Table of Contents
Treatment of oxidized lead ores (Cerussite) has long been recognized as a difficult process often resulting in low grade concentrates and low recoveries. Surface oxidation on galena ores has resulted in high tailings losses. The difficulty in treating oxidized lead ores by gravity methods is due to the softness of the oxidized lead minerals. During normal crushing and grinding processes, the soft oxidized lead minerals are overground, resulting in fines which do not respond well to gravity concentration or flotation.
THE Cerussite Flotation Process FLOWSHEET
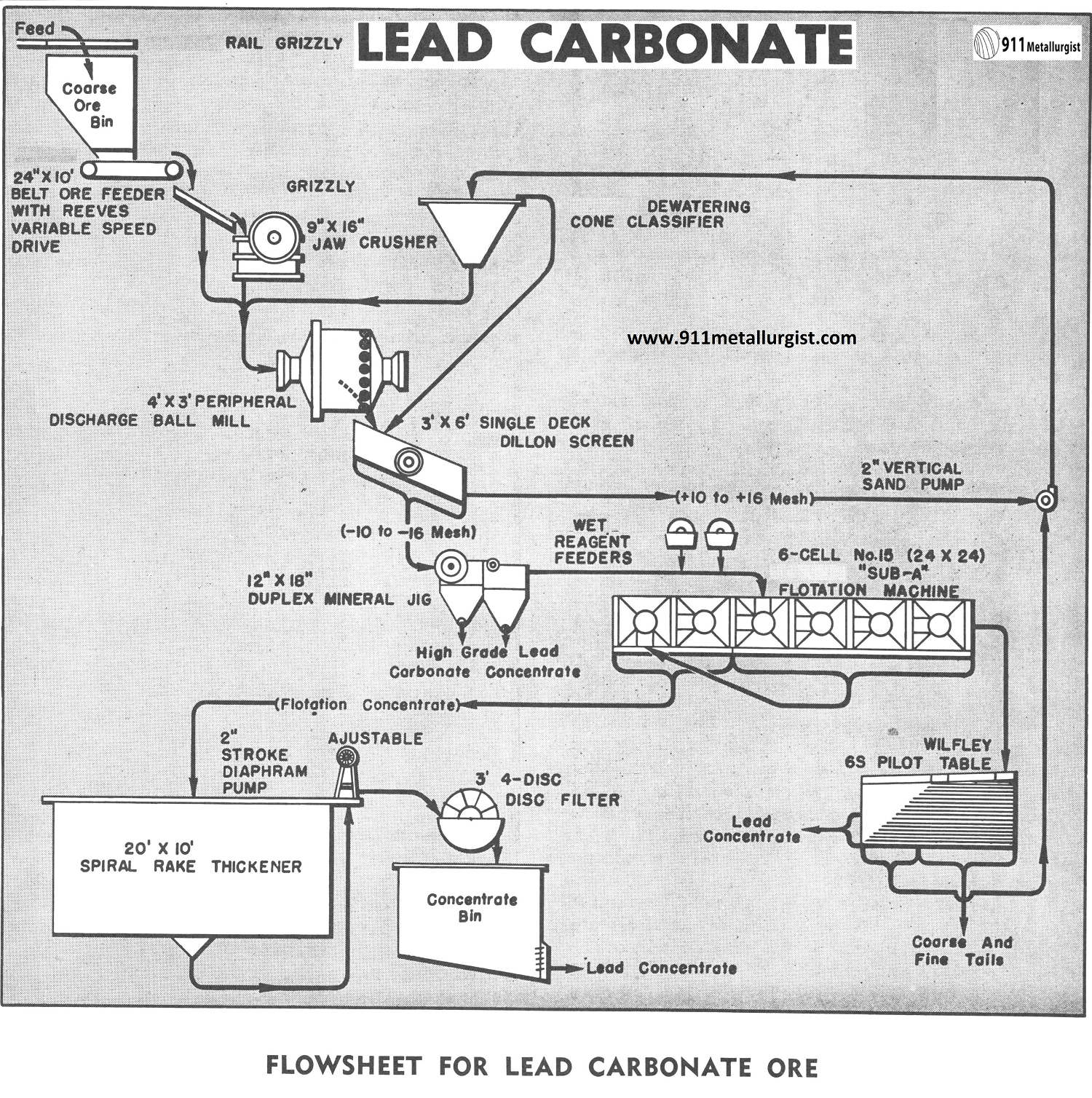
Cerussite Crushing Plant
The crushing section for this 50 ton mill consists of a 24″ wide x 10′ long ore feeder, a grizzly ahead of the jaw crusher and a 9″ x 16″ Type “H” Jaw Crusher. The length of the feeder is such that an operator can pick either high grade or waste material from the belt prior to crushing. The use of a grizzly reduces the load ahead of the jaw crusher. Grinding Section. The fine ore bin has been eliminated in this flowsheet since its advantage has been offset by additional oxidation of the lead minerals while the fine ore is stored in an ore bin. Therefore the crusher discharge goes immediately to the ball mill where overgrinding is kept to a minimum in the peripheral discharge Ball Mill. The material quickly passes through the ball mill onto a 3′ x 6′ Dillon Vibrating Screen which has a 10 mesh to 16 mesh opening. The mesh opening of course can be made coarser or finer depending upon the requirements of the particular ore. The plus 10 mesh material from the vibrating screen, is pumped with a 2” Vertical Centrifugal Sand Pump to a dewatering cone classifier. The overflow from the dewatering cone classifier is directed to the Dillon Vibrating Screen while the undersize returns to the ball mill feed. Sufficient water is added with the crusher discharge and classifier sands to maintain the correct density in the ball mill during grinding.
Lead Carbonate (Cerussite) Gravity and Flotation Circuit
The minus 10 mesh vibrating screen undersize flows to a 12″ x 18″ Duplex Mineral Jig which recovers a high grade lead concentrate. The jig tailing passes into a 6 Cell No. 15 “Sub-A” Flotation Machine with 4 cells as roughers and 2 cells as cleaners. Sulphidizer, sodium bicarbonate and a frother are used to condition the pulp in the first rougher cell. This reagent combination produces hydrogen sulphide which is most active as initially produced. The sulphidized minerals are then subjected to flotation in the 4 rougher cells of the “Sub-A” Machine and the concentrate from the 4 roughers is returned by gravity to the 2 cleaner cells, producing a high grade, clean lead concentrate.
