For a hydrocyclone to work at peak efficiency the volume of slurry and the feed pump delivery pressure must remain constant. If the cyclone feed pump is allowed to SURGE, the up and down pressure will cause poor separation at the point of high and low operating pressure.
There is a cycle to a surging pump box that causes this pressure fluctuation.
First the pump pumps all of the slurry out of the pump box. When the box becomes empty the pump gets some air which results in an air lock. The air lock prevents the slurry from entering the pump’s casing. The cyclone now does not have any feed going to it, the hydrocyclone feed pressure is lost. The pump box will fill up until the weight of the slurry in the pump box is great enough to force the air past the pumps impellor. When this happens the cyclone pressure shoots up as the pump empties the full pump box.
Some of the things that will cause a pressure surge are, not enough feed going into the pump box and the pump air locking. The operator making many large changes in his circuit, tonnage increases and decreases or extra water being added to the circuit from cleanup hoses. The design of the grinding circuit and the ore physical characteristics can cause a pump surge as well.
What happens here is if the mill discharge has an inclined launderer to flow over before it enters the pump and a pump box whose design allows an area for coarse particles to settle-in. The fine material will flow to the pump to be pumped away leaving the coarse particles behind. This coarse material can build up in the pump box until it becomes overloaded. It will then SLOUGH IN and a big portion of this coarser material will be fed directly to the pump causing an overloaded condition in the cyclone. This build up can become so great that when it finally sloughs in it will plug the pump completely off.
The cure for this is to either increase the angle of the incline in both the launder and the bottom of the pump box. This is to prevent settling. Decrease the density to wash the coarse particles in, or agitate the pump box.
![]() |
![]() |
There is one more operating question to be answered, how do you control the classification inside the cyclone?
The answer is manipulating either the TONNAGE of the cyclone feed, the DENSITY of the cyclone feed or in some cases the APEX SIZE of the cyclone.
PRESSURE is the key here, all cyclones have an optimum operating pressure range. For the sizing of the material there will be a preferred apex size. To increase the apex opening will mean to allow more material through the underflow. This will give the next stage of size reduction a higher tonnage to grind and increase the feed to the cyclone when it is reclassified. To close the opening of the apex will force more of the coarse material out of the circuit to the next stage of processing. This causes an immediate increase of pressure to the cyclone hut it will drop as the grinding circuit empties it extra tonnage.
When you increase the tonnage to a circuit you decrease its efficiency in grinding the material. As I mentioned in the chapter on grinding when you increase tonnage you lower the amount of time that the ore spends in the mill being ground. This results in a larger portion of the ore being coarser. The cyclone will then have to contend with a higher volume of ore. This increases the pressure which increases the amount of coarse material in the overflow as well as the underflow. Once the underflow goes through the next stage of grinding it will be to increase the pressure once more.
The problem now is to control the efficiency of the hydrocyclone. To do this you control the density of the cyclone. Because the cyclone works upon the pressure inside of it, adding or taking away water that is being fed to it will control the grind of the ore being discharged. As pressure increases inside the cyclone, the SPEED of the spiral increases, this increases the centrifugal force as well as the discharge rate of the cyclones underflow. The extra water in effect displaces the ore at the centre of the vortex. This causes more of the ore to be pushed closer to the side wall of the cyclone. This will take it past the point that the apex finder will dissect the flow of slurry.
Simply put, you add water to the cyclone feed to bring the density down which in turn will reduce the amount of coarse particles in the overflow. As a word of warning, keep a close eye on the cyclone, there is an increase of underflow volume when you do this which will have to be reclassified. That extra could be enough to cause the cyclone to overload.
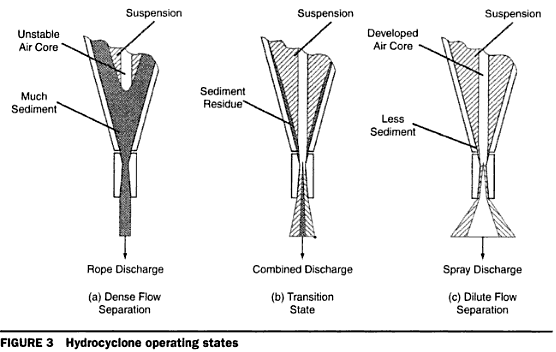
The indication that you are reaching an overload condition in your cyclone is the pressure. There is a low point and a high point that if you go over, the cyclone quits working. In some concentrators the pressure gauge on the cyclones may not be working or may not be there at all. If this is the case, all is not lost, there is a way to tell if the cyclone overloads without the gauge. The normal underflow discharge of a cyclone flares from the skirt. As the pressure increases the flare becomes less and less as the vortex gets smaller. When the Vortex collapses, the slurry will be coming out of the cyclone at the same diameter as the apex’s opening. It will also be twisted, looking very much like a thick rope. In fact that is what it is called, ROPING.
If your equipment has variable control on the apex size it is very important that it remain within the correct operating parameters. By changing this one control it can become impossible to maintain pressure and density at an acceptable level.
Cyclone Feed Pump
A 5″ x 4″ SRL-C Pump delivers a minus 1/8″ screen undersize and rod mill discharge at a rate of 288 g.p.m. of 20% solids pulp (270 T/24hr.) to a cyclone requiring inlet pressures to 44 p.s.i. with a vertical lift of 54 feet. The total dynamic head pumped varies from 100 to 150 feet, with 110 feet being the normal operation. Although a 150 feet T.D.H. would be excessive for most pumps, the SRL Pump continuously handles this severe service for many weeks before replacement of the molded rubber runner is required. During this time some 11,300 tons of abrasive solids are pumped.
Powered by a 20 HP motor, this pump draws only 17 HP in operation with minimum wear on the molded rubber parts.
The SRL Pump may be readily controlled to maintain cyclone inlet pressure by simply controlling pump speed. For example: The 5′” x 4″ SRL Pump delivers 300 g.p.m. of water against an 80 foot T. D. H. at 1150 R.P.M. At 1275 r.p.m. (10.8% increase) 300 g.p.m. of water is delivered against a 100 foot T.D.H. or an increase of 25 % in T.D.H.