Table of Contents
The object of this paper is to discuss the factors and conditions that affect the observed values of the melting points of refractory materials and to describe practical methods for the determination of these points. While it appeared to be necessary to discuss some of the general properties of silicates and refractories, these subjects have been entered into only in so far as they relate to the melting point and its determination.
Refractory materials such as fireclays, firebricks, and minerals generally, may be considered to be composed of compounds of metallic oxides, solid solutions of the oxides, the pure oxides, or mixtures of the three classes together with small amounts of a variety of chemical compounds. The oxides of silica and alumina occur most commonly in refractory materials; in combination with these, oxides of the alkali earth, the alkali, the iron group, and the rare earth metals are frequently found.
Meaning of Melting Point
In its strictest sense, the term melting point is applied to the temperature at which the solid and liquid phases of a pure crystalline substance can remain in equilibrium; at the melting point, there is usually a discontinuous change of a number of its physical properties. In the case of those refractory materials that are either amorphous or heterogeneous mixtures or compounds of oxides or other substances, the term melting point is not a definite temperature; the change from the solid condition to one in which the material will flow is gradual over a temperature and time interval. In addition, physical and chemical reactions, which are not equilibrium reactions, often take place during melting.
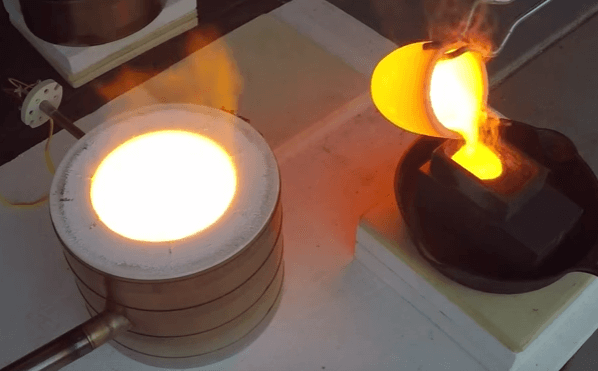
With the rise in temperature of a refractory material, the first phenomenon of importance usually observed is the sintering or vitrification of the particles; that is, the edges of the particles first become soft and liquid and the particles stick together even though all parts of the material are at the same temperature. As a result of surface tension, the soft edges of the particles become rounded off. Sintering may also be produced by the fusion of the lower melting-point constituents, the formation of eutectics and solutions, and the chemical reaction of the constituents. If, as a result of these phenomena, a substance of sufficient fluidity to diffuse through the mass is formed, the whole body may flow while the solid particles are held in suspension. From the point at which the substance begins to sinter, it may become more viscous gradually, over a long range in temperature, until it flows, or it may soften and flow distinctly over a short range in temperature. While these materials have a more or less definite temperature interval of melting, or melting range, their softening is also a function of the time.
If the refractory material is a pure crystalline compound, it will have a definite melting point, in the strict sense. Nevertheless, there are such pure refractory compounds as quartz and albite, which soften very slowly and the melting interval of which is an interval of time; that is, a long time is necessary to attain equilibrium between the crystalline solid and the liquid. For these substances, the temperature time method is not suitable for the determination of the melting point. For practical and technical purposes, the criterion of marked flow is used for such substances. On account of superheating while melting, the melting point found by this method may be much higher than the true melting point, as in the case of quartz, where it is about 50° C. higher.
By the term refractoriness of a refractory material is usually implied its resistance to the action of heat or, more definitely, its ability to retain its shape at high temperatures under accurately specified conditions. The term “refractoriness’’ is broader and more general in meaning than “fusibility,” which is usually measured by the softening point or fusing point. The latter refers to the temperature at which the material begins to lose its shape and flows. The last mentioned phenomena ordinarily take place in several stages over a range in temperature. The sintering of the material produces shrinkage and bending; but this phenomenon should not be considered as taking place in the melting range.
Assuming that the sample is in the form of a cone or cylinder, the beginning of the deformation, bending, or squatting of the specimen marks the first stage of melting; the second stage begins when the material has fused into a lump or ball or, in the case of a cone, when the apex has touched the base; the third stage begins when the lump has flattened out and is fluid. Those molting stages occur over temperature intervals of varying magnitude, depending on the substance; in many cases of more or less pure compounds, the material melts at a definite temperature or over a very small temperature interval and thus it does not serve a useful purpose to demarcate the melting stages. That particular stage in the melting range which is to be considered as the melting point or softening point depends on the material and the extent of softening that will manifest the most information concerning some limitations of use of the material or the conclusions to be derived from the melting-point test. From a general and practical standpoint and wherever the conditions of use of the material are not specifically known, the knowledge of the temperature at which a marked and distinct flow of the sample begins is most important and useful as a fixed temperature as well as a comparison temperature.
