets are about 2 ft. 6 in. across the top, and 3 ft. high, holding one mine car of rock. Barrel-shaped buckets and buckets wider at the top than at the bottom have not found much favor. The bucket must be wide at the bottom so that it will sit steadily on the muck below, buckets with small bottoms being likely to topple over and hurt the men. There are many novel methods of securing the bucket; the best and most reliable one, in my estimation, being shown in Plate XV, which is known as the drop pin. Another method is shown in Plate XII, Object 2, this being
a link flattened for about 0.75 in. on one side, and which can be passed into the hook shown, the chain being passed around the bail of the bucket. Plate XIV shows two hooks turned in opposite directions, this system is being used at the Tropic shaft of the Anaconda company.
The cars should be large and have strong bottoms. Large boulders are lifted into the bucket by means of a rock chain attached to the cage, and dumping these into the cars soon breaks them if they are light. Plate XV shows a common mine car with raised door, so that large boulders may be dumped out of it. A rock chain may be seen in Plate XII. It is well to have several of these made in different weights of chain, and 0.5-in. chain is a good average size for this purpose. A chain ladder is also shown in Plate XII, this being made of 0.5 by 18-in. bolts, with 3/8-in. chain and 0.75-in. pipe cut to go over the bolts between the chains. The ends of the bolts are riveted after the nuts are in place; in case a step is broken it is easily replaced. The chain ladder should be hung so that, in case anything should go wrong with the sinking engine, the men can climb up the chain ladder and out. In some places this is lengthened to about 35 ft., and the wooden ladders are kept down to connect with the chain ladder.
Miscellaneous Details
Where heavy ground occurs in the shaft, and the timber is being pushed in and broken, jacket sets are placed outside the regular shaft timbers. (Plate IX.) This gives an opening around the shaft, where men can work easing off the timber while the shaft is in operation; these jacket sets are raised alongside the shaft, although in a few instances they have been carried down with the sinking. The four small compartments at the corners are used as chutes, and discharge at the station below. The rock is generally very fine, and is picked out in easing off the timber. If any of the outer jacket timbers break they can be easily replaced without disturbing the shaft.
Sometimes the shaft sets themselves are pushed out of line. Vertical stringers are then run up and down the shaft, being wedged to three sets all around. The jacket timber of the middle set can be then wedged and held from coming in when the blocks between them and the shaft are taken out. The shaft set is then pushed over with a jack bar to its right position and new blocks are fitted to go between the shaft set and the jacket set. This is then repeated on the next bad set. In raising alongside the shaft for the jacket sets, a set is finished around the shaft before commencing another. The place where the ground is the heaviest is selected as the starting point for the raising; what natural support the better ground can give is thus taken advantage of.
For signals, a 0.75-in. Manilla rope, attached to a bob, is generally used, and the shaftman ties a loop on the end of the rope to make it easier to pull. When the men are being hoisted, after spitting the holes, this loop is hooked on the cage and the rope is thus hoisted away from the blast. Rope bells can be used successfully for 2,200 ft. in depth, but, after that, a combination of electric bell and rope bell must be resorted to. Electric lights are a great aid in shaft sinking, as they leave the men unencumbered with candlesticks, etc. Especially is this true in drilling, when the exhaust of the machines makes it hard to keep a light of any kind. When timbering, candles are used to give light back of the timber. An old reel may be used to hold the light wires. A couple of old pieces of shovel handle nailed about 5 ft. apart may be used for the same purpose. To protect the lights from rocks falling from above, a heavy reflector is kept above them. Electric lights are particularly useful where electric
engines are used in sinking, as they give notice to shaftmen of any interruption in the current.
To ventilate the shaft, 1-in. lining boards are run down, separating two compartments of the shaft. These boards are cut to go between centers, and cleats are nailed on both their sides, at top and bottom, to hold them in place. In order to make a circulation, a ventilating stack, called an upcast, is placed at the top of one of these compartments running up alongside the gallows frame. Where the shaft is to be sunk under hoisting shafts, the ventilation is much harder and blowers are sometimes used to furnish air. The time it takes smoke to clear away is time lost in shaft sinking. In some places the cages are run up and down through the shaft after blasting to help clear away the smoke.
I would like to ask Mr. Braly if he has any information as to the relative efficiency of the sinking pump, using it as he refers to it, discharging the exhaust into the water column or otherwise.
I have never gathered any information on that point. It is a question of getting the work done. In driving the shaft, using that method, we find it easier on the men and everything else. In the bottom of the shaft, if you exhaust back into your column, it is a quiet shaft. Another thing is the freezing: if you are sinking with air in your pump, you will find it is liable to freeze, and in that case as the air is still under compression it will not freeze the pump. The difference is very small if there is any. But, as might be expected, the pump is a little less efficient when exhausting the air into the column.
I suppose all of us know what a pump in the bottom of the shaft is. My experience has been, although I have no figures, that the capacity of a pump is quite considerably decreased if you are pumping, say, from a depth of 200 ft. through a No. 7 Knowles pump, when you exhaust the air into a column, but, on the other hand, it is also my impression that we can raise the water to a little greater distance. I would like to get some figures from somebody who has made actual tests.