The Knelson Concentrator relies on an enhanced gravitational force together with fluidization process to recover even very micron sized particles. First water is injected into the rotating concentrating cone through series of fluidization holes. Then feed slurry is introduced through a stationary feed tube. Once the slurry is filled in each cone, create a concentrating bed and high specific gravity particles are retained in the cone and then flushed into the concentrate launders. This procedure can be completed in less than one minute.
Looking for an affordable alternative to the Knelson?
The Knelson concentrator (KC) is a vertical axis bowl-type centrifugal concentrator that uses a fluidized bed to perform its concentrating duty. It was first introduced as a semi-batch unit and has gone through several iterations of design leading to the development of a continuous discharge machine. It has now become almost an essential unit operation in any gold processing plant to assess the gravity recoverable gold content in the ore as well as to recover fine free gold from the grinding circuit.
Knelson Concentrator (KC) first introduced to the hard rock milling industry there-by providing gold recovery by handling a maximum feed size of 6 mm. More recently KC-XD30 is rated to process 60 t/h of feed solids.
The use of centrifugal force in a centrifugal concentrator enhances the relative settling velocity differential between the particles differing in size and density. Separation of particles even in finer size ranges is, therefore, possible in a centrifugal concentrator like a Knelson concentrator. Naturally, many attempts are being made to evaluate its performance treating various other minerals than gold. However, literature dealing with this machine is either case specific or towards the development of empirical models. Due to this reason the role of centrifugal force on the separation of fine minerals and the role of fluidization water are not clearly understood.
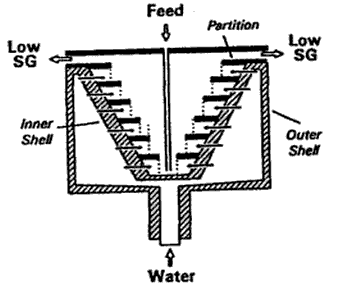
These are obviously the pre-requisites to explore its possibilities for other applications.
In any placer mineral, the density differential between the heavy minerals is marginal and hence, their separation using a gravity concentration technique requires thorough understanding of the physics of separation of particles inside it. However, the density differential between the heavy minerals and the quartz density minerals in a placer deposit is quite significant. Therefore, an attempt has been made to evaluate the performance of a laboratory scale Knelson concentrator while removing these two particle classes with an objective to understand the effects of G- force and the fluidization water pressure on the separation efficiency.
Knelson Concentrator Working Principle
Essentially all the models consist of a conical inner shell, with a series of parallel “vee” shaped riffles, bolted to a rotating outer shell. Feed is introduced in the form of slurry at the bottom of the unit through a central tube. A theoretical centrifugal force of around 60G causes the feed solids to fill the inter-riffle spaces from bottom to top. Once these spaces are full of solids the introduction of further feed starts the sorting stages where heavy minerals displace the lighter minerals and as a result the heavy minerals are trapped in the inter-riffle spaces while the lighter minerals are carried by water to the top of the unit, hence a separation occurs. To keep the bed of heavy minerals thus formed fluidised. water is introduced through the multiple fluidisation holes in the inner shell. This fluidisation water force is expected to be strong enough to inhibit severe compaction of the heavy mineral bed due to the strong centrifugal force. The concentration mechanism in a Knelson concentrator may thus be linked to a hindered settling classifier. One of the major disadvantages of this unit is the large fresh water requirement (up to 2-3 times the feed flow) to fluidise the particle bed.
