In the Merrill-Crowe Zinc Precipitation, the pregnant solution tank collects the gold and silver bearing solution recovered from other circuits of the plant: thickener overflow; primary and secondary filtration? and the Argentite circuits. Normally these solutions contain very little solids content (15-100 ppm), however, even this small amount of solids is sufficient to inhibit efficient gold and silver recovery.
The first stage of pregnant solution treatment is the removal of these solids using a vacuum precoat clarifier, which reduces the solids content to approximately 5 ppm. Dissolved oxygen is necessary for cyanide to dissolve the gold and silver and so the dissolution part of the process has tried to maintain a high dissolved oxygen level. However, in order to precipitate gold and silver using zinc dust it is necessary to remove this oxygen (or else the gold and silver remain in solution and are not precipitated). The oxygen is removed by subjecting the solutions to high vacuum and drawing out the oxygen. Zinc by itself is not very efficient at precipitating gold and silver from solution. However, a zinc-lead couple (like a very small battery) improves the zinc’s precipitating efficiency. The couple is made by adding a small amount of lead nitrate to the pregnant solution, which reacts with the zinc to partially coat the zinc dust with a fine lead film. The zinc becomes very active and precipitates the gold and silver according to the following reaction:
2Na [Au(CN)2] + zn > Na2Zn(CN)4 + 2Au
and
2Na[Ag(CN)2] + Zn > Na2Zn(CN)4 + 2Ag
The solution with the gold and silver precipitate is pumped through a filter press where the gold and silver solids are removed. The barren solution is discharged to the barren solution tank. The barren solution is recycled as process solution throughout the rest of the plant where any remaining free cyanide can be utilized. This section is intended to be read in conjunction with Flowsheet and Piping and Instrument Diagram.
The Merrill-Crowe Circuit is designed to operate to the following criteria:
Degassing Pressure ——————–20″ Hg vacuum
Zinc Dust/Gold Ratio ——————1.5 gm zn/gm Au
Zinc Dust/Silver Ratio —————- 2.5 gm Zn/gm Ag
Lead Nitrate —————————- 10% of Zn b.w.
Detailed Merrill-Crowe Zinc Precipitation Process Description and Control
Thickener overflow and filtrate from all drum filters flow into the 6 meter diam. x 4 meter pregnant solution tanks. The two tanks are connected with a 10″ diameter pipe, with no isolation valve, hence these two tanks are considered as one tank. The thickener overflow flows into the first tank at a normal rate of 36.9 cubic meters per hour, and the combined filtrate from the vacuum receivers flows into the second tank at a rate of 68.4 cubic meters per hour. A multi point level switch, mounted through the top of the first tank, has four solution level switch points set for high high (LSH) , high (LSH), low (LSL) and low low (LSL). All points alarm at the mill control panel annunciator. The high and low alarms should be interpreted as an impending problem; either the clarifier or the filtrate feed pumps are not functioning, or the throttling valve on the outlet line requires adjustment to balance the system. Under normal flow rates the high-high alarm will sound ten minutes after the high alarm if the problem is not alleviated, indicating a tank overflow condition. If a low-low alarm occurs, the tank will run dry in approximately 20 minutes. A local level indicator (LIX) has been provided in the form of a pressure gauge mounted at the bottom of the tank. All of these instruments are located on the first tank, but measure the level in both tanks as the tanks are piped together.
Pregnant solution is pumped by the 7.5 HP 6″x4″ clarifier feed pump at a rate of 105.3 cubic meters per hour to one of two vacuum precoat clarifiers. The two clarifiers are cycled; while one is operating, the other is being cleaned and prepared for operation.