The temperature at which a marked flow begins usually occurs after the start of the above mentioned first stage of melting. Especially with samples in the form of a cone and cylinder and with rapid rates of heating, the beginning of the marked and distinct flow is seen to occur when the sample is about half bent over or halfway between the first two stages.
In general, then, the practical definition of the melting point of a refractory material is identical with that of its softening or fusing point and is arbitrarily stated to be the temperature at which a marked flow of the material begins. In terms of the deformation of a cone or cylinder, the melting point is halfway between the temperature at which the deformation begins and the temperature at which the material fuses into a lump or ball or is completely bent over. For most refractory materials, the melting point is, under specified conditions, reproducible and definite enough to be worth determining.
Factors & Conditions Affecting Observed Melting Point
Chemical Composition
It is evident that the chemical composition of a refractory material will affect, to a large extent, the observed melting point. While attempts have been made to determine a relationship between the melting point and composition of fireclays, no definite and complete connection has been found. In fact, no equilibrium diagram can be established for such complex and heterogeneous mixture as fireclays and firebricks; first, because of the large number of components, and, second, because of the inhomogeneity of the chemical constituents. For the same reasons it is difficult to determine empiric relations between the observed melting point (which is not an equilibrium temperature) and the composition. Nevertheless, chemical analyses will often indicate the relative refractoriness of different materials. Of course, where we have combinations of chemically pure oxides in which are formed definite chemical compounds, solid solutions or eutectics, the temperature versus composition or equilibrium diagrams have been established for a number of groups of oxides, such as for the combinations of lime, alumina, magnesia, and silica.
The addition of an impurity to a refractory material usually lowers its melting point. For instance, in fireclay substances, the addition of sodium, potassium, iron, titanium, calcium, or magnesium compounds produces a very marked depression of the melting point; the addition of silica to fireclay materials decreases the refractoriness while the addition of alumina increases it.
Size of Particles and Shape and Position of Body
It is well known that, within certain limits, the smaller the particles of a refractory material the lower may be its melting point. The softening of the surface of the particles takes place at a lower temperature than the softening of the whole body en masse; in other words, the particles sinter together before the body flows. It is readily apparent that the smaller the particles or the finer the texture, the greater is the surface area exposed to softening. The fine division of the particles also allows a wider and more thorough distribution of the fluxing agents; consequently, the vitrification will proceed more rapidly, the solution and reaction of the constituents will be facilitated, and the material will flow at a lower temperature. On the contrary, a finer division of the particles may produce a wider and more thorough distribution of the higher melting-point constituents to the extent of raising the melting point.
The total effect on the melting point of varying the size of the particles ordinarily is not large. For example, in the case of a large number of samples of coal ash, those specimens ground “to an impalpable powder tended to soften at a slightly lower temperature than ash that would pass a 100-mesh screen. The difference averaged 6° C. and in no test exceeded 40° C.” Experiments made in the pyrometry laboratory at the Bureau of Standards on the melting points of silica foundry sands of particles just passing a 10-mesh screen showed no differences in melting point larger than the experimental error when the particles were ground to pass an 80-mesh screen. Other experiments on a fireclay brick gave a melting point of 1655° C. when ground to pass an 80-mesh screen and 1640° C. when ground to pass a 200-mesh screen. The melting point of the unground brick was found to be 1630° C. In this case it appears that the grinding served to modify the distribution of the different constituents in addition to reducing their size. All of these experiments were made under the same conditions.
Because the melting of a refractory material is accompanied by a more or less gradual decrease in viscosity, the temperature of marked flow will be dependent on the original geometrical form and position of the substance. For example, pyrometric cones in the shape of a tetrahedron with the axes at various angles from the vertical will be subject to different bending moments while softening and falling over; thus when bent over, the degree of fluidity attained will not be the same. If the same substance were in the form of a short cylinder, it is probable that one would not be able to judge by the squatting of the cylinder the temperature at which the same degree of viscosity occurs as in the case of the cone; hence the melting point observed with a cylinder may be different from that observed with a cone. However, experiments made at this Bureau showed no difference between the melting points of a cone and cylinder of the same height placed vertically and heated under the same conditions. The cylinder measured 2.5 cm. in height and 1.2 cm. in diameter; the cone was in the shape of a tetrahedron, being 2.5 cm. high and having 8-mm. sides for the base.