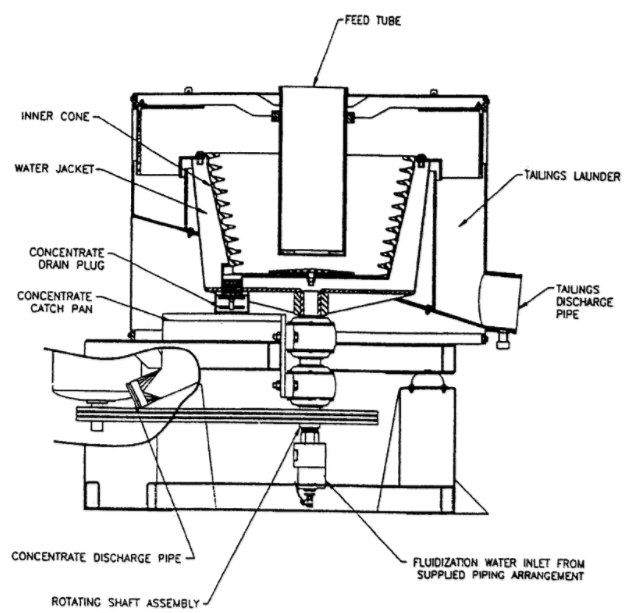
The Knelson Concentrator is a compact hatch centrifugal separator with an active fluidized bed to capture heavy minerals. A centrifugal force up to 60 times that of gravity acts on the particles, trapping denser particles in a series of rings (riffles) located in the machine, while the low-density particles are flushed out. Unit capacities range from