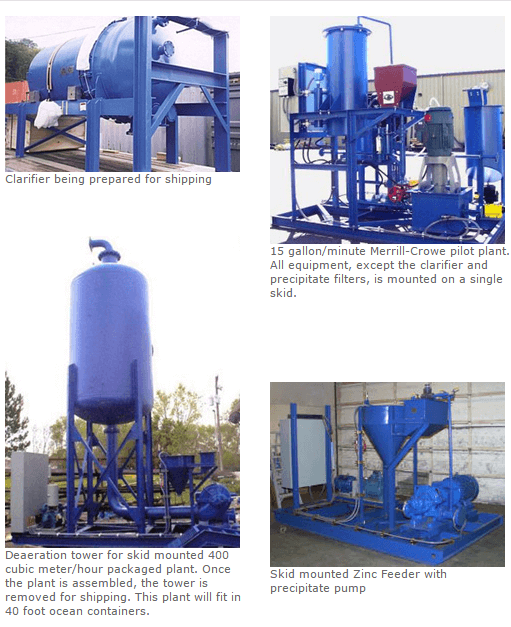
The pregnant solution enters the clarifier and is drawn through the 19-30 square foot leaves of the clarifier by a 5 HP 5″x5″ clarifier discharge pump. Flocculant can be added to the pregnant solution, just prior to the clarifier, to aid clarification if desired. A filtering mat of diatomaceous earth, referred to as precoat, is continuously added to the clarifiers to keep the coat porous and permit longer filter cycles. This continuous feed of precoat is known as body feed and is educted, with barren solution, into the inlet manifold of the clarifier. As solution flows through the clarifier leaves it encounters resistance in passing through the many small openings between the precoat particles. As the suspended solids in the pregnant solution are trapped in the pre-coat, the leaves begin to blind and resistance to flow through the leaves increases. This increase in resistance is measured as a pressure drop across the clarifier with a pressure gauge at the clarifier outlet. A level control valve at the clarifier inlet is throttled by a float mechanism in the filter. As the leaves begin to blind, the level will rise and the control valve will gradually close, slowly decreasing flow into the clarifier. At this time the blinded clarifier should be taken out or service and the other clarifier put into service. If these warnings are ignored, a low pressure (vacuum) switch at the clarifier outlet will stop the associated clarifier discharge pump on a high vacuum. The blinded clarifier taken out of service should be cleaned and precoated for the next cycle.
After the blinded clarifier has been taken out of service, the contents of the filter must be drained to the filter feed pump box by opening the lower drain plug valve. Turn on barren solution to the clarifier spray bar and rinse the plates. The spray bar is equipped with a small motor which turns the spray bar, turn this on also. After the plates are rinsed, drain the filter boot again. The clarifier is now ready for precoating. The procedure for precoating follows in the penultimate paragraph of this section.
The operating clarifier discharge pump delivers the clarified pregnant solution to a 5 meter diam. x 6 meter clarifier solution tank. This tank is equipped with a multipoint admittance level switch, which has a high point and a high high. Both will alarm at the mill control panel annunciator. The high alarm should be reacted to immediately, as it has been calibrated, at normal flow rates, to give a 7 minute warning before the tank overflows. The high high switch will alarm on an overflow condition and is interlocked to stop the operating clarifier discharge pump.
Clarified solution is pumped out the clarified solution tank to the 5′ diameter x 10′ high deaerator by the 15 HP 6″x4″ deaerator feed pump. The flowrate into the deaerator is controlled by the level in the vessel through the controller. Level is measured by a differential pressure transmitter, with diaphragm seals, which measures the pressure difference between the upper and lower deaerator outlets, and sends a 4-20 mA signal to a level controller. The controller sends its output signal to an electrically operated butterfly valve to maintain the setpoint level. Two level gauge glasses installed in the deaerator will give a local indication of level.
As the pregnant solution in the deaerator flows down over the horizontal baffles it is subjected to a high vacuum which removes the oxygen from the solution. The vacuum applied to the deaerator is supplied by the filtration circuit vacuum pumps. The vacuum in the deaerator is measured with a pressure gauge and can be adjusted with a manually operated butterfly valve.

Deaerated pregnant solution is pumped out of the bottom of the deaerator with a 40 HP 4″x3″ in-line precipitate filter feed pump. Zinc dust and lead nitrate, mixed with 3.5 cubic meters per hour of barren solution in the zinc mix tank, are introduced into the suction line of the precipitate filter feed pump. Gold and silver precipitation occurs as soon as the zinc and lead nitrate are added to the pregnant solution. To prevent oxygen from entering the deaerated solution, the precipitate filter feed pump is submersed in barren solution in a pump gland seal tank. A pressure gauge is located at the inlet to the filter feed pump, and at the zinc slurry line entering the pump suction.
