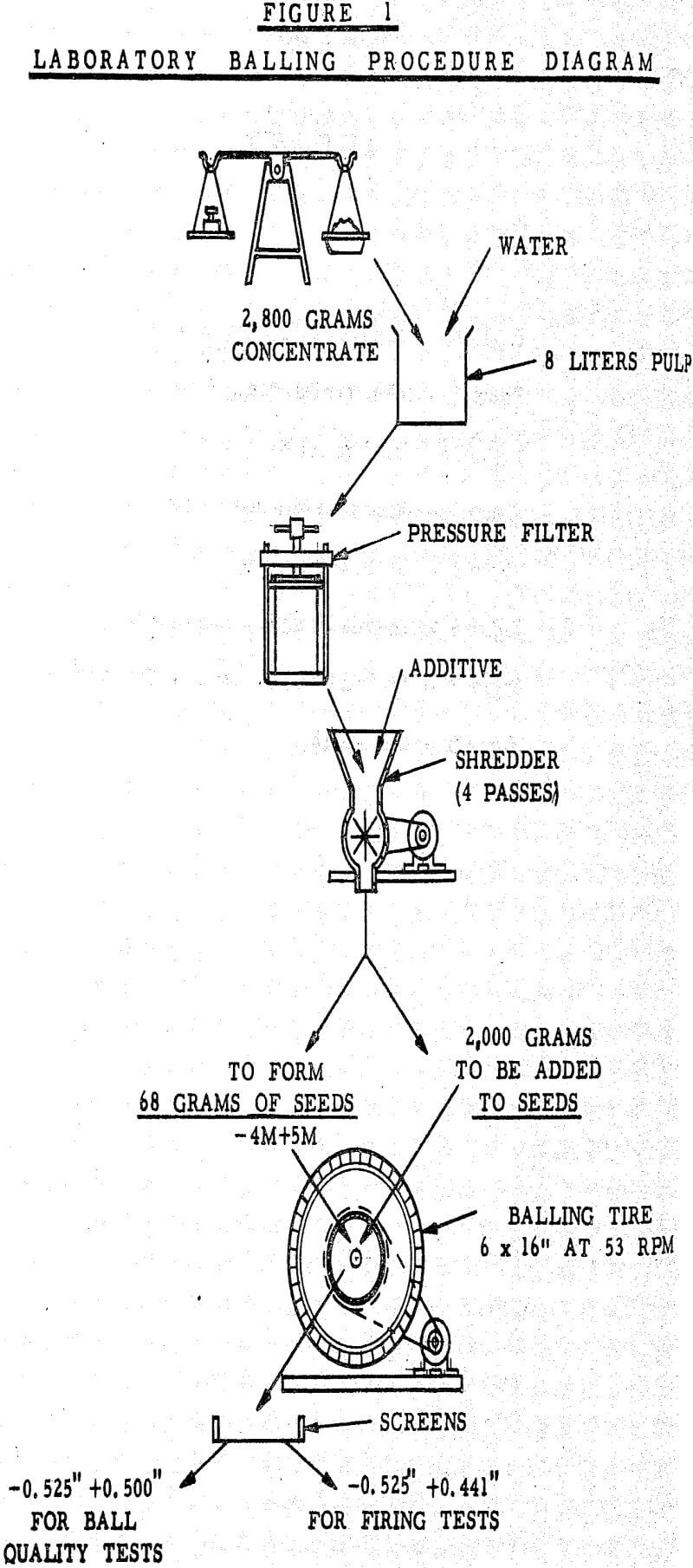
Early laboratory balling and pelletizing tests resulted in balls or pellets superior in quality as compared to production pellets, no matter what the variable being tested. In order to indicate more closely what a material would do for balling and pelletizing in a plant we felt it was necessary to approach the plant conditions. When the commercial ball size was changed from 1 in. to substantially ½ in. laboratory ball size was reduced.
It was still necessary to test a very narrow size range of balls since the compression tests were largely influenced by the diam or cross-sectional area of the ball being tested. The size we have adopted as the laboratory standard for compression testing is -0.525 +0.50 in. Our previous laboratory standard balling method included a step of mulling in a Simpson mix-muller for more uniform distribution of the bentonite. It was determined in the laboratory that this step increased the dry ball strength about 3 to 5 lb. This type of mulling is not used in any of the commercial plants so it was abandoned in the standard laboratory method of ballings.
A filtered concentrate containing 2,800 gm of solids is stirred with enough water to give 8 liters of pulp. After dispersion of the solids, the material is refiltered and shredded to about 20 mesh. A sample of the material is taken for a quick moisture determination and, if necessary, water is added to the shredded filter cake to obtain the proper starting moisture which is normally 9 to 10.5%. The optimum moisture has to be predetermined for each type of material.
The additive is stirred into the concentrate and the mix is shredded 3 times. A 2,000 gm portion of the mix is removed for balling; the remainder is used for making seed balls. As the seeds form they are removed and screened on 4 and 5 mesh Tyler screens. The +4 mesh fraction is saved as seeds and the -5 mesh fraction returned to the tire for further building. This procedure is repeated until suf-ficient seeds are obtained for the standard test.