Time and Rate of Heating
The process of vitrification and melting of refractories is a matter of time as well as of temperature. Obviously, the longer the time during which the substance is held within its vitrification range the greater the extent of sintering; that is, the softening, melting, solution, or reaction of the components. Thus, if a refractory is held for a long time within its vitrification range, its fusibility will be increased; if a refractory is kept for a long time below the vitrification range, the sintering will not be appreciable. The melting point may be increased by the occurrence of a chemical reaction that results in the formation of a compound with a higher melting point than either of the components; rapid heating would, in this case, arrest the formation of such a compound. In the case of some materials prolonged heating brings about volatilization of the more volatile constituents, such as alkali compounds, with a consequent increase of refractoriness.
The observed melting point will also vary markedly with the rate of heating. In accordance with the well-known principle of the increase in the rate of reaction with the rise in temperature, the speed of a vitrification is accelerated by raising the temperature; consequently, the faster the rise in temperature, the smaller is the total amount of sintering or vitrification. At the same time, by rapid heating the solution of the components and the formation of eutectics may be arrested considerably; thus some of the factors that can cause the material to flow are largely diminished in effectiveness.
It takes a long time for some pure refractory compounds to melt; thus the melting temperature will vary with the rate of heating, for the extent of superheating while melting will be different for every rate of heating. In practically all instances of impure refractory mixtures or compounds, the melting range will depend on the rate of heating also because of the time effect in melting. It is believed that the effect of a change of rate of heating is more marked, the closer one approaches the melting point.
As a general rule, and within certain limits, the faster the rise in temperature the higher is the apparent melting point. No better illustration of this can be found than with Seger cones, where the softening temperatures can be easily varied by 50°C. or more by changing the rate of heating. At the Bureau of Standards, no difference in melting point was found in the case of a firebrick heated to the melting point in 1 hr. and one heated for 5 hr. In the case of very rapid rates of heating, the large temperature gradient in the sample may play a part in causing a high value for the melting point.
Nature of the Surroundings
Several possible external conditions affect the melting point. The pressure of the atmosphere, per se, will have practically no effect; that is, it would take a pressure of many atmospheres to change the melting point even slightly. In an indirect manner, however, the melting point may be changed considerably in a vacuum; namely, the more volatile and fusible components, such as alkali and alkali earth compounds, may distill or sublime, thus causing a rise in melting point, and vice versa, those substances that go off at atmospheric pressure may not do so at higher pressures.
Due to chemical reaction with the gases in the atmosphere surrounding the refractory, its melting point, can be altered considerably. In the case of some materials, coal ash, for example, the nature of the atmosphere is the factor exercising the greatest influence on the melting point. The terms reducing, oxidizing, and neutral atmospheres are not sufficiently, definite and, when considering the nature of the atmosphere, the gases present should be indicated. For example, in a reducing atmosphere either carbon vapor and carbon monoxide or hydrogen and water vapor may predominate; and the effect of one atmosphere may be totally different from that of the other.
In a carbon and carbon-monoxide reducing atmosphere, many refractories are very strongly attacked, the extent being dependent on the chemical composition, the pressure, and the temperature. Under some reducing conditions, ferric oxides in fireclay substances or other refractories are reduced to the ferrous state and combine to form low-melting-point silicates, which very materially increase the fusibility. In very strongly reducing carbon atmospheres, all the iron oxides may be reduced to metallic iron, thus preventing reactions with the silicates. At high temperatures, silica and silicates are reduced by carbon forming, under certain conditions, various compounds of silicon, carbon, and oxygen. On the other hand, in oxidizing atmospheres, some substances may be oxidized, allowing or preventing them from reacting with the refractory and bringing about a change in the melting point.
Conditions in Use Affecting Apparent Melting Point
Substances coming in contact with the refractory, such as molten metals, slags, fluxes, and flue dust, often attack the refractory and may lower its melting point considerably. Since the temperature at which a refractory begins to flow is related to the degree of viscosity the material has attained, the application of a load will make the material deform faster and at a lower temperature. On account of the more intimate contact of the particles, the application of a load will allow a refractory to sinter at a lower temperature and the continued application of the force will result in the material softening or melting at a lower temperature. It also appears to be true that the larger the load applied, the lower is the temperature at which the material will soften and collapse. For instance, the softening point of a fireclay brick with no load was 1730° C. while with a load of 50 lb. per sq. in. it was 1200° C. A fireclay with a softening point of 1650° C. gave a softening point of 1435° C. with a load of 54 lb. per sq. in.; and one of 1380° C. with a load of 72 lb. per sq. in.
In general, so large a number of complex physico-chemical phenomena enter into the melting of a refractory material that it becomes impossible to predict in most cases in which direction the melting point will change by changing the factors and conditions under which the material is heated.
