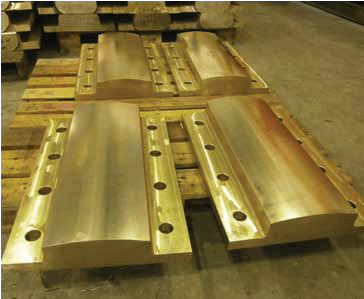
Developments in engineering during the past decade, particularly as applied to marine construction, mining machinery and other purposes in which corrosion offers a serious problem, have created a large demand for a non-ferrous metal highly resistant to corrosion and at the same time useful in general construction work as a substitute for steel without materially decreasing the factor of safety or increasing the weight of the various parts over that ordinarily used in the case of mild steel.
To obtain the combination of desired properties many compositions have been proposed and used with excellent success, but at the present time probably the most popular and most widely used combination is the non-ferrous alloy commonly called manganese bronze. This is nothing more than a high brass to which have been added, by the proper method of alloying, comparatively small percentages of aluminum, iron, or manganese with the definite purpose in view of strengthening the alloy and rendering it more dense and close-grained than the average yellow-brass casting.
In the manufacture of manganese bronze a great deal has been said about the importance of using only the highest grades of raw material and the beneficial or detrimental effects, as the case may be, of various impurities, as well as the importance of adding the ingredients according to various formulas proposed; but in most of these cases the literature on the subject has dealt principally with the manufacture of this alloy from virgin metals and raw materials of the highest purity. It is the purpose of this paper to deal particularly with the possibilities that lie in the proper development of methods for manufacturing such an alloy by more economical methods than those which have usually been discussed in other literature on the subject. Shortages have recently existed in raw materials needed for many products entering into the various branches of engineering work, particularly the non-ferrous metals, and during the next few years of reconstruction the country will be flooded with many byproducts and much scrap resulting from the extensive operations carried on during the period of the war, during which time scrap and byproducts could not be handled in sufficient volume to effect rapid production. These facts constitute conditions that make a project looking toward the efficient utilization of such materials well worth while.
When manufacturing manganese bronze or similar alloys from raw materials there is intentionally added a percentage of iron, which is generally conceded to be one of the very objectionable impurities in non-ferrous scrap, in addition to which aluminum and manganese are added, and sometimes tin in small quantities, all of which if present in the virgin metals ordinarily used in nonferrous foundry practice would be considered detrimental impurities. The composition of the average manganese bronze is as follows:
which composition shows rather clearly that there is no necessity for the use of high-grade raw materials, provided methods of manufacture can be devised to produce the proper refinement of the finished product, as the ordinary impurities encountered in non-ferrous materials offer no serious obstacles when the same elements must be added in considerable percentages to effect the desired composition.
In the manufacture of manganese bronze it has been found possible to utilize what would ordinarily be termed material of very low grade, such as skimmings from the foundry, particularly skimmings and dross ordinarily recovered from brass rolling mills or cartridge-case plants, zinc dross recovered from galvanizing plants, aluminum turnings that are ordinarily unrecoverable without serious loss and deterioration of the product due to oxidation, etc., and other byproducts and scrap metals that ordinarily are not usable as remelting scrap in foundry practice. The manufacture of high-grade manganese bronze from materials of this class, however, cannot be attempted in crucible furnaces, or practiced only on a comparatively small scale, as there is required a reverberatory or other furnace in which it is possible to accumulate a bath of considerable volume and in which the charge of metal can be worked in the same manner as in other refining processes producing on a large scale in open-flame furnaces. The idea is to so compound the various materials available as to cause one to react with the other to the mutual benefit of all the ingredients going into the charge.
A typical charge for operating a reverberatory furnace in the manufacture of manganese bronze is as follows:
With a knowledge of the general chemical composition of each ingredient going into the charge it is easy to produce a manganese bronze that will have the desired composition and will require no other treatment than, possibly, the addition of a little zinc when remelting for casting purposes.
When handling a charge such as that just shown, advantage is taken of impurities, such as the iron existing in the zinc dross, the small percentages of tin in the machine-shop turnings, etc., in figuring the final desired analysis of the alloy. It is a well-known fact that such materials as zinc dross and foundry skimmings, both of which are full of dirt and oxides, cannot be recovered in a usable condition when melted separately in crucibles or by any of the ordinary methods of melting material, without an excessive loss due to volatilization. But when the well-known reactions occurring in the manufacture of old-fashioned calamine brass are taken into consideration, it can be seen how the combination of zinc dross, brass skimmings, and other highly oxidized materials melted in contact with charcoal will produce an alloy about as well deoxidized as the average high-zinc brass. Contact, while in a molten or semi-molten state, of metallic copper and partly oxidized zinc in the presence of charcoal develops a condition extremely conducive to a thorough deoxidation and alloying of all the metallic ingredients. This reaction, together with the well-known deoxidizing effects of aluminum, manganese and iron, which are part of the charge, contributes to the production of thoroughly, deoxidized and dense material. Salt is used as a flux on account of its excellent properties for gathering and fluxing off the dirt from the charge, the oxides of iron, manganese, etc., and the reduction of any copper oxides passing from the bath into the slag.
In charging the furnace, it is the usual practice to place the manganese hardener in the bottom of the furnace and on top of it place the cartridge-case dross and zinc dross with a layer of charcoal, after which the foundry skimmings and turnings are added and the charge is melted, with occasional rabbling to clear the metal and bring all the ingredients into intimate contact. When the bath is melted, the aluminum scrap is added and the necessary zinc additions are made, after which the charge is allowed to cool slightly in the furnace and is poured into ingots for remelting purposes, after analysis has been made to determine the necessity of adding zinc or otherwise correcting the composition by the mixture of several heats in order to obtain the desired composition.
The foregoing process carried out by a skilled melter will produce an alloy that is absolutely sound and homogeneous and capable of being cast in ordinary foundry practice in the same manner as any of the so called high grades of manganese bronze, and will produce most excellent physical properties in the finished casting.
As instances of what can be obtained, the following results of tests are given. These tests were made on castings produced by the method described from initial charges of raw material practically identical with the typical charge given.
In addition to the excellent properties shown in the tensile tests, the material corresponds in every other physical respect to so-called high-grade manganese bronze produced from virgin metals, has a fine uniform fracture with a tendency to silky grain in many cases and shows toughness and resiliency equal to any other grades of manganese bronze examined.
Some objections may be raised to the use of byproducts and scrap material in the manufacture of manganese bronze because the lead content of some of these byproducts is quite high and will introduce into the alloy quantities of lead higher than are desired. It is believed, however, that the results of tests made from time to time on manganese bronze, containing in some cases a considerable percentage of lead, have shown conclusively that lead within reasonable limits is not detrimental. No concrete cases have as yet been cited in which, other things being equal, lead under 0.75, per cent, has shown seriously detrimental effects on the alloy. All the samples on which physical tests are given contained percentages of lead ranging from 0.25 to 0.50 per cent., yet none of them show in the test results any detrimental effects due to the presence of this so-called impurity. It is believed that the tolerance of a slightly higher content of lead in specifications for manganese bronze would, in general, serve admirably as a conservation measure for high-grade virgin material and offer excellent opportunities for the utilization of many metallurgical byproducts that at the present time constitute practically useless material.
The results obtained after about 3 years of operation under the process described have shown rather conclusively that the alloy commonly known as manganese bronze can be produced without resorting to the use of high-grade virgin materials with the addition of what would ordinarily be termed detrimental impurities, by the simple application of some of the well-known laws of metallurgy.