Sixty-eight gm of prepared seed balls are put into the test tire and moistened slightly along the tire walls with a fine mist spray of distilled water. The 2,000 gm of wet mix is then added to the seed balls as follows:
- The wet mix is hand-sprinkled on the seeds as fast as they can pick it up for a period of 1 minute.
- The balls are removed from the tire and screened on 4 mesh to remove any newly formed seed balls.
- The +4 mesh balls are returned to the tire and the remainder of the 2,000 gm sample is added to them as in (1) in a 3 minute time period. The rate of addition increases as the balls grow.
- The finished balls are rolled in the tire for an additional 30 sec and removed for testing.
The -0.525 +0.500 in. balls are used for moisture, drop, and green, and dry strength tests; the remainder and all other balls between 0.525 and 0.441 in are used for firing.
Green and dry strengths are determined by a Chatillon compression tester with a 25 lb testing range and 0.1 in./sec head travel.
Standard balls are fired in a Marshall Vertical Silicon Carbide tube furnace (Figure 2). Green balls are placed a single layer deep in an Inconel basket which is lowered with a thermocouple into the furnace. The basket is 6 in. diam by 2 in. deep. Any desired time-temperature cycle can be followed, depending on the requirements of the test. For one simulated shaft furnace cycle pellets are heated at a rate of 155° F/min to 2300° F, cooled at a rate of 160° F/min to 1500° F, then removed from the furnace.
Testwork
Recent laboratory studies have incorporated the use of random balance technique for evaluating simultaneously the factors of balling and pelletizing. The random balance method is essentially a random sample drawn from a full factorial design. It is generally used to effectively scan a complex problem to sort out some of the major factors that should be studied more carefully. Each factor being tested must have a number of levels, the minimum being 2. For maximum use of results, the range of variation within each factor has to be broad enough to cause change in the result and also to include the normal variations which occur in actual practice. It is considered necessary for probability considerations that at least 30 tests be run. One such aeries investigated the following variables: the fineness of concentrate grind, the amount of bentonite, 3 different bentonite samples, the use of mulling versus no mulling, and firing rate for pelletizing. These variables and their levels are shown in Figure 3.
A magnetic concentrate from Quebec was used because it is relatively coarse and can be reground to test the effect of concentrate fineness on the same concentrate. The original and reground concentrate structures are shown in Figure 4.
The properties of bentonite samples A, B, and C are shown in Figure 5. Samples A and B were plant bentonites and C was the laboratory standard Volclay.
Ball moisture was not intentionally varied but was measured for each of the 30 tests. The moistures ranged from 8.9 to 9.5% and the effect was tested by designating all tests with 9.2% or higher as high level.
For each test, in addition to ball moisture, 20 balls were subjected, to drop tests, 20 were dried for dry compression tests, and the balls that were fired were tumbled in a regular tumble drum.
Laboratory balling and pelletizing techniques must be changed if binders and other pelletizing variables are to be accurately evaluated and results used to predict actual plant performance. These variables generally include both the chemical and physical properties of the concentrates to be pelletized.
Laboratory balls are fired when it is desirable to determine what may be expected from a test concentrate in a commercial furnace. Spalling of the balls is indicated by the amount of fines generated after exposure to high drying and heating rates. Fired pellet strength is evaluated by compression and tumble tests,, The compression strength indicates the uniformity of hardness from pellet to pellet and the tumble test indicates the resistance to the abrasion that may be encountered in handling and shipping commercial pellets.
Early laboratory balling and pelletizing tests resulted in balls or pellets superior in quality as compared to production pellets, no matter what the variable being tested. In order to indicate more closely what a material would do for balling and pelletizing in a plant we felt it was necessary to approach the plant conditions. When the commercial ball size was changed from 1 in. to substantially ½ in., laboratory ball size was reduced. It was still necessary to test a very narrow size range of balls since the compression tests were largely influenced by the diam or cross-sectional area of the ball being tested. The size we have adopted as the laboratory standard for compression testing is -0.525 +0.50 in.
A filtered concentrate containing 2,800 gm of solids is stirred with enough water to give 8 liters of pulp. After dispersion of the solids, the material is refiltered and shredded to about 20 mesh.
Recent laboratory studies have incorporated the use of random balance technique for evaluating simultaneously the factors of balling and pelletizing. The random balance method is essentially a random sample drawn from a full factorial design. It is generally used to effectively scan a complex problem to sort out some of the major factors that should be studied more carefully.
The graph can be visually analyzed to see if any level of any factor appears to be significantly different from other levels for the same factor. Bentonite amount is the only variable here which shows very little overlapping of individual readings between the high and low levels. Now the effects of concentrate grind and mulling are shown clearly. The mirror image of these two lines indicates a possible interaction between the two variables. A complex analysis using a computer was necessary to sort out the individual from the combined effects of these variables and it was found to be two separate effects and not an interaction.
Spalling was evaluated by noting the percentage of tests at the high level of the independent variable which resulted in spalling. High heating rate was found to be the chief cause. Forty percent of the high heating rate tests resulted in spalling whereas 27% of, the high bentonite tests and 20% of the fine grind tests resulted in spalling.
It is fully expected that many more changes are going to be required in laboratory procedures to get even closer to plant operation. This undoubtedly will include specific changes for specific concentrates to get closer to the actual flow-sheet involved.