Reagents for Lead Carbonate (Cerussite) Flotation
Sodium bicarbonate is used with the Sulphidizer to form hydrogen sulphide. The hydrogen sulphide is most active when initially produced and the “Sub-A” Flotation Machine takes advantage of this condition by agitating and mixing the reagents with the pulp and immediately carrying the sulphidized lead to the surface for froth removal.
Flotation of oxidized lead mineral fines normally results in excess reagent consumption and an undesirable colloidal condition which adversely affects the recovery of the lead minerals into the desired froth concentrate. Certain oxidized ores can be easily sulphidized with Sulphidizer and they then tend to respond well to flotation with promoters such as reagents 404, 425, or xanthate and a frother.
Tailing Section
The discharge from the “Sub-A” Flotation Machine passes to a 6S Wilfley Pilot Table where an additional concentrate is removed. A middling is also taken from the table and returned to the grinding circuit. The tailings are discarded to waste. The pilot table gives the operator a visual indication of the results being obtained in the jig and flotation sections.
Lead Carbonate (Cerussite) Thickening and Filtration
The gravity and flotation concentrates are thickened in a 20′ x 10′ Thickener prior to filtration. The thickener not only prepares the filter feed but also provides a storage for concentrates should it be necessary to repair the filter. In this way, the rest of the mill can be kept in continuous operation even though the filter is shut-down. The thickener rakes would of course be raised as required and the thickener underflow would be returned to the thickener feed. A 2″ Adjustable Stroke Diaphragm Pump or a 2″ low head Diaphragm Pump removes the thickener underflow to a 4′ 3-Disc Filter mounted over the concentrate bin.
SUMMARY
In the concentration of oxide lead ores, it is best to remove as much of the coarse free mineral as possible by gravity methods, and in this way improve flotation conditions by avoiding sliming of the mineral. The “Sub-A” Flotation Machine is designed to handle a coarse product and is therefore ideal for flotation of the oxide minerals at a coarse mesh. Simplified flowsheets and corresponding reduction in middling products are a necessity when handling oxide lead ore.
Source: This article is a reproduction of an excerpt of “In the Public Domain” documents held in 911Metallurgy Corp’s private library.