Table of Contents
Lime Roasting is a term proposed by Ingalls for the operation of forcing air under pressure through a mixture of galena and lime at the kindling-temperature with the object of oxidizing lead and sulphur and of fritting or fusing the charge. If finely-divided galena were treated in this manner without the addition of lime, the heat set free by the oxidation of part of the lead and the sulphur would be sufficiently great to fuse undecomposed sulphide, and thus stop desulphurization. Besides the chemical action that the addition of lime, limestone or gypsum to the charge may have, the admixture has the physical effect that it keeps the particles of galena separated from one another and accessible to the oxidizing effect of the air.
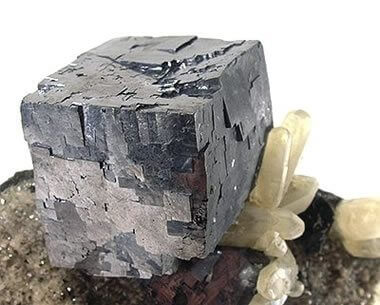
At present, three methods of lime-roasting are carried out on a working-scale,—the Huntington-Heberlein, the Carmichael-Bradford and the Savelsberg processes. In the last, which interests us here, an 8-ton charge is made up of galena, limestone and perhaps some siliceous or ferruginous flux; the whole is crushed to pass a screen with 3-mm. holes and moistened with 5 per cent, of water. It is fed gradually into a bowl-shaped converter, 6.56 ft. in diameter, supported by trunnions attached to a truck. On the bottom the converter has a grate with blast-inlet beneath. In starting, the truck with the converter is run underneath a stationary hood, which carries off the gases and fumes; the grate is covered with a layer of crushed limestone for the sake of protection; then follows a bed of glowing coal or coke, to be covered by a second layer of limestone to prevent contact of fuel and charge. A gentle blast is turned on and charge fed in to the depth of 12 in. Oxidation begins at the bottom and sulphurous gases are given off; when the roasting approaches the surface and this becomes red-hot, a second layer of charge is fed in, and feeding continued at intervals until the converter has been filled. While charging, about 247 cu. ft. of air is forced in with a pressure ranging at the start from 2.75 to 4.5 oz. per sq. in.; the volume of air is increased with the amount of charge fed, and this causes the pressure to rise to from 11.5 to 13.5 oz. per sq. in. toward the end of the blow, lasting about 18 hours. Desulphurization is followed closely by scorification and this by solidification. The charge does not become liquid as a whole, as the formation of the slag is a heat-absorbing reaction and as the blast chills the slag. The converter, when blown, is withdrawn on its truck from beneath the hood ; the charge is dumped on to an upright iron bar to break it into several pieces, which are then further reduced in size by wedging and sledging. A typical charge at Ramsbeck, Westphalia, with 100 parts of galena-concentrate (Pb, from 60 to 78; S, 15 per cent.), 10 siliceous silver-ore, 10 spathic iron-ore and 19 limestone, averaging SiO2, 11 per cent., will retain from 2 to 3 per cent, of S when successfully blown.
The literature of the process gives very little information upon the effects which variations in the addition of limestone and changes in the volume of blast may exert upon desulphurization, fusibility and losses in lead and silver. The aim of the experiments was to supply this lack as far as laboratory work could do it.
Experimental Work
The materials used in the experiments were ore, limestone and quartz. The ore was a galena-concentrate from the Coeur d’Alene district, Idaho. A screen-analysis gave the data presented in Table I., which shows that, with the exception of two grades, the 9- on 12-mesh and the through 100-mesh, the different sizes were evenly distributed. The ore was crushed to pass a 2.8-mm. screen.
The chemical analysis of an average sample gave: S, 10.58 ; FeO, 5.95; Al2O3, 4.80; SiO2, 18.58; Zn, 2.57; Pb, 54.70; CaO, 2.20; MgO, 0.40; Ag, 0.135 (= 39.50 oz. per ton); total, 99.915 per cent. Calculation sets forth that lead and zinc are covered by sulphur, being present as galena and blende, and that, in the absence of carbon dioxide, the gangue is made up of silicate or quartz and silicate. The limestone was a pure marble, which, upon analysis, gave: SiO2, 0.26; CaO, 55.01; MgO, 0.85; CO2, 44 (calculated); total, 100.12 per cent. The silica added to the charges to obtain various silicates was pure quartz, assumed to contain 100 per cent, of SiO2.
Two converters were employed for blowing the charges, one a clay crucible, the other a slag-pot. The crucible-converter, in which most of the tests were made, is represented in Fig. 1: A is a Morgan clay crucible, size K, with a hole 0.5 in. in diameter drilled in the bottom to admit the air-blast; B, an iron funnel ending in a piece of gas-pipe, connected with a T-joint, C, one arm of which is closed by a screw-plug, D. The slag-pot converter, represented in Fig. 2, is a small-size detached Devereux slag-pot. The grate, A, is a cast-iron plate perforated with holes 0.25 in. in diameter; the blast-inlet pipe, B, is screwed into the tap-hole; C is the hood for carrying off gases and fumes; D, the charging opening, closed by a hinged door. The blast for the converters was furnished by a Root blower, No. ½; the pressure was measured by a water-gauge calibrated to read in inches. The temperature measurements were made with a Le Chatelier thermo-electric pyrometer.
