Black sand may be generally defined as a constituent of “alluvial” gravel consisting mainly of fine particulate grains of heavy, dark colored minerals and rocks. These alluvial gravels, chiefly concentrated by wave, current or surface action, may also contain “eluvial” material that includes black sand. The eluvium, which results from decomposition or disintegration in place of an ore body, may have slumped or washed down slope and will not have been transported by stream action as in the case of alluvial materials.
Black sand consists predominantly of magnetite and hematite. The magnetite may sometimes contain very small amounts of nickel, manganese, chromium, and titanium. Magnetite is one of the most widespread and abundant of all oxide minerals and occurs in many igneous rocks and many rocks of a clastic sedimentary origin. Rutile and garnet are also frequently found in black sand. Other minerals such as pyrite, wolframite, scheelite, copper, galena, and cassiterite may increase the complexity of black sand and hamper the separation of precious metals while contributing no economic value. Before any separation of precious metals from placer gravels can take place, it is necessary to produce a primary concentrate. These concentrates that contain black sand are produced by a number of concentrating devices or combination thereof. They include slurry boxes, spirals, jigs, spinning barrels, cones, hydrocyclones, and centrifugal concentrators. The black sand sample used in this study came from Vancouver, B.C. area and was concentrated from placer materials.
The recovery of gold from black sand concentrate is usually labor intensive and/or environmentally hazardous. Traditionally, mercury amalgamation is used to recover the gold. This is followed by nitric acid dispersion of the mercury or crude retorting, both of which constitute potential hazard to the environment and to those who work with or in close proximity to these materials and processes. Other methods of recovery include gravity methods which are slow and are not very efficient. More sophisticated systems such as floatation and cyanidation are usually impractical for the majority of placer mine operators.
Gold extraction, recovery, and economics for refractory concentrates, using cyanide and bromine reagents have been reported. Geobrom 3400 (Registered trademark of Great Lakes Chemical Corporation), a liquid bromine carrier, was used to leach gold from refractory concentrate.
Geobrom Leaching
The agitation bottle leach technique was used for all Geobrom leaching tests. A predetermined weight of Geobrom was added to a slurry of black sand in water. The slurry was agitated at room temperature in a capped bottle using an overhead mixer. The pH and ORP (oxidation-reduction potential) of the solution were monitored during the leach but no adjustment was made. At the end of the test, the leach slurry was filtered and the cake was repulped in a volume of water equal to twice the solids weight for 10 minutes. The repulped slurry was filtered and the cake was washed with a volume of water equal to the solids weight. The gold values in the filtrate, wash, and the residue were determined by Inductively Coupled Plasma Spectrometry (ICP) and fire assay. To establish the kinetics of gold extraction, intermediate samples were taken from the leach bottle at 2, 4, 6, 12, 18, and 24 hours. Fresh water was added to the leach bottle to compensate for solution lost due to sampling.
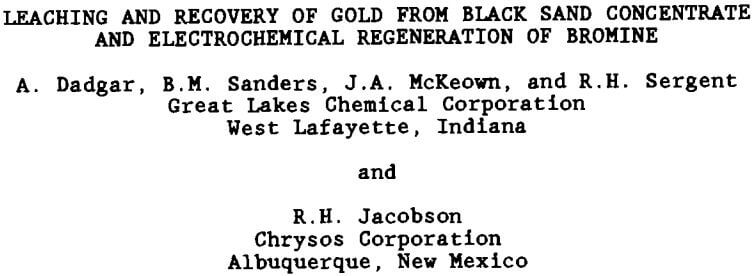