When the non-choking feature was being applied to existing crushers of the gyratory type, it was found that in several crushing machines, the attendant reduction in receiving opening could be partially offset by sloping the straight portion of the concaves at a wider angle than that for which the top shell was originally designed, because some of these older machines were designed with very conservative crushing angles. Generally speaking, however, this was not true of existing lines of jaw crushers. It is true that prevailing angles could be widened in certain cases, and for certain applications; but the jaw crusher, more than any other type of crusher, is called upon to handle very hard, tough materials, and standard designs must be based on that kind of duty. Furthermore, as was pointed out in our discussion of gyratory crushers, a certain amount of slippage occurs in all crushing chambers, and the jaw crusher, which is not essentially a high-capacity crushing machine, could ill afford to have any additional slippage built into it.
A study of these factors convinced designers that, to fully realize the advantages of the non-choking feature in the Blake-type crusher, it would be necessary to develop a new line, with crushing chambers designed specifically for that type of plate. It was realized, that improved performance particularly on hard rock would result from a substantial decrease in the prevailing practice with regard to crushing angles. And, thirdly, inasmuch as the jaw crusher is predominantly a primary breaker, it was desirable that these improvements be incorporated without sacrificing valuable inches of receiving opening.
These ideas were given concrete form in a new line of all-steel Blake-type jaw crushers, with frames of welded design, and several interesting and important refinements in mechanical details, including an improved system of lubrication.
On the right is a diagram of the crushing chamber in one of the jaw crushers. This diagram covers a machine of the same receiving opening size as the standard type on which the two preceding diagrams were based. A brief comparison will indicate why ‘the new crusher has distinctive performance characteristics. At first glance, the most striking difference lies in the depth of the crushing chambers, due partly to the non-choke design, and partly to the decreased crushing angle. This diagram was laid out for the same jaw motion as the standard-crusher diagram, and it will be noted that about the same number of strokes are required to move the material down from receiving opening to discharge opening. However, it will also be noted that the areas between successive lines are substantially greater, which is a direct indication of the relative theoretical capacities of the two crushers. In addition to this theoretical difference, there is an “imponderable” asset which accrues to the decreased crushing angle; an asset which is not subject to pre-calculation, but which contributes in no small degree to the excellent performance of the new machine, not only in increased capacity, but in reduced rate of wear on the jaw plates.
Ratings of the developed sizes of the single-toggle crusher are given in a table.
Naturally, it costs money to build such characteristics into a crusher, and, for that reason, it is hardly to be expected that this improved design will entirely supersede existing standard models of the Blake crusher. In very many applications, receiving opening, rather than optimum capacity, is the predominant factor. For such applications, especially for those involving soft, or medium-hard material the lower cost standard crusher will probably continue in favour.
https://www.metso.com/industries/aggregates/
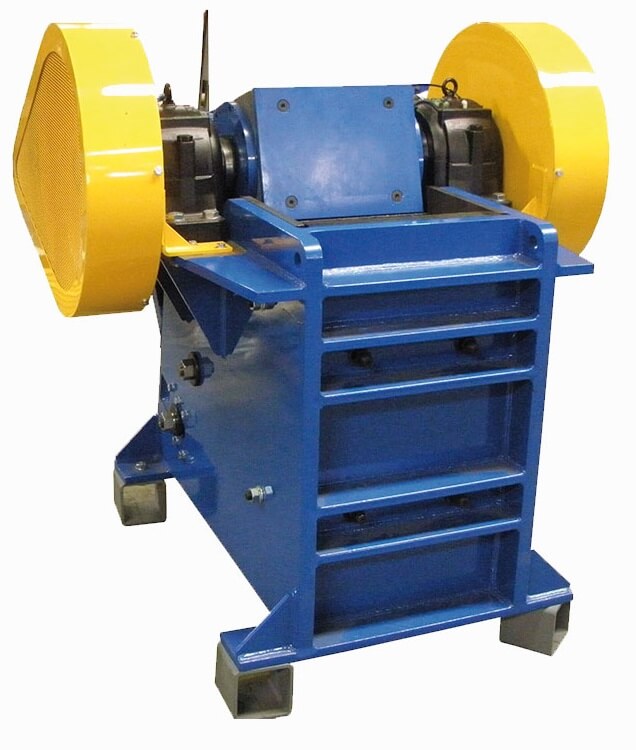