Table of Contents
Scrap metal, both ferrous and non-ferrous, present in industrial wastes, slags, smelter bi-products, sludges, refinery sweepings, ashes, etc., can be reclaimed in most instances at a profit and thus are made available for reuse in industry. Very substantial stockpiles of these scrap metal wastes are available for processing in the various industrial areas. 911metallurgist.com through its testing facilities during the past several years, has investigated many of these sources of good reclaimable metal and in the majority of cases low cost efficient treatment methods and plants have been developed and are now operating very successfully.
Generally, gravity concentration is the most practical method applicable in the recovery and treatment of scrap metallics due primarily to the gravity difference between metal and waste. The flowsheet above is a composite of average treatment methods and has been successfully applied in the recovery of such metals, alloys, and materials as brass, bronze, copper, lead, zinc, ferro-chrome, silver, gold, tin, shot, silicon carbide, and abrasives. In some instances Magnetic Separation and “Sub A” Flotation have been applicable.
Process & Method for Recycling/Recovering Metals from Scrap
A scrap metal flowsheet consists of the following basic steps:
Crushing Scrap Metal
Size reduction is generally necessary particularly on slags, drosses, and lumpy material. A heavy duty Steel Frame Jaw Crusher such as the Type J Crusher is necessary for this service. Often the metal is brittle and small enough and the slag can be effectively reduced in size by this means. Large pieces of metal, if malleable, should be sorted out whenever possible on the feeder ahead of the crusher. If this is not possible and the metal is very coarse, then an impact type crusher should be selected.
Grinding Scrap Metal
Crushing alone will not generally provide ample size reduction, so to clean and free the metal from the waste it is necessary to grind in a ball mill. The Steel Head Ball mill will effectively provide the necessary size reduction and polishing of the metallic particles. In certain cases manganese steel grate discharge head liners are desirable in the grinding unit to retain the very coarse metal in the mill for periodic clean-ups.
In any scrap metal grinding circuit it is highly desirable to provide a steady rate of feed. In the flowsheet this is accomplished by a Adjustable Stroke Belt Feeder delivering the crushed scrap waste from a storage bin. Middlings and oversize are recirculated by a Classifier to the mill feed.
Screening and Classification
The discharge from the Ball mill passes over a Spiral Screen which is attached directly to and revolves with the mill. In many cases the screen oversize product (usually 3/16″ or ¼”) is a finished high grade metallic product requiring no further treatment. Special Spiral Screens and double screens are often used if two sizes of coarse material are to be segregated from the mill discharge.
The undersize product from the Spiral Screen is treated as described under jigging. A Classifier is placed along side of the mill to return oversize and middlings back to the feed for further grinding as required.
Jigging heavy metals
The coarse oversize product from the spiral screen, if not clean, is effectively up-graded in a Improved Harz Type Jig. Here a clean metallic product is removed through the jig side draw-off outlets and a waste or middling discharges over the end of the jig. Coarse middlings, after drainage, can be diverted back to the grinding circuit if necessary for further size reduction and retreatment. Water from this coarse jigging circuit can be reclaimed if necessary.
The Mineral Jig, usually placed in the grinding circuit, treats the Spiral Screen undersize producing a high grade metal product and an unfinished tailing which is either diverted directly to tables for recovery of fines or flows by gravity to the Classifier.
The Mineral Jig is highly selective and will recover metallics down to about 200 mesh. Shotty, flakey particles are readily recoverable in this jig and it is these particles which are the cause of high losses in straight tabling circuits. Often the Improved Harz and Mineral Jigs will recover upwards of 90% of the total metal content in the feed. This leaves only the very fine sizes for the tables. Center draw-offs are often provided in Mineral Jigs for removal of coarser metal sizes.
Wedge bar screens, preferably stainless steel, are used in both the Harz and Mineral Jigs. These special screens prevent blinding and require very little attention during operation.
Tabling heavy Scrap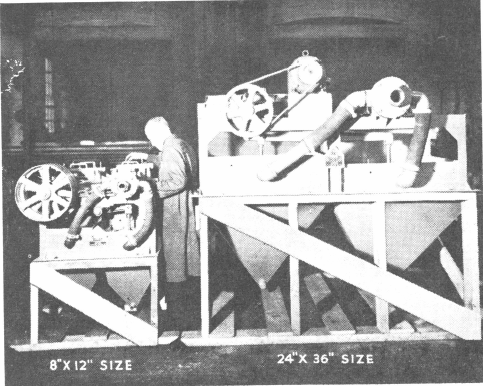
Fines not recoverable by the jigs are treated over one or more Wilfley Tables. The amount of metal recoverable here is usually small and the table serves as a pilot for the operation indicating visually the plant efficiency. If middlings are present, they can be returned by a Vertical Pump to the Classifier or in some cases direct to the mill feed.
Water Reclamation and Tailings Disposal
Generally it is necessary to reclaim water particularly in industrial locations where water must be obtained through a meter system. Pumping the refuse or waste to a Spiral Rake Thickener is indicated in the flowsheet. The thickened underflow sludge is removed by a Diaphragm Pump and diverted to waste. In some localities it is necessary to filter this product and haul it to a suitable waste disposal area.
In treating certain special products the slime or light gravity material is of considerable value and therefore must be thickened and filtered for further processing.
Mineral Jigs (Pulsating Selectors) are often furnished with center draw-offs for the concentration of coarse mineral particles.
SUMMARY
Standard Equipment products, including motors, for the flowsheet as outlined with a capacity of two tons of scrap metal waste (feed) per hour, will cost approximately $contact911. This equipment will weigh 56,000 pounds exclusive of the grinding charge. Total connected load is 57 horsepower. Laboratory examination and tests in our laboratory are advisable before making selection of equipment sizes.