Two series of tests were made in the crucible-converter, using 1 kg. of ore in each experiment. In the first series a singulo-silicate-slag was made the basis of calculation. Since the ore did not contain enough silica to form a singulo-silicate after the quantity of limestone suited for lime-roasting had been added, the deficiency was made up with quartzite. In the second series, the quantities of limestone used were similar to those in the first series, but no additions of quartzite were made; the products obtained were therefore sub-silicates of varying silicate degree. In conclusion, two tests were made in the slag-pot converter with 20 kg. of ore to see whether the size of charge had any effect upon the result. The charges were fluxed according to the most favorable results obtained in the experiments with 1 kg. of ore.
The modes of procedure in the small- and medium-size tests were similar. With the crucible-converter, the crucible was warmed in the ash-pit of an assay-furnace, the inside of the receiving-funnel was coated with a clay wash in order to make an air-tight joint, and the warmed crucible pressed into the funnel. A few pieces of limestone, nut-size, were placed in the bottom of the crucible to act as a grate; a thin layer of ignited charcoal was spread over the limestone, and the blast started. When the charcoal was burning freely, it was covered with a second layer of limestone, of a pea-size. The charge, mixed with enough water to give it the consistency of brasque, was then fed in gradually. A thin layer was spread over the limestone, and as soon as it had become ignited and glowing spots began to appear on the surface, a second layer was added, and so on until the crucible was filled. The blast was continued until no more fumes passed off from the surface. Any blow-holes that formed, here and there, were closed by adding fresh charge or by poking down the crater-like walls of the cavities. When a charge had cooled down somewhat, it was dumped out; the coarse limestone was picked off from the bottom, the slagged and unslagged portions were separated and weighed, the slagged part was crushed, added to the pulverulent part, and the whole sampled down and assayed for sulphur, lead, and silver. A crucible could be used for several charges, as these did not attack it; it had to be replaced, however, after a few runs, as it became fissured by a longitudinal or diagonal crack, caused apparently by the unequal expansion of the clay and the iron funnel.
The slag-pot converter was warmed by burning a thin layer of charcoal on the grate with a gentle blast; otherwise, the mode of procedure was the same as just outlined.
Temperature-measurements, by means of a Le Chatelier thermo-electric pyrometer, were made with five charges to see in what manner the rise in temperature took place, and to find the highest degree of heat attained in the process. Three continuous readings were taken with the crucible, and two with the slag-pot converter. The results are plotted in Figs. 3 to 7. With curves Nos. 3 and 4 the thermo-junction was fixed at about one-third the height of the crucible, with curve No. 5 at about two-thirds; with curves Nos. 6 and 7, representing the me-
dium-size charges, the thermo-couple was held near the center of the slag-pot. In all cases temperature-readings were begun when the ore-charge reached the junction, and then continued at intervals of 15 sec. In curve No. 3 the two thermowires parted at 990° C., in curve No. 6 the galvanometer ceased to act at 1,220° C. for some unexplained reason, and in curve No. 5 there was a halt at the same temperature, followed by a rise after a few minutes’ interval. These imperfect records are given, as they show, as far as they go, features similar to those of the complete records. The five curves all show a sudden quick rise of temperature to a maximum of 980° C. with the small charges, and to an apparent maximum of 1,225° C. with the medium-size charges. The subsequent gradual fall of temperature is seen only in curves Nos. 4 and 7.
Record of Results
The results obtained from the 17 tests made are recorded in Tables II., III. and IV., and the data of the 15 small-size charges relating to the elimination of sulphur and the loss in lead and silver are represented graphically in Figs. 8 to 19.
Table II. and Figs. 8 to 11 represent the singulo-silicate series of tests. The weight of a charge had to be adapted to the size of the crucible; with small quantities of flux 1,000 g. was taken; with increasing quantities, the weight had to be reduced. The percentage of limestone of the charge ranged from 4.7 to 30, and the necessary silica varied accordingly. The mixtures were moistened in each case with 5 per cent, of water. The time it took to fill a crucible varied from 4 to 9 min., the blast being kept constant at 2 in. pressure. In two cases this pressure was maintained throughout, in four it was raised to 6 in., and in four to 10 in.