laboratory scale to 150t/h for particles ranging in size from 10 pm to a maximum of 6 mm. It is generally used for feeds in which the dense component to be recovered is a very small fraction of the total material, less than 500 g t 1 (0.05% by weight).
Feed slurry is introduced through a stationary feed tube and into the concentrate cone. When the slurry reaches the bottom of the cone it is forced outward and up the cone wall under the influence of centrifugal force. Fluidization water is introduced into the concentrate cone through a series of fluidization holes. The slurry fills each ring to capacity to create a concentrating bed. with compaction of the bed prevented by the fluidization water. The flow of water that is injected into the rings is controlled to achieve optimum bed fluidization. High-specific gravity particles are captured and retained in the concentrating cone; the high-density material may also substitute for the low-density material that was previously in the riffles—made possible by the fluidization of the bed. When the concentrate cycle is complete, concentrates are pushed from the cone into the concentrate launder. Under normal operating conditions, this automated procedure is achieved in less than 2 min in a secure environment.
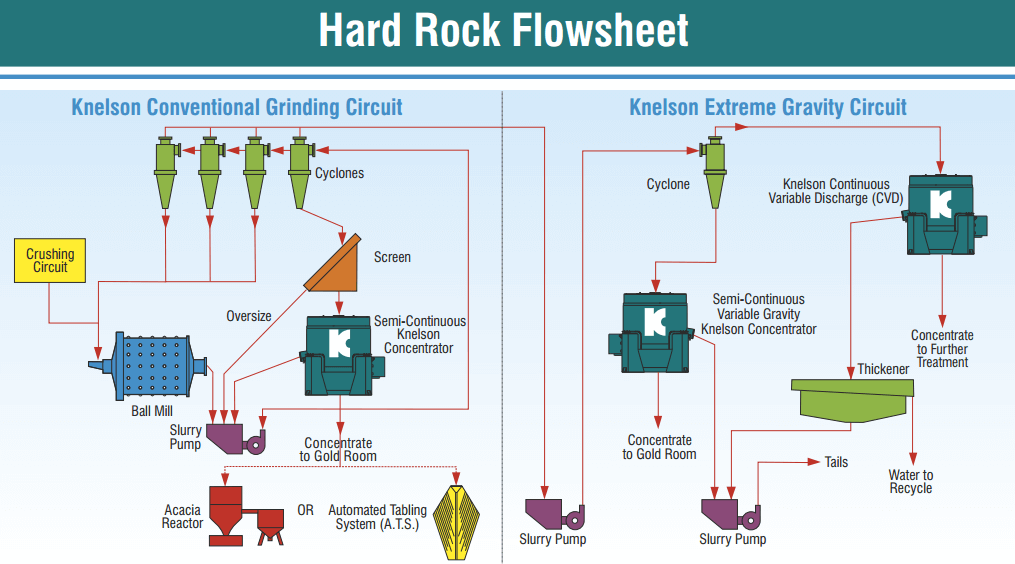
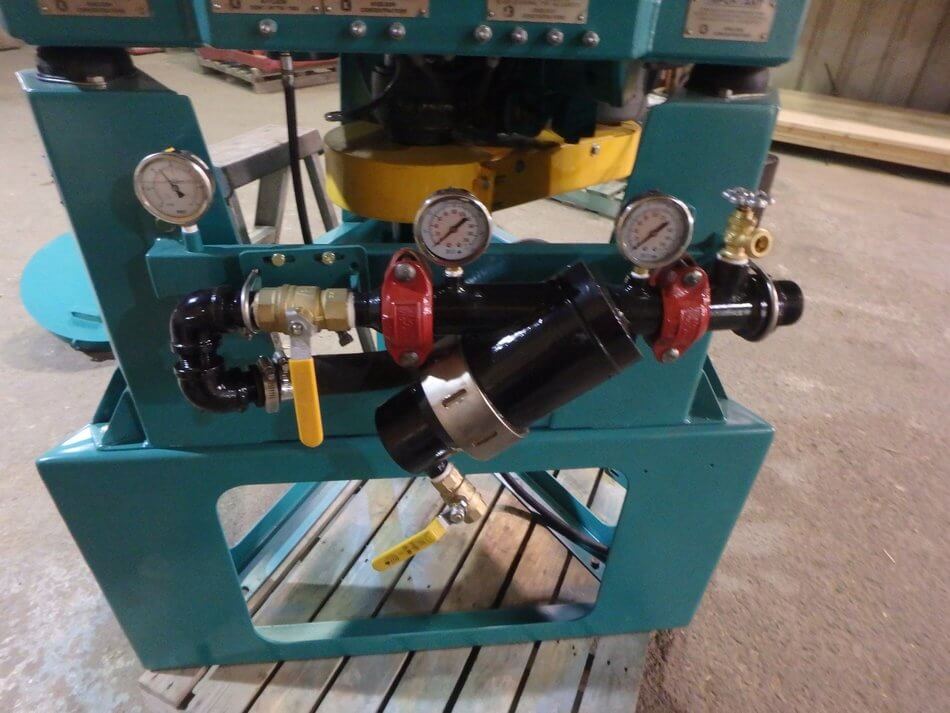
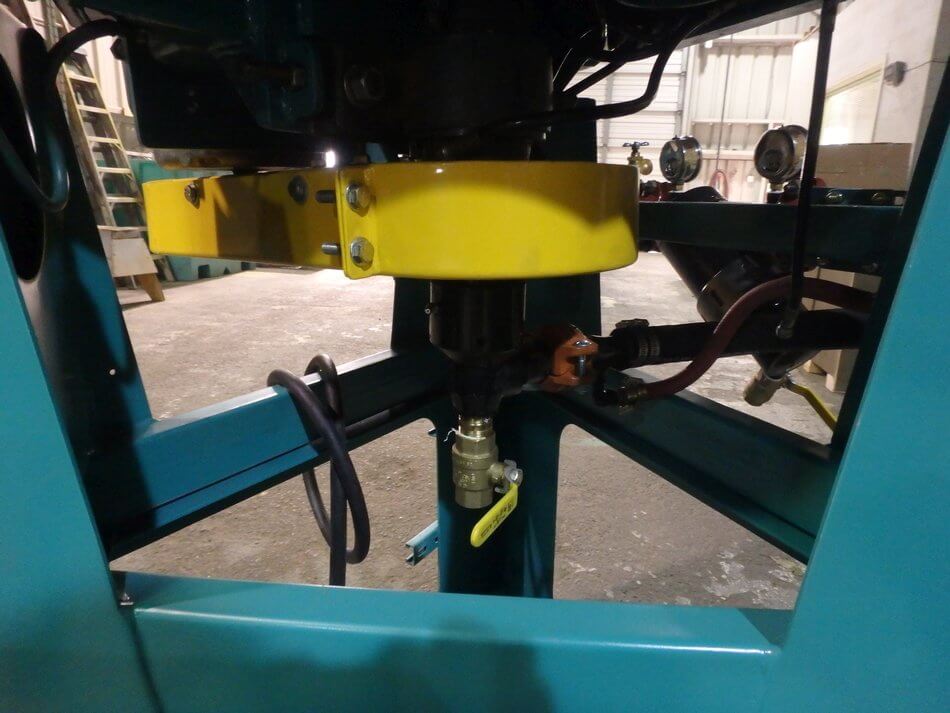
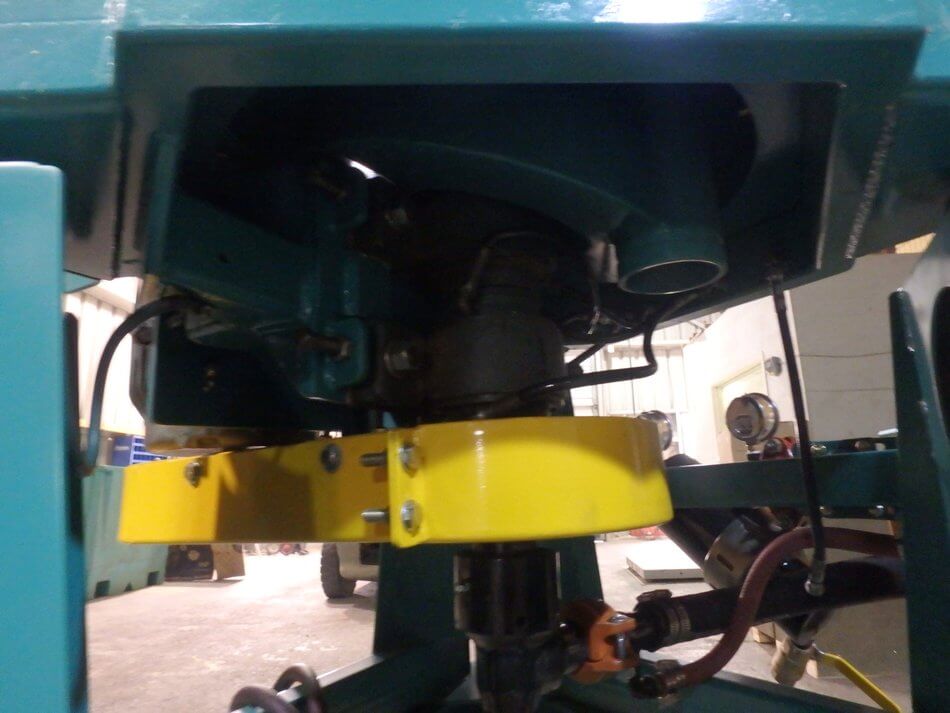
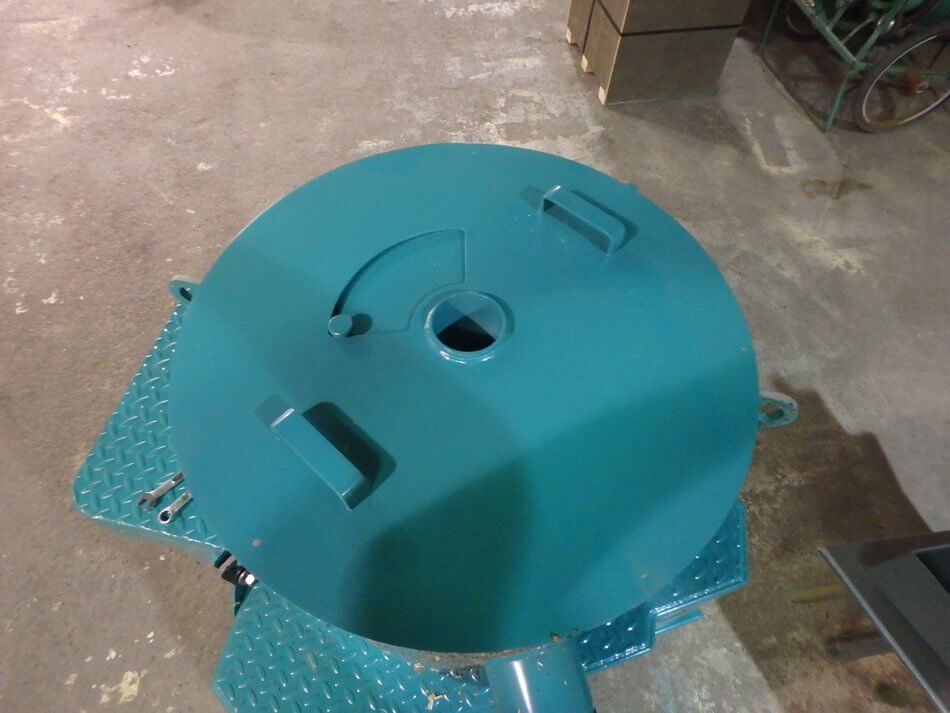
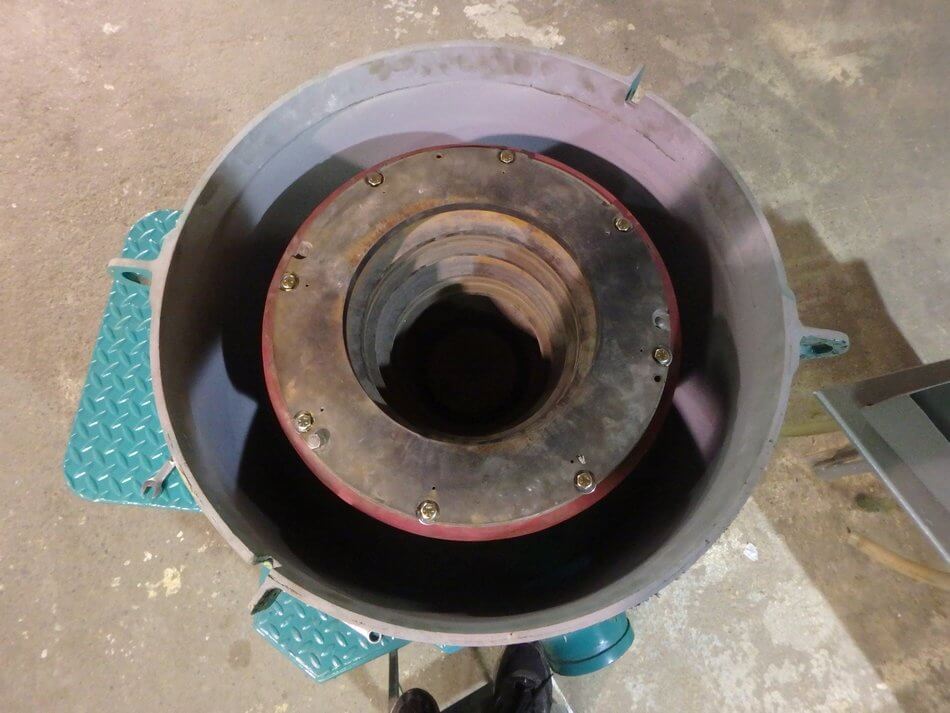
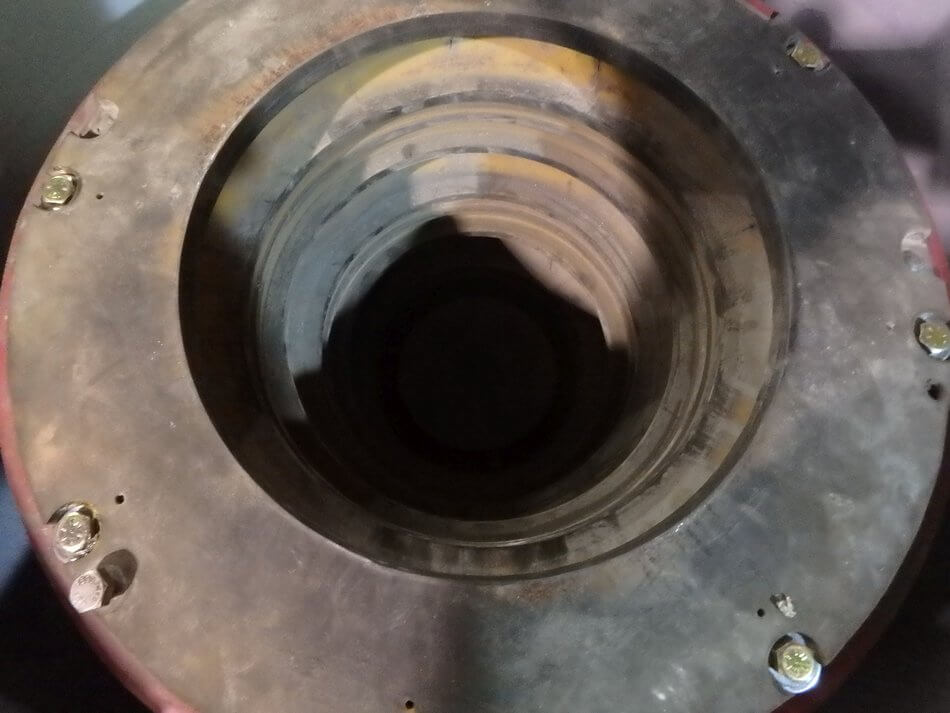
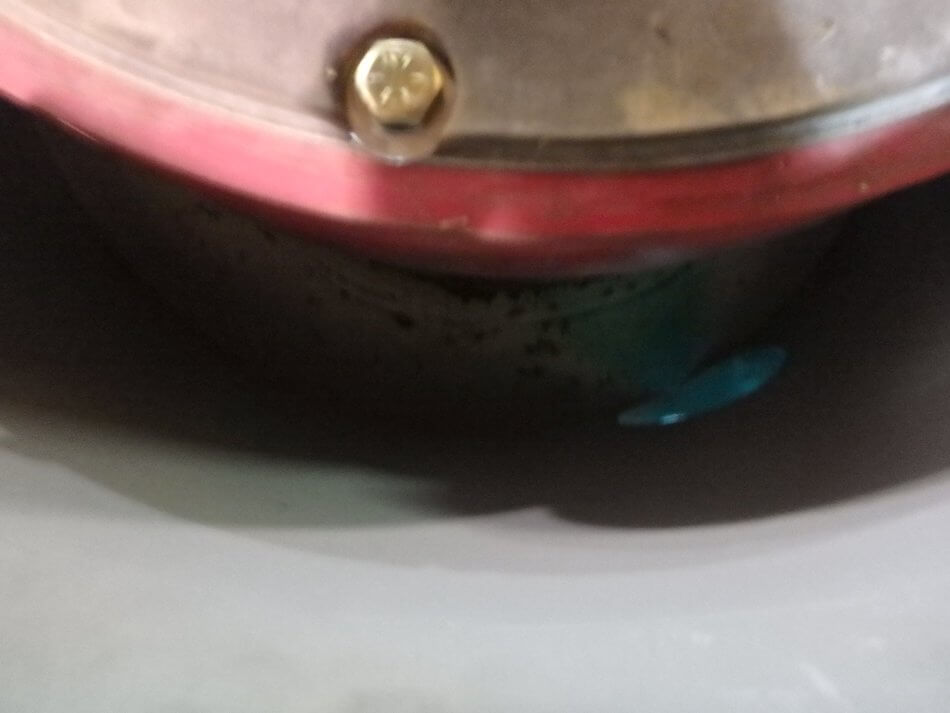