Practical Determination of the Melting Point
The ideal method of determining the melting point of a refractory material would be to observe it under the actual conditions of use; in most cases, however, this is practically impossible. What actually has to be done is to compromise between duplicating the conditions of use, on the one hand, and substituting feasible methods afforded by laboratory facilities, on the other; unfortunately one usually is compelled to decide almost wholly in favor of the latter. To determine the melting-point under conditions approximating those of use or in such a manner as to form definite and specific correlations between the melting point and other properties in use very often demands, in the case of each material, extended and elaborate investigation (as, for example, the relation of the melting point of coal ash and the degree of clinkering). Because of the great variation in the properties and characteristics of refractory materials, these conditions of test cannot be made the optimum for all materials; accordingly they cannot be made as detailed and special as if we were dealing with one type of refractory. As far as possible they should be logical, simple, and easily reproducible so that a standard and practical method for the determination of the melting point of refractories may be established.
The fact that conditions in use, such as load and chemical reaction, may give an apparent melting point widely different from that observed in the laboratory is no valid reason for determining the melting point very roughly, as by making Seger cone pyrometric measurements, and by varying and not specifying the size of the particles, the time and rate of heating, and the chemical nature of the atmosphere. Each of these factors introduces a variable into the value, for the observed melting point; and if these factors are not specified and are varied from time to time, the observed melting point will not have a definite and reproducible meaning. Since the melting-point test is used as one of a number of tests to determine whether refractories conform to specifications, it is very essential that it should have a definite meaning to the extent that a melting-point, test on the same material made in various laboratories should give practically the same value and that the value should be reproducible in the same laboratory. In order that this agreement be possible, the factors and conditions of the melting-point test should be practically the same or, at least, the existing factors and conditions should not be sufficiently divergent to produce large disagreements.
Sampling, Grinding, and Molding
When the material of which the melting point is to be determined is a fireclay brick with comparatively large pieces of grog held together by fireclay, one cannot procure a representative sample by simply breaking off a piece at random. In the case of a firebrick or any other material in which there is not uniformity of texture and composition or the particles are larger than 30-mesh, the material should be carefully sampled. It thus becomes necessary to grind it, which makes molding of the material into a cylinder or cone a requisite. With bricks of fine and uniform texture, however, a piece may be chipped off and shaped into a cone or cylinder. Materials in the form of a fine powder can, after mixing, be briqueted directly.
As the size of the particles may affect the melting point, the degree of fineness to which the material has been ground should be specified, at least approximately. There is the possibility of grinding the material so fine that any further reduction will have no effect on the melting point; also of grinding the material just sufficiently to insure uniformity in distribution, of the components and proper consistency to allow the form to retain its shape after briqueting. From the standpoint of the comparison of the melting points of different refractories, the first is the better, but it involves the labor and time of fine grinding; the second is the more feasible and, for a large variety of materials, when a cylindrical specimen is used, grinding to pass an 80-mesh screen appears to be suitable. When cones are made, the material should be ground to 100- to 200-mesh and molded with a binder. A binder is not necessary with the cylindrical form, because, with the aid of a little moisture, the material can very conveniently be briqueted under pressure. A binder should not be used if it will attack the refractory. A 10 per cent, solution of dextrin in water is a satisfactory binder. After the sample is molded, it is safest to burn off the dextrin in an oxidizing atmosphere at about 600° C’., and then determine the melting point.
Since it appears that there is no material difference between the melting point of a cone 2.5 cm. high and having 8 mm. sides for a base and a cylinder 1.2 cm. in diameter and 2.5 cm. high, either may be used. As shown above, the cylinder is the most convenient to use.
Precautions should be taken that in no case the melting-point specimen is too large for the rate of heating used, because large temperature gradients may be set up in the specimen. The smaller the sample, the easier it is to maintain fair temperature uniformity in the sample in a laboratory furnace.
Time and Rate of Heating
In order to approximate the usual conditions of use, the rate of heating would have to be slow and the time prolonged; such a course is not desirable or convenient in the laboratory. The time of heating should not be so long, as to waste time nor to make it tedious to watch the specimen; nor should the rate be so fast as to mask the melting effect or to make the melting interval too short to afford sufficient time to measure the temperature at the melting point.
The time of heating from room temperature to about 1000° C. may usually be very short, for it is believed that the rate during this interval is not of much consequence. For materials melting around 1700° C., a total time of heating of not less than 30 min. and up to 2 hr. and a rate of heating (from about 50° below the melting point and during melting) between 5° and 10° C. per minute are satisfactory. The following table represents a temperature versus time curve of heating of a firebrick, the melting point of which was determined at the Bureau, with sufficient approximation:
It should be emphasized that in stating the melting point of a refractory material the temperature-time curve must be represented as definitely as necessary to allow the duplication of practically the same value for the observed melting point.
Type of Furnace and Conditions Existing in Furnace