The runs lasted from 14 to 18 min. The blown product weighed less than the original charge, as was to be expected. The data giving the percentages of slagged and pulverulent parts of the blown charges show that limestone could form as much as 24 per cent, of the weight of the charge, and this when blown still furnish more than 95 per cent, of slagged material. When, however, this quantity of limestone was exceeded, and the lead in the charge reduced to less than 33.7 per cent., and the sulphur to less than 6.54 per cent., the heat generated was
insufficient to fuse the charge; this remained pulverulent, with here and there an agglomerated particle distributed through it. Slagged ore had the general characteristics of ore that has been agglomerated on the hearth of a hand-reverberatory roasting-furnace; the color, however, was more greenish-brown than black; it was tough, and the hardness increased as the additions of limestone decreased; wherever the elimination of sulphur was imperfect, streaks or bunches of undecomposed galena could be easily traced.
Curves Nos. 8 and 9, representing the percentage of sulphur remaining in the blown charge and the percentage of sulphur eliminated, show that in a charge the percentage of sulphur decreases as that of limestone increases until the latter reaches 20 per cent., and that from this point on the residual sulphur remains constant at 3.5 per cent. On the basis of percentage of sulphur eliminated, the maximum of 60 per cent, is reached with a charge containing between 16 and 20 per cent, of limestone, and then begins to decrease. In curve No. 10 the loss of lead increases from 2.55 per cent, with increasing limestone until 10.6 per cent, has been reached; it then remains constant to 12.7 per cent., when it drops quickly, reaching zero
with 20 per cent. The loss in silver, represented by curve No. 11, follows that of the lead; it increases with additions of limestone to 16 per cent, and then falls, at first gradually, and later more quickly. As limestone forming 24 per cent, of the weight of the charge is the permissible limit, if, when blown,
it is to be satisfactorily slagged, it may be inferred that, for practical purposes, the loss in silver increases with the additions of limestone. If curve No. 11 is compared with curves Nos. 9 and 10, a similarity between the two will be seen, indicating that the loss in silver increases with the elimination of sulphur and of lead.
Table III., giving the data of the sub-silicate series, is arranged in the same manner as Table II. There is an additional heading, giving the silicate-degree of the charge; furthermore, charges Nos. 8, 9, 9a and 10 have been run with a high-pressure blast, and in charges Nos. 11, 12, 13 and 13a, of similar composition, the initial blast-pressure of 2 in. has been kept constant.
Curves Nos. 12 to 19 represent graphically the data relating to the elimination of sulphur and the loss of lead and of silver. The proportions of slagged and pulverulent parts of a charge remained satisfactory as long as the addition of limestone did not exceed 16.6 per cent, of the weight of the charge, and with it the percentage of sulphur was not reduced below 8.81 per cent, and that of lead below 45.6 per cent.; beyond these limits the blown charge was not sufficiently coherent to be suited for a blast-furnace charge.
Curves Nos. 12 to 15 show that the residual sulphur (3.76 to 5.47 per cent.) and the sulphur eliminated (47.4 to 61.6 per cent.) decrease and increase respectively with the addition of limestone until this forms 13 per cent, of the charge. Comparing curve No. 12 with No. 14, and No. 13 with No. 15, shows that the oxidation of sulphur proceeds more quickly with a high than with a low pressure, but that it is not so effective; the percentages of residual sulphur are greater and the percentages of elimination smaller. Comparing curves Nos. 14 and 15 of the low-blast sub-silicate series with the corresponding curves, Nos. 8 and 9, of the singulo-silicate series, it is found that the percentages of residual sulphur and elimi-
nated sulphur are respectively lower and higher in the singulo-silicate than in the sub-silicate series. The loss in lead, curves Nos. 16 and 17, is greater with high- than with low-pressure blast. This is due, no doubt, to the greater prevalence of blow-holes with the former. It is greater in the singulo-silicate than in the sub-silicate series. The probable explanation is to be found in the presence of a larger amount of slag-forming material for a given quantity of lead. The loss in silver with the sub-silicate series is shown in curves Nos. 18 and 19. It is seen to be proportional to the loss of lead, as was the case with curves Nos. 10 and 11 in the singulo-silicate series.
Table IV. gives the data of the two tests made with singulo-silicate charges using 20 kg. of ore. In order to compare the effect of the size of charge, the leading data are brought together in Table V.
Passing over the irregularities in the percentage of lead lost, Table V. shows one decided difference—viz., that the loss in silver is very much greater with a small than with a large charge. There is no reason apparent why this should be the case. Without a larger number of tests to substantiate the greater loss, this, for the present, must be considered as accidental.
Conclusion
The above experiments were carried on with a single ore, and the results find direct application only to this ore or to one very similar to it. Nevertheless, they have a more general application; they point to the conclusions:
- That in lime-roasting a siliceous galena-concentrate low in blende, charges containing a wide range of lime and silica, and little iron, can be successfully blown.
- That a singulo-silicate charge, with limestone equal to 16 per cent, of the weight of the ore, gives most satisfactory results as regards the physical condition of the product, the elimination of sulphur, and the loss of lead and silver.
- That the same is true with a subsilicate charge.
- That a low-pressure blast is a better desulphurizer and causes less loss than a high-pressure blast.