The precipitate filter feed pump delivers the gold and silver precipitate at a rate of 108.5 cubic meters per hour to two 36″ x 36″, 25 plate precipitate filter presses. An orifice plate and flow transmitter monitor slurry flow, and a flow totalizer in the mill control panel totalizes the amount of precipitate being fed to the presses. A panel mounted counter displays the totalized amount. A high pressure switch will alarm at the mill control panel at a pressure of 50 psig.
The filter presses serve to filter the zinc/gold/silver precipitate from the slurry. The plates are precoated with the same precoat system used by the clarifiers. The two presses can be operated in parallel or series; however, under normal operating conditions they will operate in parallel, with one being in service while the other is being cleaned and prepared. The pressure filter cycle time is approximately every two days.
The slurry line from the precipitate filter feed pump divides into two separate filter press feed lines. Manually adjusted butterfly valves can be operated to direct flow to either or both filter presses. A pressure gauge in the slurry line prior to the line dividing to the two filters, can be monitored by personnel, as it will give an indication of when the operating press(es) is becoming loaded. As the slurry enters a press, the solids are trapped in the precoat, and the now barren solution flows out of the press to the barren solution tank. During the filtering process, the plates will load, much as in the clarifiers, as the precipitate is trapped in the precoat the resistance to flow through the plates increases creating an increase in pressure drop across the press. A pressure gauge at the inlet to each filter will give local indication of the increasing pressure. The pressure at the inlet of a newly cleaned filter will be approximately 10 psig and will rise to approximately 50 psig when the press is full. At this time the loaded press must be taken out of service and the other cleaned nd precoated press put into service, by adjusting the appropriate butterfly hand valves.
Once feed to the loaded press has been discontinued, the plant air inlet ball valve is opened to blow air through the press to remove any excess liquid or barren solution entrained in the filter cake and to separate the cake from the plates. The filter cake from the press will have a final moisture content of approximately 50% solids. The press is then opened and the cake is manually scraped off the plates into a collection chute below the press. The chute delivers the cake to a screw feeder which feeds the rotary dryer described in the following section.
Both clarifiers and precipitate filter presses must be precoated after cleaning. Only one clarifier or filter can be precoated at one time. The precoat must be batch mixed, prior to its use, in the precoat tank. Barren solution and dry diatomaceous earth (precoat) are added to the tank, and thoroughly mixed with the 3 HP precoat agitator. When mixed, the 7.5 HP 6″ x 4″ precoat pump is started, ensuring that all valves feeding precoat to the filters and clarifiers are closed. The precoat will recirculate back to the precoat tank. It is important that this pump not be dead-ended. The precoating procedure for the clarifiers is slightly different from that of the filter presses.
For the clarifiers, open the appropriate valves to allow the precoat batch to fill the clarifier tank. The precoat pump can now be stopped. Adjust the valves at the clarifier to allow flow to recirculate through the clarifier and its discharge pump. Turn on the clarifier discharge pump and allow
recirculation until the recirculating precoat solution is clear, indicating that the leaves are now coated. The clear solution must be left in the clarifier and the pump left running on recirculation, until the unit is returned to service, to prevent the precoat from falling off the leaves.
For the precipitate filter presses, the precoat pump becomes the recirculating pump. Mix up a batch of precoat as described above, and start the precoat pump on recirculate back to the pre-coat mix tank. Ensure that the precipitate filter press is closed after discharging the cake. Adjust the
appropriate valves to allow precoat mixture to circulate through the press and back to the precoat mix tank. Allow circulation to continue until the precoat solution is clear, indicating that the plates are now coated. Turn off the precoat pump, and allow the clear solution in the lines to drain back to the pre-coat mix tank.
https://www.911metallurgist.com/silver-sulphide-leaching-filtration-circuit-startup-shutdown-procedures
https://www.911metallurgist.com/merrill-crowe-zinc-precipitation-startup-and-shutdown-procedure
Zinc Dust and Lead Nitrate
Zinc dust is supplied in 45 kg pails and must be manually fed into the zinc dust feeder. The zinc dust feeder will automatically feed the zinc dust into the zinc mix tank.
NOTE: While the mill is operating, the zinc dust feeder must never be allowed to run empty. It is imperative that the feeder has an adequate supply of zinc dust at all times. The lead nitrate reagent mix system is identical to those described for the flotation reagents. Dilute lead nitrate is pumped, with one of two metering pumps, to the zinc mix cone.